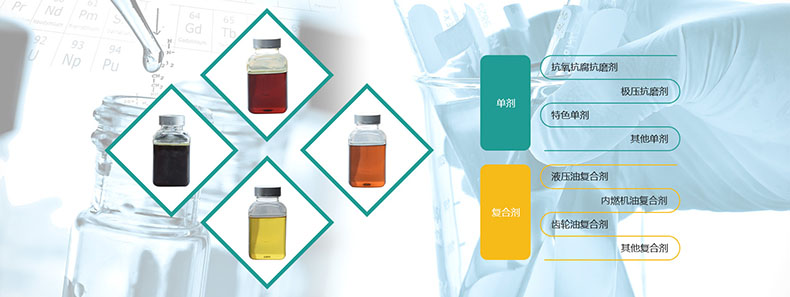
一、概述
作为润滑剂的重要组成部分,与基础油相比,添加剂在配方中占有的比例比较少,一般不超过25%。国内将添加剂按其功能一般分为两大类,非功能添加剂和功能添加剂。非功能添加剂主要指改善油品高低温流变及抗泡沫等润滑油通用性能的添加剂,如粘度指数改进剂、降凝剂、抗泡剂及抗乳化剂,其添加数量常要根据每批基础油的性能指标而随时调整;功能添加剂则指在润滑剂中强化或赋予某些方面特性的添加剂,如清净分散剂、抗氧剂、极压抗磨剂、油性剂、金属减活剂、防锈剂等。润滑剂的配方一经形成,功能添加剂的添加比例就随之确定,一般不再更改。
另外,一般将为调制特定油品预先配制的多种添加剂的混合物称为复合添加剂,也简称复合剂。复合剂分为内燃机油复合剂和工业润滑油复合剂,内燃机油复合剂中包括汽油机油复合剂、柴油机油复合剂、通用内燃机油复合剂、二冲程汽油机油复合剂、铁路机车用油复合剂、船用发动机油复合剂等,工业润滑油复合剂包括工业齿轮油复合剂、车辆齿轮油复合剂、通用齿轮油复合剂、液压油复合剂、汽轮机油复合剂和防锈油复合剂等。
世界润滑油添加剂消耗量随润滑油需求量的增长而呈稳定增长趋势。车用润滑油一般占润滑油总量的50%左右,而其添加剂用量则在80%以上,特别是其中的重负荷发动机油使用添加剂比例最高。车用润滑油消耗的功能剂包括清净剂、分散剂、抗氧剂、抗磨剂、摩擦改进剂等,非功能剂主要包括粘度指数改进剂、抗泡剂、降凝剂、破乳剂等。随着汽车工业的发展及其对润滑油需求的增长,轿车发动机油对添加剂的需求增长最快,但对清净剂和抗磨剂的需求增长相对缓慢。
二、添加剂的分类
国际上对石油添加剂没有统一分类,有的按油品的种类来分,有的按添加剂的作用来分,国外石油添加剂公司多自成体系。SH/T 0389《石油添加剂的分类》按应用场合将添加剂分为润滑剂添加剂、 燃料添加剂、 复合添加剂和其他添加剂四部分。 对一剂多用的添加剂, 按其主要作用或使用场合来划分。润滑剂添加剂详细分类见下图:
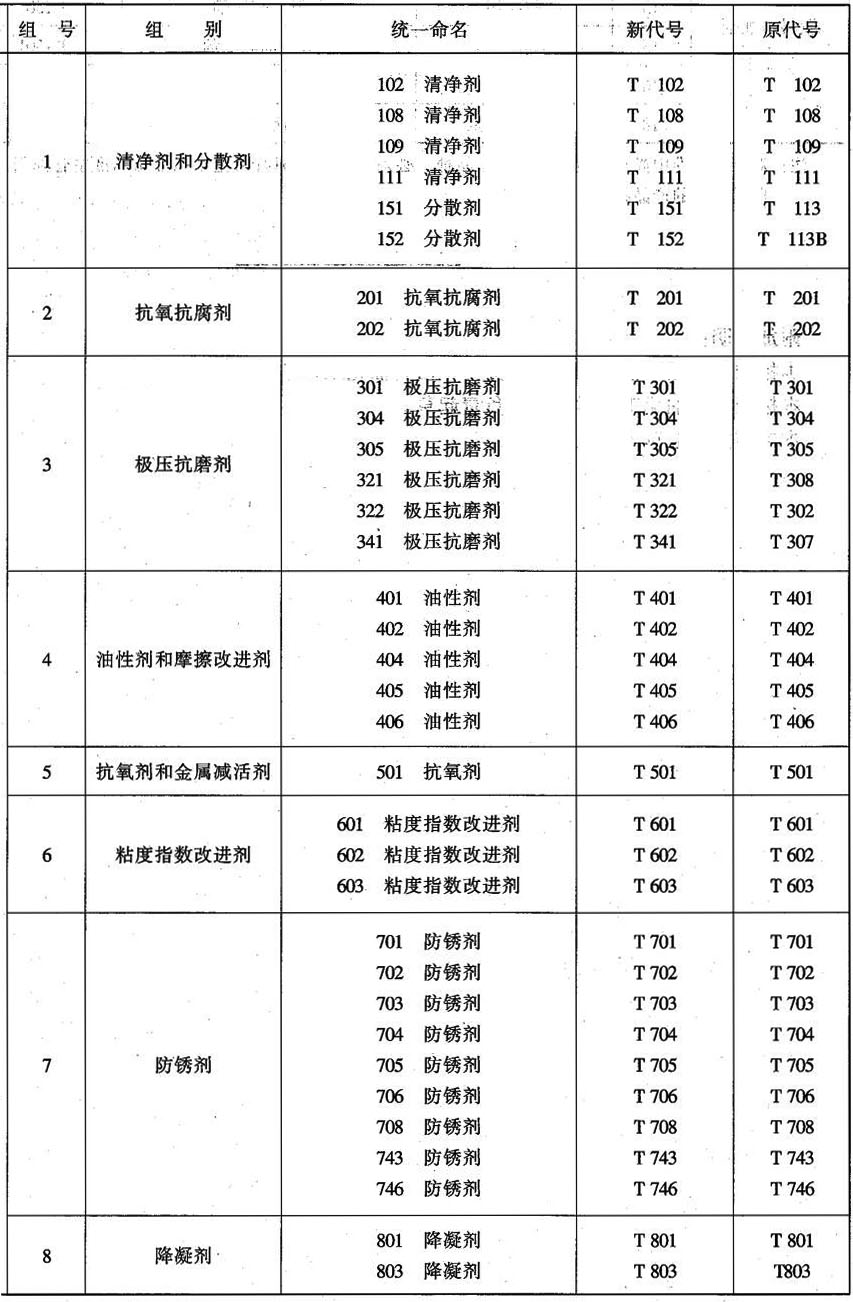
润滑剂添加剂详细分类
三、非功能添加剂
非功能添加剂在润滑剂中的比例高的可达5% ~15%,加量小的仅有10~30μg/g,无论加量大与小,其应用都非常广泛,如粘度指数改进剂是调制所有多级车用油及工业用油必备的组分,抗泡剂则应用于几乎所有的润滑剂产品之中。
1、粘度指数改进剂
在大跨度的多级油中,由于粘度级别跨度大,对其高低温性能要求较高,需要油品有较好的粘温性能,为此必须加人一定量的油溶性高聚物,以保证油品既要在较高温度下保持一定的油膜强度,又要在较低温度时具有一定的流动性。这类高聚物就是粘度指数改进剂。为了便于使用,粘度指数改进剂通常用100SN或150SN的基础油稀释为5%~ 15%的液胶。由于液胶中稀释油的含量较大,在应用于高档油品时,应选用质量优良的稀释基础油,以免对成品质量造成影响。粘度指数改进剂主要用于内燃机油、液压油、自动传动液和齿轮油中。粘度指数改进剂不仅能稠化基础油,改善油品的粘温性能,使油品具有良好的高温润滑性和低温流动性,而且可降低燃料和润滑油的消耗,实现油品通用化。在调制多级油时,粘度指数改进剂的加人量一般在10%左右,由于其用量很大,国内外各大润滑油公司和添加剂公司都对粘度指数改进剂的生产及发展非常重视。
粘度指数改进剂的作用与它本身的结构特点有关。粘度指数改进剂多是油溶性链状大分子聚合物,当其溶解在润滑油中时,很长的聚合物链在油中舒展成一个网,阻碍了油的流动,使粘度增大。当温度升高时,溶解度增大,聚合物链越发舒展,阻止油流动的阻力就越大,使得油在高温时仍具有较高粘度,当温度降低时,聚合物链就开始卷曲起来,形成小团,这样油品的流动就比较容易些,粘度增加较小,从而达到改善油品粘温性质的目的。
目前,国外最常用的粘度指数改进剂有氢化苯乙烯一双烯聚合物[如氢化一苯乙烯一丁二烯聚合物(HSB)、氢化一苯乙烯一异戊二烯聚合物(HIS)、氢化异戊二烯(HI)]、聚甲基丙烯酸酯(PMA)、聚异丁烯(PIB)、乙丙共聚物(乙烯丙烯共聚物,OCP)4大类。有资料显示,在全球粘度指数改进剂市场上,乙丙共聚物在世界市场上所占有的份额最大,为39%;占第二位的是聚甲基丙烯酸酯,为29%;苯乙烯一异戊二烯占第三位,为25%;苯乙烯酯和聚异丁烯各占约3%,富马酸酯约占1%。
国内的粘度指数改进剂的主要类型有聚乙烯基正丁基醚、聚甲基丙烯酸酯、聚异丁烯、乙丙共聚物、聚丙烯酸酯等,多功能粘度指数改进剂的发展也很快。
每一种粘度指数改进剂都有其优缺点,见下表。不同类型粘度指数改进剂在增稠、提高粘度指数、冷启动、泵送、剪切安定等性能方面各有长短,要根据所要调合油品的要求进行精心选择。聚异丁烯的增稠能力、低温性能和粘温性能差,多级油中已不再使用,聚甲基丙烯酸酯的抗剪切性能好,增稠能力差,且价格较高,乙丙共聚物增稠能力强,抗剪切性能差,但价格便宜,苯乙烯一异戊二烯共聚物的综合性能优异。
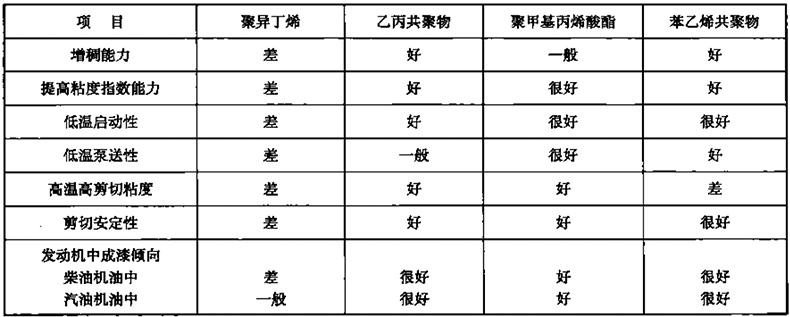
不同类型粘度指数改进剂的性能对比
当前粘度指数改进剂的发展趋势,不仅要求其能改善油品的粘温性能,使油品具有良好的高温润滑性和低温流动性,还要求油品在机械剪切力的作用下粘度损失适度,以及对油品的氧化安定性、清净性不产生明显的负面影响。目前主要采用共聚或接枝技术,进一步改善粘度指数改进剂的剪切稳定性、热氧化安定性和低温性能,或使其兼具有降凝或分散性能成为多功能添加剂。
1.1 乙丙共聚物
近年来各国对乙丙共聚物的研究重点是开发多功能的乙丙共聚物,将乙丙共聚物和PMA或HSB结合到一起,从而改进它的各种性能。目前,据文献报道乙丙共聚物有非分散型、分散型和分散抗氧型三种。
1)非分散型乙丙共聚物
非分散型乙丙共聚物粘度指数改进剂(也称乙丙胶或OCP)为浅黄色透明粘稠液体,能改善油品的粘温性能,提高粘度指数,其增稠能力强,但低温流动性稍差。目前,国内采用降解法生产非分散型乙丙粘度指数改进剂的工艺已经相当成熟,但产品质量不易控制,并且原料成本价格较高,从而制约了此类粘度指数改进剂的发展。
乙丙胶中含乙烯、丙烯的比例不同,生产出的粘度指数改进剂性能也不同。当乙烯含量过高时,油溶性变坏,低温下形成凝胶,但有利于提高粘温性能,当丙烯含量过高时,使其增粘能力降低。因而这两种单体比例应适当,一般乙烯:丙烯(质量比)为40: 60或50:50,聚合物结晶度不高于15%。非分散型的乙丙共聚物又可以分为无定型OCP,半结晶型OCP和结晶型OCP。
20世纪60年代末、70年代初美国几大公司及意大利Agip Petroli等公司先后成功地开发出乙丙共聚物粘度指数改进剂,其产品除具有高稠化能力、较好的剪切稳定性等特点外,又因其生产原料来源丰富、生产工艺简单、产品价格相对便宜、综合性能较好而得到广泛的应用。如牌号为ECA9291的粘度指数改进剂其柴油喷嘴剪切稳定性指数SSI为50左右,基本为无定型的高聚物,其乙烯含量为40% - 50%,国内此类产品牌号为RHY-612。随后,为了适应剪切稳定性的要求,很多国内外厂家生产出了SSI为35左右的无定型OCP,国内此类产品牌号为RHY-613。随着欧美规格对SSI为25或更低的粘度指数改进剂的需求,许多添加剂厂家生产出SSI为25或更低的粘度指数的无定型OCP,国内产品牌号RHY-614 和RHY-615。有文献对各种无定型OCP的各项性能进行对比,发现无定型的OCP要改善剪切稳定性就要降低相对分子质量,因而增稠能力随之下降,加入量增多就会使内燃机油的清净性变差。特别是SSI为25的产品,加入量增加不仅会使清净性变差,而且低温性能也会变差。
