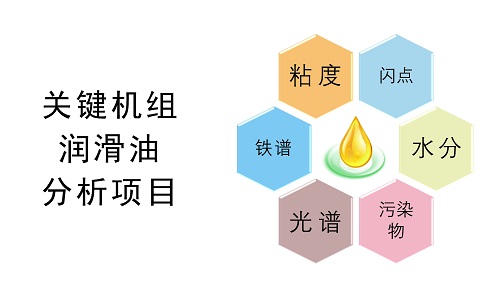
课前测试ppt下载:课前测试。课后试卷及答案下载:试卷、答案
前言
一、状态监测概述
状态监测对于关键机组长周期运行来说至关重要,定期开展状态监测,发现问题后积极采取治理措施,可以延长机组运行周期。
狭义的状态监测是指振动分析,通过监测设备各部位的位移、速度、加速度的变化趋势,利用各类图谱和算法,分析故障产生原因,提出治理措施。广义的状态监测见下图:
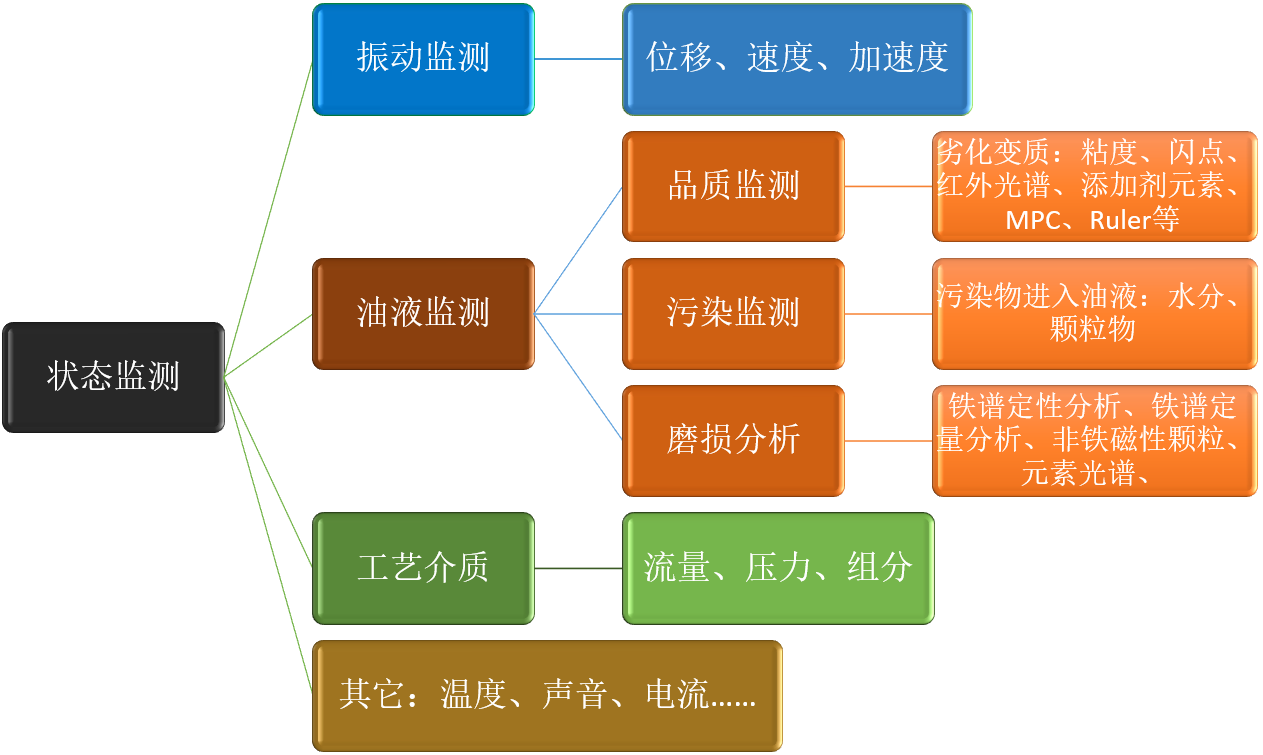
油液监测:主要包括三方面内容,一是品质监测:监测油品是否劣化变质,主要监测粘度、酸值、氧化、添加剂元素、MPC的变化趋势;二是污染监测:监测油品是否进入了异物,受到污染,主要监测水含量、泡沫特性、水分离性、清洁度、闪点的变化趋势;三是磨损监测,监测摩擦副是否发生异常磨损,主要是监测机械杂质、光谱、铁谱分析的变化趋势;通过上述项目的监测判断油品是否劣化变质、被污染,设备是否存在磨损,提出治理措施[CY] 。
(注:该分类方法不完全准确,例如:油品劣化、污染均可能导致粘度变化,这样分类是为了便于查找异常原因,提出治理措施)。
ISO 18436《机器的状态监测和诊断-人员资格和评估的要求》还提出了热成像、声发射和电机电流等监测手段。
在多年的状态监测工作中,推荐大家还应该多关注工艺介质参数,例如:流量、压力、介质成分以及温度等因素的变化情况,综合分析设备故障可能的原因,提出准确的治理措施。 机器状态监测与诊断所需参数可参见GB/T 22393《机器状态监测与诊断 一般指南》。
二、润滑油体系概述
润滑油主要分为两大体系:一是内燃机油,二是工业用油[CY] 。内燃机油主要包括:车用油、船用油、航空发动机油、以及燃气发动机油等。内燃机油的粘度的测定是以100℃为基准,工况苛刻,更新换代快,使用量占润滑油耗量的一半以上;工业用油包括钢厂、矿山、炼油化工、以及机械加工等行业的设备用油。工业用油的粘度测定是以为40℃为基准,工况相对简单,但关键机组要求长周期运行(4-5年),所以对润滑油品质和运行维护要求很高。
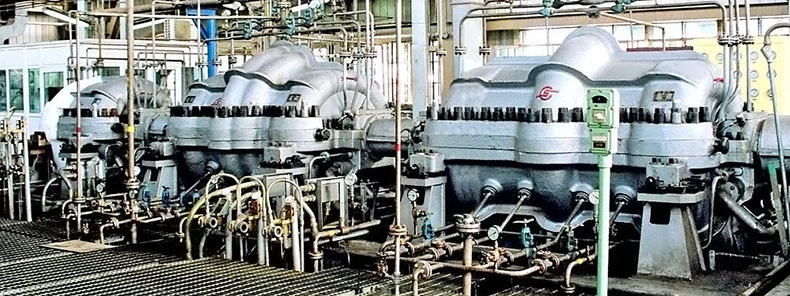
48万吨乙烯裂解气压缩机
本文主要讲解关键机组润滑油分析项目,共计20余个。讲解了每个项目的基本概念、监测的意义、分析方法、评定标准、变化的原因、对应的治理措施以及一些相关的知识点和标准。大家可以把这个教程作为一个目录,遇到问题时进行查阅。
本文大部分内容来自标准规范,部分来自网络和文献,也有不少个人的见解(上角标[CY]),欢迎大家随时批评指正。
三、润滑油取样
3.1、取样位置
取样的目的决定取样的位置,见下表 [CY] :
目的 | 位置 | 理由 |
日常监测 | 1、油冷器后,过滤器前 ; 2、过滤器后。 | 1、油液被冷却后溶解度降低,溶解物析出。 2、异常情况下,确保进入摩擦副的油品达到标准。 |
故障分析 | 离摩擦副最近的回油支线 | 样品中包含有完整磨损与污染的信息,最能体现设备当前的运行状态。 要有及时性! |
开机油运 | 1、各摩擦副前; 2、过滤器后。 | 1、滤网实验,验证供油管路足够干净,确保杂质不会进入摩擦副; 2、即将进入摩擦副的油品,其各项指标的好坏直接关系到润滑效果。 |
评价过滤器 | 过滤器前后同时取样 | 对比分析就可以了解过滤系统是否运行正常。 |
也可参考GB/T 14541《电厂用矿物涡轮机油维护管理导则》的取样要求。
3.2、取样要求
3.2.1 润滑油取样执行GB/T 4756-2015 《石油液体手工取样法》,需要注意以下几点:
- 油品要具有代表性;
- 最好在设备运行时;
- 位置固定;
- 充分置换取样的管线;
- 不要被污染;
- 做好标记,至少包括下述内容: 单位名称、机组编号、油的粘度等级、取样部位、取样日期、取样人以及备注。
3.2.2 润滑油在线监测取样执行GB/T 27867《石油液体管线自动取样法》。
注:本文介绍的方法均为离线取样分析。
四、重复性与再现性
4.1 重复性:同一样品,同一人员,同一设备和环境,分析结果的误差范围;例如开口闪点≤8℃。
4.2 再现性: 同一样品,不同人员,不同设备和环境,分析结果的误差范围;例如开口闪点≤14℃。
4.3 置信度:可靠性、置信水平,≥95%。
一、粘度/黏度(Viscosity)
1.1 基本概念
粘度源于液体的内摩擦,油液受到外力作用而发生相对移动时,油分子之间产生的阻力使油液无法进行顺利流动,描述这种阻力大小的物理量称为粘度。
粘度的度量方法有绝对粘度和相对粘度两大类。其中绝对粘度分为动力粘度、运动粘度两种;相对粘度主要有恩氏粘度、赛氏粘度和雷氏粘度三种。详见各种粘度的概念及换算。
动力粘度: 流体在剪切应力作用下流动时内摩擦力的量度。 其值为所加于流动液体的剪切应力和剪切速率之比。 单位是毫帕・秒(mPa・s)。
运动粘度:在同一温度下的动力粘度除以该温度下的密度,用mm2/s表示,也记做cSt,厘斯。国际标准化组织(IS0)规定统一采用运动粘度之后,各国都逐步改用了运动粘度,单位以mm2/s表示。
1.2 监测的意义
运动粘度是衡量油品油膜强度、流动性的重要指标。在用油运动粘度的变化反映了油品发生深度氧化、聚合、轻组分挥发、生成油泥以及受燃油稀释、水污染和机械剪切的综合结果。粘度的增长会增加动力消耗,过高的粘度增长甚至会带来泵送困难,从而影响润滑造成事故。粘度的下降则会造成发动机油油膜变薄,润滑性能下降,机件磨损加大,粘度大幅下降往往会造成拉缸的后果。
粘度作为润滑油最重要的检测指标,无论是定期监测还是故障分析,都是必选项。
1.3 分析方法
标准概述:目前我国运动粘度测定方法的有GB 265-1988《石油产品运动粘度测定法和动力粘度计算法》和GB 11137-1989《深色石油产品运动粘度测定法(逆流法)和动力粘度计算法》。其中GB 265是测透明石油产品的运动粘度;GB 11137是测不透明的深色石油产品和在用油的,该方法修改采用自ASTM D445。美国实验与材料协会还开发了ASTM D7042《液体动力粘度和密度及计算运动粘度测定 斯塔宾格粘度计》,同时测定液体动力粘度和密度,同时计算及运动粘度,该方法可测定各温度下的动力粘度和密度,速度快。
GB 265 方法概要:在某一恒定的温度下(通常为40℃或100℃)测定一定体积的液体在重力下流过一个标定好的玻璃毛细管粘度计的时间。粘度计的毛细管常数与运动时间的乘积即为该温度下测定液体的运动粘度。
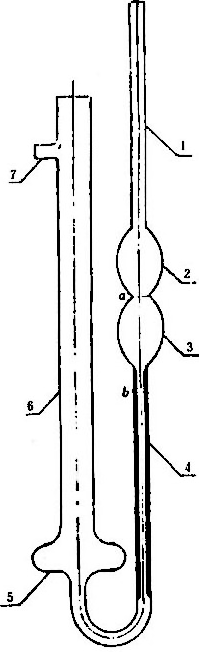
毛细管粘度计
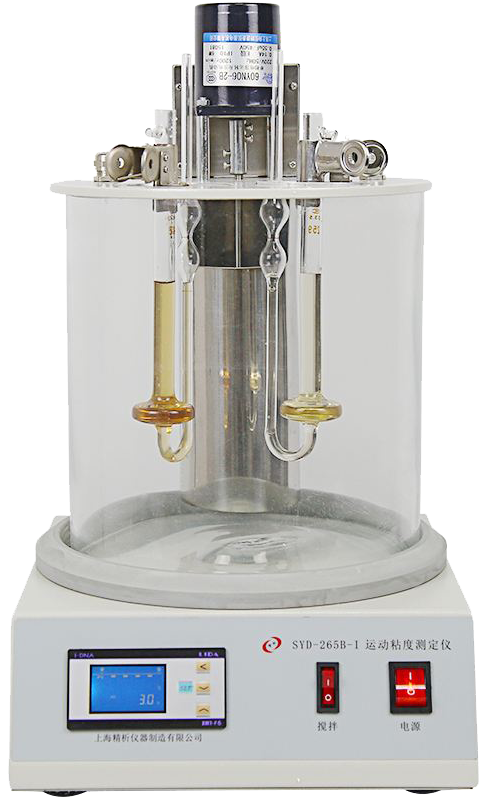
自动粘度计
1.4 评定标准(报警指标、换油指标)
油品在使用过程中的监测评价指标主要分为两类:一类是采用绝对值,例如:水分、清洁度、机械杂质、铁含量等。二是采用相对值(变化率),例如粘度、酸值、碱值、部分金属元素含量等,是指相对于新油(或加注运行后)的变化率;闪点既要考虑绝对值,也要考虑变化量。
不同的种类润滑油的运行监控指标和换油指标差别很大,《润滑油使用及评定标准汇总表》整理了部分油品的 运行监控指标和换油指 。下面仅以常用的工业润滑油做举例说明。
换油指标
1.4.1 液压油
SH/T 0599-2013《液压油换油指标》与SH/T 0599-1994相比,40℃运动粘度、酸值指标都有所收紧,同时增加了清洁度指标和泡沫特性(24℃)指标。
取样频次和要求详见标准,当使用中的油品有一项指标达到换油指标时应采取维护措施或更换新油。换油指标详见下表:
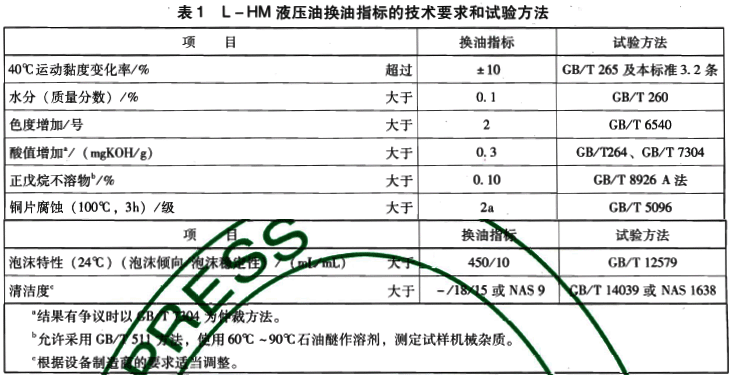
1.4.2 齿轮油
SH/T 0586-2010《工业闭式齿轮油换油指标》替代SH/T0586-1994 L-CKC1994(2003)《工业闭式齿轮油换油指标》,规定了L-CKC、L-CKD工业闭式齿轮油在使用过程中的定期质量监控和换油指标。换油指标详见下表:
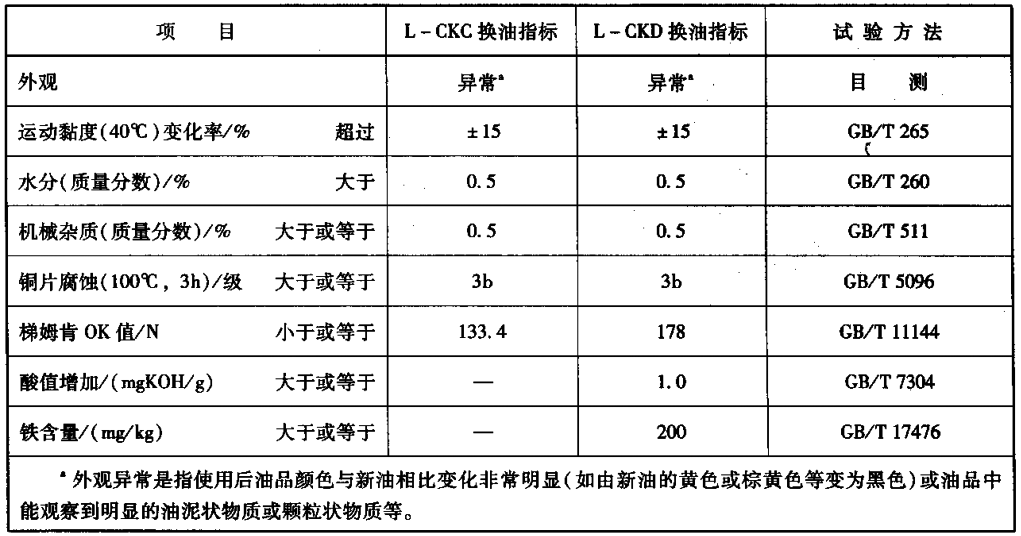
1.4.3 内燃机油
发动机机油主要起到润滑、冷却与清洗等作用。机油在作用过程中,本身化学特性会有所改变,添加剂会被逐渐消耗,燃烧产生的污染物与机件磨损产生的金属颗粒与机油混合产生复杂的油泥溶于机油中,时间一长,这些不溶物不但会加速发动机磨损,还会导致发动机锈化腐蚀、散热不畅等严重后果。因此,视情更换机油是对发动机最好的呵护。
柴油机油换油指标
GB/T 7607-2010《 柴油机油换油指标 》技术要求和试验方法下表,当使用中的油品有一项指标达到换油指标时应更换新油。
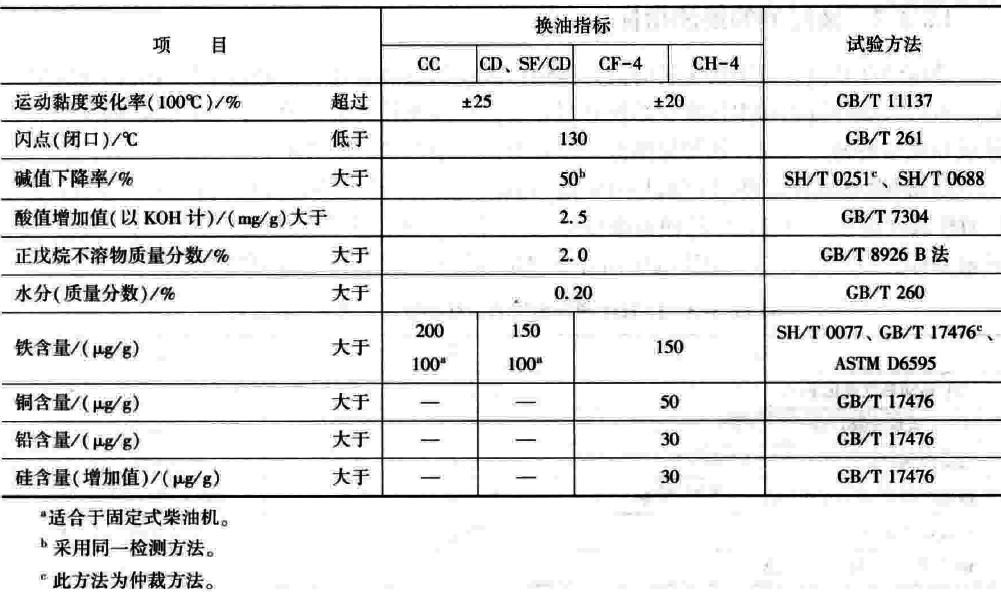
内燃机车柴油机油换油指标
TB/T 1739《内燃机车柴油机油换油指标》技术要求和试验方法下表,当使用中的油品有一项指标达到换油指标时应更换新油。
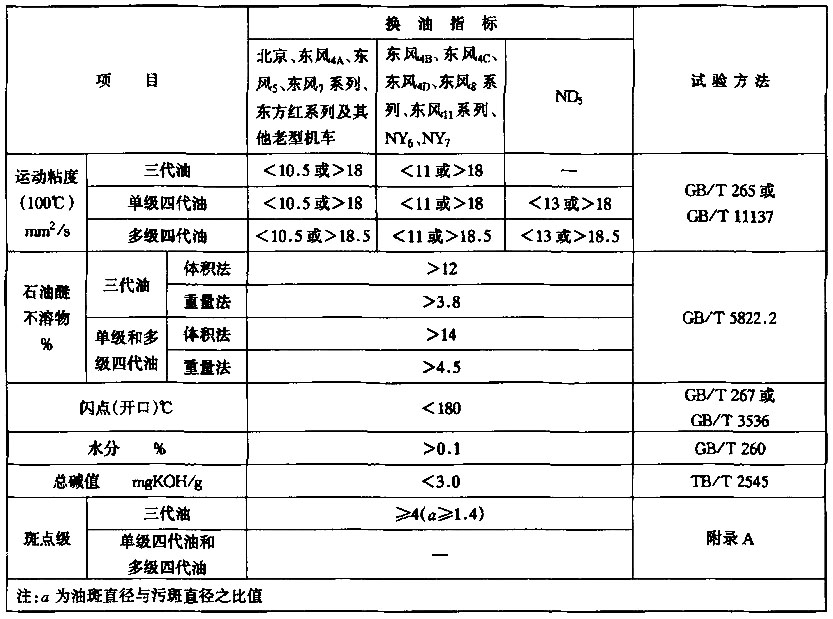
汽油机油换油指标
GB/T 8028-2010《 汽油机油换油指标 》规定了在使用过程中的汽油机油换油指标,适用于汽车汽油发动机和固定式汽油发动机所用汽油机油在使用过程中的质量监控和换油要求。技术要求和试验方法下表,当使用中的油品有一项指标达到换油指标时应更换新油。
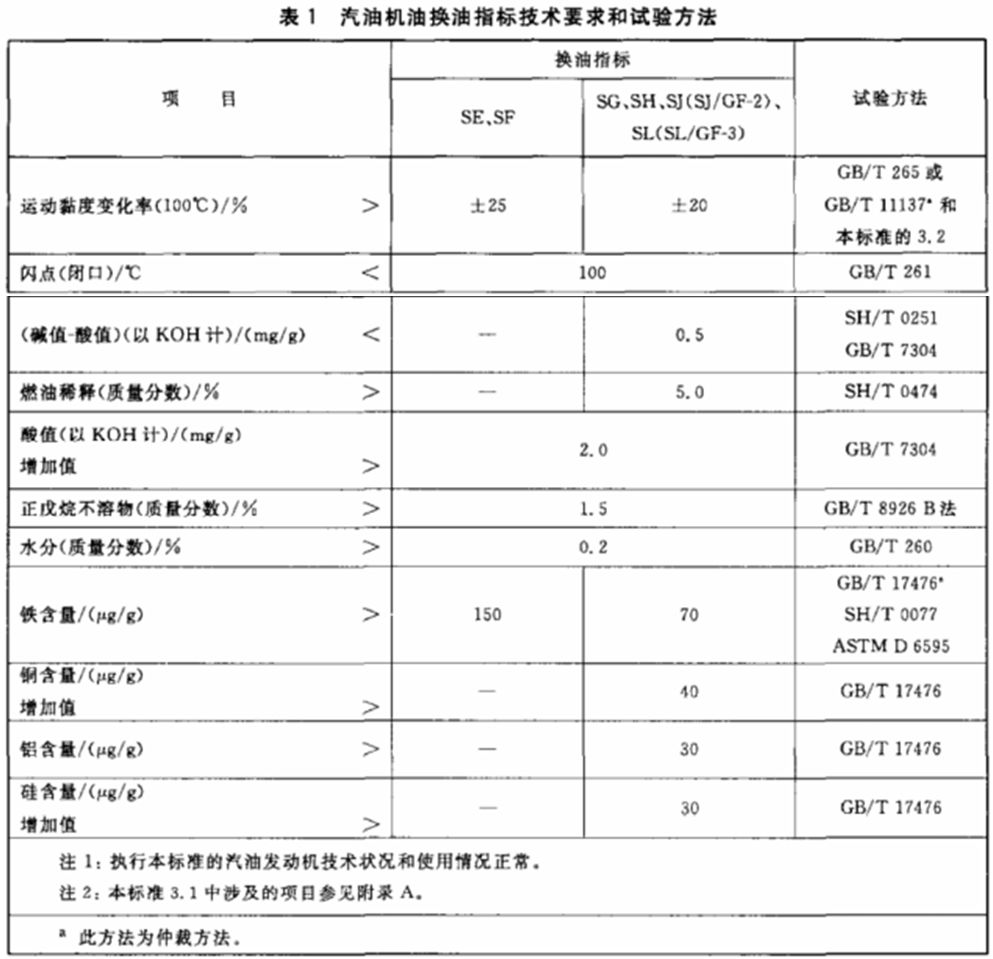
1.4.4 汽轮机油(涡轮机油/循环油)
SH/T0636-2013《L-TSA汽轮机油换油指标》对SH/T0636-1996(2003)进行了修订。增加水分和清洁度的要求。酸值和液相锈蚀的试验方法也进行了变更。试样应在油冷却器出口处采取。
酸值、水分、清洁度每3个月(工作时间)则定一次,运动粘度、抗乳化每6个月测定一次,液相锈蚀、旋转氧弹每12个月测定一次。
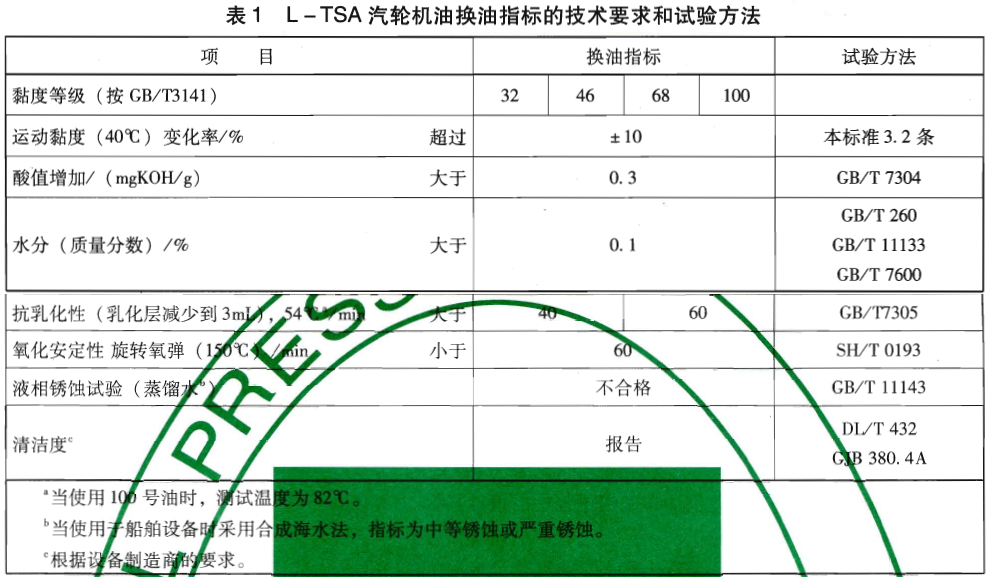
运行维护指标
1.4.5 涡轮机油维护管理导则
近年,国内外涡轮机油运行维护标准趋于统一,例如:GB/T 14541与ASTM D4378-13。
GB/T 14541《电厂用矿物涡轮机油维护管理导则》 运行监控指标如下图:

GB/T 14541-2017《电厂用矿物涡轮机油维护管理导则》运行控制指标
ASTM D4378《在用蒸汽、燃气和联合循环涡轮机的汽轮机矿物油监测的标准操作规程》运行监控指标如下图:
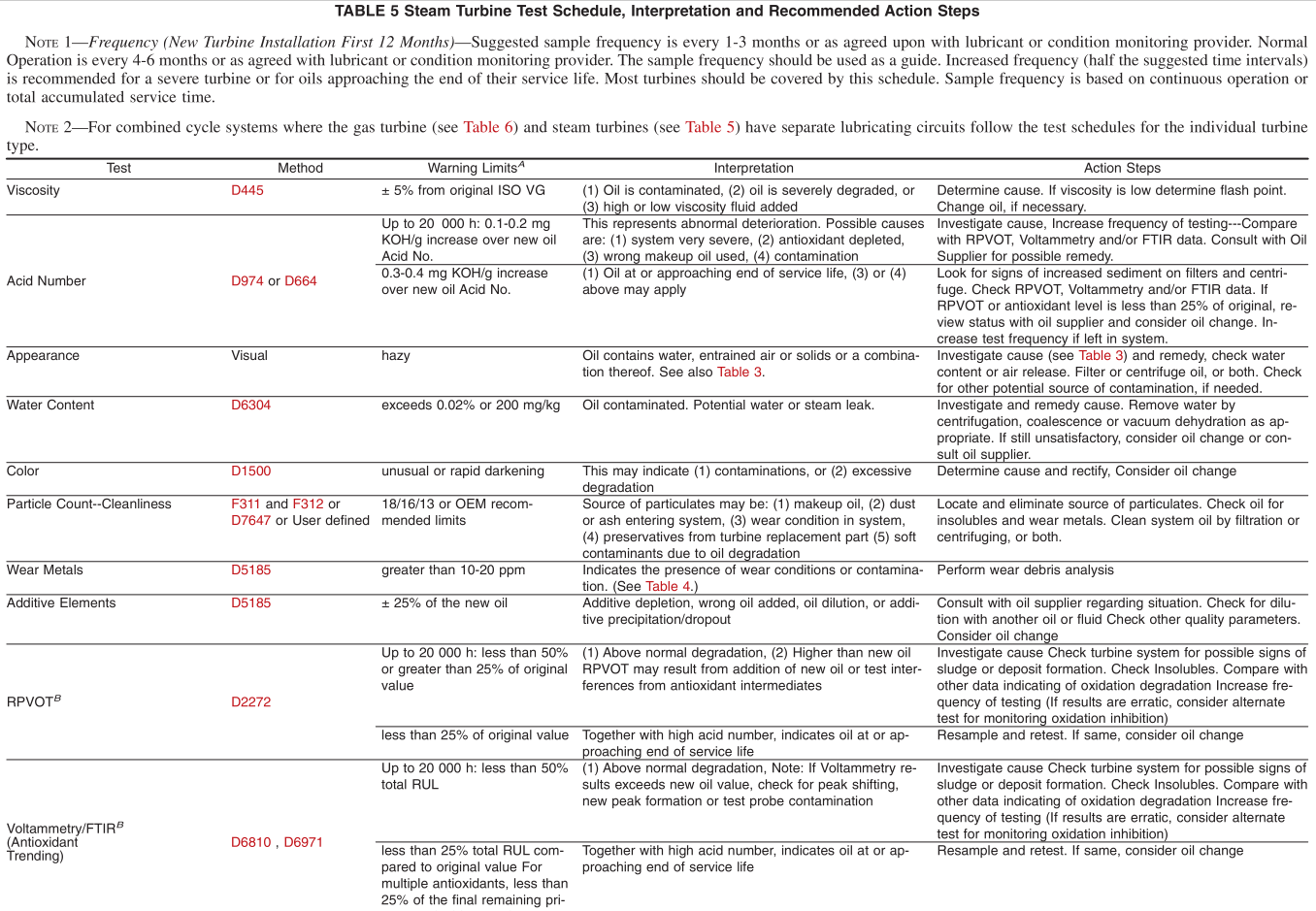
ASTM D4378-13《在用蒸汽、燃气和联合循环涡轮机的汽轮机矿物油监测的标准操作规程》运行监控指标
1.5 变化的原因
- 油被污染。
- 油被严重降解。
- 添加高粘度或低粘度流体。
1.6 采取措施
- 确定原因。
- 如果粘度低,则分析闪点。
- 如有必要,更换油。
1.7 相关知识点
- 美孚ATF 220润滑油粘度;
- 美孚SHC 600系列润滑油粘度记忆法;
- 冷冻机油分析前预处理,详见DIN51503-2-2015《冷冻机油换油标准》;
- 搅拌器齿轮箱粘度下降原因。
二、粘度指数(Viscosity Index)
2.1 基本概念
粘度指数表示润滑油粘度随温度变化的程度,用于定量表示润滑油的粘温特性。粘度指数越高,表示粘度受温度的影响越小,粘度对温度越不敏感。
2.2 监测的意义
用于评价润滑油的优劣,35—80为中粘度指数润滑油;80—110为高粘度指数润滑油;110以上为特高级粘度指数润滑油。粘度指数处于100—170的机油,为高档次多级润滑油。

2.3 分析方法
标准概述:GB/T 1995-1998等效采用ASTM D2270-1993计算石油产品粘度指数,GB/T1995-1998存在一个缺点,需要提前知道/预估粘度指数是大于100还是小于100,才能选取计算公式进行迭代计算。因此,ASTM D2270-10(2016)改进了计算方法,可以直接利用40℃和100℃运动粘度计算石油产品粘度指数。
根据ASTM D2270计算方法编制了粘度指数计算器等工具:粘度指数计算器、调和粘度计算器、粘度温度计算器。
2.4 变化的原因
粘度指数是液体的物理特性,一般不会发生变化,除非其组成成分发生了变化。润滑油的粘度随温度的升高,呈自然对数往下降[CY],见下图。
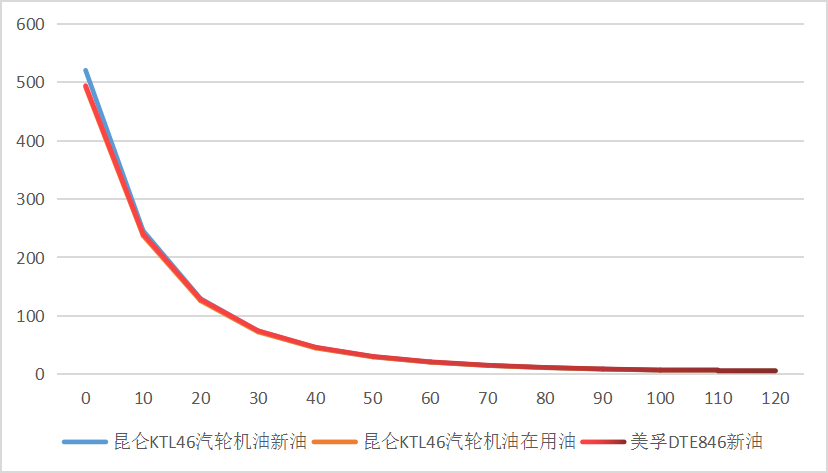
三种润滑油的粘温特性实测曲线
2.5 相关知识点
粘度指数越高,往往油品的精炼程度越高。合成油的粘度指数一般都在130以上,所以也经常用这个指标来鉴别真假润滑油。油品鉴别可参考四招教你鉴别真假润滑油一文。
三、水含量/水分(Water Content)
3.1 基本概念
润滑油中的水一般呈游离水、乳化水和溶解水三种状态。油中水污染的来源通常有两种情况:潮湿的空气和冷却水或冷凝水。一般而言,空气中的水份含量较少,因此进入润滑系统中会导致润滑油水分增高,但是含量不会太大;而冷却水或冷凝水进入润滑系统中,则会使油中水含量急剧增加。
3.2 监测的意义
油中过多的水将严重影响设备的润滑效果,主要表现在以下几个方面:
(1)水会促使油品乳化,降低油品粘度和油膜强度,使润滑效果变差;
(2)水会促使油品氧化变质,增加油泥,恶化油质,加速有机酸对金属的腐蚀;
(3)水会使油中添加剂发生水解反应失效,产生沉淀堵塞油路,不能正常循环供油;
(4)低温时,水会使润滑油流动性变差,黏温性能变坏;高温时,水会发生汽化,破坏油品,产生汽阻,影响润滑油的循环。
因此,一旦润滑油被水污染,不仅油品颜色会发生变化,且本身性能也会发生改变,因此需要及时采取相应措施进行脱水处理。
3.3 分析方法
测定润滑油中水含量的方法有三类:蒸馏法(GB/T 260, ISO 3733 ,ASTM D95)测定常规水含量、容量法(GB/T 11133、ASTM E203-16)和库仑法(GB/T 7600、ASTM D6304)测定微量水。
3.3.1 蒸馏法
蒸馏法测定水分的标准为 蒸馏法(GB/T 260, ISO 3733 ,ASTM D95) 。测试原理是将被测试样和与水不相溶的溶剂共同加热回流,溶剂可将试样中的水携带出来。不断冷凝下来的溶剂和水在接收器中分离开,水沉积在带刻度的接收器中,溶剂流回蒸馏器中。实验装置见下图:
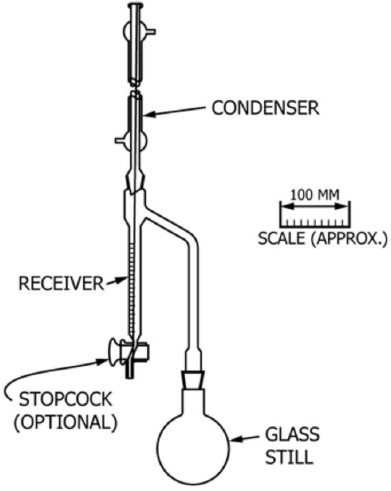
蒸馏法水份测定仪
GB/T260方法的水含量最小计量值为0.03%,若水含量小于0.03%则称为“痕迹”。在仪器拆卸后接受器中没有水存在,结果报告为“无”。容量法和库伦法精度更高,可以精确到ppm级别。
3.3.2 容量法和库伦法
容量法(GB/T 11133、ASTM E203-16)和库仑法(GB/T 7600、ASTM D6304)统称卡尔菲休水分测定法,二者测定的基本原理一致,在合适的弱碱如吡啶存在时,试剂中1mol的I2将1mol的SO2氧化为H2SO4,同时消耗2mol的H2O。
两者最大的区别在于I2的来源不同,容量法中的I2来自于滴定剂,根据消耗的卡氏试剂的消耗量,计算试样的水含量;库仑法中的I2则是通过电解含I离子的电解液产生,依据法拉第定律,电解所消耗的电量与碘的物质的量成正比,即电解1mol的碘,消耗1mol的水,需要2倍的96493C的电量,所以可通过滴定中消耗的电量计算试样的水含量。
容量法更适用于水分含量高的样品的测量,而库仑法则仅适用于微量、痕量水的测定,可达到ppm级。
3.4 评定标准(报警指标/换油指标)
不同标准规范对水含量的要求不同,产品出厂时一般要求为“无”。
使用中一般要求小于100ppm或200ppm。GB/T 7596-2008《电厂运行中汽轮机油质量》和GB/T 14541-2017《电厂用矿物涡轮机油维护管理导则 》要求≤100ppm;ASTM D4378-13要求小于200ppm 。
3.5 变化的原因
- 油被污染;
- 潜在的水或蒸汽泄漏。
3.6 采取措施
- 调查并纠正原因。
- 通过离心、聚结或真空脱水(视情况而定)去除水分。
- 如果仍然不满意,考虑更换机油或咨询石油供应商。
3.7 相关知识点
四、酸值(Total Acid Number;TAN)
4.1 基本概念
中和1g油液试样中全部酸性组分(KOH)所需要的碱量,以mgKOH/g表示。酸值分为强酸值和弱酸值两种,两者合并即为总酸值。通常所说的酸值即是指总酸值。国内常用酸值,国外常用总酸值TAN。
4.2 监测的意义
- 对新油酸值的检测,一方面能反映基础油的精制程度,酸值越低表示基础油的精制程度越深,质量越好;另一方面对于含有酸性添加剂的润滑油,酸值的高低一定程度上能间接反映润滑油酸性添加剂添加量的多少。酸值是成品油质量的控制指标。
- 对于不含酸性添加剂的在用油来说,酸值表示油品氧化变质的程度。油品在使用过程中与空气中的氧发生反应,生成一定量的有机酸,会对机械部件造成一定程度的腐蚀。所以,对在用油的监测中酸值是项重要检测项目,是判断设备润滑状况的重要指标。
- 含酸性添加剂的在用油,其酸值在运用初期会有所下降。这主要是油品酸性添加剂逐渐损耗的原因。之后酸值又逐步上升,这是因油品氧化变质所造成的。所以在对油液酸值的监测中,可以根据酸值的变化情况,并结合其他检测指标,综合分析获得添加剂消耗情况以及油品性能变化等多组信息。
4.3 分析方法
酸值的测试方法分为颜色指示剂法、电位滴定法、温度滴定法三大类。
4.3.1 颜色指示剂法:
颜色指示剂法 主要有GB/T 264《石油产品酸值测定法》和GB/T 4945《石油产品和润滑剂酸值和碱值测定法(颜色指示剂法)》。GB/T 4945等效采用ASTM D974。颜色指示剂法主要用于浅色油品的酸值检测,深色油品由于基体颜色的干扰,不适宜采用颜色指示剂法。基本原理是:用沸腾乙醇抽出试样中的酸性成分,然后用氢氧化钾乙醇溶液进行滴定。通过混合物颜色的变化,判断滴定终点,再计算出试样的酸值。
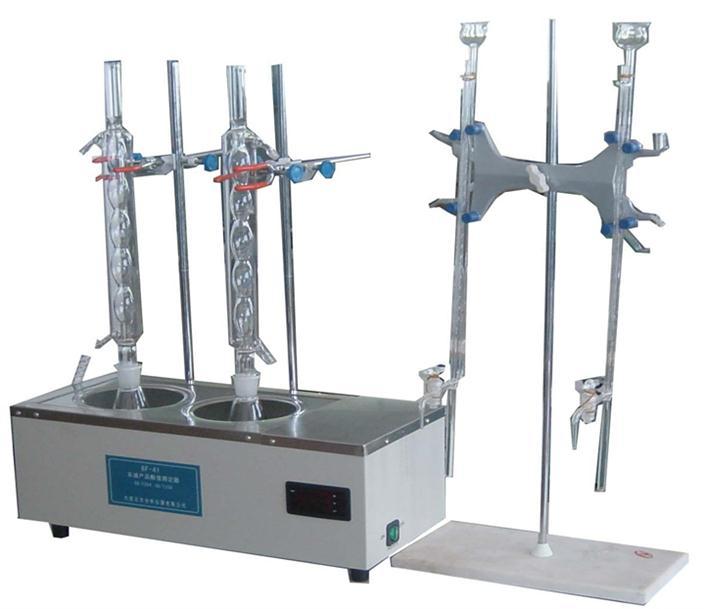
4.3.2 电位法:
电位法有GB/T 7304《石油产品和润滑剂酸值测定法》,等效采用ASTM D664。基本原理是:将试样溶解在含有少量水的甲苯异丙醇混合溶剂中,在用玻璃电极和参比电极作为电极对的电位滴定仪上,用氢氧化钾的异丙醇标准溶液进行滴定,以电位计读数对滴定溶剂作图,取曲线的突跃点作为滴定终点。若无明显的突跃点时,则以新配的水性酸和碱缓冲溶液的电位值作为滴定终点。
4.3.3 温度滴定法
温度滴定法是基于测定化学反应体系的温度变化来测定待测组分含量的。目前关于TAN温度滴定法的ASTM标准正在制定中。
4.3 评定标准(报警指标/换油指标)
不同种类的润滑油酸值是不一样的。例如:汽轮机油酸值较低一般要求小于0.2(含极压添加剂的小于0.3);齿轮油的较高可达到0.5-0.6。主要是因为齿轮油添加的抗磨剂/极压添加剂较多,显酸性(例如:二烷基二硫代磷酸锌——ZDDP)。
ASTM D974实验时间达到20000小时:比新的油酸值增加0.1-0.2 mg KOH/g。 ASTM D664 比新的油酸增加0.3-0.4 mg KOH/g。
4.5 变化的原因
润滑油在使用过程中与氧气接触,基础油氧化生成过氧化物,过氧化物反应生成醛、酮、醇,最终产物为各种有机酸(主要为羧酸、环烷酸),降解的结果使油的各项指标变差,性能变坏,危及设备的正常运转及使用寿命。润滑油氧化机理可参考《润滑油氧化学化方程式》一文。
- 系统非常严重。
- 抗氧化剂耗尽。
- 使用了错误的补充油。
- 污染。
- 在使用寿命结束或接近使用寿命结束时。
4.6 采取措施
- 调查原因,增加测试频率——与RPVOT、伏安法和/或FTIR数据进行比较。与润滑油供应商协商可能的补救措施。
4.7 相关知识点
4.7.1 几个相关的概念
酸值、碱值和中和值:酸值是表示润滑油中含有酸性物质的指标,单位是mgKOH/g。碱值是表示润滑油中碱性物质含量的指标,单位是mgKOH/g。碱值亦分强碱值和弱碱值两种,两者合并即为总碱值(简称TBN)。我们通常所说的”碱值”实际上是 指”总碱值(TBN)”。中和值实际上包括了总酸值和总碱值。但是,除了另有注明,一般所说的”中和值”,实际上仅是指”总酸值”,其单位是mgKOH/g。
4.7.2 酸值与腐蚀的关系
GB/T4945第5.2条:由于各种各样的氧化产物都可能对酸值造成影响,而且有机酸的腐蚀性变化也很大,因此本方法不能表明在使用条件下油品的腐蚀性。酸值与油品对金属的腐蚀趋势之间没有一定的相关性。加有复合添加剂的发动机油通常用本方法既可测出酸值,又可测出碱值。GB264未提及腐蚀相关内容。
五、机械杂质(Mechanical Impurities)
5.1 基本概念
所有悬浮和沉淀于润滑油中的固体杂质统称为机械杂质。机械杂质主要来源于生产、储存、使用过程中的外界污染、机器磨损和腐蚀污染。大部分情况下是由粉尘、铁屑和积炭颗粒组成。
