一、标准概述
ASTM D6224-09《Standard Practice for In-Service Monitoring of Lubricating Oil for Auxiliary Power Plant Equipment》,第一版发布于1998年,上一版为2002年。该标准规定了电厂辅助设备在用润滑油的定期监测和质量要求,其它工矿企业润滑油监测可参考执行。
由于未找到该标准对应的国标和相关标准,本网站对其主要内容进行了翻译,不足之处敬请指导。
相关标准有:ASTM D4378《Standard Practice for In-Service Monitoring of Mineral Turbine Oils for Steam, Gas, and Combined Cycle Turbines》,对应国标为:GB/T 14541《电厂用矿物涡轮机油维护管理导则》。
二、范围
用于发电的服务辅助(非涡轮)设备中的矿物油和磷酸酯润滑油。辅助设备包括齿轮、液压系统、柴油发动机、泵、压缩机和电液控制(EHC)系统。
本标准包括取样和测试时间表以及建议的措施,以及关于油如何降解的信息。
常用于发电厂控制系统的磷酸酯类液体外,本标准还适用于矿物类石油产品,不适用于合成类产品。
三、意义和用途
这种做法的目的是帮助用户,特别是电厂的操作人员,保持对他们的矿物润滑油和润滑监测程序的有效控制。这种方法可用于根据油况和测试结果进行换油,而不是根据使用时间或日历时间。它的目的是节省运行和维护费用。
这种做法也旨在帮助用户监视矿物润滑油,防止过量的条件——高级组件磨损,石油降解,或污染,从而减少潜在的灾难性的机器问题,更有可能发生在缺乏这样一个油状态监测计划。
这种做法并不一定要参考当前所有的油品测试技术,也不意味着要排除使用替代仪器或测试方法,以提供有意义或符合趋势的测试数据,或两者兼有。一些油品测试设备和传感器(通常用于筛选油品,根据标准方法进行测试)提供了与水、微粒和其他污染物相关的趋势指标,但并不直接测量这些指标。
本规范适用于矿物类石油产品,而不是合成类产品,但电厂控制系统中常用的磷酸酯类流体除外。
四、技术要求和方法
4.1 润滑油一般特性
一般来说,润滑油的设计目的是减少摩擦和磨损,提供冷却,控制沉积,并消除污染的影响。基础油的润滑性能可以通过选择添加剂来提高。不同的机器有不同的润滑油添加剂要求,其中一些将在本节中介绍。适当的润滑可以缩小或防止金属表面之间的接触,减少部件的磨损。
齿轮油:主要要求是,通过保持运动表面之间的润滑油膜,防止磨损和减少其他形式的损伤,如点蚀和磨损。
液压油:需要传递液压压力和能量,减少泵、阀和气缸的摩擦和磨损,并保护金属表面不受腐蚀。为了获得机器操作和控制的最佳效率,油的粘度应该足够低,以减少管道中的摩擦和压力损失。然而,也有必要有足够高的粘度,以提供满意的磨损保护和减少液体泄漏。高粘度指数流体有助于在较宽的温度范围内保持满意的粘度。优质液压油的抗磨性能通常可以通过适当的添加剂得到改善。由于泵和阀门的间隙往往是关键的,因此提供足够的过滤设备(全流量或旁路,或两者都有)以保持最小的颗粒含量,从而最大限度地减少磨损是很重要的。液压油中的抗氧化剂添加剂应使油具有良好的氧化稳定性,避免形成不溶性胶或污泥;油应具有良好的水分离性能,并且,由于空气可能被带入系统,油应具有良好的空气释放性能和抗起泡性。同样,良好的防锈性能将有助于保持系统金属处于令人满意的状态。
