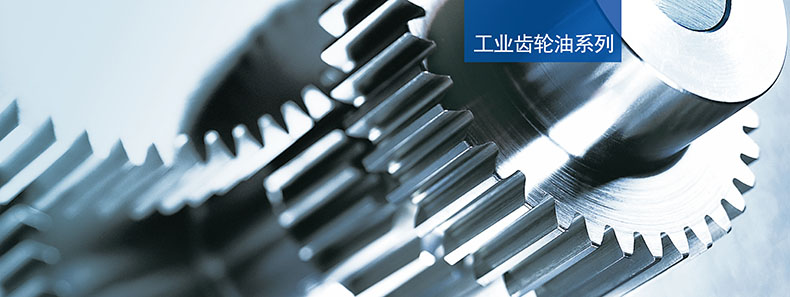
一、概述
齿轮传动是机械传动中一种最重要的传动方式。齿轮传递运动和动力是靠齿轮的齿面相互啮合完成的,期间必然产生摩擦。为保持齿轮机构的使用寿命,需对啮合齿面进行润滑。润滑油可在齿面上形成吸附膜和反应膜,降低摩擦系数并承受外载荷。
工业齿轮油是工业齿轮传动装置所需要的专用润滑油,主要包括开式工业齿轮油、闭式工业齿轮油和蜗轮蜗杆油。齿轮油的主要功能是在相互啮合的齿面间起润滑和冷却作用,以减少摩擦、降低磨损,同时也有缓和冲击与振动、防止腐蚀生锈,以及清洗摩擦面尘粒与污染物的作用。此外,还可改善胶合性,防止齿轮破裂、点蚀、胶合的一个因素。
二、工业齿轮油分类
根据齿轮传动形式和工作条件不同,工业齿轮油分为闭式工业齿轮油、开式工业齿轮油和蜗轮蜗杆油。GB/T 7631.7等效采用ISO 6743-6,制定了工业齿轮油分类标准。
三、工业齿轮油产品标准
3.1 国外工业齿轮油产品标准
早期含铅工业齿轮油所满足的美国钢铁公司USS 222规格以及美国齿轮制造商协会AGMA 250.03 规格,是工业齿轮油的最低要求。美国齿轮制造商协会(AGMA)的产品标准包括:抗氧防锈型工业齿轮油AGMA 250.04R&O;中负荷工业齿轮油AGMA 250.03 EP和重负荷工业齿轮油AGMA 250.04 EP。
开式齿轮油的规格有AGMA 251.02(R&O)与AGMA 251.02(Mild EP)共2种,前者为抗氧防锈型,后者为中负荷开式齿轮油。现代工业齿轮油在此基础上要求油品具有更高的热稳定性、抗乳化性和高温极压抗磨性能,代表此性能的规格为美钢USS 224。美国钢铁公司224规格为世界最高水平的工业齿轮油,不论是油品的极压性能、抗乳化性能、防锈性能,还是热氧化性能,都比其他标准严格。美国蜗轮蜗杆油有两个军用标准,即轻负荷蜗轮蜗杆油MIL-L-15019E6135和重负荷蜗轮蜗杆油MIL-L - 18486B(OS)。
国际标准化组织(ISO)发布了ISO 12925-1《闭式齿轮油使用规范》,该标准包括了ISO 6743-6中的6个润滑油型产品,即CKB, CKC, CKD, CKE, CKS 和CKT油,黏度等级从VG32~1500有11个牌号,每一牌号都规定了详细的性能指标。
3.2 国内工业齿轮油产品标准
GB 5903-2011《工业闭式齿轮油》非等效采用ISO 12925-1《闭式齿轮油使用规范》、美国齿轮制造商协会标准ANSI/AGMA 9005-E02《工业齿轮润滑》,制定了L-CKB、 L-CKC和CKD产品标准。
在SH/T 0094-1998《蜗轮蜗杆油》中,CKE标准参照采用美国军用标准MIL-L-15019E -1982中6135号制定, CKE/P参照采用美国军用标准MIL-L- 18486B(OS)-1982制定。
普通开式齿轮油执行SH/T 0363-1992《普通开式齿轮油》。
更多润滑油产品标准请参考产品标准清单。