20世纪80年代有人研究过半结晶型OCP,主要是提高OCP中的乙烯含量到70%以上,这样使OCP具有部分结晶,从而达到在改善剪切稳定性的同时,改进增稠能力和低温性能。具有相同SSI的半结晶型OCP的增稠能力比无定型的高很多,产品主要有润英联的Infineum V8800, V8700, V8600,目前仅限于在国外基础油中使用。因为我国目前主要广泛使用的基础油为含蜡量高的基础油,而这种半结晶型的OCP由于乙烯含量高因而有结晶,因此对含蜡高的基础油的倾点及低温性能均有影响,也和某些降凝剂如T803互相有影响,因此在国内的应用比较少。
20世纪80年代百润敏研究开发了一个新的结晶型OCP粘度指数改进剂,可以使乙烯集中在分子的中间,而丙烯则在分子的两端。这种粘度指数改进剂比起半结晶型OCP的增稠能力与低温性能都得到了很大的改善。目前,国外此类产品有SSI为50和37两种结晶型OCP,其增稠能力比无定型及半结晶型OCP大大增加,并且低温性能也有所改善,但目前还不能生产SSI为25的OCP产品,因此在国外只在汽油机油中使用。并且也存在因为结晶型OCP的结晶太强,在含蜡基础油中与降凝剂的配伍性的问题。
2)分散型乙丙共聚物
由于发动机技术的发展,对添加剂要求越来越高,添加剂用量也大大增加。如果一种单一添加剂能提供多种作用以满足发动机油的要求,则润滑油中的添加剂加人量将明显减少,因此各大公司均在研究多效添加剂。分散型粘度指数改进剂的优点是具有改进粘温性能和分散性能两种作用,即除保持其原有粘度指数改进剂的特征外,还可代替一部分无灰分散剂,若使用分散型粘度指数改进剂,分散剂的用量将减少,这样对低温粘度的影响变小,从而可以使用更重一些的基础油,反过来又改进了油品的使用性能。
为了充分利用乙丙共聚物的特点,同时赋予它新的性能,20世纪70年代末,首先由Rohm & Hass公司推出新一代的分散型乙丙共聚物粘度指数改进剂,随后多家公司又先后推出了不同结构的分散型乙丙共聚物粘度指数改进剂。在国外分散型乙丙型粘度指数改进剂占粘度指数改进剂销售份额的一半(以美国为例),而国内高档润滑油用的分散型乙丙共聚物大部分依赖进口。
3)多效乙丙共聚物
在分散型乙丙共聚物的领域中,更为活跃的工作是研究多效剂,即除了分散性外,还赋予抗氧和(或)抗磨性,多效粘度指数改进剂几乎与多效无灰分散剂同步发展。目前已有3种形式的混合OCP工业化,即分散型OCP、分散抗氧型OCP和接枝有PMA的OCP。
1.2 氢化—苯乙烯—双烯共聚物
氢化苯乙烯异戊二烯共聚物为无定型聚合物,可用在高蜡基础油中。同时SSI达到25%时,其用量很低,增稠能力很好,低温性能也不错,因而是新一代有前途的粘度指数改进剂。氢化一苯乙烯一双烯共聚物一般为白色粒状或片状固体,为苯乙烯与丁二烯或异戊二烯通过阴离子聚合,再催化氢化,使其双烯单体中的剩余双键饱和,以提高热氧化安定性。
氢化一苯乙烯一双烯聚合物有无规、嵌段和星状等不同的结合方式。无规共聚物的组成为50% ~60%的苯乙烯和40%~50%的丁二烯。嵌段共聚物有A-B两段和A-B-A三段结构两种。A为聚甲基丁二烯,B为聚苯乙烯,由于聚苯乙烯链段油溶性较差,因此嵌段共聚物只适用作助增粘剂。星状共聚物是以苯乙烯为核心,聚合度为5~15的甲基丁二烯由枝杈形成的,相对分子质量为(30~70)×104,相对分子质量分布低于1.5。
氢化苯乙烯一双烯聚合物的稠化能力和剪切稳定性都较好,能满足多级内燃机油的要求,特别是配制大跨度的多级内燃机油;但低温性能较差,并且价格较贵。近年来有文献报道此类粘度指数改进剂的高温高剪切粘度较低,难以满足低粘度多级内燃机油对高温高剪切粘度的要求。
氢化一苯乙烯一双烯共聚物主要由Shell公司研究开发,近几年来主要围绕引人功能基团使聚合物具有分散性能进行。目前星状共聚物主要包括加氢的聚异戊二烯和加氢的聚异丁烯嵌段。
1.3 聚甲基丙烯酸酯
聚甲基丙烯酸酯具有良好的粘度指数提高性能、低温性能,同时可通过调整相对分子质量赋予其降凝效果而得以广泛应用。采用不同碳数的甲基丙烯酸烷基酯单体,在引发剂和相对分子质量调节剂存在下通过溶液聚合制备。如烷基碳链足够长,可兼有降凝作用,与含氨极性单体共聚则具有一定的分散作用,在多级油中可降低无灰分散剂用量。用于配制多级内燃机油的PMA,相对分子质量一般为15x10左右。相对分子质量为(2~3)x104的PMA,可配制低温性能极好的液压油、多级齿轮油、数控机床油、自动传动液等。PMA的增粘能力较差,不适合单独配制多级柴油机油,但由于其低温性能好,较适合配制低粘度级别的多级汽油机油(如5W-20,5W-30)。
聚甲基丙烯酸酯是很早引入内燃机油中的,作为粘度指数改进剂,其低温泵送性好,但是由于其增稠能力差,加入量很大,因而对清净性的影响太大,同时低温CCS也一般。有的公司为克服这一弱点,将其与乙丙共聚物结合使用,有些改善,但仍未根本克服它的缺点,在内燃机油中使用较少,但它在液压油及齿轮油中广泛使用。
2、降凝剂
降凝剂就是能够降低润滑油凝点和倾点的添加剂。润滑油降凝剂的品种很多,综合国内外的研究和实践,对于基础油感受性较好的大致有聚酯、聚烯烃和烷基萘三类。聚酯类(Polyester)有聚甲基丙烯酸酯、醋酸乙烯酯/反丁烯二酸酯共聚物等,聚烯烃类(Polyolefin)有聚a-烯烃(Poly-a-olefine)、烷基化聚苯乙烯等,烷基萘(Alkynaphthalene)主要是氯化石蜡和萘的缩聚物。
聚甲基丙烯酸酯可用于各类润滑油,与其他添加剂复合配伍性好,但因为其结构中含有极性基团,对油品(如变压器油)的电器性能有一定影响,烷基萘降凝剂原料易得,制备工艺简单,但对于深度脱蜡油的降凝效果较差,而且颜色较深,影响油品色度,聚a烯烃降凝剂原料易得、工艺较简单,是一种浅色降凝剂,其降凝效果与聚甲基丙烯酸酯相可用于各类润滑油品,并兼有一定的增粘作。
降凝剂是通过其分子上的烷基链与蜡共晶或芳香核的吸附而起到降凝作用,因而其化学结构对降凝剂的降凝效果具有决定性的影响。由于油品中固体烃组成复杂,结晶范围较宽,因而具有不同侧链长度和结晶温度的降凝剂结构,较具有单一烷基侧链和结晶温度的结构具有较好的降凝作用和不同油品的适应性。鉴于此,一般均采用几种不同碳数的单体共聚,并调整侧链的平均长度,以适应不同脱蜡深度制取的各种粘度和来源的基础油。
降凝剂的降凝效果与基础油的性质密切相关,特别是凝点和粘度。另外,基础油的烃族组成对降凝剂的感受性也有明显的影响,烷烃和环烷烃对降凝剂的感受性最好,少环长侧链的轻芳烃有一定的感受性;而中、重芳烃和胶质对降凝剂无反应,这些重组分在油中达到一定浓度后,可使降凝剂完全丧失降凝作用。此外,润滑油馏分轻重也会影响到对降凝剂的感受性。
基础油的组成性质不仅影响降凝作用,对凝点的稳定性也有一定影响。所谓凝点稳定性,是指加有降凝剂的某些油品,经过长期储存后,能够保持其凝点不回升的性质。当然,凝点回升也和降凝剂有关,一般来说加有烷基萘的油品凝点稳定性较差,而加有聚甲基丙烯酸酯和聚a-烯烃的油品凝点则比较稳定。国内常用降凝剂见下表,目前的研究主要集中在聚甲基丙烯酸酯和聚烯烃类。
类型 | 烷基萘 | 醋酸乙烯酯与丁二酸脂共聚物 | 聚α烯烃 | 聚甲基丙烯酸酯 |
国内牌号 | T801 | T802 | T803、T803A | T602 |
2.1 聚甲基丙烯酸酯
聚甲基丙烯酸酯是一种高效浅色降凝剂,对各种润滑油均有很好的降凝效果。作为降凝剂其烷基侧链的平均碳数要在12以上才显示降凝效果,以14酯的效果最好。为了适应不同脱蜡深度制取的各种粘度及倾点以及不同油源的润滑油,调整烷基侧链的平均碳数,生产出系列的降凝剂产品来满足油品的要求。聚甲基丙烯酸酯是目前研究最感兴趣的领域,也是应用最广泛的降凝剂。
2.2 聚a-烯烃
聚a-烯烃降凝剂颜色浅,效果好,可适用于各种润滑油中,其效果与PMA相当,但价格比PMA便宜。聚a-烯烃降凝剂可根据烷基侧链的平均碳数不同和相对分子质量大小生产一系列产品。