柴油机油:除润滑油的典型作用是润滑、清洁、冷却和密封外,柴油发动机油的配方还能防止燃烧过程中产生的酸和烟尘颗粒。柴油发动机油与碱性添加剂混合,以中和柴油燃烧时产生的硫酸。它们还与分散剂/清洁剂混合,以保持发动机清洁,燃烧的副产品(燃料烟灰)悬浮。在柴油发动机中发现的磨损状态的组合要求润滑油中含有高水平的抗磨添加剂,以保护发动机在最严重的条件下免受磨损。多级润滑油(高粘度指数)常用于要求在宽温度范围内工作的柴油发动机润滑油。
涡轮机油:这些油提供令人满意的润滑和冷却轴承和齿轮(例如,在辅助涡轮机,泵和齿轮箱作为循环油)。他们也可以作为一个总督液压液。油的粘度必须足够高,以保持在负载表面上有足够厚的油膜,但又必须足够低,以减少能源损失,同时提供足够的冷却。这些油是推荐的程度上的轴承和齿轮的负荷小于齿轮油的应用。涡轮或循环油,或两者都有,具有优良的抗氧化性,并含有防锈剂;它们通常被称为R&O油。它们还可以包含添加剂,以改善水的可分离性和减少泡沫倾向。
压缩机油:这些油提供令人满意的润滑和冷却轴承和齿轮(例如,在辅助涡轮机,泵和齿轮箱作为循环油)。他们也可以作为一个总督液压液。油的粘度必须足够高,以保持在负载表面上有足够厚的油膜,但又必须足够低,以减少能源损失,同时提供足够的冷却。这些油是推荐的程度上的轴承和齿轮的负荷小于齿轮油的应用。涡轮或循环油,或两者都有,具有优良的抗氧化性,并含有防锈剂;它们通常被称为R&O油。它们还可以包含添加剂,以改善水的可分离性和减少泡沫倾向。此外,为了避免油包水乳液在后冷却器中积聚,水应该分离出来而不是形成乳液。
电液控制(EHC)油:三芳基膦酸酯EHC流体本质上是耐火的,并在其整个使用寿命内保持这种性能。非常低的蒸气压和这些流体的化学性质导致高闪点,燃点和自燃温度。应使用旁路系统持续净化EHC流体,以保持酸值、水分和颗粒在低水平。水分可导致EHC流体水解,导致酸值升高。应避免使用铜和铅合金构成的部件。这些流体的化学性质与矿物油不同;因此,对测试结果的解释将会有显著的不同。如果对分析结果的解释有疑问,应咨询流体供应商。
4.2 影响油品使用寿命的操作因素
4.2.1 新的油品质量和预期用途的适用性
使用符合公认标准(如制造商军用规格和OEM规格)的高质量油品是潜在的长期使新的油品质量和预期用途的适用性-使用符合公认标准(如制造商军用规格和OEM规格)的高品质油品是潜在的长期使用寿命的最佳保证。小心的油储存是重要的,以防止退化的润滑剂在储存或分配。准确的润滑油容器标签是至关重要的,以确保正确的识别。
- 粘度是石油最重要的特性。油的承载能力和润滑性能与油的粘度有关。使用粘度不正确的油会增加磨损率、热量积聚和润滑油降解。在极端情况下,使用粘度不正确的油可能导致迅速的灾难性故障。
- 使用符合设备制造商要求的油。对于制造商仅提供一般粘度分类而没有具体性能标准的情况,用户应咨询设备制造商、润滑油供应商和润滑领域的专家。
- 收到新鲜、未使用过的润滑油时,宜向供油方获取典型试验数据。在收到第一次充油后,取一个样品,以确认典型的测试数据,并作为基线。
- 为避免设备可能与残留冲洗油或之前充注的油混合,在真正基线油样启动时,对新充注油进行油样检查。