四、工业齿轮油组成
4.1 基础油
用于调配工业齿轮油的基础油主要有矿物油与合成油两大类。矿物油与合成油相比价格便宜,性能也基本能满足要求,因此,大多数工业齿轮油都用矿物油来调配。随着材料科学和齿轮加工技术的发展,齿轮设计不断趋于小型化,使得齿面的比负荷增大,齿轮油的工作温度升高。至此矿物油不能满足长期高温工作的要求,需用合成工业齿轮油来解决。用于调配工业齿轮油的合成润滑油品种有聚a-烯烃油、酯类油和聚醚合成油。
聚a烯烃油可制备极高黏度的工业齿轮油,也可以制备出寒区和严寒区使用的低倾点和低温性能优良的齿轮油品种。聚醚因其黏度大、黏度指数高、润滑性好和热氧化后不生成积炭等优点,广泛用作长寿命齿轮油。酯类油的黏度范围和润滑性能均稍差于聚醚,仅用于航空齿轮、仪器仪表齿轮、钟表齿轮等传动装置的润滑,或与聚a-烯烃油调和使用,以改善低温和橡胶溶胀性能。虽然合成油的性能优于矿物油,但由于其价格太贵,因此不普遍使用。半合成油主要用矿物油与聚a-烯烃油或酯类油调和,以提高黏度和改善低温性能。
4.2 添加剂
为了防止油膜破裂造成齿面磨损、擦伤、烧结等现象,延长其使用寿命,提高传递功率效率,减少功率损失,在齿轮油中一般都加入极压抗磨剂。过去常用的极压抗磨剂是硫-氯型、硫-磷-氯型、硫-氯-磷-锌型、硫-铅型和硫-磷-铅型添加剂,而目前普遍采用硫-磷或硫-磷-氮型添加剂。极压抗磨剂是工业齿轮油中最重要的添加剂,它的加入可以提高齿轮油的耐负荷性和抗擦伤能力。添加剂分子中的氯、硫、磷等活性元素在摩擦面的高温条件下与金属发生化学反应,生成氯化铁、硫化铁、磷化铁薄膜,防止金属表面直接接触。工业齿轮油常用的极压抗磨剂见下表。
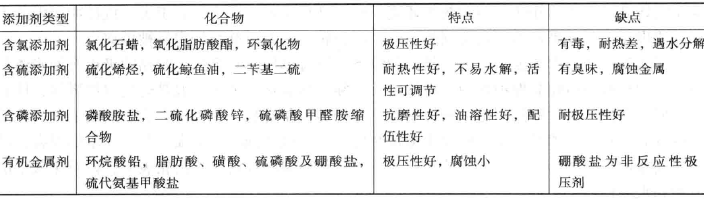
五、齿轮传动润滑条件
5.1 闭式齿轮传动
齿轮机构是机械中最主要的一种传动机构,其传递功率范围大,传动效率高,可传递任意两轴之间的运动和动力。
齿轮传动是靠齿轮机构中每对啮合齿面的相互作用和相对运动来完成的,这种传动更容易产生磨损与卡咬。与滑动轴承相比,多数齿轮的齿廓曲率半径小,一般为几十毫米,因此润滑形式相当复杂。齿面间既有滚动又有滑动,产生复杂的螺线运动,而且滑动的方向和速度变化急剧。润滑是断续性的,每次啮合都需重新形成油膜,形成油膜的条件较差。
一些重载机械如水泥磨机、起重机、卷扬机的齿轮齿面接触应力可达400~1000MPa。冶金机械齿轮传动齿面接触应力更高,齿面接触应力已超过1000MPa,达到1200~1500MPa。由于过载负荷较大,常常承受很大的过载负荷,这样会促使疲劳点蚀的发展,使齿轮过早地磨损破坏。齿轮装置工作时,由于工况条件的变化,齿面所处的润滑条件不同,在启动、停车、低速重载、高速重载等有冲击负荷条件下工作时,齿面处于边界润滑状态。
5.2 开式齿轮传动
在机械设备中,有一些齿轮传动没有防尘罩或机壳,齿轮完全暴露在外面,称为开式齿轮传动。开式齿轮传动中易落入灰尘、屑等外部介质而造成润滑油污染,齿轮易于产生磨料磨损。当对开式齿轮给以覆盖时,在相同的工作条件下,开式齿轮的润滑要求与闭式齿轮相同。