3、抗泡剂
能够改善润滑油泡沫性能,包括发泡性和泡沫稳定性的添加剂称为抗泡剂,也称消泡剂。
润滑油在使用过程中,受到高速搅拌或不同压力的循环扰动往往会产生泡沫,引起润滑油供给中断、润滑性能变差、冷却效果显著下降、机械振动发出异常噪音等不良后果,为解决润滑油在使用过程中这种问题、最简单有效的方法就是使用抗泡剂。
抗泡剂从原理上说,可分为破泡剂和抑泡剂。破泡剂是破除已经形成的泡沫,使泡沫变小、减少,以致消失;抑泡剂就是能够阻止泡沫的生成。在多数情况下,两者兼而有之且很难区别,所以统称为抗泡剂。
抗泡剂产品多种多样,但选择性很强,往往在一种体系中能消泡,而在另一种体系中却无效果或效果很差,甚至发泡。在润滑油体系中,使用最广泛的是聚甲基硅氧烷类抗泡剂,也称为硅油,其次是近年来使用越来越多的聚丙烯酸酯型非硅抗泡剂。
3.1 硅油
硅油是一种无色无味的油状液体,它具有化学稳定性高、凝点低、挥发性小、添加量少、抗氧化与抗高温性能优良等优点,是使用范围最广的一种润滑油抗泡剂。硅油在润滑油中处于不溶解的均匀分散状态,才具有抗泡性。分散在油中的硅油粒子越小,抗泡效果越好,抗泡作用的持续时间越长,因为小颗粒的硅油粒子在被分散体系中比较稳定,不易聚集、沉降而失效。将硅油以尽可能小的粒径分散于润滑油中,普遍使用的方法有:(1)将硅油溶解于煤油、轻柴油等溶剂中,配成硅油母液,然后在搅拌下加入润滑油中。硅油在溶液中的浓度越低,分散于润滑油中的硅油粒子越小,消泡效果越好。通常配制的硅油浓度在5%~10%(质量分数)。(2)用特殊机械(如胶体磨)将硅油制成母液再加人到油品中。在使用硅油抗泡剂时,应根据油品的轻重选择适当的硅油牌号,否则就得不到好的抗泡效果。一般来说,粘度小的硅油适用于粘度较大的润滑油,粘度大的硅油适用于粘度较小的润滑油。此外,还应注意的是,在发泡倾向和泡沫稳定性这两个不同的特性上,高粘度硅油和低粘度硅油的表现相反。因此,在实际应用时,常将低粘度硅油和高粘度硅油混合使用,如T901就是粘度(-25℃) 100 ~ 1000的混合物。
需要特别注意的是:硅油抗泡剂对调合技术十分敏感,硅油的加人方法不同时,发泡倾向和泡沫稳定性会有很大差异。其次,硅油在酸性介质中不稳定,与酸性添加剂复合使用时会削弱甚至失去抗泡性。因此如何将硅油以尽可能小的粒径分散于润滑油中是抗泡剂在实际应用中的技术关键,国内外对此都作了大量的研究工作,其中效果较好、使用比较普遍的有如下几种方法。
1)将硅油配成溶液加入油品中:将硅油溶解于煤油、轻柴油、溶剂油等溶剂中,配成硅油溶液,然后在搅拌下加入润滑油中,硅油在溶液中的浓度越低,分散于润滑油中的硅油粒子越小,消泡效果也越好。 这一方法虽然比较简单,但在工业生产中要进行高速搅拌难以实现,只在某些中型生产装置上才可行。
2)用特殊机械将硅油抗泡剂制成母液再加入油品中:将高浓度的硅油溶液(比如10%的煤油溶液)加入少量基础油料中,再用胶体磨制成硅油母液,然后按需要量将母液加入油品中。或将硅油直接加入少量基础油中,使用高速乳化混合机制成母液再加人油品中。该法的优点在于硅油抗泡剂的加人不需要辅以任何溶剂,这对于某些严格控制溶剂加人的油品具有重要意义。
3)将硅油制成消泡剂加入润滑油中:将硅油与各种分散稳定组分,按最佳配方混合,然后经胶体磨等加工工艺制成硅油消泡乳剂,用于内燃机车液力传动油,提高了硅油的消泡效果及其持久性。
4)将硅油与适当的表面活性物质复合使用:将某些极性物质或表面活性物质如高级醇、酯、有机胺等与硅油同时加人油品中,可以显著地提高硅油的抗泡持久性。
以上四种硅油加入方法中,将硅油配成硅油溶液或再辅以少量活性物质助剂,再在一般搅拌下加人润滑油中较好,它具有操作简便、实用,不需要特殊机械加工硅油溶液或母液的特点。只要硅油粘度选择适当,硅油溶液的浓度足够低(溶液的选择和加入量以不影响油品其他性质为前提),就不难获得较满意的抗泡效果,它特别适用于工业生产,近年来,国外也有这方面的论文和专利发表。
3.2 聚丙烯酸酯型抗泡剂
聚丙烯酸酯型抗泡剂具有对调合技术和酸性介质不敏感、长期储存稳定性好的优点,因对空气释放性能无影响而广泛用于液压油、汽轮机油。目前,在国际市场上出售的英国Edwin-Cooper公司的PC1244和路博润生产的LZ 889A即属这类抗泡剂。我国在20世纪80年代以后也开发了这类添加剂(T911,T912),经过实际应用证明了这类抗泡剂具有对各种调合技术和酸性介质不敏感,对空气释放值的影响比硅油小和长期储存后抗泡性不下降、稳定性好等优点。
将聚丙烯酸酯抗泡剂用于液压油等油品中,具有比硅油抗泡剂好的空气释放性,这对解决液压系统因油中气泡引起的噪声和振动有重要意义。
聚丙烯酸酯型非硅抗泡剂的出现,增加了润滑油抗泡剂的品种,提供了根据各种润滑油的特性选择不同抗泡剂种类的可能性,有时将两类抗泡剂复合使用会得到更好的效果。需要注意的是,该剂不能与T601,T705、T109等添加剂复合使用。
国内外主要的商品抗泡剂类型、牌号、化学名称、主要性能见下表。
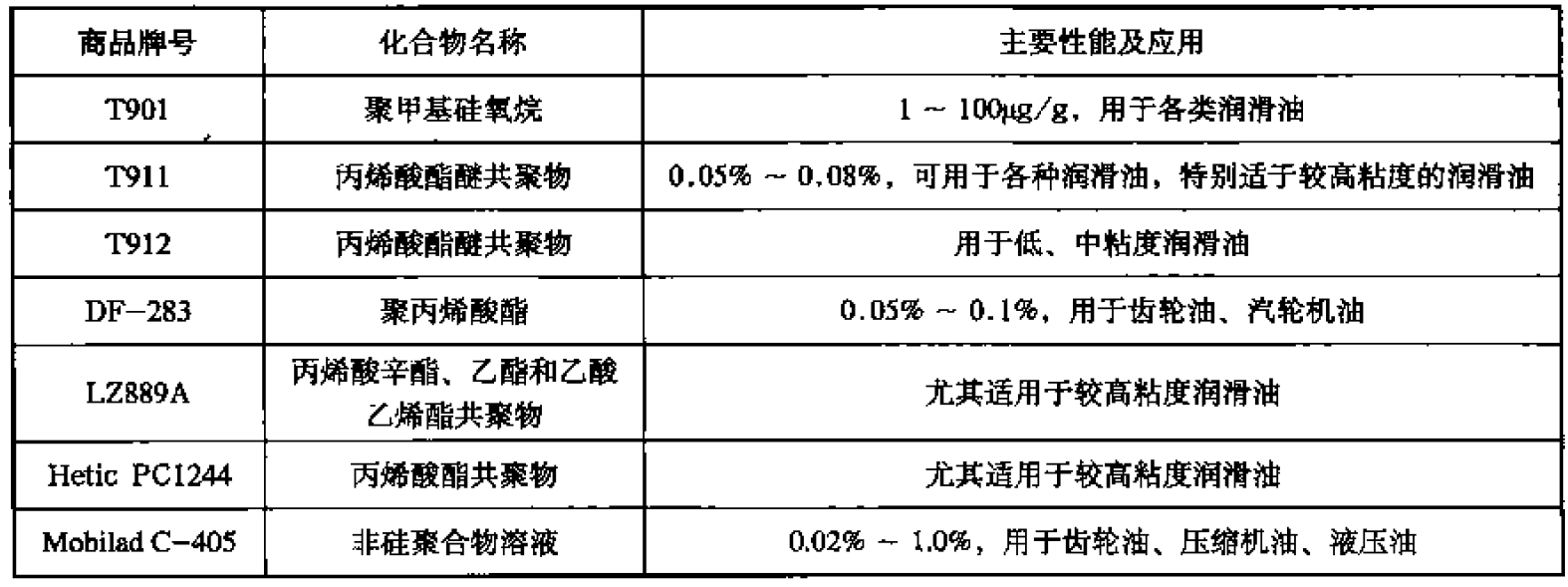
抗泡剂类型、牌号、化学名称、主要性能
4、破乳剂
能够减弱、消除润滑油的乳化现象的添加剂称为破乳剂。润滑油尤其是工业齿轮油、汽轮机油、液压油等在使用过程中难免与水接触,水会以细小的粒子均匀分散到油中形成油包水型(W/O)乳化液,使润滑油的润滑作用受到削弱甚至丧失,机械发生磨损。
从润滑油的组成上看,导致乳化的潜在因素是三方面:(1)润滑油基础油中的极性物质,如胶质、沥青质等;(2)某些清净分散剂、防锈剂、极压抗磨剂等具有表面活性而起着乳化的作用;(3)油品在使用过程中因氧化衰变而产生极性物质,如羧酸、酯类等。在这三种因素中,第一种因素可通过提高基础油的精制深度来预防,后两种因素只能通过添加破乳剂来消除。
加入破乳剂,会使润滑油与其中水的界面张力增大,分散状态从热力学上的稳定态向不稳定态转化即从油包水型(W/O)向水包油型(O/W)转化,细小的水粒子从分散状态重新聚集,并从油中沉降出来达到破乳化的效果。
针对船用润滑油的特点,国内开发了一种多单体合成的油溶性聚醚类高分子化合物破乳剂DL-32,用于添加剂量大、破乳要求高的船用油时效果非常明显。添加少量后不仅能延长船用油的寿命,破乳指标达到先进水平,而且能增强其他助剂在船用油中的作用,同时具有消泡作用。DL32在润滑油中的抗乳化能力与T1001相当,在抗磨液压油中优于T1001,油溶性好于T1001,这便于润滑油在常温下添加抗乳化剂,有利于在无加热条件下使用,加剂量约0.02% ~1%。
四、功能添加剂
功能添加剂,顾名思义是在润滑油基础油之上强化或提供某些功能的添加剂,各种功能添加剂的开发及其相互配伍规律的研究是润滑油及其添加剂业务的核心。最常用的功能添加剂有清净分散剂、抗氧剂、极压抗磨剂、金属减活剂、防锈剂等。
1、金属清净剂
金属清净剂是内燃机油的重要添加剂,是用量最大的一种润滑油添加剂,在有的油品(例如船用气缸油)中用量可达10%~15%,其功能主要是中和油品燃烧和衰变生成的酸性物质,并防止金属表面生成漆膜积炭。
金属清净剂的发展始于20世纪30年代中期,到了50年代,由于大功率增压柴油机及船用柴油机开始采用高含硫燃料,为解决活塞积炭较多和缸套腐蚀磨损等问题,开发出了含有碱金属(呈胶态碳酸盐)、易溶于正盐中、金属含量高的“过碱度”和“高碱度”金属清净剂,如低、中、高及超高碱值的磺酸盐、烷基酚盐、环烷酸盐及烷基水杨酸盐产品,以适应各级油品的质量要求。进人80年代,一些性能优异的水杨酸盐、新型酚盐和低灰分高性能的镁盐等相继被开发并且逐渐投入使用。新世纪以来,国内润滑油添加剂产品品种也获得发展,在润滑油升级换代的推动下,水杨酸盐、磺酸盐和环烷酸盐金属清净剂产品的性能逐渐接近美日等发达国家水平。