5.2 监测的意义
- 机械杂质是新油质量的重要控制指标,因为油品在生产、储运过程中都会带来机械杂质。
- 对于在用油品来说,定期检测油中机械杂质含量的变化趋势也十分必要。机械杂质是工矿企业润滑管理的常规监测项目之一。因为油品中的外来粉尘砂粒污染以及机件磨损的磨损碎屑等都会加速机械设备的异常磨损,同时还会堵塞油路及过滤器,导致设备产生润滑故障。机械杂质是判断设备是否需要换油的指标之一。
- 不同牌号的新油,其出厂的机械杂质含量指标有所不同。有些品牌的内燃机润滑油由于其金属的盐类添加剂的添加量较高,会使新油的机械杂质含量偏高,有别于其他种类的润滑油。可以区别对待,但必须满足出厂标准。
5.2 分析方法
国内测定润滑油机械杂质采用GB/T 511《润滑油机械杂质测定法》,该标准修改采用原苏联标准rOCT 6370-1983( 1997)《石油、石油产品和添加剂机械杂质测定法》,进口品牌一般使用ASTM-D473《用萃取法测定原油和燃料油中沉积物的标准试验方法》,这三个测试方法的原理一样。
称取一定量的试样,溶于所用的溶剂(95%乙醇、乙醚、甲苯、乙醇-甲苯、乙醇-乙醚)中,用已恒重的滤纸或微孔玻璃过滤器过滤,被留在滤纸或微孔玻璃过滤器上的杂质即为机械杂质。

5. 4 评定标准(报警指标/换油指标)
机械杂质的含量≤0.005%(质量分数)时,则可认为无机械杂质。润滑油产品和使用过程中均要求“无”。
5.5 变化的原因
- 污染。
- 磨损。
5.6 采取措施
- 调查原因,增加测试频率——与清洁度、状态监测进行比较,与设备供应商协商可能的补救措施。
5.7 相关知识点
机械杂质是用溶剂(95%乙醇、乙醚、甲苯、乙醇-甲苯、乙醇-乙醚)去除可溶物后,过滤剩下的物质。一定要与甲苯不溶物,正戊烷不溶物的区别。 因为堵塞滤芯的不仅有机械杂质,还有甲苯不溶物,正戊烷不溶物。 前者是系统带入或摩擦产生的,后者是油品氧化或与介质反应生成的。
六、闪点(Flash Point)
6.1 基本概念
润滑油(或燃油)的蒸气与空气所形成的混合气与火焰接触发生瞬间闪火时的最低温度称为闪点(又叫闪火点)。
闪点又分为开口闪点和闭口闪点。开口闪点用于重质润滑油和深色润滑油闪点的测定,闭口闪点用于轻质润滑油和燃料油的闪点测定,一般情况下,开口闪点要比闭口闪点高出10-30℃。润滑油闪点一般指开口闪点。
6.2 监测的意义
- 闪点值能够用于运输、贮存、操作和安全管理等方面,可作为分类参数来定义“易燃物质”和“可燃物质”,其准确定义参见它们各自的特殊法规和相关标准。
- 闪点值可用于表示在相对非挥发或非可燃性物质中是否存在高挥发性或可燃性物质。闪点试验是对未知组成材料进行其他研究的第一步。
- 闪点试验不能用于有潜在不稳定的、易分解的或爆炸性的样品,除非事先确认在本标准规定的温度范围内,加热与闪点测定仪金属部件相接触的规定量的此类样品不会产生分解、爆炸或其他不良影响。
- 对含卤代烃样品得到的闪点试验结果要谨慎分析,因为此类样品可能会产生异常结果。
6.3 分析方法
闪点分为开口闪点和闭口闪点,润滑油闪点一般指开口闪点。开口闪点用GB/T3536、ASTM-D92、ISO 2592克利夫兰开口法测定。闭口闪点用GB/T261、ASTM D93、ISO 2719宾斯基-马丁闭口杯法测定。
6.3.1 开口闪点
开口闪点用GB/T3536、ASTM D92《克利夫兰石油产品闪点和燃点的测定 开口杯法》。该方法是把试样装入仪器的坩埚中到规定的刻线,先迅速升高试样的温度,当接近闪点时再缓慢地以恒速升温。在规定的温度间隙下,用点火器火焰按规定通过试样表面,使试样表面上的蒸气发生闪火的最低温度作为该样品的开闪点。
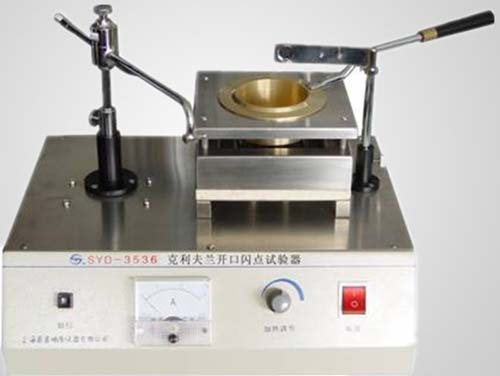
开口闪点测定仪
6.3.2 闭口闪点
闭口闪点用GB/T261、ASTM D93、ISO 2719宾斯基-马丁闭口杯法测定。该方法是把试样装入封闭的加热杯内,在连续搅拌下用很慢的恒定速度加热。在规定的温度间隙和同时中断搅拌的情况下,将一小火焰引入杯内。试验火焰引起试样上的蒸气闪火时的最低温度即为闭口闪点。

6.4 评定标准(报警指标/换油指标)
闪点是一项安全指标,使用过程中既有相对标准,也有绝对标准。相对标准是与前次测定值之差不大于10℃。绝对标准是不能低于180℃。
6.5 变化的原因
- 污染。
6.6 采取措施
- 确定原因,检查其他品质参数,考虑换油。
6.7 相关知识点
- 闪点是一项安全性指标。在选用润滑油时,应根据使用温度考虑选择润滑油的闪点指标。一般要求闪点比使用温度高出20-30℃,保证使用安全和减少油品挥发损失。
- 在用油闪点的高低既取决于自身的特性,还取决于油中是否混人轻质组分及其含量的多少。如发动机油的闪点在使用过程中下降较快,则表明该发动机燃油泄漏严重,影响润滑效果,应立即修理发动机。对于发动机的油液监测,闪点是必检项目。
- 对于某些润滑油品,若同时测开口、闭口闪点,则可以作为油品组分均匀性、挥发性的测定方法。这是因为测开口闪点时有一部分油蒸气挥发了,若同一油样开口、闭口闪点之差太大,则表明该油组分不均匀,易挥发,在使用中应加以注意。
- 冷冻机组等湿式压缩机组在使用过程中,润滑油与烃类介质接触,烃溶入润滑油使其其闪点显著下降,闪点不能代表润滑油的真实值,实验前应当进行脱气处理,详见DIN 51503-2-2015《冷冻机油换油指标》。
更多请参考《开口闪点与闭口闪点区别与选择》一文。
七、水分离性/抗乳化性/破乳化度(Water Separability)
7.1 基本概念
润滑油水分离性也叫抗乳化性或破乳化度。是一种液体以极微小液滴均匀地分散在互不相溶的另一种液体中,形成乳状液的现象。它是两种液体的混合而并非相互溶解。润滑油在使用过程中与水接触,在一定条件下载会产生不同程度的乳化。
润滑油的抗乳化性或破乳化度是指油品遇水发生乳化经过加温静置能迅速实现油水分离的能力。
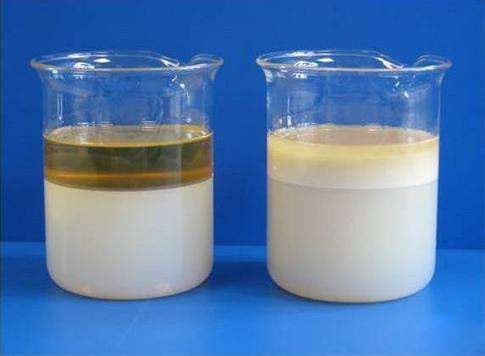
润滑油和水的乳化液
7.2 监测的意义
- 水分会促使油品乳化,降低油品粘度和油膜强度,使润滑效果变差。
- 水分会促使油品氧化变质,增加油泥,恶化油质,加速有机酸对金属的腐蚀。水分会使油中添加剂发生水解反应失效,产生沉淀堵塞油路,不能正常循环供油。
- 低温时,水分会使润滑油流动性变差,黏温性能变坏;高温时,水分会发生汽化,破坏油品,产生汽阻,影响润滑油的循环。
7.2 分析方法
润滑油水分离性也叫抗乳化性,GB/T 7305等效采用ASTM D1401《石油和合成液水分离性测定法》。近似标准有:GB/T 8022《润滑油抗乳化性能测定法 中高粘度》和GB/T 7605《运行中汽轮机油破乳化度测定法》。
方法概要:在量筒中装入40ml试样和40ml蒸馏水,并在54℃或82℃(40℃粘度>90mm2/s时)下搅拌5min。每隔5min观察一次乳化液,当乳化层<3ml时,记录分离所需的时间。静止30min或60min后,如果乳化液没有完全分离,或乳化层没有减少为3ml或更少,则记录此时油层(或合成液)、水层和乳化层的体积和时间。
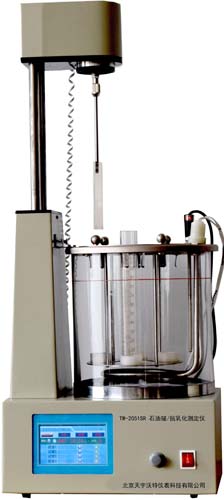
水分离性测定仪
在日常油液监测工作中,常用的方法是GB/T7305,测试过程中,对于成品油是用蒸馏水来检测,但对于监测在用油的抗乳化性能时,最好要用设备现场可能进入润滑油的水质来检测。例如检测化工厂轴承油的抗乳化性能时,应用循环冷却水,蒸馏水和冷却水所测的差别较大,这是因为冷却水中的污染物相对较多,加强了油品的乳化性能。
7.4 评定标准(报警指标/换油指标)
水分离性/抗乳化报告解读:39-38-3(20)表示:油层厚度-水层厚度-乳化液厚度(经历时间)。40℃粘度小于100cst的润滑油实验时间不超过30分钟,40℃粘度大于等于100cst的润滑油实验时间不超过30或60分钟。
7.5 变化的原因
影响润滑油水分离性能的主要因素有基础油的精制程度、油品污染度和油品添加剂的配伍状况。对于调配好的成品油,使用过程中产生的机械杂质、油泥等污染物都会严重影响油品的水分离性或破乳化度。
- 污染。
- 劣化。
7.6 采取措施
与指示降解程度的其他试验数据进行比较。如果含水量和锈蚀程序A是可接受的,则无需采取任何措施。
7.7 相关知识点
乳化必须具有三个必要条件:一是必须有互不相溶(或不完全相溶)的两种液体;二是两种混合液中应有乳化剂(能降低界面张力的表面活性剂)存在;三是要有形成乳化液的能量,如强烈的搅拌、循环、流动等。
八、空气释放性(Air Release Properties)
8.1 基本概念
游离在润滑油里的空气有两种形式:滞留在油液内部的是气泡,漂在油面上的是泡沫。气泡浮到油面上,就成为泡沫。气泡上升到油面上所需的时间,我们称之为润滑油的空气释放性。对于浮在油面上的泡沫,泡沫破裂、消失所需的时间,我们称之为泡沫特性,或者抗泡性。
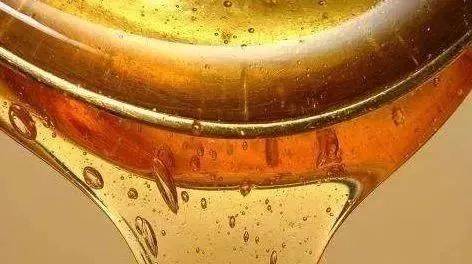
8.2 监测的意义
润滑油与设备(如轴承、联轴器、齿轮、泵和回油管)中的空气搅动可能会在油中产生细小气泡的分散。如果储液罐中的停留时间太短,气泡无法上升到油表面,则空气和油的混合物将在润滑油系统中循环。这可能导致无法保持油压(尤其是离心泵),轴承和齿轮中的油膜不完整,以及液压系统性能差或故障。夹带的空气会导致涡轮机和液压系统的控制出现气穴和灵敏性。
8.3 分析方法
SH/T 0308-92(2004)参照采用ASTM D3427《润滑油空气释放值测定法》编制。
将试样加热到25, 50或75℃,通过对试样吹入过量的压缩空气,使试样剧烈搅动,空气在试样中形成小气泡,即雾沫空气。停气后记录试样中雾沫空气体积减到0.2%的时间(用min表示)。
40℃时,粘度 | 温度选择 |
<9 mm2/s | 25 ℃ |
9~90 mm2/s | 50 ℃ |
>90mm2/s | 75 ℃ |
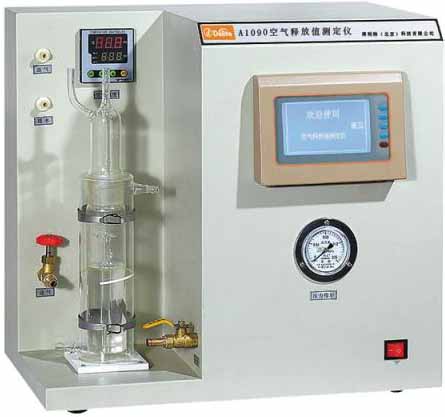
8.4 评定标准(报警指标/换油指标)
汽轮机油的空气释放值一般在4-5min,较好的产品可达2~3min。一般要求不超过新油的2倍。
API 614《石油、石化和天然气工业润滑、轴封和控制油系统及辅助设备》对润滑油油箱大小的要求是多少?