开式齿轮传动的润滑方法一般是全损耗型的,而任何全损耗型润滑系统,最终在其齿轮表面只有薄层覆盖膜。接触面常处在边界润滑条件下,因为补充到齿面的新油,会由于齿面压力作用而被挤出,加之齿轮回转时离心力等的综合作用,只能在齿面上留下一层薄油膜。因此,润滑油必须具备高黏度或高稠度和较强的黏附性,以确保有一层连续的油膜保持在齿轮表面上。
开式齿轮暴露在变化的环境条件中工作,例如北方运河水闸的开式齿轮在冬季0℃以下的环境中工作,造纸机干燥机滚筒的开式齿轮系统在高湿度和60℃以上的环境温度中工作;水泥窑转筒环形齿轮在热、雨和灰尘环境。在自动化生产工厂中,对于大型机械冲床中的大型开式齿轮,其环境虽然不是苛刻的因素,但齿轮上的润滑剂却较容易被抛离。
5.3 蜗轮蜗杆传动
三种常用蜗杆传动为普通圆柱蜗杆传动、圆弧齿圆柱蜗杆传动及环面蜗杆传动。影响蜗杆传动承载能力的主要因素有接触线长度、当量曲率半径和接触线分布情况。环面蜗杆传动夹角接近90℃,形成油契条件好,同时接触齿数多,当量曲率半径大,所以承载能力高。圆弧齿圆柱蜗杆传动和普通圆柱蜗杆传动相比较,夹角和当量曲率半径都较大,所以形成油契条件好、承载能力高。同齿轮传动相比,蜗杆副的相对滑动速度是高的,对大多数工业齿轮而言(准双曲面齿轮除外),其相对滑动速度仅为其节圆圆周速度的1/3左右,而蜗杆副的相对滑动速度还略大于其节圆圆周速度。蜗杆副传动中滑动沿齿高方向和齿方向都存在但是以齿向为主。蜗杆传动的滑动速度值大,这是影响蜗杆传动承载能力的重要因素。
六、工业齿轮油性能
6.1 黏度和黏温性
适宜的黏度可以保证在弹性流体动力润滑状态下形成足够厚的油膜,使齿轮具有足够的承载能力,降低齿面磨损。在流体动力润滑状态下,齿轮油的黏度决定润滑膜形成的厚度。齿轮油的黏度高,弹性流体润滑油膜厚度大。齿轮是处于混合润滑状态下工作的,在齿面受重负荷和高冲击负荷时,应采用较高黏度的齿轮油。黏度指数越高,黏度随温度的变化越小,可保证在较高齿面工作温度时形成足够的滑油膜。
6.2 极压抗磨性
两个齿轮工作面啮合时,在负荷不大的情况下作面完全被齿轮油隔开,这时为流体动力润滑状态,摩擦阻力由齿轮油的黏度决定。当负荷增大时,啮合齿面发生弹性变化,润滑油黏度在压力下急剧增大,还能迅速形成极薄的弹性流体动力膜,仍能将摩擦工作面隔开。因此,流体动力润滑和弹性流体动力润滑与齿轮油的黏度有关。当负荷继续增大时,齿轮表面的凸起部分将油膜划破而发生直接接触,齿轮工作面间已不可能存在完整的油膜,润滑只能靠齿轮油中的极性分子吸附在金属表面一层或几层分子构成边界吸附膜,这种吸附膜可以由物理或化学吸附形成。在高温、高压工作条件下,边界吸附膜发生脱附,这时齿轮工作面间的润滑要靠齿轮油中的活性组分与齿面金属发生反应生成的化学反应膜来完成。例如,齿轮油中所含的硫、磷、氮化合物与金属表面发生反应,生成比工作面金属软的化学反应膜,填补金属表面凹凸不平之处。此时摩擦滑动剪切运动在化学反应膜中进行,可防止金属表面拉伤。这种以吸附膜或反应膜进行润滑的状态称为边界润滑状态。