金属清净剂在润滑油中主要有增溶、胶溶、酸中和、清洗等几方面作用。(1)增溶作用:借助表面活性作用使润滑油氧化及燃烧不完全而生成的不溶物增溶于油内,由于这种增溶作用降低了它们的活性,抑制其生成漆膜、积炭和油泥等沉积物的倾向。(2)胶溶作用:清净剂吸附于金属表面形成一层覆盖膜,从而阻止胶质及烟灰粘附于金属表面上,或是清净剂吸附于烟灰及其他非油溶性的固体粒子表面,成为一种覆盖膜,从而阻止它们聚集成更大颗粒沉积在金属表面。(3)酸中和作用:清净剂的酸中和作用包括多方面,其一为中和由润滑油氧化和燃烧不完全而生成的酸性氧化产物或酸性胶质,使其失去活性而变为油溶性,其二为中和含硫燃料燃烧生成的SO2、SO3,进而生成的硫酸,以抑制其促进烃类氧化生成沉积物的作用;其三,也抑制这些酸性产物对活塞环及缸套间的腐蚀磨损作用。(4)清洗作用:清洗作用可以看做是清净剂增溶、胶溶、中和等机理的综合表现,通过润滑油的润滑冲洗,使这些被增溶、胶溶和中和的物质离开摩擦副表面,回到曲轴箱或被过滤器滤除,以保持摩擦副的清洁光滑。
金属清净剂按不同有机官能团基质可分为烷基苯磺酸盐、烷基水杨酸盐、硫化烷基酚盐、环烷酸盐、硫磷酸盐以及其他羧酸盐,按不同的碱性组分可分为钡盐、钙盐、镁盐、钠盐等,分别制成低碱性、中碱性与高碱性,而以高碱性钙盐的用途最为广泛。纵观国内外润滑油的发展形势,新型清净剂需要具备三个方面的优势:一是综合性能好,可通用于各类高档油品配方,二是在中性盐保持一定含量时有效碱值高,能降低在油品中的加人量,达到减少消耗、降低成本的作用,三是低灰分、无毒性,减少对环境的污染及危害。
近二三十年来,金属清净剂种类并无太大变化,行业内对于金属清净剂高碱度化机理及其作用原理的认识基本成熟。原料与工艺的模式化使得产品质量与性能在短时期内难以上升到新的高度,但各大公司对提高产品质量的工艺和原料优化等的研究工作并没有停止,特别是内燃机油的低灰分化对清净剂的性能提出了新的要求,清净剂主要是向高碱度化和多元化方向发展。成磺酸盐的发展重点在于提高磺酸盐的碱值,目前已经开发出TBN(总碱值)400mgKOH/g产品, TBN 高达 500 mgKOH/g的产品也已见诸报道。水杨酸盐也从中碱值提高到TBN 300mgKOH/g的钙盐和TBN 400mgKOH/g镁盐,目前还在开发高碱值的钠盐、镁/硼、钙/硼复合盐等系列产品。随着汽车工业的发展,对润滑油清净剂提出了多功能化的要求,推动着复合多效清净分散剂的开发,复合多效清净剂是润滑油清净分散剂发展的重要方向,除了金属的多元化,基质也开始朝着多元化的方向发展。
一般地说,金属清净剂的制备工艺主要有无溶剂工艺、烷氧基化工艺和碳酸化工艺三种。提高稳定性及胶体分散性,简化工艺,提高产品过滤速度是合成工艺的关键点,具体的制备方法是各公司的核心技术,保密非常严格。无溶剂工艺,是烷基酚作为“促进剂”与水合氢氧化钡反应生成中间产物,溶解并分散于反应介质中,实现从固相到有机相的转移。中间产物在CO2作用下生成碳酸钡及烷基酚,碳酸钡聚集生长到一定程度后,将被表面活性剂包围,形成载荷胶团。离心或过滤反应体系中未反应或粘度较大的固体颗粒后,即得到胶体分散的碳酸钡型清净剂。反应过程中持续通人CO2,直至固体氢氧化钡反应殆尽,而烷基酚则得以循环利用。烷基酚钡及硫磷酸钡盐制备工艺均属此列,该工艺过程简单、不使用溶剂、成本低。烧氧基化工艺,作为一种制备碳酸镁型清净剂的可行工艺,多年来一直受到人们的高度重视。在反应过程中,金属镁与烷氧基醇反应得到可溶于油相的烷氧基镁化合物,在CO2作用下形成中间产物,可以稳定地存在于油相中,在水作用下,水解生成碳酸镁及烷氧基醇。碳酸镁胶核与表面活性剂形成稳定的胶体粒子,烷氧基醇也得以循环使用。该工艺由于使用金属镁及烷氧基醇,成本高、难以工业化。
碳酸化工艺,以金属氧化物作为起始原料的碳酸化工艺是现实中主流的生产工艺。
在润滑油金属清净剂中,磺酸盐、硫化烷基酚盐、水杨酸盐占绝大多数,目前仍然保持强劲的发展势头,环烷酸盐因其扩散性较好多用于船用气缸油。
1.1 烷基酚盐
烷基酚盐是20世纪30年代后期出现的润滑油清净剂之一,并被迅速制成各种衍生物,如硫化烷基酸盐、甲醛缩合烷基酚盐、胺甲醛缩合烷基酸盐(曼尼希碱)等。现代各种发动机油所使用的烷基酚盐清净剂大多为中高碱性多功能团烷基酸盐产品,如近年开发出了耐热性、耐负荷性和清净分散性更好的中高碱值的硫化烷基酚盐。迄今关于硫化烷基酚盐的组成结构及性能改进的专利还一直不断出现,例如通过改变硫含量及与经基的联结方式、烃基结构特征、碱性组分的含量以及与其他组分复合来改进各种使用性能。
在使用方面,虽然酚盐的酸性较弱,制备高碱性产品也不容易,但它在油中较易分解、具有较强的中和能力,同时抗氧、抗腐蚀性能较好,与磺酸盐的协和效应较佳,尤其还可与磺酸盐的许多性能进行互补。目前,超高碱值(TBN>400的产品已见诸报道)和高碱值硫化烷基酚钙添加剂主要用于船用油,也可以与其他单剂复配调制车用内燃机油,如用超高碱值的硫化烷基酚钙金属清净剂与聚异丁烯丁二酰亚胺无灰分散剂、抗氧剂、ZDDP抗磨剂等组成的复合剂,可调制SC/CC,SG/CD级内燃机油,生物降解性能超过传统酚盐
1.2 磺酸盐
磺酸盐添加剂由于原料易得、成本低,而使用性能可以适应各种不同要求(如低碱度磺酸盐分散作用好,而高碱度磺酸盐具有特优的中和能力及高温清净性,所有的磺酸盐又均具有一定的防锈性能等),因此应用广、发展快,形成了低、中、高、超高不同碱值及钡、钙、镁、钠不同金属以及两种以上金属复合的系列化产品。
磺酸盐添加剂的高温清净性和低温分散性介于烷基水杨酸盐或硫化烷基酚盐与丁二酰亚胺之间,尤其是所有的磺酸盐添加剂的抗氧抗腐性都很差(高碱度磺酸盐添加剂甚至还有促进氧化的作用)。因此现代发动机油除了将不同高、低碱度的磺酸盐复合外,更主要的是将磺酸盐与硫化烷基酚钙及丁二酰亚胺等清净分散剂以及其他添加剂(如ZDDP抗氧抗腐剂等)复合使用。磺酸盐的生产工艺在金属清净剂中的研究最为领先,其制备工艺大体可以分为:原料的制备、磺化、金属化(包括高碱度化)、产物分离精制等几个步骤。磺化工艺比较简单,般是芳烃与浓硫酸进行磺化反应即可。许多公司生产合成磺酸盐时,实际采用的烷基原料包括蜡裂解a-烯烃(C16 - C20)、聚乙烯(C20 ~ C24)、八聚丙烯(C24)等原料,均可制得性能较佳的产品。随着加氢工艺的普及,石油磺酸原料越来越少,合成烷基苯磺酸已成为研制磺酸盐添加剂的主要原料。低碱度磺酸盐对烟灰的分散能力比较好,高碱度磺酸盐具有较好的酸中和能力和高温清净性,二者仍是近年来的研究重点。
1.3 烷基水杨酸盐
烷基水杨酸盐是20世纪40年代初出现的润滑油清净剂之一,从一开始就被高度重视并于50年代初被大规模工业生产和实际应用。由于该剂具有良好的高温清净性,酸中和能力、较好的热稳定性以及一定的低温分散能力和抗氧抗腐蚀性能,它的使用对于保证发动机内部清净、减少积炭、延长发动机寿命起到重要作用,因而被广泛应用于内燃机润滑油领域。尤其是随着润滑油向高档化的发展,提出了低硫、低磷、低灰分等需求,与磺酸盐,硫化烷基酚盐、硫磷酸盐等相比,烷基水杨酸盐具有不可替代的优势。烷基水杨酸盐产品是在烷基酚上引人羧基,并将金属由羟基位置转到羧基位置。这种转变使得其分子极性极强,高温清净性大为提高,已形成了低、中、高、超高等不同碱值及不同金属(钙、镁)的系列化产品。然而传统的烷基水杨酸盐制备过程比较复杂,从苯酚和a-烯烃开始制备烷基水杨酸盐共分为七步反应、十多道工序,生产过程和原材料的控制困难,导致产品色泽较深、生产成本过高以及污染严重,影响了产品的推广使用。近年来,国外烷基水杨酸盐系列产品得到了快速发展,其合成方法也不断被改进和更新