8.5 变化的原因
- 污染。
- 加入了过量的消泡剂。
- 过多的防锈剂。
8.6 采取措施
- 观察系统并排查原因。纠正的原因。与其他分析结果比较考虑加换油。
8.7 相关知识点
混有空气(无论是大气泡还是微小的空气雾沫)的液压油在工作时会使系统的效果降低,润滑条件恶化。此外,还会造成驱动系统压力不足和传动反应迟缓。严重时会产生异常的噪声、气穴腐蚀、震动,甚至损伤设备,并使油品老化。液压油标准中有此项指标要求,是因为在液压系统中,如果溶于油品中的空气不能及时释放出来,将会影响液压传递的精确性和灵敏性,不能满足液压系统的使用要求。
更多请参见《润滑油中气泡如何产生的,有啥危害》一文。
九、泡沫特性/抗泡性(Foaming Characteristics)
9.1 基本概念
润滑油在使用过程中与混入空气接触,经循环产生气泡,我们通常把浮在油品表面的气泡称为泡沫,常用体积来表示。
润滑油的泡沫特性/抗泡性有2项,一是泡沫倾向性,二是泡沫稳定性。泡沫倾向性是产生泡沫的能力;泡沫稳定性是泡沫破裂/消失的能力。
9.2 监测的意义
在高速传动、大容量泵送和飞溅润滑等系统中,油的泡沫倾向可能是一个严重的问题。可引起润滑不足、汽蚀和润滑油溢出损失、可导致机械故障。
9.3 分析方法
GB/T 12579等效采用国际标准ISO 6247《润滑油泡沫特性测定法》编制。进口品牌润滑油一般采用ASTM D892泡沫特性测定法,三个方法基本一致。
SH/T 0722《润滑油高温泡沫特性测定法》等效采用ASTM D6082。适用于测定传动液和发动机油在150℃时泡沫特性。
润滑油泡沫特性测定法方法概要:试样在24℃时,用恒定流速的空气吹气5min,然后静止10min,分别记录试样中泡沫的体积。取第二份试样,在93.5℃下进行重复上述操作,记录第二组数据;第二份试样泡沫消失后,再在24℃下重复试验,记录第三组数据。
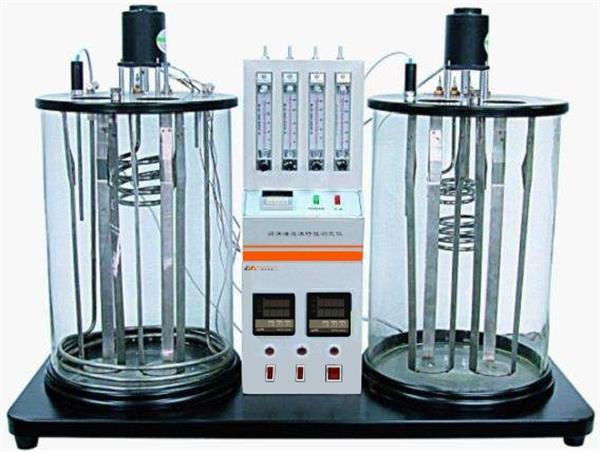
报告给出3组共计6个数字,各数字含义分别如下表。
报告 | 数据解读 |
前24℃:200/5 | 第一份试样在24℃时: 泡沫倾向性为200mL/泡沫稳定性为5mL |
93℃:50/0 | 第二份试样在93℃时: 泡沫倾向性为50mL/泡沫稳定性为0mL |
后24℃:210/5 | 第二份试样在24℃时: 泡沫倾向性为210mL/泡沫稳定性为5mL |
9.4 评定标准(报警指标/换油指标)
超过以下限制:倾向性450毫升和稳定性10毫升;不同油品的标准略有不同。
9.5 变化的原因
- 污染。
- 消泡剂耗尽。
- 过多的防锈剂。
9.6 采取措施
- 高倾向性数据应通过油层目视检查进行确认。
- 纠正的原因。
- 与油供应商确认是否可采取排气、加换油、过滤、再生。
9.7 相关知识点
几个相关的概念比较:
《润滑油泡沫特性、水分离性、空气释放性的区别》 一文详细讲解了润滑油油抗泡性(泡沫倾向性/泡沫稳定性)、抗乳化(水分离性)、空气释放性概念的区别。
十、氧化安定性(Oxidation Stability)
10.1 基本概念
润滑油的抗氧化安定性是指:润滑油在一定的外界条件下,抵抗氧化作用的能力。所有的润滑油在使用过程中都会发生氧化作用,逐渐生成一些醛、酮、酸类和胶质、沥青质等物质,氧化安定性则是抑制上述不利于油品使用的物质生成的性能。一些使用寿命较长的工业润滑油都有此项指标要求,因而成为这些种类油品要求的一个特殊性能。
10.2 监测的意义
- 油品变质,产生酸性物质,导致机件腐蚀,锈蚀
- 润滑剂变成腐蚀液,大大缩短机件的寿命
- 粘度增加,导致油耗和阻力的增大,磨损加剧(摩擦热增加)
- 产生漆膜和油泥,对汽轮机和液压系统的破坏,造成伺服阀,推进阀的失效、积碳对内燃机系统的破坏
- 功率损失(15%以上)
- 大大缩短机件的寿命
- 堵塞滤清器
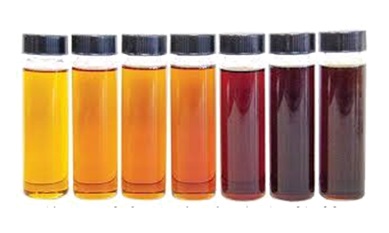
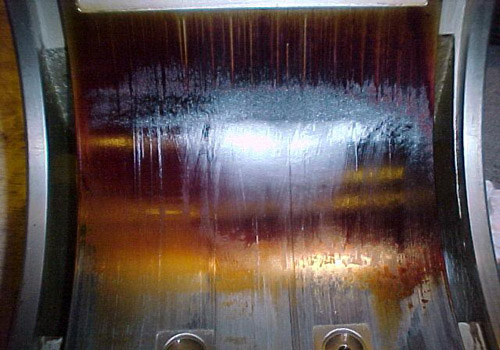
10.3 分析方法
测定油品氧化安定性的方法很多,根据用途可分为三类[CY]:
- 一是研发/台架实验:主要用于产品的研究、开发、质量控制等用途的台架试验,例如:SH/T 0719《润滑油氧化诱导期测定法 PDSC》,等效采用ASTM D6186;
- 二是产品性能评价实验:新油品性能评估分级(美孚DTE Light、 DTE 732、 DTE 832都是美孚公司32号汽轮机油),例如:
- (1)GB/T 12581《润滑油氧化安定性测定法 TOST》,特别是易被水污染的润滑剂的氧化安定性,等效采用ASTM D943-20;
- (2)ASTM D7873《120℃不含水的加抑制剂涡轮油的氧化稳定性和不溶形成 Dry TOST》。
- (3)SH/T 0450《合成油氧化腐蚀测定法》;
- (4)SH/T 0123《极压润滑油氧化性能测》等效采用ASTM D2893测定润滑油的氧化稳定性。
- (5)SH/T0196《润滑油抗氧化安定性测定法》等效采用苏联国家标准TOC1981-52。
- (6)SH/T 0832《润滑油热表面氧化的测定 压力差示扫描量热法》修改采用欧洲协调委员会标准CEC L-85-T-99《润滑油热表面氧化测定法 压力差示扫描量热法》。
- 三是在用油剩余寿命实验:
- (1)SH/T 0193《润滑油氧化安定性的测定-旋转氧弹法 RPVOT BVOT》,等效采用ASTM D2272-14a;
- (2)ASTM D6971《润滑油抗氧化剂含量测定-RULER》等。RULER:剩余使用寿命评估程序。通过测量润滑油中抗氧化剂的剩余浓度来定量地测定润滑油的剩余使用寿命。润滑油中抗氧化剂种类主要分为胺类和酚类。酚类抗氧化剂易挥发,先降解;胺类抗氧化剂耐高温,后降解,但易形成漆膜。
- (3)SH/T 0931《在用石油基和烃基润滑油氧化状态监测 傅里叶变换红外光谱(FT-IR)趋势分析法》,修改采用ASTM D7414。润滑油与空气中的氧气 生反应时,会生大量的氧化产物,如醛、酮、酯和羧酸。这些产物都是含羰基的物质,通过FT-R测定1800cm-1~1670cm-1范围内羰基基团所引起的特征吸收,来衡量润滑油氧化程度。采用光谱峰高或峰面积表达润滑油氧化值。
大部分实验基本原理相同:一定量的油品+空气(或氧气)+金属催化剂(铜)的存在下,在高温下氧化一定时间,然后测定油品的酸值、粘度变化及沉淀物的生成情况。
下面以常用的在用油性能检测实验 SH/T 0193为例介绍:
方法概要:将试样、水和铜催化剂线圈放入一个带盖的玻璃盛样器内,置于装有压力表的氧弹中。氧弹充入620kPa压力的氧气,放入规定的恒温油浴中(汽轮机油150℃,矿物绝缘油140℃),使其以100r/min的速度与水平面成30°角轴向旋转。试验达到规定的压力降所需的时间(min)即为试样的氧化安定性。结构图如下:
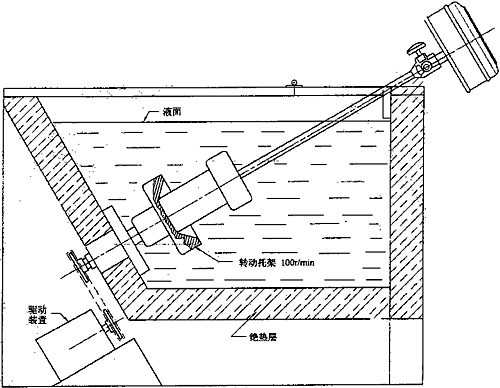
润滑油氧化安定性的测定-旋转氧弹法
10. 4 评定标准(报警指标/换油指标)
在用润滑油评价方法分为3类,一类是看抗氧剂的剩余含量,例如伏安法(RULER)、FT-IR(傅立叶红外光谱),一般要求抗氧剂含量不能低于新油的25%;二是看润滑油实际的抗氧能力,例如,旋转氧弹RPVOT,一般要求不小于新油的50%或一定的数值。不同油品/标准略有不同。 二是看氧化物生产的量,例如红外光谱。
10.5 变化的原因
- 润滑油与空气中的氧气 生反应时,会生大量的氧化产物,如醛、酮、酯和羧酸。导致酸值变化、粘度变化及沉淀物的生成。
10.6 采取措施
- 增加检测频率
- 检查油系统是否有淤渣或沉淀物形成的迹象。
- 检查不溶物。
- 添加抗氧剂或加换油
10.7 相关知识点
1、润滑油是如何氧化的,氧化方程式是什么?
2、润滑油氧化机理及危害。
3、润滑油为何要具备良好的氧化稳定性与热稳定性?