- 这一基准应作为流体物理和化学性质的参考样本,并用于将来与使用过的石油信息的比较。这是最重要的!新油的推荐试验已在本规程中给出。警告:安装后的润滑油的物理和化学性质可能与供应商提供的新润滑油的结果不一致。应遵循生产保质期建议。如果没有可用的保质期指导信息,并且润滑油的保质期超过两年,则应咨询润滑油制造商以确认是否适合使用。)
- 应遵守制造商的保质期建议。油应储存以保持其原始质量和防止污染。对储存的油进行测试,以确保和记录其质量、清洁度和对其预期用途的持续适用性。建议在储存润滑油时遵循石油制造商的建议,以确保最大的产品寿命。
- 补充油通常应该是相同的类型,质量和制造商。可用的配方可能会在一段时间内发生变化。润滑油的不兼容性可能来自混合不同的基础油和添加剂包装,应避免。当油必须混合时,应进行测试,试图确定相容性符合ASTM D7155。在混合油之前,应考虑咨询润滑剂供应商和设备制造商。
4.2.2 使用中油品变质
空气(氧气)、高温、金属和水(水分)都在一定程度上存在于润滑系统中。记录这些促进润滑剂退化的因素。润滑油的劣化是由下列一个或多个过程引起的:
- 氧化降解:这一过程是由大气中的氧引起的化学变化的结果,并通过在空气、水、热和某些金属的存在下催化的连锁反应进行。氧化的结果可能包括酸值增加,粘度增加,或污泥和清漆沉积,或在润滑系统内的最终产物的组合。
- 热降解:这个过程发生在缺氧和高得多的温度下。通常,超过300℃的温度可能会导致碳氢化合物分子裂解并产生各种降解物种。其中一些物种是低分子量的副产品,可以蒸发或燃烧(在油中产生明显的烧焦气味),其他降解物种是高分子量的副产品,可以形成污泥和清漆。
- 润滑油沉积和油泥(漆膜):由于润滑剂通过热和机械力降解,它们可能产生亚微米、高分子量、极性不溶性颗粒。这些颗粒可能会结块,在油中不溶,因为它在本质上是非极性的,并吸附在润滑系统的金属部件上。一些用于制造润滑剂的高精炼基础油(API II类及以上)可能对这些降解副产物的存在不太容忍,因为它们的纯度高,偿付能力低。基础油与适当的配方可以导致低沉积倾向的油。沉积物(如清漆)对设备操作人员来说是非常昂贵的,因为它们可能沉积在轴承和转动齿轮表面,增加磨损,滞留在伺服阀上,导致阀门粘滞和卡住,覆盖在热交换器上,降低其性能,并在储层中形成催化剂,进一步降解。如果系统中存在沉积物,可以对沉积物进行分析,找出可能的根本原因。不溶性极性化合物可以通过使用一些静电分离技术和小心地进行高速冲洗来除去。当这些条件的润滑剂沉积和污泥发生时,油的粘度有可能急剧下降,由此产生的液体的闪点也可能发生变化。
- 水解:水解是存在水分时的一种降解方式。这对磷酸盐(和其他酯类)非常重要,也可能对油基产品中的添加剂系统产生影响。水解的主要特点是在流体中产生腐蚀性的酸。
- 添加剂消耗:添加剂是用来保护油和提高其性能的能力。当这些添加剂在使用过程中消耗殆尽时,油的性能将会由于油的氧化、起泡、过度磨损或过早生锈而降低。
- 补新油率:几乎每个系统都需要添加新油,以弥补由于泄漏、更换过滤器或其他维护而造成的损失。监测添加新油的数量和频率,因为他们在决定系统油费用的寿命中起着非常重要的作用。
4.2.3 污染
润滑油的污染来自系统内外。常见的污染类型有:初始启动或大修后引入的碎片、润滑油降解副产品、部件磨损碎片、空气中的微粒和水(水分)。污染往往是影响油品使用寿命的最重要因素。油污是更换机油和冲洗以恢复系统清洁的一个有效理由。