硫化烷基水杨酸盐添加剂是国外20世纪80年代研究开发出的一种新型的金属清净剂,具有优异的耐热性、高温清净性、良好的极压抗磨性、抗氧化安定性,并兼有一定的低温分散性,是一种性能全面的润滑油添加剂。该类产品与磺酸盐、低碱值烷基水杨酸盐等具有良好的复合作用,可广泛应用于不同档次的内燃机油中,有着很好的发展前景。
超高碱值烷基水杨酸钙的碱值可高达350mgKOH/g以上,除具有优异的高温清净性能外,还明显提高了油品的酸中和能力,而且在保证油品碱值相同的情况下,能明显降低添加剂在油品中的加人量,节约加剂成本,可广泛应用于不同档次的内燃机油中。
近年来对硼酸盐型清净剂、超高碱值烷基水杨酸镁盐及混合基质产品的研制也取得了重大进展,有望成为未来金属清净剂发展的主流。尤其是混合基质清净剂的研制,可成功地将磺酸盐与水杨酸盐在反应初期溶为一体,使烷基水杨酸与烷基苯磺酸两种不同的表面活性剂同时参与反应,形成一种混合型的表面活性剂胶束,既可克服磺酸盐和水杨酸盐在使用性能上的不足,同时还可很好的解决两种产品共存时出现沉淀等问题,从而提高产品的综合性能。
1.4 硼酸盐
在高碱性金属清净剂中以硼酸盐取代碳酸盐得到硼化高碱度金属清净剂,有着比传统金属清净剂更加优越的性能,已经成为世界各大公司研制和开发的重点之一。目前国外主要有新日本石油、路博润、德士古和壳牌等公司进行了工业化生产。
无论是硼化的水杨酸盐或者硼化的磺酸盐、烷基酚盐,其制备工艺都分为一步法和两步法。一步法指的是硼化反应与高碱度化反应同时进行,两步法指的是该反应由高碱度化反应与确化反应两部分组成。所谓高碱度化,就是在溶剂、金属碱化物、促进剂的存在下,向油溶性的金属盐溶液中通入酸性气体(二氧化碳)进行碳酸化反应;硼化过程是在高碱度化反应产物的滤液中加人确酸,加热进行研化反应。确化产物经过冷却、汽提除却溶剂和水后,即可得到硼酸盐型金属清净剂。
2、无灰分散剂
分散剂在润滑油中的主要功能是分散和增溶。分散作用是指分散剂提供的油溶性基团能有效地抑制烟灰、氧化产物的聚集,使得这些粒子有效地分散于油中;增溶作用是指分散剂能与生成油泥的羰基、羟基(原本不溶于油)等直接作用,从而达到溶解效果。
分散剂主要品种包括聚异丁烯丁二酰亚胺、硼化无灰丁二酸酯、无灰磷酸酯、苄胺四种。聚异丁烯丁二酰亚胺是用的较广泛和使用量最多的一种分散剂,20世纪60年代后开始大量使用。根据性能和用途不同丁二酰亚胺可以分为单丁二酰亚胺、双丁二酰亚胺、多丁二酰亚胺和高相对分子质量分散剂。丁二酸酯仅路博润有产品(LZ936),无灰磷酸酯仅德士古有产品(TLA202)。
单烯基丁二酰亚胺的低温分散性能特别好,多用于汽油机油,但其抗氧化、防锈和抗乳化能力较差,尤其是高温稳定性欠佳,不宜在增压柴油机油中应用。经过结构改进的合成双烯基丁二酰亚胺和多烯基丁二酰亚胺的高温稳定性得到了明显的改善,可用于增压柴油机油。
由于高碱金属清净剂有较强的酸中和能力,可及时地中和那些作为油泥母体的酸性氧化产物,使丁二酰亚胺能更持久地发挥分散作用。丁二酰亚胺较强的分散能力,又可以提高碱金属清净剂中大量碱性组分[CaCO3, Ca (OH) 2]在油中的稳定性,使其不易在使用过程中发生沉淀而影响油品质量。丁二酰亚胺与高碱金属清净剂的适当复合,可以取长补短,发挥出协和效应。
随着汽车发动机的发展,对车用润滑油的要求也越来越严格,高档润滑油在其中的比重不断加大,这样就对无灰分散剂的要求也越来越高。一方面,要求无灰分散剂具有更加良好的分散性能,以满足换油期延长、采用废气循环系统后对油品中油泥增加的问题;另一方面,要求无灰分散剂具有更加良好的高温性能,以满足发动机压缩比增加、工作温度更高的要求。原来的普通丁二酰亚胺由于自身结构方面的原因,很难满足这些要求。高分子无灰分散剂的出现解决了这一问题,其特征为采用了相对分子质量更高的聚异丁烯作为原料,按照其结构可分为不同的种类。这类无灰分散剂的特性在于在保持良好低温分散性能的同时,大幅度提高了产品的热稳定性能和高温清净性能,更适于调制高档内燃机油。
2.1 聚异丁烯丁二酰亚胺无灰分散剂
聚异丁烯丁二酰亚胺(以下简称丁二酰亚胺)是目前用途最广泛、用量最多的一种无灰分散剂。为了提高丁二酰亚胺的高温稳定性,对其进行了一系列结构改进研究,使丁二酰亚胺的品种数量增加,并初步趋于定型化。一般在合成反应中加大烯基丁二酸酥与多烯多胺的比例,可制得双丁二酰亚胺及多丁二酰亚胺。
双丁二酰亚胺及多丁二酰亚胺比单丁二酰亚胺的高温稳定性明显改善,可作为增压柴油机油的分散剂组分。同时,其低温分散性能虽相应地稍有损失,但仍有很好的分散作用。双丁二酰亚胺与单丁二酰亚胺的分散性相差不大,故双丁二酰亚胺已有取代单丁二酰亚胺之势。
丁二酰亚胺无灰分散剂的生产主要由经化和胺化两步反应组成。第一步,相对分子质量950 ~2500的聚异丁烯(PIB)与顺丁烯二酸酐(MAA)反应制得聚异丁烯丁二酸酐(PIBSA),主要有氯化烃化、直接热加合、催化加合三种工艺;第二步, PIBSA再与不同比例的多乙烯多胺(通常为三乙烯四胺、四乙烯五胺)反应制得单、双和多聚异丁烯丁二酰亚胺。
我国目前生产无灰分散剂主要采用氯化工艺合成中间反应原料聚异丁烯马来酸酐(简称烯酐),再将产物与多烯多胺反应得到最终产品。其生产过程可分为两个步骤:经化一加合过程与胺化过程。
随着环保法规的日益趋严,汽车尾气排放新标准的实行,含氯产品的应用范围将会受到越来越大的限制。在实际润滑油的调制过程中,特别是调制高档车用内燃机润滑油,为了提高产品对油泥的分散作用,无灰分散剂在其中的加入量也在不断加大,结果油品中的氯含量也随之增加。这样就造成了油品提升分散性能与满足环保需求之间的矛盾。产品含氯与清洁燃料要求之间的矛盾,也决定了采用该种工艺合成的产品在燃料添加剂中应用前景尚不明朗。
为了能够真正做到降低无灰分散剂中的氯含量,需要从生产原料入手,利用高活性聚异丁烯合成无灰分散剂。一般认为,如果聚异丁烯组分的末端烯烃含量大于70%,即可认为该聚异丁烯为高活性聚异丁烯。利用高活性聚异丁烯合成无灰分散剂,同样需要两步反应过程:加合过程与胺化过程。其中,胺化过程与氯化工艺合成无灰分散剂对应过程一致。加合过程与氯化工艺方法不同,通常采用热加合工艺与催化加合工艺。
2.2 硼改性无灰分散剂
硼改性无灰分散剂(主要是硼改性聚异丁烯丁二酰亚胺)具有良好的分散性能、抗氧化性能。由于引人了硼元素,抗磨性能得到了提高,可有效地防止金属表面拉伤和擦伤,同时可减少无灰分散剂的一些不良作用,改善与橡胶密封圈的相容性,这在高档润滑油中很有用处。最近许多油品规格都对油品和橡胶密封圈的相容性提出了苛刻的要求,据介绍,硼改性无灰分散剂在高级内燃机油、汽车自动传动液(ATF)、二冲程油和船用油等方面得到广泛应用。润英联、雅富顿等新推出的内燃机油复合剂、ATF复合剂和二冲程油复合剂中大部分含有硼元素,一般来自硼改性无灰分散剂。
理论上,含氮的无灰分散剂都可以进行硼化,包括高相对分子质量的无灰分散剂及曼尼希碱型无灰分散剂。只要有碱性氢的物质都可以作为硼改性无灰分散剂的前体物质。
硼改性无灰分散剂的技术关键是研化反应。以往国内合成的产品都不同程度有“长毛”的现象,即硼化产品在空气中放置一段时间后,产品有研析出、外观不透明、质量不稳定,因而如何上硼是技术的关键。确化反应可在有溶剂或无溶剂条件下进行,无溶剂下可用氮气吹扫生成的水,用于硼化的溶剂有环己烷、正辛烧、甲苯、二甲苯、矿物油等。有专利报道,反应过程中用醇和水作为促进剂,作用是把反应过程中自聚成大分子的确化物分解成单分子状态,使确改性无灰分散剂中的确是一种化合态的确,而不是一种聚合形式的无机盐,从而提高其储存稳定性和热稳定性。
用于合成硼改性无灰分散剂的含硼化合物主要有四类:(1)硼酸类:硼酸、偏硼酸、四硼酸、焦硼酸, (2)硼的氧化物,如B2O3,及其水合物,(3)硼的氯化物、氟化物和其他硼化物; (4)硼酸酯类:,如单酯、二酯、三取代的酯等,也包括偏硼酸酯类化合物,报道最多的是硼酸和硼酸酯类化合物。