十一、防锈性能/液相锈蚀(Rust-Preventing Characteristics)
11.1 基本概念
- 锈蚀:指金属表面与水分及空气中氧接触生成金属氧化物的现象。
- 缓蚀性:指润滑油品阻止与其相接触的全属表面被氧化的能力。
11.2 监测的意义
很多情况下,如汽轮机中,水分可能混入润滑油,从而使铁部件生锈。 液压油、循环油 等润滑油也存在这样的可能。所以抗氧防锈是润滑油的基本性能,它能对润滑系统中的过流部件能起到很好的保护。新设备或闲置设备也需要涂刷防锈油以保护其表面不被锈蚀。
11.3 分析方法
GB/T 11143《加抑制剂矿物油在水存在下防锈性能试验法》用于汽轮机油、液压油、循环油等其他油品及比水密度大的液体的防锈性能测试,它修改采用ASTM D665 ;ASTM D3603《汽轮机油在有水的情况下防锈特性的标准试验方法 水平圆盘法》用于新油性能评定。
GB/T 11143方法概要:将300mL试样和30mL蒸馏水或合成海水混合,把圆柱形的试验钢棒全部浸在其中,在60℃下进行搅拌。建议试验周期为24 h,也可根据合同双方的要求,确定适当的试验周期。试验周期结束后观察试验钢棒锈蚀的痕迹和锈蚀的程度。
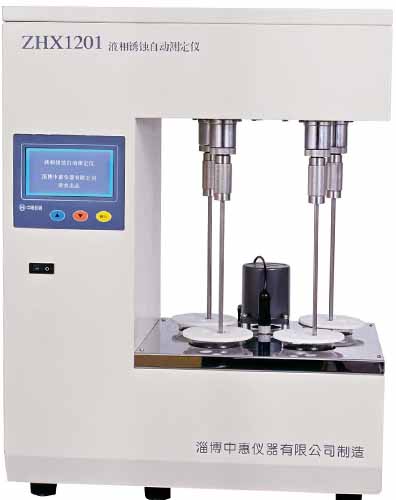
液相锈蚀测定仪
- 无锈:实验钢棒上没有锈斑。
- 轻微锈蚀:限于锈点不超过6个,每个锈点直径不大于1mm。
- 中等锈蚀:锈蚀超过6个点,但小于试验钢棒表面积的5%。
- 严重锈蚀:锈蚀面积超过试验钢棒表面积的5%。
11.4 评定标准(报警指标/换油指标)
无论是润滑油产品标准还是使用过程中的评价标准都要求“无锈”。
11.5 变化的原因
- 添加剂消耗。
- 过度污染。
11.6 采取措施
- 更换油。
- 咨询油供应商是否可添加防锈剂。
11.7 相关知识点
很多情况下,如汽轮机中水分可能混入润滑油,从而使铁部件生锈。本试验能表明加入适量抑制剂的矿物油,有助于防止这种情况引起的锈蚀。
对于防锈油,其缓蚀性则用GB/T 2361《防锈油脂湿热试验法》和SH/T 0081《防锈油脂盐雾试验法》。
十二、不溶物(Insolubles)
12.1 基本概念
不溶物指标是指在用润滑油中不溶于正戊烷或甲苯溶剂的物质含量。不溶物的多少能反映在用润滑油的污染和劣化情况。不溶物按其溶剂溶解性分类为正戊烷不溶物和甲苯不溶物两类。
正戊浣不溶物主要指油中磨损金属颗粒、粉尘杂质、积炭等固体杂质;以及油品裂解、降解产生的树脂状物质。
甲苯不溶物则主要指油中的磨损金属颗粒、粉尘杂质和积炭等固体物质。
12.2 监测的意义
在用油正戊不溶物和甲苯不溶物的差值能反映油品裂化衰败的程度,润滑油与工艺介质的相溶情况。
12.3 分析方法
GB/T 8926-2012《在用的润滑油不溶物测定法》,修改采用ASTM D893。
方法概要:将一份有代表性的在用润滑油试样与正戊烷混合,离心分离后,倾倒出上层油溶液,用正戊烷洗涤沉淀物两次,干燥,再称重,得到正戊烷不溶物。
测甲苯不溶物时,把另一份试样与正戊烷混合,并离心分离;将沉淀物用正戊烷洗涤两次,用甲苯-乙醇溶液洗涤一次,再用甲苯洗涤一次,然后干燥不溶解物质,并称重,得到甲苯不溶物。
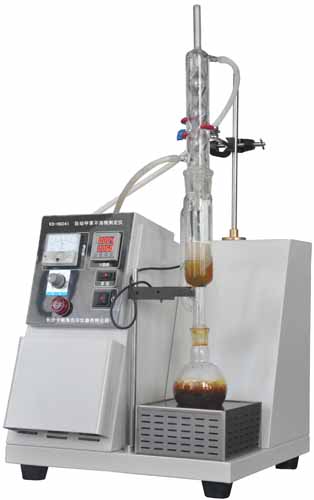
甲苯不溶物含量测定仪
12.4 评定标准(报警指标/换油指标)
正戊烷不溶物:汽轮机油质量分数<0.1%,柴油机油<2%,汽油机油<1.5%。
12.5 变化的原因
- 设备磨损。
- 污染。
- 油或添加剂的降解。
- 油与工艺介质接触后反应。
12.6 采取措施
- 调查原因。
- 过滤油或离心油,或两者兼有。
- 考虑换油。
12.7 相关知识点
正戊烷不溶物、甲苯不溶物、机械杂质三者的关系。
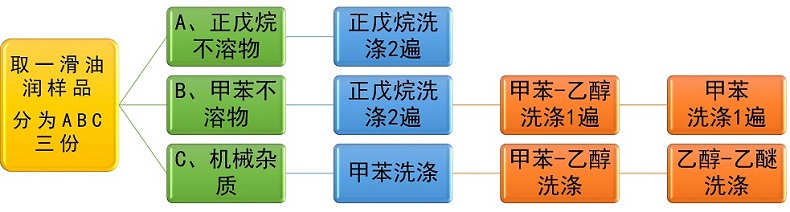
质量:正戊烷不溶物>甲苯不溶物>机械杂质
- 不溶物是评价在用润滑油污染程度及衰败变质的一项质量指标。主要用于对在用润滑油的检测,以判断油品的污染变质情况。
- 对于柴油机油来说,不溶物是评定其质量变化的尤为重要的指标。
- 若同时测定正戊烷不溶物和甲苯不溶物,能有效检测油品高温氧化、裂解所形成树脂状物质的数量。而树脂状物质是油泥的重要组成部分,反映了油品的衰败程度。(讲浮环密封案例)
- 国外许多石油公司和柴油机供应商都用不溶物作为评价柴油机油质量衰败程度的重要指标。我国也有一些企业用该项指标来指导设备定质换油。
案例:浮环密封,润滑油与工艺介质接触导致润滑油过滤器压差异常上涨,切换密封气并对油品进行净化,延长机组运行至检修周期。
十三、碱值(Base Number)
13.1 基本概念
总碱值:中和1g试样中全部碱性组分所需要的酸量,并换算为等当量的碱量,以mgKOH/g表示。
13.2 监测的意义
- 总碱值是内燃机油的重要质量指标,能反映内燃机油中磁性消净分散深加剂的多少。在内燃机运行过程中,燃料油中的含硫组分在燃烧过程中产生SO2,与冷凝水接触生成稀硫酸,这对柴油机零部件具有强烈的腐蚀性。因此内燃机油中必须要有足够量的碱性添加剂来中和燃料油产生的酸性物质。
- 内燃机油的工作环境温度较高,易与空气中的氧发生化学反应产生酸性物质,使油品氧化变质,产生较多的油泥。因此内燃机油中的碱性添加剂还起到防止油品氧化的作用,通过检测总碱值可以监测碱性添加剂防油品氧化的能力。
- 对新油总碱值的检测,能反映油品质量是否达到相应等级柴油机油的质量指标。对在用油品总碱值的检测,可反映油中碱性添加剂的损耗和油品氧化变质的程度,从而指导设备视情况换油或增添高碱值的新油。例如柴油机发电厂用的高碱值柴油机油,在使用过程中碱值会不断下降。为了保证柴油机油中有足够的碱值,就需定期检测碱值的变化,并不断补加新油。
13.3 分析方法
SH/T 0251《石油产品碱值测定法 高氯酸电位滴定法》修改采用ASTM D2896。该方法规定可用正滴定法或返滴定法,通常用正滴定法。
方法概要:将试样溶解于滴定溶剂中,以高氯酸-冰乙酸标准滴定溶液为滴定剂,以玻璃电极为指示电极,甘汞电极为参比电极进行电位滴定,用电位滴定曲线的电位突跃来判断滴定终点。
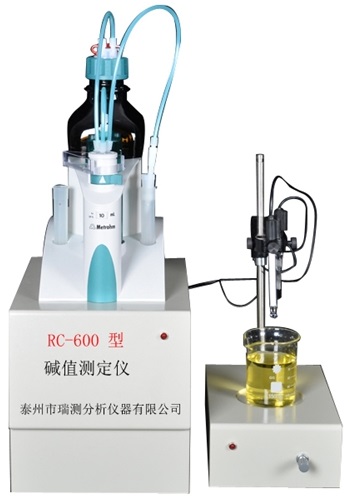
12.4 评定标准(报警指标/换油指标)
柴油机油,下降率超过50%;GBT7607-2010《 柴油机油换油指标 》。
汽油机油 ,<0.5mg/g; GB/T 8028-2010《 汽油机油换油指标 》 。
12.5 变化的原因
- 内燃机油清净分散剂的数量减少。
12.6 采取措施
- 考虑换油。
13.7 相关知识点
润滑油中碱性组分主要有:有机碱、无机碱、氨基化合物和碱性添加剂等。内燃机油的清净分散剂是碱性的,所以碱值主要用于间接检测内燃机油清净分散剂的数量。
十四、倾点(Pour Point)/凝点(Solidification Point)
14.1 基本概念
倾点:润滑油在规定的试验条件下冷却,每间隔3℃检查一次试样的流动性,直至试样能够流动的最低温度即为倾点。
凝点:润滑油在规定的试验条件下冷却,将样品试管倾斜45°,经1min后试样液面不移动的最高温度即为凝点。
凝点和倾点都是表示油品的低温流动性,无原则性差别,只是测定方法有所不同。一般情况下倾点高于凝点2~3℃。过去前苏联和我国多用凝点指标,西方国家多用倾点。现在都逐步改用倾点来表示润滑油的低温性能。
14.2 监测的意义
- 润滑油的凝点和倾点是润滑油低温性能的重要质量指标。倾点或凝点高的润滑油不能在低温下使用,否则将堵塞油路,不能正常润滑。
- 对于发动机来讲,使用倾点或凝点高的润滑油将造成起动困难。尤其是在寒冷地区,应选择较低倾点或凝点的润滑油。
- 对于低温环境下使用的机械设备,在选用润滑油时,一般选用倾点或凝点比使用环境温度低10~20℃的润滑油。
14.3 分析方法
14.3.1 倾点的测定方法:
GB/T 3535修改采用ISO 3016《石油产品倾点测定法》,进口品牌润滑油采用更多采用ASTM D97《石油产品倾点测定法》 。
方法概要:试样经预加热后,在规定的速率下冷却,每隔3℃检查一次试样的流动性。记录观察到试样能够流动的最低温度作为倾点。
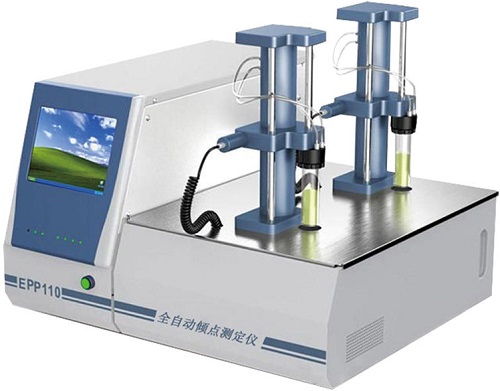
14.3.2 凝点的测定方法
润滑油倾点测定按GB/T 510《石油产品凝点测定法》进行。测定样品凝点时,将试样装在规定的试管中。在冷却到接近预计温度时,将试管倾斜45°,经过1min后,观察液面是否移动。记录试管内液面不流动时的最高温度作为凝点。
14.4 评定标准(报警指标/换油指标)
无。选择润滑油时考虑其低温适用性。
14.5 变化的原因
- 基本无变化。
14.6 采取措施
- 无。
14.7 相关知识点
油品的凝点与蜡含量有直接关系,油品中的蜡含量越多,凝点越高。因此凝点在石油产品加工工艺中可以指导脱蜡工艺操作。它往往是鉴别多级机油的重要参数,也是鉴别伪劣产品的重要指标。
十五、抗磨性(Anti-wear Properties)/极压性(Extreme Pressure Properties)
15.1、基本概念
润滑油的抗磨性和极压性是衡量润滑油润滑性能的重要指标。抗磨性是指润滑油在轻负荷和中等负荷条件下,能在摩擦副表面形成润滑油薄膜以抵抗摩擦副表面磨损的能力。极压性是指润滑油在低速高负荷或者高速冲击负荷条件下,抵抗摩擦副表面发生烧结、擦伤的能力。
15.2 监测的意义
润滑油在使用过程中时常会因极压抗磨添加剂损耗降低润滑油的抗磨性能,导致设备润滑部件的异常磨损。在开展设备润滑磨损状态监测过程中,有必要对新油和在用油的极压抗磨性能进行不定期的抽查,以确保润滑油品的极压抗磨性满足设备需求。
15.3 分析方法
润滑油抗磨损性能的测定方法很多,“四球法”应用最为广泛。
- 润滑剂极压性能测定法 四球法:GB/T 12583等效采用ASTM D2783;
- 润滑剂承载能力的测定 四球法:GB/T 3142;GB/T 3142与GB/T 12583《四球法 润滑剂承载能力测定法对比 论文》;
- 润滑油承载能力的评定法 FZG目测法:SH/T 0306修改采用ASTM D5182,主要应用于齿轮和变速箱用油评定,汽轮机油也常用;
- 润滑油抗磨损性能的测定 四球法:SH/T 0189修改采用ASTM D4172;
- 润滑剂摩擦系数测定法 四球法:SH/T 0762修改采用ASTM D5183。
GB/T 12583方法概要:四球机的一个顶球,在施加负荷的条件下对着油盒内的三个静止球旋转。油盒内的试样投设三个试验钢球。主轴转速为1760r/min±40 r/min,试样温度为18~35℃。按本标准的规定逐级加负荷,做一系列的10s试验直至发生烧结。
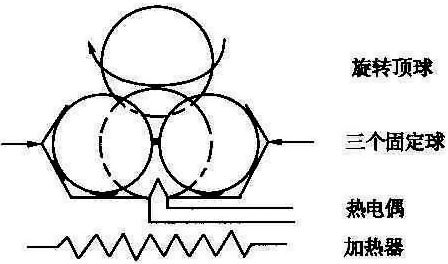
四球磨损试验机示意图
下面是“四球法”测定润滑油抗磨性和极压性的主要检测指标。
- 最大无卡咬负荷PB值,即在试验条件下钢球不发生卡咬的最高负荷。它表征油膜强度。
- 烧结负荷PD值,即在试验条件下使钢球发生烧结的最低负荷。它表征润滑油的极限工作能力。