- 设备启动条件:油系统在启动前的污染通常包括防腐剂、油漆、湿气、锈粒和建筑碎片,如灰尘、污垢或焊接飞溅。在制造、装配、安装、维修或修理过程中,必须极其小心地避免任何污染进入机器。如果可行,建议在开始操作前冲洗系统。在开始操作之前,流体清洁度应达到ISO 4406.2级别以下的一到两个级别。如果不进行冲洗,应在启动或维修后不久测试油,以确认其清洁度。
- 外部固体污染:固体污染由任何足够小的材料通过轴承密封和排气口或可以引入补充油。无论污染源是什么,必须通过监测油液状况和定期使用过滤器和离心机等净化设备来处理污染。
- 外部液体污染:冷却剂泄漏,湿气或蒸汽凝结,或引入不适当的润滑油会损害机油。积聚的水促进油的降解,并干扰润滑。不适当的润滑剂造成的污染,不彻底更换润滑油是不容易纠正的。油品监测程序可用于监测和识别在使用过程中可能遇到的污染物。
- 内污染:污染物包括磨损碎片和油降解产物。内部污染物的类型因设备类型和油类而异;发电速率将在很大程度上取决于设备的运行条件。所采用的分析方法必须能够识别预期的磨损碎片和降解产物。测试频率应足以说明工作条件。
4.3 取样
4.3.1 通用
当从油箱或运行中的设备中提取润滑油样品时,重要的是提取的样品具有代表性,并从指定的位置采集,以监测润滑油的性能。以下是一些关于正确取样技术和取样处理技术的建议指南。(请参见实践D4057。)用户应该有书面程序,以确保样品的采集始终符合良好的维护规范。
4.3.2 代表性取样
代表性取样位置是指支持可重复和代表性的润滑剂取样的取样位置,以监测设备的健康状况和润滑剂的性能。为了具有代表性,当机器或设备在正常工作温度、负载、压力和速度下运行时,收集油样。确保不溶性物质均匀地悬浮在体系中。流体样本在以下情况下可能不具代表性:(1)系统流体热样本时冷(2)系统中的流体是一种颜色或在一个内联眼前清晰玻璃样本是一个不同的颜色或清晰和(3)储层流体的流体粘度不同的样本都是在相同的温度。每次取样都应采用相同的方法,以确定可靠的石油性质趋势。
应当注意的是,有时可能要求提供不具代表性的样品。在此期间,必须按照要求者指定的抽样说明进行。例如,样品可以从容器的顶部或底部取下,以检查是否受到污染。在所有情况下,取样点应标记在取样容器上。
4.3.3 取样部位/取样位置
分配过滤器上游和轴承、齿轮等机器部件下游的样品位置,以获得最佳数据。过滤器下游的采样仅用于确定过滤器或过滤系统的效率(贝塔比)。
4.3.4 冲洗过程
- 冲洗通常用一个备用的容器/瓶子来截取被清洗的液体。在获得样品之前,冲洗5到10倍的死区体积是很重要的。
- 油接触到的所有硬件都被认为是死区,必须进行冲洗,包括系统盲端、采样端口、阀门和适配器、采样装置上的探针、使用真空采样泵的适配器、还有用于真空泵的塑料油管(这种油管不应重复使用,以避免油之间的交叉污染)。
- 在打开样品口并冲洗后,将样品容器/瓶注满大约其容量的50%,并留有足够的空隙,以便在测试前摇晃样品。在闪点测试的情况下,为了最精确的测试,减少头部空间体积。
4.3.5 记录抽样程序
确保每个样本被以同样的方式从同一点,操作符定义和文档油取样过程——接受的每个系统如:(1)工具(2)线冲洗要求(3)采样地点(4)抽样方法(5)安全要求(6)样品瓶标签。