目前国内大多数内燃机油复合添加剂广泛使用以高碱度金属清净剂与丁二酰亚胺等无灰分散剂适当复合的复合型添加剂。从目前看,聚异丁烯丁二酰亚胺热点主要集中在开发兼具优良低温分散性和高温清净性、高温抗氧化性,并能降低无灰分散剂用量的新型高相对分子质量无灰分散剂。从生产工艺而言,热烃化工艺(不用氯气催化)研究活跃。
无灰分散剂的研究发展方向是更好的油泥和漆膜控制能力,优良的烟炱分散能力,改善低温性能,低温动力粘度小,与其他添加剂相容性好,耐水性好,并可生物降解,以满足现代汽车对油品的要求。目前,除传统的和典型的丁二酰亚胺型无灰分散剂以外,陆续出现了酯型、酯胺型、硼化型和苄胺型无灰分散剂。
丁二酸酯是20世纪70年代发展起来的分散剂,它是将聚异丁烯与马来酸酐反应得到的产物再与多元醇(如季戊四醇)反应得到的酯类分散剂,具有很好的抗氧和高温稳定性,主要应用于汽油机油和柴油机油中;磷酸酯无灰分散剂的分散油泥的能力稍差,但生成漆膜的倾向较小,具有优良的热稳定性,主要用于柴油机油和涡轮增压汽油发动机油中,苄胺是酚醛胺型的缩合物,在汽、柴油机油中除具有较好的分散性和沉积控制能力以外,还具有一定的抗氧化性,硼化丁二酰亚胺除具有分散性外还兼具抗氧化性能和良好的橡胶相容性。
国内生产的无灰分散剂以聚异丁烯丁二酰亚胺无灰分散剂为主,共有5个品种。T151为单烯基丁二酰亚胺,T152为双烯基丁二酰亚胺,T153为多烯基丁二酰亚胺,T154为高氮双烯基丁二酰亚胺,T155为低氮双烯基丁二酰亚胺。此外,高分子无灰分散剂T161、酯类无灰分散剂已实现工业化生产。
3、抗氧剂
润滑油的氧化是造成油品质量变差,以致需要更换的重要原因之一。由于氧化过程可以生成过氧化物、醇、醛、酸、酯、轻基酸等产物,这些化合物又进一步缩合生成不溶于油的产物,并附着在设备上,有些氧化产物与废气和水分形成油泥,造成油路的堵塞。此外,各种有机酸类产物还会造成金属(活塞环与缸套、轴承等处)的腐蚀,从而使磨损增大。因此,需要加入抗氧化添加剂,减缓润滑油的氧化变质过程,延长润滑油的使用寿命。
抗氧化剂分为一次抗氧化剂和二次抗氧化剂。一次抗氧化剂也称为连锁反应停止剂,主要用胺和位阻酚系的化合物很快和过氧游离基(ROO·)反应,而后和烷氧游离基(RO·)反应,防止(切断)氧化的连锁反应;二次抗氧化剂也称为氢过氧化物分解剂,主要用如硫醚、磷酸盐、硫磷酸盐等化合物与氢过氧化物(ROOH)反应生成非自由基和非活性物质而阻止氧化。二次抗氧化剂和一次抗氧化剂组合使用可得到相辅相成的效果。
近年来,随着高档润滑油在控制粘度增长、沉积物降低、减少阀系磨损等方面的苛刻要求,对抗氧剂的性能也提出更高要求。用作抗氧抗腐剂的化合物主要是一些含硫、磷、氮和金属有机化合物以及多种烷基酚,由于传统的烷基酚类和胺类抗氧剂在高温条件下易失去活性,其使用范围受到限制。而仅仅使用ZDDP系列抗氧抗腐剂已经无法满足高档润滑油的抗氧化性能要求,因此各种抗高温的屏蔽酚型、胺型、有机铜盐、碱金属盐类等新型无灰抗氧剂的研制工作得到较快发展。
酚型抗氧剂中使用最广泛的产品是2,6-二叔丁基对甲酚(T501),由于其在低温时抗氧化效果较好,所以除用于燃料外,多用于变压器油、汽轮机油和液压油等使用温度较低的油品中。其他酚型抗氧剂还有对苯二酚、β-苯酚等,可使变压油寿命自3个月到年的时间提高到15年之久。此外还有不少双酚型抗氧剂,如4,4-亚甲基,2,6-二叔丁基对甲酚,双酚抗氧剂在较高温度下使用效果比T501更好,可用于灰分要求严格的航空润滑油中。含有硫元素的酚型抗氧剂在加氢基础油中具有较好的抗氧化作用,如CiBa的L115 (含硫双酚)和L108(含硫单酚)产品。
胺型抗氧剂的热分解温度比酚型要高,可用于100- 140℃之间,其代表化合物有N,N--二仲丁基对苯二胺、N-苯基N-仲丁基对苯二胺、N-苯基-a茶胺(T531),同时含有氨基和烃基的化合物,其抗氧化效果超过了只有一种官能团的化合物。这类抗氧剂是无灰型抗氧剂,多用于变压器油、液压油、汽轮机油以及航空润滑油中。酚型抗氧剂和胺型抗氧剂共同使用时会有协同增效作用。
各种金属(如Cu, Zn,Mo, Sb等)的烷基硫代磷酸化合物都具有一定的抗氧化能力和抗磨、减摩、抗腐和极压作用。特别是二烷基二硫代磷酸锌(ZDDP)产品,具有优良的抗氧、抗磨、抗腐性能,可广泛地应用于润滑油尤其是发动机油中。
ZDDP的结构有仲烷基、伯烷基和芳烷基三种,其性能有很大差异,这就是为什么国内外主要添加剂公司开发了系列ZDDP品种的原因。从热稳定性来看,烷基芳基>长链伯烷基>短链伯烷基>仲烷基;从抗磨性能来看,仲烷基>短链伯烷基=长链伯烷基>烷基芳基,从水解安定性来看,仲烷基=长链伯烷基>短链伯烷基>烷基芳基。正确选用不同结构的ZDDP非常重要。一般热稳定性差的ZDDP有较大的载荷性,热稳定性增加、其载荷性下降。
ZDDP系列产品中由于硫、磷两元素对环境的危害性及发动机运转条件的苛刻化和某些内燃机油和工业用油的特殊要求,人们开始寻找抗高温的无灰抗氧剂,如二烷基硫代氨基甲酸酯、噻唑类油溶性杂环化合物(如苯并三氮唑衍生物、烷基硫甲基苯并三氮唑、噻二唑、巯基苯并噻唑类等)。二烷基硫代氢基甲酸酯和噻唑类油溶性杂环化合物是一类低灰、低磷型抗氧抗腐剂。针对低硫、低磷的要求开发出不含硫、磷的油溶性有机金属盐,如铝盐和铜盐。前者以其良好的减摩性能可广泛用于调配各种润滑油,能明显降低摩擦系数,提高发动机燃油经济性,延长发动机寿命,同时该剂还具有良好的抗氧化性能,与ZDDP有显著的协同作用。后者的种类比较多,但不含硫磷的有机铜盐化合物主要为其不含硫磷的羧酸盐类,如油酸铜、硬脂酸铜、棕榈酸铜、环烷酸铜、C18~C24烯基丁二酸铜和苯乙烯马来酸铜等,该类抗氧剂的应用必将是汽车用润滑油控制氧化过程的一个重大突破。
此外,氨基甲酸酯、氢基甲酸盐类抗氧剂、硼酸酯型抗氧剂、有机铜盐等抗氧剂,具有较高的热分解温度、在高温下具有较好的抗氧化效果,不含磷,对汽车三元催化转化器的影响小。近年来,随着高档润滑油的发展,人们越来越注重这类抗氧剂的应用和开发。尽管抗氧剂化合物种类很多,但在润滑油中获得广泛使用的抗氧剂类型有限。
随着润滑油使用条件的苛刻化,对润滑油高温抗氧性提出更加严格的要求,开发新的符合润滑油要求的新型抗氧剂就成为添加剂研发机构关注的重点,中国石油润滑油公司为生产符合要求的润滑油产品,目前已开发出了一些新的抗氧剂产品。
4、极压抗磨剂
润滑油的基本功能,就是减少机械的摩擦和磨损,防止因为摩擦生热而导致的胶合。为了提高润滑油的润滑性能,除了改善基础油的各种理化性质外,更为重要的是向基础油中加入不同类型的添加剂。所谓的“载荷添加剂”,就是可以达到降低摩擦系数、减少磨损的化学物质。载荷添加剂从其功能上来分,习惯上分为油性添加剂、抗磨添加剂和极压添加剂三大类,这种分法实际上是按照它们所能起作用的工作条件为标准的。
对传统矿物油基润滑油载荷添加剂的研究,主要集中在抗磨剂和极压剂的工作。按照作用机理的不同,大致可以分为两大类:活性和非活性添加剂。活性添加剂主要是指分子结构中含有硫、磷、氯等活性元素,可以与金属表面发生化学反应形成保护膜的化合物;非活性添加剂主要是指通过自身或其分解产物在摩擦表面形成保护膜的添加剂,如硼化合物、硅化合物、铝化合物等。
在中等负荷及速度条件下,摩擦表面因大量放热而温度可以高达150℃甚至更高,这就使得摩擦表面吸附的油性剂发生脱附,进而失去减摩抗磨的作用。在这种工作条件下,必须使用那些在较高温度下能与新生金属表面作用生成化学吸附膜的表面活性物质,才能起到防止摩擦表面胶合的作用,这样的化学物质就是所说的“抗磨添加剂”。
在低速高负荷或高速冲击摩擦条件下,即在所谓极压条件下,摩擦面容易发生烧结,抗磨损添加剂也无能为力,为防止烧结而使用的添加剂称为极压添加剂。