- 综合磨损值ZMZ,是润滑油在所加负荷下使磨损减少到最小的抗极压能力的一个指数,它等于若干次校正负荷的算术平均值。
- 磨斑直径D,是指润滑油在负荷为392N,时间为60min的长磨条件下,钢球表面的磨损斑痕的直径,用来评价润滑油的抗磨能力。
15.4 评定标准(报警指标/换油指标)
用于评定新油的极压抗磨等级。
15.5 变化的原因
- 极压抗磨添加剂消耗。
15.6 采取措施
- 加换油。
15.7 相关知识点
根据摩擦副的接触应力选择低、中、高极压性能的润滑油。接触面的应力计算和润滑油的极压性能选择可参考JB/T 8831《工业闭式齿轮的润滑油选用方法》或ANSI/AGMA 9005-E02《工业齿轮润滑》。
现代设备负荷的增高和工作环境的恶劣,使许多设备特别是那些低速重载的摩擦副表面间难以形成完整连续的抗磨润滑油膜。在这种条件下,全凭润滑油中的极压抗磨添加剂与金属起化学反应、在摩擦副表面生成剪切应力和熔点都比原金属要低的极压固体润滑膜来防止摩擦副表面烧结磨损。例如重负荷的工业齿轮油、车辆齿轮油等对极压抗磨性能都要有较高的要求。若极压性能不好,则在高负荷、冲击负荷的作用下,润滑油很难起到良好的抗磨作用,加速摩擦副的异常磨损。因此,对有极压性能要求的润滑油必须进行极压性能检测。四球法的PD值检测是评价润滑油极压性能最简单且最实用的方法之一。
十六、光谱分析
16.1 基本概念
光谱分析分为红外光谱和元素光谱。红外光谱主要用于分析添加剂消耗、污染物累积、油品的降解、水污染等趋势监测。元素光谱主要用于监测添加剂元素、磨损金属和污染物的含量;元素光谱原子发射光谱法和原子吸收光谱法。
16.2 监测的意义
润滑油在使用过程中基础油氧化降解、添加剂消耗、污染物混入以及设备磨损都需要及时进行监测,通过监测这些物质的含量的变化趋势可分析判断设备的运行状态。
16.3 分析方法
16.3.1 原子发射光谱法:
SH/T 0853修改采用ASTM E2412《在用润滑油状态监测法 傅里叶变换红外(FT-IR)光谱趋势分析法》。方法概要:
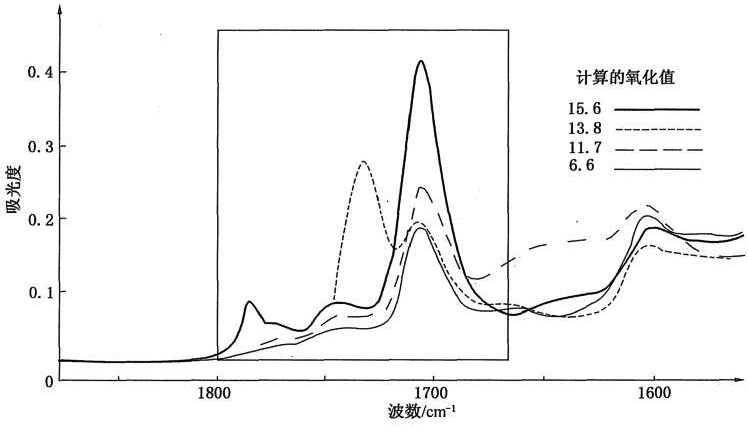
红外光谱分析新油配方中含有羧基组分
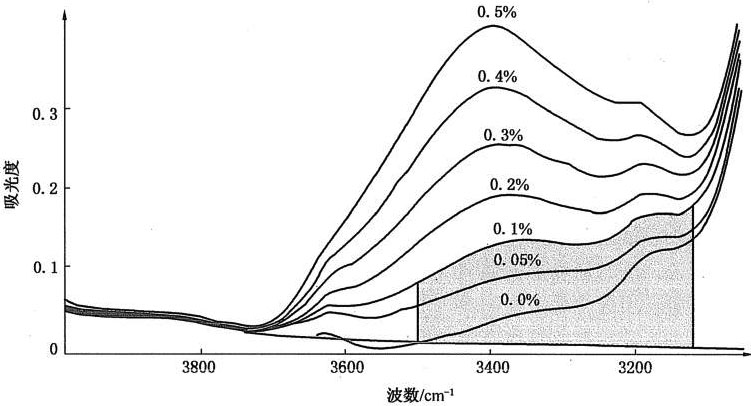
红外光谱 水含量
16.3.2 原子发射光谱法:
GB/T 17476等效采用ASTM D5185《用感应耦合等离子体原子发射光谱法(ICP-AES)测定使用过的润滑油中的添加元素、磨损金属和污染物以及基础油中选定元素》。本标准可测定使用过的润滑油中各种添加剂元素、磨损金属和污染物的含量。它也能测定基础油或再生基础油中多种金属含量的变化。所测定的元素包括:铝 、硼 、钡、钙、铬、铜、铁、铅、镁、锰、铝 、镍、磷、钾、钠 、硅、锡、银、硫、钛、钒和锌共 22种元素。
方法概要: 油样可不经过消解直接稀释后测定。将待测油样或经稀释后的油样放置在光谱仪的高压火花里激发“燃烧”,使油样中的各元素原子被激发为高能态。核外电子从不稳定的高能轨道跃迁回原轨道,同时释放出具有特征波长的光子,形成发射光束。发射光束由光栅按其波长分开,通过光电倍增管或固体检测器将各光谱的光信号转化为电信号而被测定。各特征波长发射光的强度大小与油样中相应元素的含量成正比。
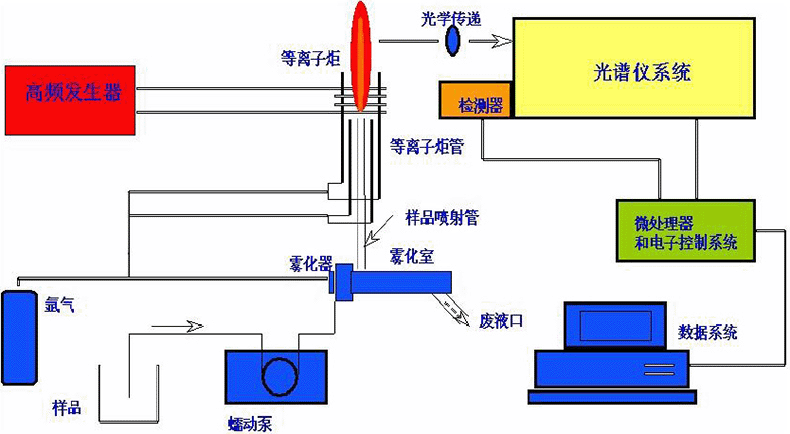
16.3.3 原子吸收光谱法:
方法有SH/T 0228《润滑油中钡、钙、锌含量测定法(原子吸收光谱法)》,SH/T 0061《润滑油中镁含量测定法(原子吸收光谱法)》等。
方法概要:油样首先进行预处理,配制成待测样品。将样品吸入火焰并汽化转变成气态自由原子状态,同时将具有与被分析元素相同特征波长的光束射入火焰。所测元素的自由原子吸收射入的特征波长的光能而产生吸收信号,吸收光能量的大小与被测油样中该元素的含量成正比。
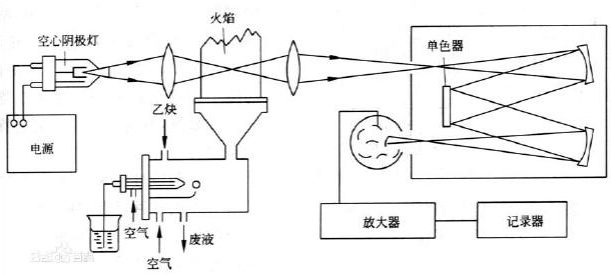
16.4 评定标准(报警指标/换油指标)
原子发射光谱:金属磨损量<10-20ppm。添加剂元素:±25%;
16.5 变化的原因
- 磨损
- 污染
16.6 采取措施
- 进行磨屑分析。
16.7 相关知识点
方法对比:
原子发射光谱法:该方法的特点是检测速度快、测定元素范围广、操作简便,故被广泛用于油液监测领域,但测量精度比原子吸收光谱要低。
原子吸收光谱法:润滑油添加剂元素原子吸收光谱分析法的主要特点是精度高,测定元素范围广。但该方法的检测速度较慢,难以满足油液监测快速、大量的要求,所以应用面不广。
十七、铜片腐蚀(Copper Corrosion)
17.1 基本概念
润滑油中活性硫化物、低分子有机酸、无机酸、碱对金属的腐蚀作用。
17.2 监测的意义
润滑油对机械零部件的腐蚀,主要是油中活性硫化物、有机酸、无机酸等腐蚀性物质引起的。这些腐蚀性物质一方面是基础油和添加剂生产过程中残留下来的,另一方面则是油品在使用过程中的氧化产物。为了保证油品对机械设备不产生腐蚀,腐蚀试验几乎是评定新油质量的必检项目。
17.3 分析方法
GB/T 5096《石油产品铜片腐蚀试验法》与ASTM D130《石油产品铜片腐蚀试验法》方法相同。
方法概要:将一块已磨光好的铜片浸没在一定体积的试样中,根据试样的产品类别加热到规定的温度,并保持一定的时间。加热周期结束时,取出铜片,经洗涤后,将其与铜片腐蚀标准色板进行比较,评价铜片变色情况,确定腐蚀级别。
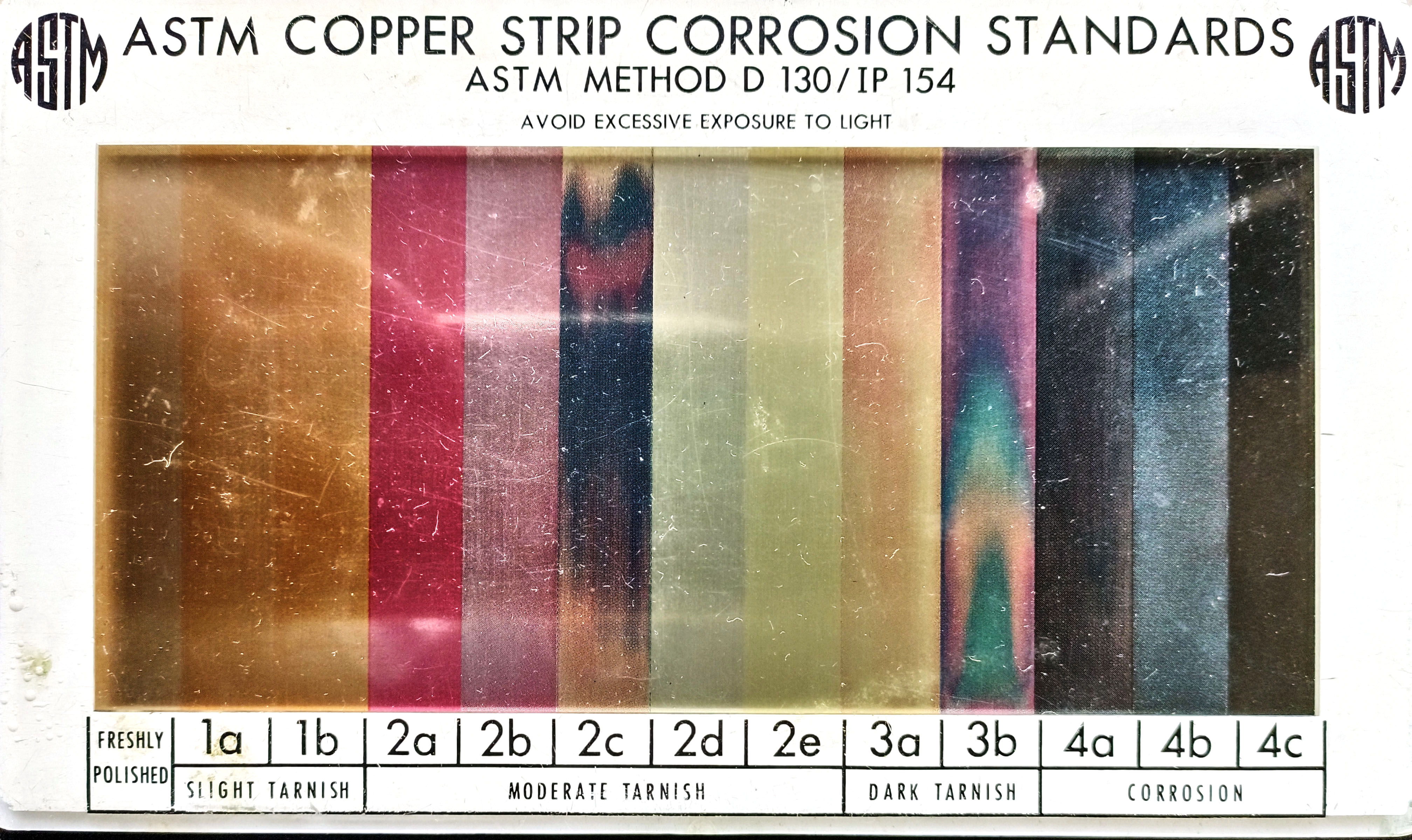
ASTM D130铜片腐蚀比色卡
腐蚀标准色板分级,分为四度12级:1无腐蚀;2为中度,2c开始认为有轻度腐蚀,新油不允许;3为深度,3a已认为有腐蚀;4为重度腐蚀,4a已是严重腐蚀。
17.4 评定标准(报警指标/换油指标)
不同润滑油对铜片腐蚀的接受程度差别很大,例如:汽轮机油2a,齿轮油3b。
17.5 变化的原因
- 添加剂消耗。
- 污染。
- 系统维护不正常(如疏于排水、排水设备故障等)。
17.6 采取措施
- 调查原因,进行必要的维护和操作更改。
- 加换油、排气、脱水。
- 重新检查锈蚀试验,如果试验结果没有变化,请与油供应商协商可能的补救措施。
17.7 相关知识点
原油中含有硫化物,大部分硫化物在提炼过程中被除去。然而,在石油产品中残留的硫化合物中,有些可能对各种金属有腐蚀作用,这种腐蚀性与总硫含量不一定直接相关。油品制备时残留的无机酸和碱,对金属的腐蚀作用。
十八、颗粒污染度(particulate contamination level)
18.1 基本概念
颗粒污染度,也叫清洁度或颗粒度,是指通过检测油液中污染粒子的分布、大小尺寸及数量来评价油品的清洁程度。 颗粒污染度标准分为颗粒度测定方法、测定标准、分级标准。
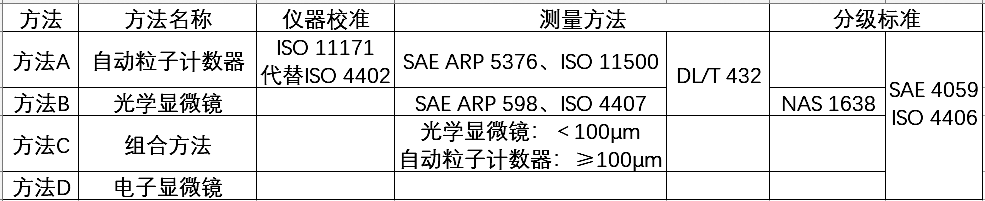
参考 SAE 4059F
测定方法有自动颗粒计数法和显微镜测定法;测定标准有:DL/T 432(自动颗粒计数法和显微镜测定法)、ISO-11500(自动颗粒计数法)、 ISO 4407(显微镜测定法)等;分级方法有NAS 1638(显微镜测定法和称重法)、SAE 4059F(自动颗粒计数法和显微镜测定法) 、ISO 4406、GB/T 14039等。
18.2 监测的意义
润滑油在实际应用中的污染是不可避免的,对液压介质进行污染控制的目的是为了最大限度地保持液压介质的清洁,从而延长设备和润滑油的使用周期。
18.3 分析方法
根据仪器测试的原理不同,可以分为两类:自动颗粒计数法和显微镜对比法。
18.3.1 自动颗粒计数仪法
依据遮光原理来测定油的颗粒污染度。当油样通过传感器时,油中颗粒会产生遮光,不同尺寸颗粒产生的遮光不同,转换器将所产生的遮光信号转换为电脉冲信号,再划分到标准设置好的颗粒度尺寸范围内并计数。
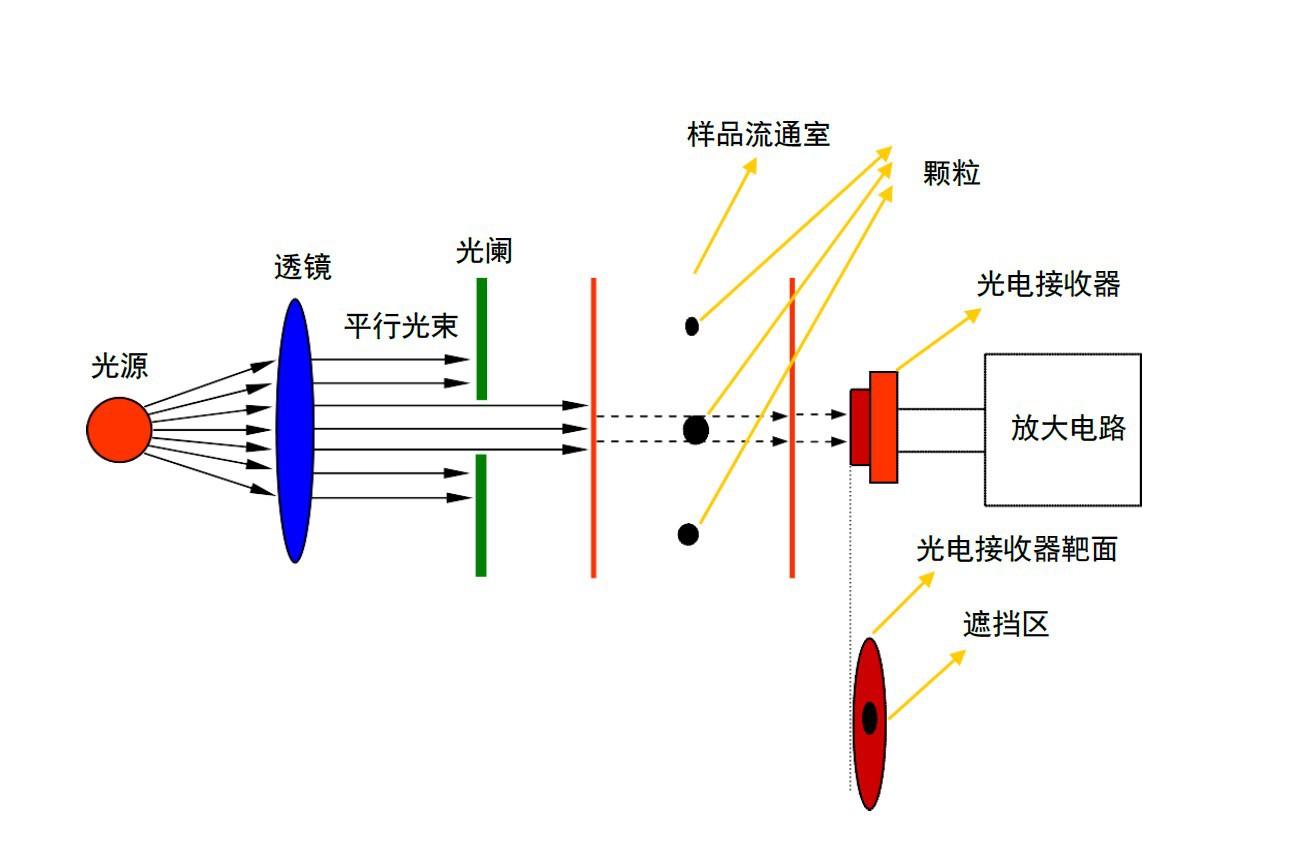
使用自动颗粒计数器计数所报告的污染等级代号由三个代码组成,该代码分别代表如下的颗粒尺寸及其分布:
- 第一个代码代表每毫升油液中颗粒尺寸≥4μm(c)的颗粒数;
- 第二个代码代表每毫升油液中颗粒尺寸≥6μm(c)的颗粒数;
- 第三个代码代表每毫升油液中颗粒尺寸≥14μm(c)的颗粒数;
18.3.2 显微镜对比法
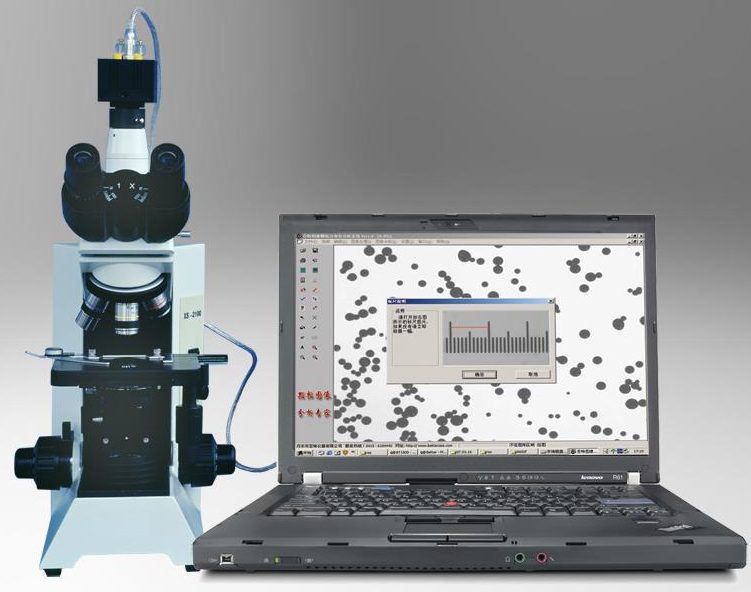
显微镜对比法油液污染等级用>5μm和>15μm两个尺寸范围的颗粒浓度代码表示。相当于自动颗粒计数器计数的6 μm和>14μm。
18.3.3 颗粒物数量、代码的换算
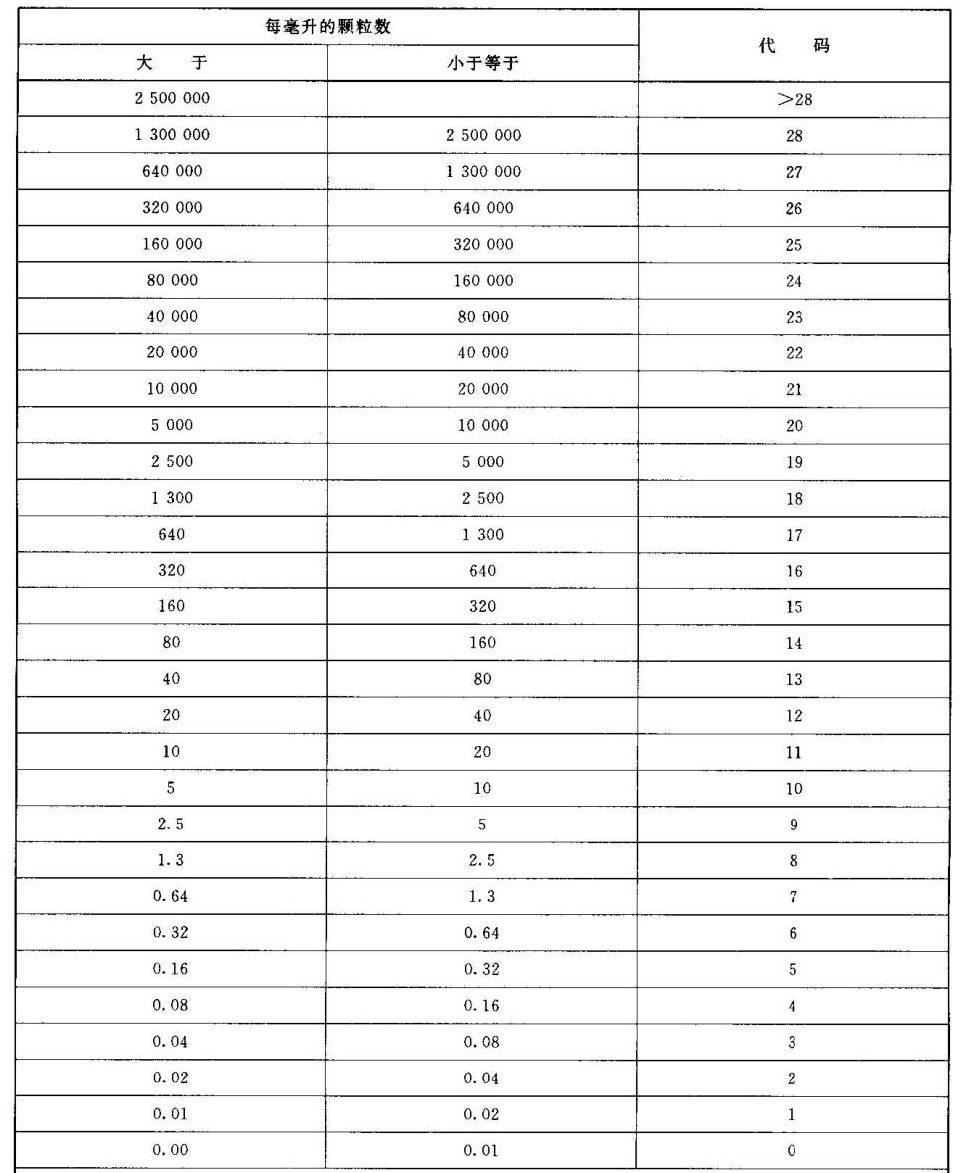
颗粒物数量、代码的换算
ISO和SAE标准是按照100ml计量的,上述颗粒数*100,等级不变。
18.3.4 ISO等级、NAS等级的换算
两种清洁度标准不能直接比较或转换,因为两种体系的基本原则相差很大。ISO 4406是 ≥4μm、≥6μm 、≥14μm或>5μm、>15μm;NAS 1638 是分段计数的,5~15μm、15~25μ m、25~50μ m 、50~100μ m 、>100μ m 。SAE 4059包括了这两个标准。但是根据经验和设备运行使用情况,可做如下简单换算。
- 21/17/14可以换算为NAS 8级,理由是:工程实际应用表明,对摩擦副影响最大的是6-14μm的颗粒;小于6μm颗粒进入摩擦副影响不大;大于14μm颗粒不能进入摩擦副,所以影响也不大。为方便记忆,直接用中间一个数字减9即可,即:17-9=8。
- -/17/14 前面的“-”表示4μm的不用考虑;
- */17/14 前面的“*”表示4μm的太多,无法计量。
18.4 评定标准(报警指标/换油指标)
API 614等使用标准一般要求“19/17/14 ”或更好“18/16/13“ 或OEM。新产品往往不能达到 “19/17/14 ” ,而需要在使用1-2周后才能达到该标准。
18.5 变化的原因
- 新建/检修系统时,未彻底清理干净:油箱、泵、管路、驱动机构/润滑部件,举例:PSA管路现场焊接;
- 系统使用过程中产生的:运动部件磨损、润滑油讲解;
- 外界污染:加油过程、尘杂环境。举例:磨煤机。
18.6 采取措施
- 定位和消除微粒来源。
- 检查油中是否含有不溶性和磨损金属。
- 通过过滤或离心或两者一起清洗系统油。
18.7、相关知识点
NAS1638是分段计数的,有5个尺寸段。由于实际油液各尺寸段的污染程度不可能相同,因此被测油样的污染度按其中的最高等级来定。这会引起一个问题。例如,测出的5~15μm的污染度可能是4级,15~25μm颗粒的污染度可能是6级,25~50μm可能是5级,而50~100μm颗粒的污染度可能是8级,这时数据就很难处理,往往使得概念不清。如果保守的话,就会按照规定判定为8级,认为系统很脏。而事实上,新的磨损理论表明只有尺寸与部件运动间隙相当的颗粒才会引起严重的磨损,也就是说5~15μm的颗粒危害最大,而50~100μm由于无法进入运动间隙,对磨损的影响却不大。
- 润滑油系统中的污染物从何而来?