极压抗磨性能是齿轮油的最重要性能。齿轮在传动中,齿与齿间接触面不大,啮合部压力很高,润滑条件苛刻,对润滑油要求高。对重负荷下工作的齿轮,特别是双曲面齿轮和弧齿锥齿轮以及蜗轮蜗杆等,为了使齿面不产生擦伤、胶合、点蚀及磨损,齿轮油应具有良好的极压抗磨性。在重载荷和冲击负荷下,要靠齿轮油来形成润滑膜,防止齿轮金属工作面直接接触。如果齿轮油的极压抗磨性差,轻则会造成齿面磨损,重则会使齿面擦伤、剥落,甚至发生胶合,严重影响齿轮传动机构的正常工作。
6.3 抗氧化安定性
由于齿轮的高速运转会产生大量的热而使油温升高,加快油的氧化速度,使油变质,从而齿轮产生磨损、腐蚀,所以齿轮油应具有良好的抗氧化安定性。齿轮油在工作中受摩擦工作面产生的热而升高温度,同时还接触空气、水和具有催化作用的金属,因此很容易氧化。齿轮油氧化变质后会失去原有的性质,不但不能保证齿轮传动机构的正常工作,而且氧化产生的酸还会腐蚀金属,氧化产生的油泥、漆膜会沉积在齿轮表面,严重影响齿轮的正常润滑。因此,齿轮油的氧化性能决定油品的使用寿命。
6.4 抗剪切安定性
齿轮在运转中所引起的对齿轮油的剪切作用,使油的黏度改变,特别是油中添加的黏度指数改进剂最容易受到剪切影响,因此齿轮油应具有良好的抗剪切安定性。
6.5 防腐防锈性
齿轮油中含有活性添加剂组分,在边界润滑状态时,这些活性组分要与齿面金属反应生成化学反应膜,保证齿轮工作面的润滑。另一方面,齿轮传动机构中还有许多铜或铜合金部件,油中的活性组分不应腐蚀这些铜部件。齿轮油在使用中发生氧化会产生腐蚀性酸,要防止它们对金属的腐蚀。在齿轮运转中,因油被氧化而形成油泥胶质酸性物质使齿轮生锈,特别是和冷凝水接触时也容易生锈和腐蚀,所以要求齿轮油具有良好的防锈性能。
6.6 抗泡沫性
齿轮油受激烈搅动,产生泡沫,使油不能充分供应,减低润滑性能,所以要求齿轮油具有良好的抗泡沫性
6.7 抗乳化性
齿轮在运转中常接触到冷凝水和冷凝液等使齿轮油乳化,引起添加剂水解或沉淀分离,产生有害物质,使齿轮油变质,失去润滑性,所以要求齿轮油具有良好的抗乳化性。如果油品不具备迅速彻底分离水的能力,则可能由于油品的乳化而使其润滑性和流动性变差,使油品其他性能如极压抗磨、防腐防锈性能遭到破坏。油品的抗乳化性与基础油的精制深度有关,精制越深,油的抗乳化性越好,随着基础油黏度的增加,馆分变重,胶质、重芳烃等极性物质增多,其抗氧、抗乳化性随之下降。工业齿轮油所加添加剂大多属表面活性剂,都对油水界面张力产生影响,从而改变了油品的抗乳化性。因此,工业齿轮油的乳化除基础油的影响外,抗乳化剂的种类、抗乳化剂与其他添加剂之间的配伍性对其影响更大。在使用中,由于添加剂的降解和消耗,会使原配方中的抗乳化性能发生变化,从而降低了油品的抗乳化性。
七、齿轮齿面损伤与润滑的关系