传统的抗磨添加剂通常含有硫、磷、金属,但研究显示,添加剂中的金属(锌)会随着汽车尾气的排放以颗粒物的形式排入大气,堵塞后处理装置的颗粒捕集器,磷会致使催化剂转换器中的经转换催化剂中毒,对氧气传感器也有负面影响,硫可使废气排放系统中降低NOx,排放的催化剂中毒。这就促使了新型抗磨添加剂的发展趋势向着无灰、低磷和低硫的方向进行。
按照添加剂的分子结构可将抗磨剂分成氯系、硫系、磷系、氮系、硼酸盐、铝系、稀土化合物、纳米材料抗磨剂等。
4.1 氯系
含氯抗磨剂主要有氯化石蜡、氯化联苯等,这类添加剂在摩擦表面由于热分解或断裂C-Cl键,放出氯原子或生成HCl,再进一步与金属反应生成FeCl3, FeCl2等低熔点金属盐膜,易于剪切,从而起到润滑作用。
氯系添加剂有两个主要缺点限制了它的广泛应用和发展。一是氯化合物遇水容易水解生成游离的HCl,从而造成金属表面的腐蚀,与硫系极压抗磨剂相比,当反应性相同时,氯系极压剂的载荷性能要低得多;二是含氯化合物对环境具有危害性,会造成对水源、空气和土壤的污染,随着环保意识的不断加强,氯系添加剂的使用越来越受到限制。因而近年来,氯化石蜡代用品在国外已有很大的发展。氯化石蜡代用品主要是高分子醋类、磷酸酷、含磷添加剂、含氮添加剂和高碱性的磺酸盐。但是氯化石蜡代用品价格高,极压活性却不太理想,对难加工的金属主要还是依靠氯化石蜡。
4.2 硫系
硫系添加剂国外称为“含硫承载添加剂”,主要用作极压剂或油性剂,有的也具备抗磨作用。就其种类而言,主要包括硫化动植物油、硫化烃、硫代酯、多硫化物等。含硫化合物在一定温度下,会发生分解,生成的活性硫再和铁反应形成保护膜。一般来说,分子中硫的含量越高,就越易分解,与金属的反应也就越容易,而单硫化合物对热不敏感,很难分解,所以不宜作为极压添加剂。
国外含硫添加剂的品种很多,主要包括丁烯硫化油脂和硫化酯、黄原酸酯、硫代碳酸盐、二硫代氨基甲酸盐和多硫化合物等。其中硫化异丁烯是硫系极压抗磨剂最主要的产品,针对不同的用途,各公司可以同时生产不同性能的硫化异丁烯。
4.3 磷系
含磷添加剂主要用作抗磨剂,当然,抗磨、极压和减摩性是互相关联的,作为抗磨添加剂也需要有一定的承载能力,也就是有一定的极压性。一般而言,含磷剂的极压性不如含硫添加剂,但磷对于钢质摩擦副有良好的抗磨作用。
磷系极压抗磨剂品种较为复杂,不仅表现在化合物种类上,也表现在元素组成上。有含单一磷元素的,有含硫、磷两种元素的,有含磷、氮两种元素的,也有含硫、磷、氮三种元素的,即使元素组成相同,化合物结构也可以不同,不同磷化物用于不同目的。磷系极压抗磨剂的热稳定性越差,则抗磨性越好,但抗磨持久性下降。国外含磷极压抗磨剂主要是亚磷酸酯、磷酸酯、硫代磷酸酯和酸性磷酸酯胺盐。
在含磷载荷添加剂中,二烷基二硫代磷酸金属盐(MDDP)是一类性能极为突出的添加剂。由于分子中同时含有磷、硫元素,几乎所有的MDDP都具有优异的抗氧化性能和极压抗磨性能,围绕这一类添加剂所进行的研究工作,也是目前最深入的。
4.4 氮系
含氮化合物在润滑油中的作用,最初主要作为腐蚀抑制剂、分散剂和抗氧剂等。如含氮杂环化合物苯并三氮唑及其衍生物,由于可以与金属铜生成苯三唑铜盐,从而在氧化亚铜的表面上形成覆盖膜,保护金属不受腐蚀。随后的研究发现,许多含氮、硫的化合物具有抗磨承载能力,如苯并三氢唑衍生物、烷基硫甲基苯并三氯唑、1,3,4-噻二唑等。
含氮多功能添加剂由于分子中不含磷、硫和金属等,对于环境的影响较小,是当前添加剂开发工作的热点之一。Crompton公司(由Uniroyal和Witco公司合并而成)和Ciba公司在含氮抗磨添加剂的研制方面做了许多工作,开发了一系列无灰、无磷、抗疲劳的极压抗磨添加剂,可代替或部分代替目前广泛应用的ZDDP。
4.5 硼酸盐
硼酸盐添加剂的突出特点是具有优良的承载能力、良好的抗磨性以及特殊的油粘度与摩擦性能的关系。含酸盐的齿轮油的极压性比S-P型、Pb-S型齿轮油的极压性都高,并且具有很好的减摩性。其中,无机硼酸盐是一种高效多功能润滑油添加剂,具有优异的极压抗磨减摩性能以及良好的热氧化安定性、防锈防腐性、密封适应性,比硫系、磷系添加剂性能更优越,无毒无臭,不污染环境,已在工业齿轮油、二冲程发动机油、车辆齿轮油中得到应用,并具有明显的节能效果。但无机酸盐添加剂在油中的分散稳定性及水解稳定性差,易产生沉淀。一般的硼酸盐添加剂溶于水,不溶于油,而它又需要一定的结晶水才有极压抗磨效果,所以不能用于见水部位的润滑。硼酸盐遇水会使性能降低或消耗殆尽,且硼酸盐在使用时须借助分散剂将其精细地分散到矿物油脂中。所以,尽管其载荷能力、抗磨损性能、热氧化安定性、高温抗腐蚀性和密封性等均比常用的硫一磷型极压抗磨剂优越得多,但使用不方便,并具有选择性,大大限制了它的应用。因此,研制出综合性能优良的硼酸盐润滑油添加剂一直受到人们的关注。
目前,国外已形成了比较成熟的无机硼酸盐生产工艺,如雪佛龙已生产出OLOA9750胶体硼酸盐极压抗磨剂,我国茂名石油工业公司也开发出了胶体硼酸盐,其产品性能达到了OLOA-9750的水平。有机硼酸酯极压抗磨剂除了具有良好的抗磨作用外,还具有较好的防腐蚀性、抗氧化性、油溶性等特点,属多功能添加剂,具有良好的发展前景。
4.6 钼系
钼化合物润滑材料因其优良的摩擦学性能而在众多的润滑材料中占有非常重要的位置。其中二硫化钼(MoS2)、油溶性二烷基二硫代氨基甲酸硫化氧钼(MoDTC)及二烷基二硫代磷酸硫化氧钼(MoDTP)等,已广泛应用于航空、航天、航海、机械等诸多领域。可作为润滑油脂添加剂的含铝有机化合物有MoDTC和MoDTP,它们具有更优良的抗磨和极压性能。其作用机理在于含硫有机金属配合物润滑剂借助硫原子与金属基体发生反应而粘附,进而形成极压化学润滑膜,同时部分分解为MoS2固体润滑膜,MoS2固体润滑膜对摩擦表面的凹凸起填平作用,对摩擦阻力起缓和作用。
4.7 稀土化合物
近几年来,稀土化合物在摩擦学领域的应用研究一直是摩擦化学家们关注的热点之一,由于稀土元素的4f轨道电子影响,稀土化合物与其他相同晶体结构的金属相比,摩擦系数和磨损率都有明显的差别。目前研究比较多的有稀土卤化物、稀土氧化物和稀土金属,应用对象主要是润滑脂、涂层和水基加工液等。
目前,大多数研究者认为稀土化合物具有优异抗磨减摩性能的主要原因来自两个方面:一是在摩擦表面生成含稀土元素的多相表面润滑保护膜提高了减摩性能;二是在摩擦表面生成稀土摩擦扩散层,保护金属材料,使金属摩擦副材料的硬度提高,耐磨性能改善。
4.8 纳米材料
纳米材料独特的结构使其具有奇特而优异的摩擦学性能,具有传统固体润滑剂(如聚四氟乙烯、MoS2、石墨粉体)所无法比拟的优越性。在润滑油中加入纳米添加剂可显著提高其润滑性能和承载能力,减少添加剂的用量,提高产品的质量,同时在节约能源和改善尾气排放等方面的效果也十分突出,特别适用于苛刻条件下的润滑场合。纳米添加剂目前在应用中面临的主要问题是纳米粒子在润滑油品中的分散稳定性较差,在使用过程中容易发生团聚而形成沉积,从而丧失润滑性能。需要系统研究纳米粒子在基础油中的分散稳定机制,考察其在不同摩擦条件下所表现出的分散、团聚、沉降、粘着、消耗等行为规律,并在此基础上探索改善纳米添加剂分散稳定性的方法。
纳米粒子作为润滑油添加剂的研究还处于起步阶段,许多基础性研究工作需开展,其组成、结构和性能之间关系的研究还很不成熟,目前的研究范围主要围绕着制备方法、测试技术、性能及应用领域的拓展。综合来说,纳米润滑材料的发展面临如下几个急需解决的问题:(1)寻找普遍可行的纳米材料制备技术,降低成本, (2)纳米粒子的制备和表面修饰“一体化”,直接生产油溶性或水溶性纳米粒子添加剂,(3)了解纳米粒子的应用背景,选择各种合适的纳米材料;(4)掌握纳米材料作为润滑油添加剂的最佳粒度、浓度、温度、负荷、转速与其他添加剂的配伍及对基体材料的性能影响等; (5)建立与纳米粒子相适应的实验室评价、检测手段。抗磨剂是润滑油使用的重要的添加剂品种,尤其在齿轮油中应用更为重要。