应当注意的是,有时可能要求提供不具代表性的样品。在此期间,必须遵守要求者规定的抽样程序。例如,样品可以从容器的顶部或底部取下,以检查是否受到污染。在所有情况下,样品点应在样品容器/瓶上注明。
4.3.6 记录抽样程序
按规定频率采集油样;这将确保尽早发现任何问题。采样频率将专门为每台机器或设备设置,因为每台机器或设备的预期性能、条件、位置、操作环境和维护计划都是独特的。
4.3.6 样品容器/瓶
用油样容器或油瓶取油样:
- 清洁:如果对其清洁度有疑问,请使用另一个样品容器/瓶。如果不可能,请用待取样的液体将其冲洗掉。要特别注意确保用于水可分离性、颗粒计数和磨损碎片测试的样品容器/瓶子是清洁的。
- 对取样材料的抵抗力:例如,耐火的磷酸酯液体会溶解某些塑料。(包括瓶盖内的衬垫)为了验证样品容器/瓶的阻力,如果时间允许,允许样品站在样品容器/瓶中并观察其效果。铝箔或聚四氟乙烯(PTFE)制成的好,耐盖衬垫。
- 适用于要求的处理:顶部漏水的样品容器/瓶子和保护不当的玻璃样品容器/瓶子不适合装运。如果空运,必须遵守严格的包装要求。
- 适用于所要求的分析:例如,一些塑料样品容器/瓶可能不被接受用于闪点测试(根据测试方法D92),因为挥发性物质可能会从容器/瓶壁泄漏。使用玻璃或聚乙烯的样品容器/瓶子进行磨损碎片分析样品(以避免材料浸出)。
4.3.6 样品标签
样品标签正确地标签样品容器/瓶,以跟踪特定设备的历史。设备必须唯一标识。标签应适当包括以下信息:
- 客户名称
- 场地(或植物名称)
- 位置(单元号、槽号、舱号等)
- 设备序列号(或其他ID)
- 机油和机器的使用时间
- 采样日期
- 采样液体类型
- 采样点
- 净化系统类型(过滤器、离心机等)
- 上样后补样(量)
- 冷却剂添加剂。
4.3.6 新交付的油品取样
使用前彻底清洁所有采样设备,以避免交叉污染。
- 对正在检查的流体采取具有代表性的样品,但要从最能表明被碎片和水严重污染的点(即桶或油罐舱底部上方)取得样品。
- 当货物装在桶里时,按照惯例D4057对其进行取样。
- 当怀疑有污染时,除了对每一桶进行取样外,恐怕没有别的办法了。
- 对于散装货物,请在每个油罐车舱内取样。如果这些样品没有碎片和水,则可以将这些样品结合起来进行后续的实验室分析。用户可以决定对单个隔间样品进行数量有限的测试;复合样品还可以进行其他性能的测试。
- 最好从柔性管道的出口或至少从罐体底部阀门歧管处取样品。这一点很重要,因为油罐车的内容物可能会被留在底部阀门歧管中的残余物质所污染。这种情况尤其可能发生在不同的产品被放在不同的隔间中运送,或者之前不同的产品被运送到其他地点,但随后没有进行充分的清洁和冲洗。在取样之前,死管必须排干和冲洗。
- 这些采样器允许收集容器底部的沉淀物,而不会由于刮擦容器衬里或内壁而造成虚假污染。
4.3.6 样品的保存和油的分析
一般建议将油样立即运至油品分析实验室,最好在取样后的合理范围内进行分析。如果油样储存时间过长,可能会导致样品不具有代表性。
- 如样本须保留较长时间,应与油品分析化验所达成协议,作出特别安排,以确保样本的完整性不受影响。特殊的安排可能包括储存在深色的琥珀色玻璃瓶在环境中油样在容器/瓶中存放的时间越长,产生的氧化产物越多。
- 将样品储存在远离强光和尽可能接近室温的地方(深色油瓶)[CY]。
4.4 样品的保存和油的分析