齿轮传动具有效率高、结构紧凑、工作可靠、使用寿命长、传动比稳定等一系列特点,是机械传动中最主要的一种传动形式。但是,由于设计、制造以及使用不当、润滑不良等原因,齿轮传动在工作过程中,常常会发生失效。常见的齿轮传动的失效形式,有轮齿的折断、齿面磨损、齿面点蚀、胶合、塑性变形等五大类型。在这些失效形式中,润滑对其影响程度是不一样的,有的甚至只是非直接性的影响。但是,不论是那一种失效形式,都将导致齿轮传动不能正常工作。
齿轮齿面损伤详见《工业齿轮损伤形式》一文。
7.1 润滑对齿轮磨损的影响
在齿轮传动装置中,时常发生齿面磨损现象。磨损是多方面原因所致,其中中等磨损多数是由于齿面不规则、齿轮齿形的误差大、润滑油黏度不够或因某种条件使齿轮工作在混合膜润滑边界条件下所造成的,这种因为重载、过载或润滑油抗磨性能差引起的磨损更为严重。这种磨损的发生将迅速去除齿面材料,破坏齿的形状和齿轮装置的平稳性,甚至引起停机故障。磨损是开式齿轮和在恶劣环境下工作的齿轮常见的一种失效形式。对渐开线齿轮传动,磨损的部位通常发生在齿轮的节圆附近和齿顶高处。导致磨损的直接原因,是因为在轮齿工作表面存在有摩擦,为此,欲减轻磨损,可通过在两齿轮工作表面处添加润滑剂,同时提高润滑油的黏度和油性,或在润滑油中加入极压添加剂,都能有效地减少磨损。对于因润滑油中混入有泥沙、尘土或因长期没有经过及时更换而导致轮齿工作表面产生的磨料磨损,可适当降低润滑油的黏度,从而对齿面上的磨粒有更好的清洗效果。当然,定时清除油中的沉淀物或更换润滑油,以及在润滑油的循环系统中安装过滤设备,也可达到良好的减轻磨损的作用。另外,润滑油中的一些添加成分或因油的变质,往往会使轮齿工作表面发生不同程度的腐蚀性磨损。如果极压添加剂过于活泼,会导致在齿面上形成的薄膜因摩擦作用而不断脱落,反而加速了齿面的磨损。为了防止磨料磨损,保持润滑油的洁净是非常必要的。油浴式润滑选用较低黏度的油,有利于磨粒的沉淀。循环式润滑系统中装置过滤器,并定期进行油质的净化处理,有的还安装磁性过滤器,用以清除油中的铁屑末,定期对润滑系统的油质取样化验,定期清洗换油。这些措施都是使润滑油保持清洁,以达到防止磨料状磨损的目的。
7.2 润滑对齿轮腐蚀的影响
齿轮腐蚀主要与齿轮工作环境有很大关系。其一,由于油中的冷凝水或者冷却热交换器中漏出水而引起;其二,由于润滑油中的酸或腐蚀添加剂引起齿轮腐蚀。为消除腐蚀磨损的发生,首先要根据齿轮自身材料或工作环境来考虑,通过某些油的添加剂阻止在齿轮表面生锈而达到防止腐蚀的目的;另一方面使用抗氧化性能好的油来防止酸的形成。
7.3 润滑对点蚀的影响