- 润滑油中的固体颗粒会对运动表面有何影响。
十九、剩余使用寿命(RULER)
19.1 基本概念
通过测量润滑油中抗氧化剂的剩余浓度来定量地测定润滑油的剩余使用寿命。
19.2 监测的意义
润滑油中的抗氧剂会随之使用时间延长逐渐消耗,首先消耗的是酚类抗氧剂(先导型抗氧剂),而后消耗的是胺类抗氧剂(分解润滑油被氧化形成的产物)。通过监测这两类抗氧剂的含量来表征润滑油的剩余寿命。低端润滑油只有酚 类抗氧剂。
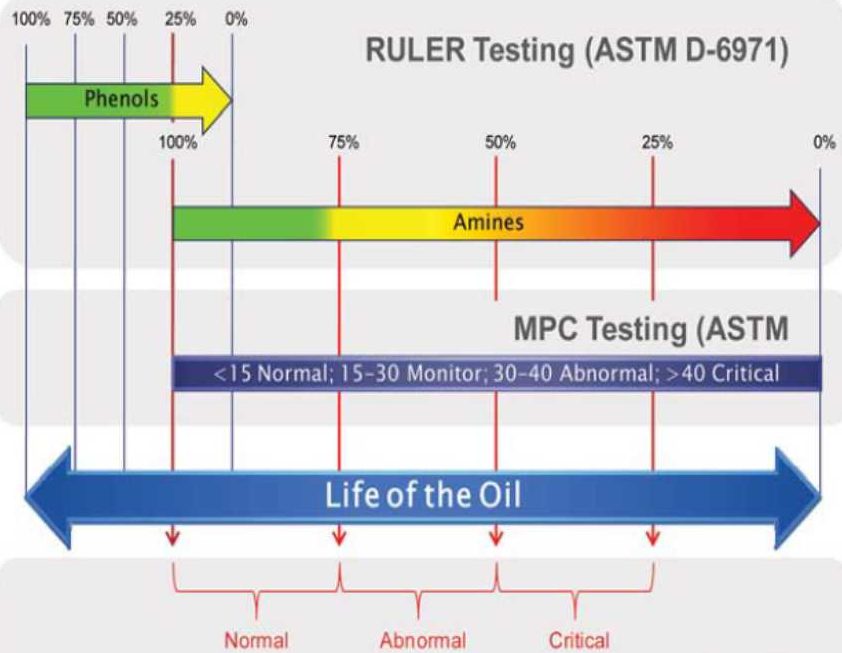
酚类 胺类抗氧剂消耗顺序 润滑油寿命
19.3 分析方法
RULER的检测基于线性伏安法。原理是在特定的电压值下,溶液中抗氧化剂的化学活性被激活,形成氧化电流,并得出一条氧化电流对时间的曲线,即报告中”剩余抗氧化剂含量图” 上的曲线,简称”RULER曲线”。随后通过软件将新油与旧油的RULER曲线进行峰面积相比,算出旧油中剩余抗氧化剂含量。润滑油中抗氧化剂种类主要分为胺类和酚类。通常情况下,在8~12s产生胺类的吸收峰;13~16s产生酚类的吸收峰,如下图所示。
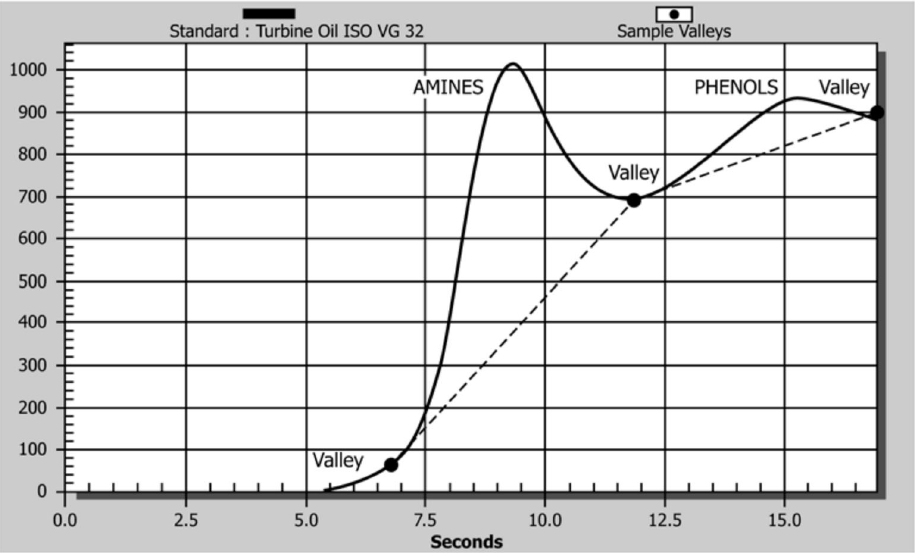
横坐标代表检测时间,单位”s”;纵坐标代表电流的反馈。
润滑油剩余使用寿命测定的方法:
- ASTM D7590在用润滑油主要的抗氧化剂含量测定 线性扫描伏安法;
- ASTM D6971无锌透平油中受阻酚和芳香胺抗氧化剂含量测定 线性扫描伏安法;
- ASTM D6810-13无锌透平油中受阻酚抗氧化剂含量的标准试验方法 用线性扫描伏安法;
- ASTM D7527-10润滑脂中抗氧化剂含量的标准试验方法 线性扫描伏安法。
方法概要:汽轮机油抗氧化剂含量(RULER)的测定方法为ASTM D6971,结果报告为抗氧化剂胺类、酚类的百分含量。具体检测步骤如下:
- 新油RULER图(下图细线):取一定量待测油样的新油置于RULER专用测试试剂中,摇匀、静置后检测,得RULER曲线A;
- 在用油RULER图(下图粗线):取与新油相同含量的在用油于RULER专用测试试剂中,摇匀、静置后检测,得RULER曲线B;
- 解图:将A、B曲线数据导入电脑进行解析。
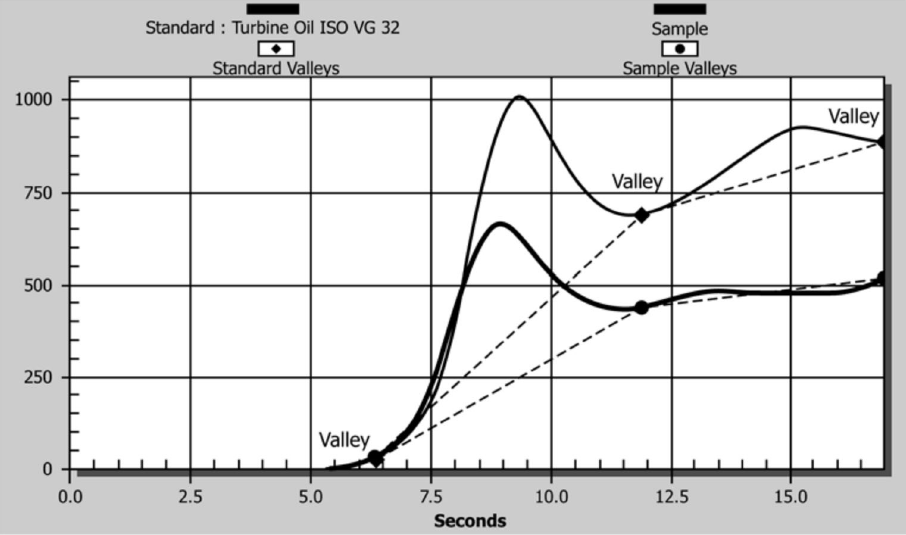
19.4 评定标准(报警指标/换油指标)
酚类或胺类抗氧剂>25%。
19.5 变化的原因
- 消耗
19.6 采取措施
- 加换油
- 咨询油品供应商补充添加剂。
- 监测漆膜和污染物。
19.7 相关知识点
润滑油中抗氧化剂种类主要分为胺类和酚类。酚类抗氧化剂易挥发,先降解;胺类抗氧化剂耐高温,后降解,但易形成漆膜。
十二、漆膜倾向性(MPC)
20.1 基本概念
用膜片比色法测定在用涡轮机油中不溶的有色物质,用不溶物的含量表示润滑油生成漆膜(Varnish)倾向性程度, 简称MPC,漆膜倾向性指数。
20.2 监测的意义
该测试可作为润滑油生成不溶物的趋势监测,作为润滑油状态监测的一部分,应用在ASTM D4378《在用蒸汽、燃气和联合循环涡轮机的汽轮机矿物油监测的标准操作规程》。
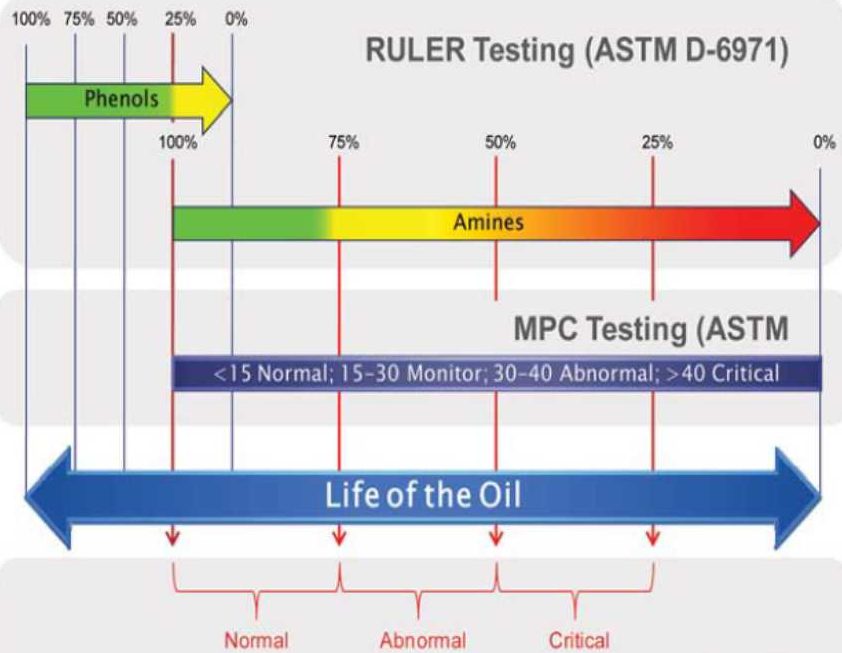
20.3 分析方法
GB/T 34580-2017《用膜片比色法测定在用涡轮机油中不溶有色物质的方法》 ,它参照采用ASTM D7843-12,最新版为 ASTM D7843-21 。
方法概要:用直径为17 mm、孔径为0.45 um硝基纤维素材料的微孔滤膜将不溶物从运行涡轮机油中分离出来,并用色差仪来测量该膜的颜色,结果用CTELAB色度中的∆E来表示。
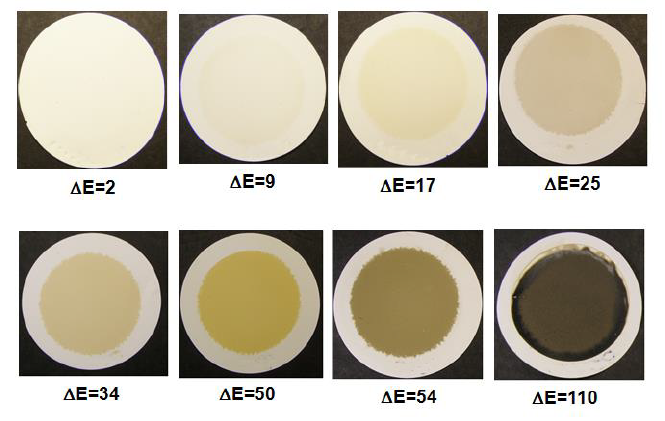
20.4 评定标准(报警指标/换油指标)
- ∆E <15:正常;
- ∆E 15~30:监控;
- ∆E 30~40:不正常;
- ∆E >40:严重。
20.5 变化的原因
- 润滑油被氧化。
20.6 采取措施
- 颗粒污染物;
- 监测氧化性能;
- 采取措施去除漆膜;
- 更换油品。
20.7 相关知识点
对机组润滑油进行状态监测时,一定要结合颗粒污染物、漆膜倾向性指数、氧化性能(例如旋转旋转氧弹)等指标进行综合分析和判断,同时关注轴瓦温度变化情况。
二十一、残炭(Carbon Residue)
21.1 基本概念
油品的残炭值,是指油品在特定的高温条件下,经过蒸发及热裂解过程后,所形成的炭质残余物占油品的质量百分数。主要用于内燃机油:柴油机油、汽油机油的测定。
21.2 监测的意义
残炭值的大小与油品的化学组成及灰分含量有关。除灰分外,油品中的胶质、沥青质及多环芳烃等物质是残炭的主要来源。故通常情况下,残炭值可用来表征油品的相对生焦倾向的大小(含有生灰添加剂的油品除外),用于指导原料的选择及油品的生产工艺。
21.3 分析方法
目前我国正在使用的残炭测定方法共有4种:康氏法(GB268):微量法(GB/T17144)、电炉法(SH/T170)和兰氏法(SH/T160)。康氏法是世界各国普遍采用的一种标准方法;微量法是近些年国内外普遍采用的一种简便而高效的残炭测定方法,我国于1997年正式列为国家标准方法;电炉法源于原苏联,使用的国家很少;兰氏法因其残炭数据与康氏残炭间只存在近似关系,故较少被采用。鉴于不同残炭测定方法的工作原理、实验装置、操作条件等因素均存在一定差别,利用不同方法得到的测定结果间的相关性如何一直是油品分析工作者关心的问题。
康氏法有: GB268、ISO 6615、ASTM D189,三个方法是一致的。把已称重的试样置于坩埚内进行分解蒸馏。残余物经强烈加热一定时间即进行裂化和焦化反应。在规定的加热时间结束后,将盛有碳质残余物的埚置于干燥器内冷却并称重,计算残炭值(以原试样的质量百分数表示)。
21.4 相关知识点
康氏法广泛应用于多种石油产品。本方法和ZBE 30001《石油产品残炭测定法(兰氏法) 》这两种方法所测得的残炭值,不但在数值上不相同,而且它们之间也找不到满意的相互关系。对于一些不容易装入兰氏焦化球的重质残渣燃料油、焦化原料等油料,宜用本方法测定残炭燃烧器燃料的残炭值,可用来粗略地估计燃料在蒸发式的釜型和套管型燃烧器中形成沉积物的倾向。同样,不含硝酸戊酯(或如果含有硝酸戊酯,则只要事先测定未加此添加剂基础燃料)的柴油,残炭值大体上与燃烧室的沉积物有对应关系。
二十二、LNF磨粒分析
22.1、基本概念
使用CCD成像技术和先进的图像处理程序,通过测量润滑油中颗粒尺寸分布、增长趋势和磨粒形状来识别颗粒形貌、生产率和机械故障的严重程度。
22.2 监测的意义
相当于颗粒物分析和铁谱分析 ,参考颗粒污染物和铁谱分析的意义。
22.3 分析方法
ASTM D7596《LNF磨粒分析 润滑油自动颗粒计数和颗粒形状分类的标准》方法概述:将样品置于LNF磨粒分析仪的转盘中,样品通过检测器上的导管进入成像仪内自动进行颗粒计数和形貌分析,仪器原理如下图:
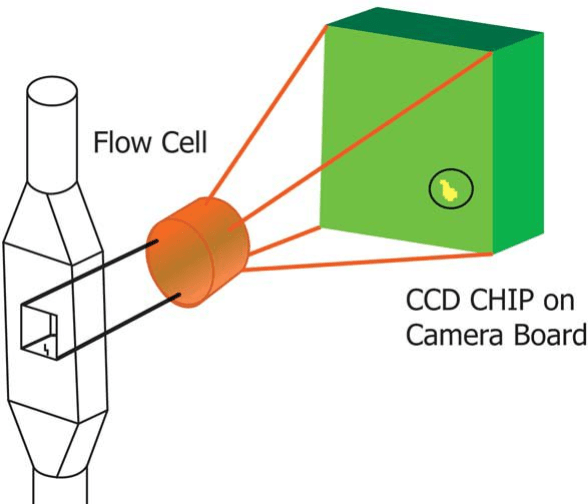
22.4 相关知识点
通过LNF磨粒分析能同时了解到油品的NAS,ISO清洁度以及五种磨损颗粒(切削磨损颗粒、疲劳磨损颗粒、滑动磨损颗粒、非金属颗粒、其他颗粒)的大小数量等信息,从而系统地掌握润滑系统中的磨损颗粒和污染物的情况,对判断设备是否运行正常或者是否需要预先性维护具有重要的意义。
二十三、蒸发损失(Evaporation Loss)和挥发性(Volatility)
23.1 基本概念
蒸发损失:在有恒定气流抽出的条件下,润滑油试样在坩埚内加热所产生的挥发性油蒸气的质量损失。
挥发性:液体形成蒸气的趋势。
23.2 监测的意义
润滑油的挥发性与油耗、粘度稳定性、氧化安定性有关,这些性质对多级油和节能油尤其重要。蒸发损失与润滑油的挥发度成正比,蒸发损失越大,实际应用中的油损耗就越大。液压油在使用中蒸发,还会产生气穴现象和效率下降,可能给液压泵造成损害。
23.3 分析方法
润滑油蒸发损失的测试方法有GB/T7325-1987《润滑脂和润滑油蒸发损失测定法》和SH/T0059-2010 《润滑油蒸发损失测定法 诺亚克》。
GB/T 7325方法是把放在蒸发器中的润滑油试样置于规定温度的恒温浴中,热空气通过试样表面22h,然后根据试样的质量损失计算蒸发损失,可以测定在99-150℃范围内的任一温度下润滑油的蒸发损失。该方法主要用于合成润滑油和润滑脂的蒸发损失评定。
SH/T 0059-2010方法参照ASTM D5800-08标准编写并进行了修订。SH/T 0059方法是试样在规定的仪器中,在规定的温度和压力下加热1h,蒸发出的油蒸气由空气流携带出去。根据加热前后试样量之差来测定润滑油的蒸发损失。
国外主要测试方法有ASTM D972,DIN 51581和JISK2220 (5.6) 等。
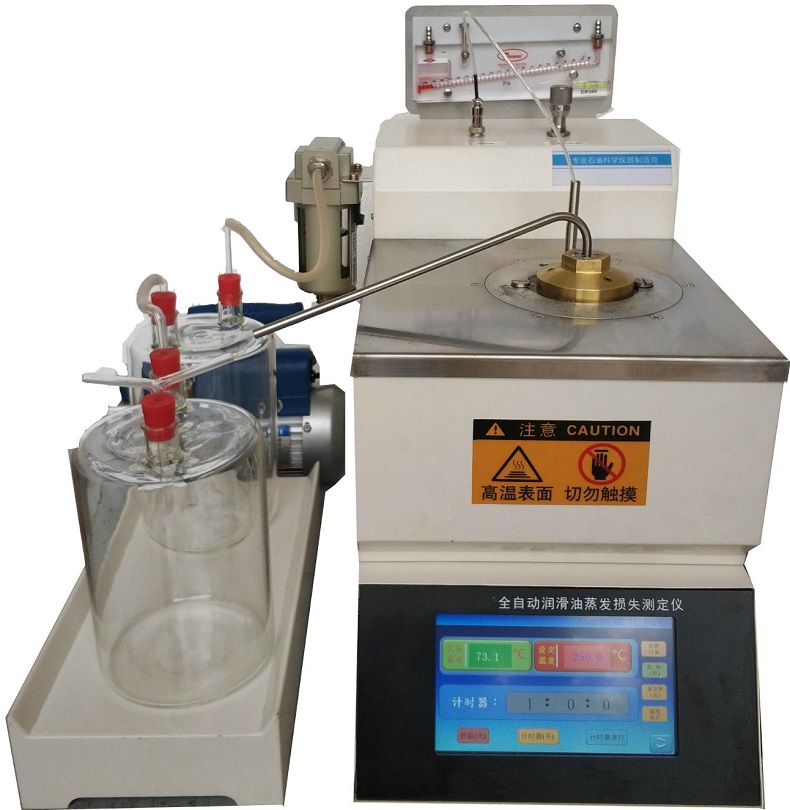
23.4 评定标准(报警指标/换油指标)