一般建议将油样立即运至油品分析实验室,最好在取样后的合理范围内进行分析。如果油样储存时间过长,可能会导致样品不具有代表性。
- 当(1)设备的临界状态需要检测时,(2)油品质量存在问题时,或(3)需要基线数据用于趋势研究时,应检查新油的交付情况。可能被污染的水库的大小也应加以考虑。
- 经验表明,有必要对进口润滑油的取样、检查和验收程序和验收标准进行标准化。负责抽样和测试的人员必须具有必要的经验和技能,并且在任何时候都要一丝不苟地注意细节,以避免错误的结果。
- 同样重要的是,所有进厂的油料都要有充分的监控,以防止不正确或被污染的材料被输送。应注意交付集装箱的清洁度;如果容器外面脏了,里面可能有油的颗粒污染。当润滑剂与脏污或维护不善的设备接触时,颗粒污染也会成为一个问题。灌装设备的最后过滤可用于代替或除颗粒计数。当润滑剂与脏污或维护不善的设备接触时,颗粒污染也会成为一个问题。灌装设备的最后过滤可用于代替或除颗粒计数。最终的过滤器应与被充注设备的润滑系统过滤器一样细或更细。
- 对来料的抽样应按照适当的抽样程序进行(见第6节)。
- 所有的样品都应立即进行外观检查。
- 各种类型的新油的测试时间表指南见表1。使用桶时,在油投入使用之前,应先对复合样品(或散装样品)进行测试。个别样品应保留,直到大样品合格为止。
- 在油轮交付时,在油轮卸货之前要完成的额外测试只能从接受非规格产品所涉及的风险来判断。也就是说,如果随后的测试表明这是必要的,那么在投入使用之前,费用是否能够很容易地收回和纠正。
- 用户和供应商应清楚地沟通新油的产品规格。如果样品不符合用户和供应商商定的产品规格,则应重新测试样品,以验证最初的测试结果。如果需要,应进行重新取样和测试,以验证该样品是否具有装运的代表性。如果重新测试或重新取样仍然不符合产品规格,应进行调查,以确定问题是由于运输、处理或产品配方。如果需要,应进行重新取样和测试,以验证该样品是否具有装运的代表性。如果重新测试或重新取样仍然不符合产品规格,应进行调查,以确定问题是由于运输、处理或产品配方。用户必须认识到典型值与购买规范不相同。
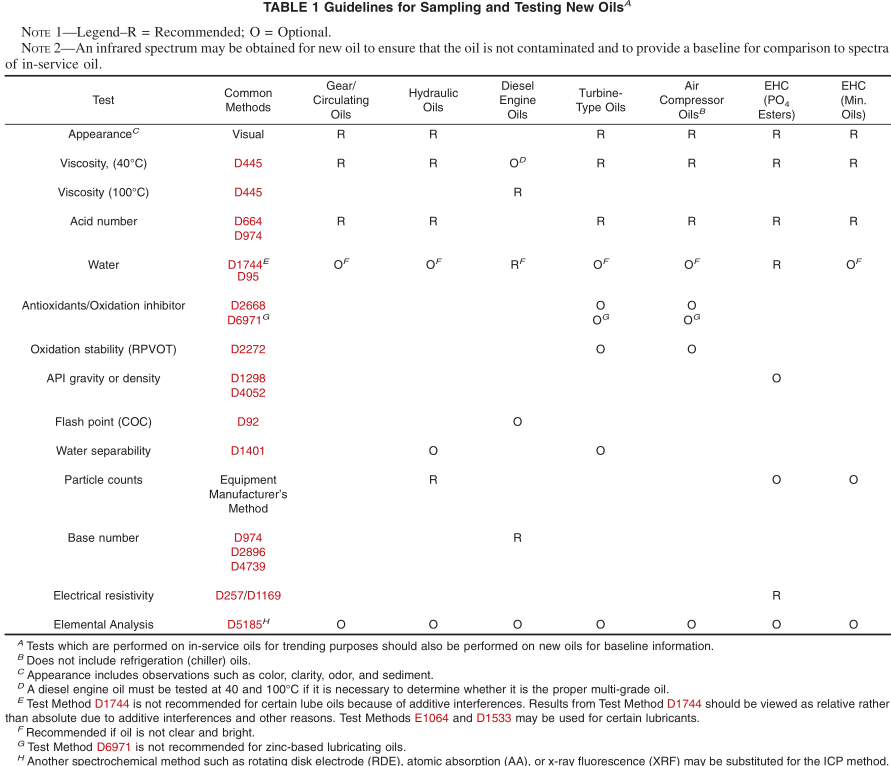
4.4 监测的意义
4.4.1 在确定持续使用的油和设备的状况时,在用油的重要特性包括:
4.4.2 黏度
大多数商品油是根据ISO(国际标准组织)粘度分类系统销售的。工业流体分为ISO VG-32、VG-46、VG-68和更高的粘度等级,在40℃时对应于32、46、68 cSt(分级D2422)。柴油发动机油在100℃下使用cSt单元进行测试,并使用SAE J300分级。齿轮油在40℃下使用cSt单元进行测试,并使用AGMA或SAE分类。粘度(例如,对于多级油)可以在40和100℃下测量,以计算粘度指数,并确定使用了正确的油。检查使用过的油粘度的主要目的是确定使用的油是否正确,并检测污染情况。在极端情况下,由于热降解或氧化降解,使用过的油的粘度会显著增加。污染可以使粘度增加或减少,这取决于污染物。乳化水和柴油烟灰会增加粘度,而柴油、氟利昂或溶剂会降低粘度。磷酸酯液中溶解的水能略微降低液体的粘度。来自不同润滑剂的污染可以改变油的粘度在任何方向。通常用于粘度测定的方法是试验方法ASTM D445。
4.4.3 酸值