疲劳点蚀也是闭式齿轮传动中常见的一种接触疲劳现象。它是由于齿面长期在变化的接触应力条件下工作,而造成的在齿面间产生麻点状剥蚀损伤现象。点蚀大多先发生于轮齿靠近节线处的齿根面上,然后随着运动的进行,向其他部位扩展。点蚀的存在,往往会导致齿面的磨损,从而影响齿轮传动的精度和寿命,甚至会引发断齿,因此要加以避免。实践表明,齿根部分的齿面最易产生点蚀。其原因在于,此部分齿面上的滑动率为负,裂纹容易产生,再加上润滑油的渗透性,对裂纹有一定的挤胀作用,从而加速了裂纹的发展,于是就有金属块的脱落。一般而言,润滑油的黏度对点蚀的影响颇大。通常情况下,稀薄的润滑油比黏稠的润滑油更易渗透到裂缝中去,造成裂纹的扩展;黏度大的润滑油缓冲吸振性强,容易建立承载油膜,故润滑油的黏度越高,抗点蚀能力就越强。此外,润滑油的某些成分,如油性剂、极压添加剂等,往往会起到降低摩擦、增大边界油膜强度的作用,在一定程度也可以提高齿轮的抗点蚀能力。尽管如此,对添加成分的选择也应适当注意和小心。若油中存在有腐蚀性物质,如水分和氧化物,均会导致金属齿面形成锈蚀,从而引发裂纹。此外,油中的气泡也会造成金属过早地脱落。再有,加了极压添加剂的润滑油,对蜗杆传动的抗点蚀作用并不明显。综上所述,应从润滑油的黏度、添加成分的性能,如油性、极压性、氧化性、抗腐蚀性等方面进行综合考虑,尽量避免润滑剂对点蚀造成的负面影响,以提高齿面的抗点蚀能力。
7.4 润滑对胶合的影响
胶合是高速重载齿轮经常发生的一种破坏形式,主要是因两工作齿轮齿面间的压力大,瞬时温度高,润滑效果差,而造成两齿面黏结在一起形成的。影响胶合的因素很多,仅就润工业润滑油选用指南滑而言,润滑油的黏度、种类、润滑方式对其均有一定程度的影响。
一般的矿物油,由于不含油性剂和极压剂,主要依靠黏性在轮齿工作表面之间产生流体润滑膜来减轻并防止胶合的产生。这类润滑油黏度越大,防胶合性就越好。对于加入了油性剂的复合矿物油,由于油性剂分子的吸附作用,能形成比纯矿物油更为牢固的边界油膜,从而用以抵抗胶合发生。但是,当齿轮传递负荷较重时,轮齿处于高压边界和高温边界润滑,此时仅靠油性剂的物理、化学吸附的方法强化,油膜已不是可行的办法,需要油中含有极压添加剂,使用含极压添加剂的润滑油才能有效地防止胶合的发生。这种极压添加剂在齿轮处于高温、高压状态下,能释放出活性元素与金属铁迅速生成化学反应膜。这层覆盖油膜具有较高的强度,能承受较大的载荷,从而提高抗胶合能力。需要指出的是,激活极压添加剂需要较高的温度条件,为此对油中添加剂的活泼程度也有一定的要求,即添加剂应是活泼的,但又不应太活泼,否则油中的硫、磷、氯等活性物质将会对金属产生过度的腐蚀作用。故极压润滑油多用于重负荷的齿轮传动,而在非极压状况下则不宜使用。
润滑油的供给量和润滑方法对胶合的产生也有一定影响。一般是供油越充足,油的胶合极限负载可得以提高。但经实践表明,供油量多至一定程度时,这种情况将不再出现。如经过调质处理的直齿轮传动,其供油量达到0.8L/min,润滑油所能承受的胶合极限力矩为120N.m,当油量超过此值时,润滑油负载的胶合极限力矩值将不再增加。
油浴润滑和喷油润滑是齿轮传动中常用的润滑方法。循环式喷油润滑比灌注式油浴润滑的冷却效果要好,对抗胶合是有利的,而且在一般情况下从啮出侧喷油比啮入侧好。试验证明,从啮入侧喷油运行温度较高,从啮出侧喷油运行温度有所降低。通过采取某些措施,连续冲洗齿面,有效地降低齿面温度,这对防止胶合是很有必要的。从防止点蚀的角度出发,供油量不宜过多,但是为了防止黏着,又必须要有充分的供油位是统取得良好的润滑效果。