随着齿轮箱朝着缩小体积、减轻重量、增大功率、提高效率和增加可靠性等方向发展,对齿轮油也提出了更苛刻的要求。概括而言,就是要求油品除了具有良好的摩擦学性能外,还应尽可能满足节能、环保和安全等要求。国内长期开展润滑油极压抗磨剂的研究开发,目前市场上的品种较多,也基本满足了润滑油生产企业的需求。
5、金属减活剂
金属铜、铁等能够催化油品氧化变质,氧化生成的酸又使金属部件腐蚀磨损,氧化产物缩合还进一步生成油泥和沉积物,使油品变稠沉积在机械部件上,或者造成油路堵塞。能够抑制金属的催化作用从而延缓润滑油衰变的添加剂称为金属减活剂。目前国内外常见的金属减活剂主要是噻二唑类和苯三唑类金属减活剂,研究领域亦以苯三唑衍生物和噻二唑衍生物为主。关于苯三唑衍生物的研究主要围绕两个方面:一方面是进一步提高与抗氧剂的协同作用,尤其是与胺型抗氧剂的协同作用,另一方面是在维持减活剂抑制金属腐蚀及辅助抗氧性能的基础上,增加其他的功能,如防锈性及乳化性等。而噻二唑衍生物主要着重于工艺改进,方向为无毒、无污染及降低成本。
一些具有优良极压抗磨性的多硫化物,是调制齿轮油的主要添加剂。但在使用过程中产生的活性硫会引起铜的腐蚀。加入少量的苯三唑类金属减活剂T551能使工业齿轮油通过高温铜片腐蚀试验。T551是优良的铜腐蚀抑制剂;T551金属减活剂与T501抗氧剂复合使用时具有增效作用,可在降低T501用量40% ~60%的同时,使油品的抗氧化性得以保证。因此,T551具有优良的抑制铜腐蚀及辅助抗氧化等性能,其用量低、效果好,是一种高性能多效添加剂。自1986年工业生产以来,T551主要应用于变压器油、工业齿轮油、油膜轴承油、通用机床油、汽轮机油和液压油等多种润滑油中。T551唯一的不足是会与ZDDP或氨基甲酸盐类抗氧剂互相作用产生沉淀,因而不能共用。噻二唑类金属减活剂T561是较好的一种铜腐蚀抑制剂,用于抗磨液压油中能抑制ZDDP水解引起的铜腐蚀现象,已经广泛应用于工业用油和内燃机油中。
国外生产并应用的金属减活剂主要还有IR39和IR30,IR39添加剂的结构、性能与国内生产的T551相当,而IR30的性能优于IR39。另外近年来还开发出了一系列新型的金属减活剂。
6、防锈剂
水、酸、氯化物、硫化物等是极易引起金属腐蚀或锈蚀的物质,通过使用抑制这些物质对金属的腐蚀作用的添加剂,可防止、延缓、阻止金属的腐蚀或锈蚀作用,这种添加剂称为防锈剂。防锈剂按照化合物类型主要分为:磺酸盐(石油磺酸钡、石油磺酸钠)、羧酸(羧酸盐及衍生物,如长链脂肪酸、壬基苯氯乙酸、N-油酰肌氢酸、烯基丁二酸等)、酯类(山梨糖醇单油酸酯、已二酸丁酯、丁三醇单油酸酯等)、有机磷酸及其盐类(如单或双十三烷基磷酸、十二烷氧基丙基异丙醇胺盐等)及胺、胺盐、胺衍生物和杂环化合物(如氧化石蜡饱和脂肪酸、二环己胺生成的盐、辛酸二环己胺盐、苯并三氮唑、烷基取代的咪唑咻及其有机酸盐等),共计五类。
防锈剂广泛用于防锈油、液压油、汽轮机油、金属加工等工业润滑油中。内燃机油的防锈问题则主要通过添加兼具防锈性的石油磺酸盐清净剂加以解决。
五、添加剂的复配
现代工业润滑油生产大多采用复合添加剂进行调合,不但调合工艺简单,而且可降低总加剂量,节约成本。20世纪80年代以前,国际市场上除少量添加剂以复合剂形式出现外,大部分添加剂都是以单剂的形式出现,80年代之后国际市场上润滑油添加剂主要以复合剂的形式出售,并持续改进配方以提高使用经济性能,发展多功能添加剂。
在复配技术中,除了采用多功能添加剂外,很重要的是研究添加剂的协同效应,两种添加剂在一起使用时的效果比单独使用一种添加剂时的效果要好得多,这样就可以大大降低添加剂的总加剂量。降低润滑油中添加剂的总加剂量是提高油品质量和降低成本的重要措施。目前,抗磨液压油的总加剂量已经由过去的1.5% - 2.0%降到0.4% ~0.6%;工业齿轮油的总加剂量也降至1.2%以下。汽轮机油在相同的加剂量下,抗氧化寿命已由原来的3000 ~ 4000h提高到10000h以上。某些单剂的加剂量也明显下降,如过去一般加0.05%-0.1%的破乳剂,现在只要加人0.005%就可起到较好的效果。
国外润滑油调合厂基本上都采用各添加剂公司的复合剂生产润滑油产品,由于复合剂质量有严格的复合工艺条件和单剂的质量保证,所以采用复合剂生产的润滑油质量易于符合规格标准。目前国外添加剂公司销售的单剂品种越来越少,复合剂的品种越来越多。添加剂的复配技术是润滑油研究的核心,对于添加剂复配的研究要立足于对于各种单剂性能的掌握,在保证各种单剂性能得以充分发挥的前提下,注重复配添加剂的稳定效果,保证效能的持久发挥也是至关重要的,添加剂复配需关注以下几个方面。
(1)各种单剂的稳定性。
各种添加剂单剂是润滑油产品的基本组成单元,在进行添加剂复配时首先考虑选用性能稳定的单剂产品。添加剂原料和合成工艺对其性能会产生影响,选用原料来源稳定和工艺成熟的添加剂是保证添加剂复配效果的根本。要通过严格的添加剂验收标准控制其质量并确保其合理的质量波动不会对添加剂的复配效果产生影响。如磺酸盐、硫化烷基酚盐、烷基水杨酸盐类金属清净剂是润滑油中用量较大的添加剂之一,也是对于润滑油质量影响最大的单剂,生产清净剂的原料结构发生变化很可能引起添加剂稳定性的变化,由此复配的添加剂产品的长期稳定性就会出现问题。
(2)发挥出各种添加剂的协同效应。
每种润滑油都需要有两种以上的添加剂进行复配。添加剂的复配之所以称为是一种技术,是因为添加剂的复配效果并不是各种单剂性能的简单加合。有的单剂组合后不但可以发挥出各自的效力,还可能使某些方面的性能得以较大程度的强化,即为添加剂的“协同效应”;相反地,有些单剂组合后消减了各自的某些性能,形成了“抑制效应”。添加剂的复配要能较大程度地发挥其协同效应,这样形成的添加剂配方最经济,性能更持久。
(3)添加剂的互相制约。
从添加剂复配稳定性的角度讲,有些添加剂单剂的组合会出现问题。如时有高碱磺酸盐一烷基水杨酸盐或高碱磺酸盐一高碱硫化烷基酚盐的复配后出现稳定性差的问题的报道,苯三唑类金属减活剂(T551,C20)与二烷基二硫代磷酸锌类抗氧剂(T202)复合时可能会出现沉淀现象;金属清净剂(T109)、稠化剂(T601)、防锈剂(T705)存在时会削弱非硅抗泡剂(T911,T912)的作用,等等。当进行添加剂复配研究时,需审慎选用这样的添加剂组合。
(4)各种添加剂的添加顺序和方式。
复配添加剂时,单剂的添加顺序及添加方式也是应首先进行考查并确定的,尤其是抗泡剂、抗乳化剂等加量较少的添加剂,如果加入顺序和方式不适当就难以发挥出添加剂的效力。
(5)添加剂体系的稳定性及与基础油的相容性。
在添加剂复配过程中除通过各种模拟试验和台架评定验证复合效果外,进行体系稳定性的考查也是必需的。一般是通过将所调合的润滑油产品在高温和低温条件下进行一定时间的存放来考查添加剂复配的稳定性和与基础油的相容性。
我国基础油资源丰富,包括石蜡基、环烷基、中间基在内的各种类型的基础油具有各有的特点,尤其是近年加氢基础油和合成基础油的广泛应用使得我们必须关注基础油对添加剂的溶解性能。对于基础油相容性差或自身稳定性不好的添加剂复配,即使能通过实验室各种评定,我们也应谨慎采用,以保证所调合产品的长效性能。
(6)根据法规要求确定添加剂复配的路线
我国的环保和排放法规主要参照欧洲标准制定,近年来日益严格。润滑油的组成对汽车排放会有一定影响,包括金属清净剂和抗氧剂等有灰添加剂的使用会受到严格的限制。在添加剂复配时,须选用低硫、低磷及低硫酸盐灰分的添加剂单剂,以适应新的发动机技术和排放法规的要求。
更多信息请参考《润滑油脂及其添加剂》一书。