部分合成航空润滑油要求蒸发损失损失小于一定值。
23.5 变化的原因
- 用于新油性能的测定。
23.6 采取措施
- 无。
23.7 相关知识点
部分机组使用粘度较小的润滑油,造成现场油雾多、卫生差,部分油箱甚至设置了专用的排油烟风机和收集器。
二十四、相容性(Compatibility)
24.1 基本概念
润滑油相容性实验分为:润滑油与润滑油的相容性实验,润滑油与橡胶的相容性(密封性)实验。
24.2 监测的意义
润滑油在线置换过程中,确保两种油品不发生异常反应,生成过多的沉淀物,导致油品性能降低。润滑油使橡胶密封件溶胀、 收缩、硬化、龟裂,质量增加或减少 ,导致密封失效。
24.3 分析方法
24.3.1 两润滑油相容性实验
润滑油之间的相容性实验是测试两种润滑油混兑后再一定条件下是否产生沉淀以及理化性能是否改变,主要用在润滑油(在线)替换前进行,ASTM D7155《涡轮机油混兑相容性实验》。方法概要:两种油液分别以90:10、50:50、10:90、比例,充分搅拌混合后在65摄氏度的烤箱中储存23-25 小时,在外线照射,然后进行评估,混合液的任何一项指标应介于两种油液之间或优于性能更优者认为合格,否则认为该项测试不合格。
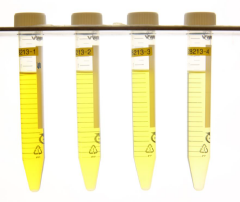
24.3.2 润滑油与橡胶件相容性实验
实验标准有SHT0877、SH/T0429、GJB1820。
方法概要:橡胶在润滑油中浸泡一定时间后,可能发生溶胀、收缩、硬化、龟裂,质量增加或减少,硬度也可能变大或变小,其他力学性能如抗张强度也可能变化。若润滑油与橡胶相容性好,则上述变化较小,否则上述变化较大。
24.4 评定标准(报警指标/换油指标)
两润滑油混合后的指标不低于较差的一种润滑油的指标。
24.5 变化的原因
- 两种润滑油的添加剂发生反应。
- 润滑油与橡胶发生反应。
24.6 采取措施
- 无。
24.7 相关知识点
在液压系统中以各种类型的橡胶作为密封件者很多,在机械中的油品不可避免地要与一些密封件接触。橡胶相容性不好的润滑油可使橡胶溶胀、收缩、硬化、龟裂,影响其密封性,因此要求润滑油与橡胶有较好的适应性。液压油标准中要求橡胶密封性指数,它是以橡胶圈浸在油中一定时间的变化来衡量的。
二十五、剪切安定性(Shear Stability)
25.1 基本概念
剪切安定性是指油品抵抗剪切作用,保持粘度以及和粘度有关的性质不变的能力。
25.2 监测的意义
润滑油中的粘度指数改进剂是链状高分子聚合物,工作时在零件摩擦表面不断受到剪切,使分子扭变、断裂,造成润滑油相应温度下的粘度下降,粘温性变差。所以多级油(内燃机油)规格项目中对剪切安定性提出了要求。
25.3 分析方法
测定剪切安定性的方法很多,有超声波剪切法SH/T 0505-2017《含聚合物油剪切安定性的测定 超声波剪切法》、喷嘴剪切法SH/T 0103-2007 《含聚合物油剪切安定性的测定柴油喷嘴法》、SH/T 0845-2010《传动润滑剂粘度剪切安定性的测定 圆锥滚子轴承试验机法》、威克斯泵剪切法、FZG齿轮机剪切法,这些方法最终都是测定润滑油品的粘度下降率。
通过测定润滑油在高温高剪切速率条件下的表观粘度测定也可以反映油品的剪切安定性,实验方法为SH/T 0703-2001润滑油在高温高剪切速率条件下表观粘度测定法 多重毛细管粘度计法。
方法概要:在规定温度下,将30ml试样在聚能器(超声波振荡器)中受超声波剪初10min引起的粘度损失,以油的粘度下降率来表示。
25.4 评定标准(报警指标/换油指标)
无。
25.5 变化的原因
- 用于新油性能的测定。
25.6 采取措施
- 无。
25.7 相关知识点
加入增黏剂的润滑油在使用过程中,由于机械剪切的作用,润滑油中的高分子聚合物被剪断,使油品粘度下降,影响正常润滑。
二十六、分析式铁谱法(Analytical Ferrography)
26.1 基本概念
在用润滑油中磨损颗粒在分析式铁谱仪的磁场作用下沉积在基片上,然后在铁谱显微镜下对磨损颗粒的形态、尺寸和覆盖面积进行观察和测量,定性分析机械的磨损状况。用于分析内燃机油、齿轮油、液压油等油品在使用过程中机械零部件产生的磨损颗粒的形态、尺寸大小和浓度变化趋势。
26.2 监测的意义
铁谱的目的是根据在油中观察到的颗粒的数量和类型来诊断被取样机器的工作状态。正常运行的机器显示一致的粒子浓度和粒子类型从样品到样品。颗粒浓度的增加,伴随着颗粒类型的大小和严重程度的增加,预示着磨损的开始。
26.3 分析方法
国内一般采用SH/T 0573-93在用润滑油磨损颗粒试验法 分析式铁谱法 ,国外一般采用ASTM D7690-11(2017)《用分析铁谱法对使用中的润滑剂颗粒进行显微表征测试》。
在用润滑油中的磨损颗粒在分析式铁谱仪的磁场作用下沉积在基片上,然后在铁谱显微镜下对磨损颗粒的形态、尺寸和覆盖面积进行观察和测量,以分析机械的磨损状况。
26.4 评定标准(报警指标/换油指标)
暂无,依靠分析人员的长期积累的经验。根据磨损颗粒的类型和材质,结合摩擦副材质,判断磨损部位及严重程度。
26.5 变化的原因
- 异常磨损。
26.6 采取措施
- 监控磨损的发展趋势,结合状态监测判定机器可运行的时间。
26.7 相关知识点
SH/T 0573-93 在用润滑油磨损颗粒试验法 分析式铁谱法 磨损颗粒定性分析:
- 正常磨损颗粒的特征是薄片状、表面光滑,颗粒细小均匀,长轴尺寸为0.5~15 um,厚度为0.15~1um。在机械磨合阶段,还产生一些长条状、扁平状的颗粒,这种颗粒也属于正常磨损颗粒。
- 切削磨损颗粒的特征是线状、卷曲状、弧状、车屑状、长条状,当硬摩擦面有锐边时,产生较粗大的切削磨损颗粒,长度为25~100 um,宽度为2~5 pm;当两个摩擦面之间存在一个硬的夹杂物时,产生较细小的切削磨损颗粒,长度为5~10 um,厚度约为0.25mm;
- 滚动疲劳磨损颗粒有三种形态:疲劳剥落碎片、球状和层状颗粒。(1)、疲劳剥落碎片长轴尺寸一般大于10 um,最大可达100 um ,形状因子小于5:1,有一个光滑的表面和不规则的周边。(2)、球状颗粒直径一般为1~3um,最大可达10um;(3)、层状颗粒是扁平的薄片、长轴尺寸为20~50 um、形状因子大于30 :1、颗粒表面有一些空洞。
- 严重滑动磨损颗粒的特性是长轴尺寸在20um以上,形状因子大于5:1、小于30 :1、表面有明显的滑动条纹、有时出现高温引起的色彩。
- 有色金属的磨损颗粒特征是颗粒不按磁场方向排列。而以随机方式沉淀,它们大多偏离铁磁性磨损颗粒链或处在相邻两链之间,并往往带有有色金属本身的特征颜色。
- 铁的氧化物中红色氧化物颗粒在白色偏振光下呈红棕色多晶体团状,主要成分是aFe2O3,而黑色氧化物颗粒在白色反射光下呈黑色,表面有蓝色和桔黄色的小斑点,主要成分是不成固定比例的Fe3O4、a Fe3O4 ,和FeO的混和物;
- 摩擦聚合物特征是在双色光下可观察到无定形的胶体中嵌有金属磨损颗粒,金属磨损颗粒呈红色,而胶体呈透明的绿色。
- 腐蚀磨损颗粒的特征是颗粒非常细小,即使在放大倍数为1000的情况下,单个颗粒也不容易区别开来,颗粒在谱片出口区两侧有堆积,并在整个谱片上都能观察到。
- 切削磨损颗粒、疲劳磨损颗粒、严重滑动磨损颗粒、腐蚀磨损颗粒、金属氧化物都属于不正常磨损颗粒,它们的大量出现意味着机械的磨损严重。
- 谱片的加热分析:(1)调节谱片加热器,使温度达到330±10℃。(2)将谱片置于谱片加热器上,加热90s,(3)在铁谱显微镜下观察磨损颗粒表面生成的氧化层的特征回火色,通常在白色反射光下,铸铁磨损颗粒呈草黄色,低合金钢磨损颗粒呈蓝色。
二十七、色度(Color)
27.1 基本概念
用标准比色卡定量表述石油产品(润滑油、加热油、柴油燃料油和石油蜡等)的颜色等级。
27.2 监测的意义
石油产品颜色的测定主要用于生产控制,是一项重要的质量特性,因为颜色很容易被产品的用户观察到。在某些情况下,颜色可以作为材料精制程度的标志。当某一特定产品的颜色范围已知时,超出该范围的变化可能表明可能受到另一产品的污染。
27.3 分析方法
GB 6540等效采用ASTM D1500《石油产品颜色测定法》。 方法概要:将试样注人试样容器中,用一个标准光源从0.5-8.0值排列的颜色玻璃圆片进行比较,以相等的色号作为该试样的色号。如果试样颜色找不到确切匹配的颜色,而落在两个标准颜色之间,则报告两个颜色中较高的一个颜色。
27.4 评定标准(报警指标/换油指标)
GB/T 14541《电厂用矿物涡轮机油维护管理导则》≤5.5;SH/T 0599《液压油换油指标》变化<2。
27.5 变化的原因
- 污染。
- 过度降解。
27.6 采取措施
- 确定原因并纠正,或考虑换油。
27.7 相关知识点
颜色并不总是产品质量的可靠指南,不应该在产品规格中不加区分地使用。
感 谢 !
课程到此结束,欢迎大家并提出宝贵意见。下期课程讲解设备润滑所涉及到的标准规范。
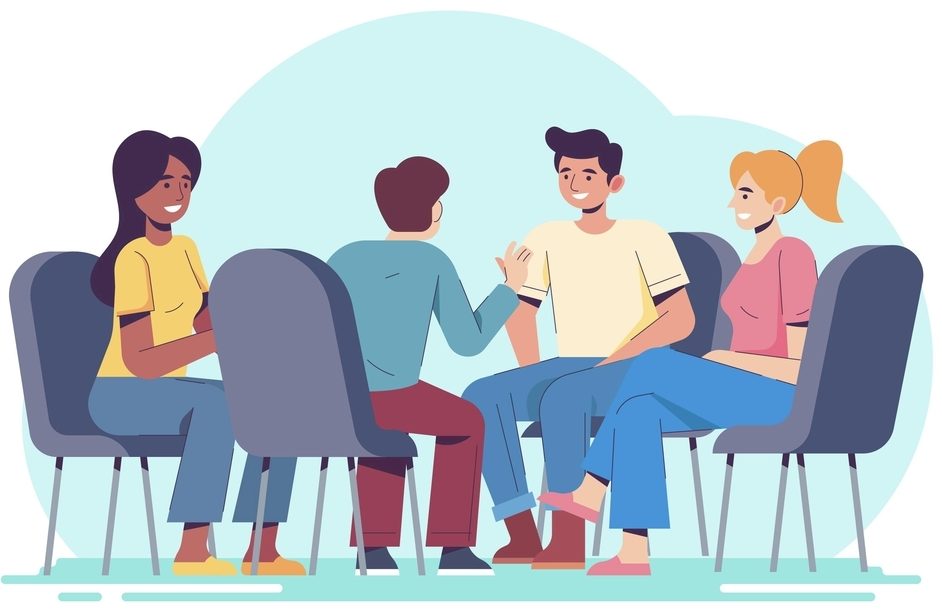