7.5 润滑对齿轮传动其他方面的影响
一般情况下,齿轮传动中由振动产生的噪声将随润滑油黏度的增加和供油量的加大有减小倾向,但从有关方面的试验结果来看,若润滑油黏度由50mm2/s增加到100mm2/s,齿轮运转噪声无明显变化;而若在润滑状态下继续增加供油量,其减小噪声的效果也不明显。正确的润滑方法也将在一定程度上起到缓冲吸振、减轻噪声的作用。一般而言,为保证啮合齿面间存在足够的润滑油,润滑油从啮入侧喷入比从啮出端喷入效果要好一些。
润滑对齿轮传动质量的另一影响是齿轮传动的效率。齿轮传动效率的损失,一方面来自轮齿间的摩擦,一方面来自对润滑油的搅拌。由摩擦学有关知识可知,齿轮处于液体润滑状态下工作是最为理想的,在此状态下,则油的黏度成为影响轮齿工作表面摩擦的最重要的特性。润滑油黏度越高,在两工作表面间产生的油膜就越厚,其抵抗磨损的能力就越强。但为了降低油中的内摩擦,往往又要求黏度应适当选低。针对这一矛盾,在对润滑油进行选择时应做到二者兼顾。然而,搅油功耗也与润滑油黏度有关。一般情况下,在转速相同的情况下,黏度越高,功耗越大。但是蜗杆传动却例外,因为在蜗杆传动中,轮齿的工作面间有相对滑动,传动摩擦大,齿面产生的温度高,而润滑油的黏度随温度升高会有所降低,故一般需用黏度高的润滑油。
在闭式齿轮传动中,若采用的是浸油润滑方式,当油面过高时,往往也会导致搅油功耗太大;油面太低,则会造成润滑不全面,故此齿轮的浸油深度应视齿轮的圆周速度而定,必要的时候,还应加设带油轮。
八、工业齿轮损伤防止措施
8.1 合理润滑
工业齿轮失效的原因主要涉及到齿轮副材料、表面加工处理、齿轮副加工精度、润滑油品的选用等多方面的因素。通常齿轮传动失效多发生在齿轮的轮齿处,造成齿轮失效的因素有很多,而润滑不理想则是最主要的因素之一。在工业应用的齿轮传动中,润滑不良造成的齿轮失效形式主要有以下几种:齿面擦伤、齿轮表面点蚀、齿面胶合、齿面塑性变形、螺旋和双曲线齿轮磨损失、蜗轮蜗杆磨损失效、开放齿轮磨损失效等。
合理润滑可以明显延缓或防止齿轮的失效。一般情况下,磨损是因为齿轮油极压抗磨性能不能满足齿轮润滑要求就会产生;点蚀是因为齿轮油润滑性能不足,防腐蚀性能差引起;而断齿与胶合主要是因为齿轮油量不足,或者是修理后齿轮的装配不良,如紧固螺钉柠得太紧,或者齿轮间隙调整不当等,很容易产生断齿或胶合,这种现象与齿轮油质量关系不是很密切。因此发生齿轮失效,一定要看失效形式,然后才能判断由什么原因引起。
齿轮油防止胶合、擦伤、波纹、螺脊、点蚀、剥落、抛光、磨粒磨损、腐蚀性磨损等损伤出现的能力叫做承载性或承载能力。齿轮油的极压性是指在摩擦表面的高温下,极压剂与金属反应生成化学反应膜的能力。化学反应膜可以防止出现胶合、擦伤、波纹、螺脊,减轻点蚀、剥落和磨粒磨损,但是化学反应膜的临界剪切强度低于基体金属,在摩擦过程中,化学反应膜不断被磨损掉而成为磨屑,所以化学反应膜的生成和磨损就是一种腐蚀性磨损。齿轮油的极压性强,表明油中的极压剂化学活性高,与金属的反应速度常数大,反应活化能低。在相同条件下,比极压性弱的齿轮油生成的化学反应膜厚。如果齿轮油的极压性太强,就会出现腐蚀性磨损,承载能力反而下降。
对齿轮润滑油黏度的选择要适当,如果润滑油的黏度太小,难以在齿的表面形成起到保护作用的油膜,齿面的摩擦力就会增加,磨损也加大。润滑油的油质要清洁,不能有杂质,使用时应进行过滤,剔除灰尘、砂粒、金属屑等。
8.2 做好散热
对封闭式齿轮来说,传动散热较为关键,应及时清扫齿轮箱,加强对齿轮箱的冷却、通风工作。加润滑油时,油量淹没大齿轮的1/3即可,注油量太多时,会增加齿轮的运行阻力,使内部发热。
8.3 避免超载
超载容易加大煤矿机械设备各传动系统的负荷,同样也能加大两齿面之间接触处的接触应力。动载荷增加时,易出现齿面点蚀现象。
8.4 及时检测
对齿轮传动的间隙、润滑接触面积、发热情况、响声等,要进行检测和判断,发现不正常应及时调整、更换,这样也可以避免齿轮失效的发生,延长其使用寿命,保证设备正常运转。
九、工业齿轮油选择
美国齿轮制造者协会于1994年发布了ANSI/AGMA 9005《工业齿轮的润滑》选用标准。该标准反映了当时工业齿轮润滑油的技术发展和应用情况。我国于2000年参照ANSI/AGMA 9005-D94标准,对原ZBJ 17003-1989标准进行了修订,修订后的标准为JB/T 8831《工业闭式齿轮的润滑油选用方法》,于2001年发布实施。JB/T 8831-2001标准规定了工业闭式齿轮润滑油的选用方法,包括选择润滑油的种类、黏度以及润滑方式。该标准适用于渐开线圆柱齿轮、圆弧圆柱齿轮及锥齿轮,适用于转速低于3600r/min、节圆圆周速度不超过80m/s的齿轮传动。
JB/T 8831-2001明确了了工业闭式齿轮油的种类、黏度以及润滑方式。
十、工业齿轮油更换
10.1 工业齿轮油的劣化
齿轮润滑油在使用过程中会逐渐变质、劣化,这主要表现在理化指标上发生变化。
10.2 工业齿轮油的换油指标
工业齿轮油更换与齿轮磨合情况、齿轮的载荷、齿轮油的种类和质量、润滑部位在机械中的重要性等均有关。一般来说,用油量较少的齿轮箱可根据实践经验定期换油。如AGMA规定正常情况下6个月换油。不与水直接接触的引进减速机使用说明书规定4000 ~5000h换油,因运转条件不同也有短至2000h、长至8000h的。用油多、消耗量大的大型齿轮装置集中润滑系统,由于定期补油,常根据油品变质情况按质换油。在通常情况下,工业齿轮油使用者主要根据腐蚀、锈蚀、沉淀、油泥、黏度变化和污染程度等情况,决定是否更换新油。为了定期进行质量监控,我国制定了CKC工业齿轮油的换油指标SH/T 0586《工业闭式齿轮油换油指标》。当有一项指标达到换油指标时,应更换新油。
十一、工业齿轮润滑故障及对策
详见《工业齿轮润滑故障及对策》一文。
更多油品信息请参考《工业润滑油选用指南》一书。