用来表示氧化程度的最常用的测试是酸值(测试方法ASTM D664或ASTM D974)。对于磷酸酯,酸度通常是水解的一种指示。许多在润滑油中使用的防锈剂是酸性的,有助于新油的酸值。如果酸值高于新油的值,则表明存在酸性氧化产物,或酸性物质污染的可能性较小。由这两种试验方法测定的酸值并不完全相同,只是大致相关;应该一致地使用单一方法。不建议对颜色明显变暗的老化磷酸酯液体使用D974试验方法,特别是那些在使用前已经染色的液体。
4.4.4 水分/水含量
如果矿物油是清澈和明亮的,溶解的水的数量存在的意义不大。大多数矿物油在常温下与75ppm的水混合仍保持清澈。磷酸酯液体在环境温度下可容纳1000ppm以上的水,而且仍然清澈明亮。通过筛选方法(如矿物油的热板飞溅测试)确定的水的存在可以通过标准测试方法确定。含有大量水的油不能保持充分的润滑。试验方法ASTM D95的分析范围为0.05 ~ 25%,试验方法D1744的分析范围为50 ~ 1000μg /g。其他方法(如测试方法D96,D1533,E1064)可用于测量油品中的水分含量。
4.4.5 抗氧化剂水平
抗氧化剂浓度的测定对于工业润滑油的氧化和剩余使用寿命的监测具有重要意义。现有的测量酚(或胺)抗氧化剂浓度的方法包括红外光谱法(包括傅里叶变换红外)和线性扫描伏安法。
- 傅里叶变换红外(FTIR):测试方法ASTM E2412是一种精细的红外光谱法,可以用来监测混入油脂中的剩余抗氧化剂。它也可以用来监测氧化产物的增加随着石油降解。每一种抗氧化剂都是一种特定的化学物质,能够吸收特定波长的红外光和吸收能力;有些抗氧化剂可能不能被红外光谱检测到。(如果波长和吸收率已知,测试方法D2668可用于抗氧化剂。)
- 线性扫描伏安:伏安法是一种电化学测试技术,可用于测定多种抗氧化添加剂。该技术通过一个3电极传感系统应用一个电压斜坡,并测量当施加的电压等于抗氧化剂的氧化电位时的电流流动。峰值电流的电位可以诊断抗氧化剂,而峰值的振幅与抗氧化剂的浓度成正比。抗氧化剂,如受阻酚和胺,可通过测试方法D6971进行测量。
4.4.6 氧化稳定性(RPVOT)
新型含油抗氧化缓蚀剂最重要的性能之一是其在使用过程中的抗氧化能力。这是通过添加抗氧化剂来实现的,这些抗氧化剂的配方是为了保护油本身不被降解。测定抗氧化剂添加剂的浓度或添加剂的抗氧化能力(与新油相比)是监测工业润滑油降解的一个重要因素。这种测量的结果将为用户提供氧化稳定性储备的评级。测量氧化阻力的方法通常是热的,催化降解技术,如测试方法ASTM D943或ASTM D2272。试验方法D943通常用于新润滑油的比较,对于使用中的监测来说太长了。然而,与新油相比,D2272试验方法被广泛用于监测氧化稳定性储备。
新型含油抗氧化缓蚀剂最重要的性能之一是其在使用过程中的抗氧化能力。这是通过添加抗氧化剂来实现的,这些抗氧化剂的配方是为了保护油本身不被降解。测定抗氧化剂添加剂的浓度或添加剂的抗氧化能力(与新油相比)是监测工业润滑油降解的一个重要因素。这种测量的结果将为用户提供氧化稳定性储备的评级。测量氧化阻力的方法通常是热的,催化降解技术,如测试方法ASTM D943或ASTM D2272。试验方法D943通常用于新润滑油的比较,对于使用中的监测来说太长了。然而,与新油相比,D2272试验方法被广泛用于监测氧化稳定性储备。
4.4.7 颜色
新型润滑油的颜色从浅到中等深不等。深色会在服役中发生,但在一段时间内变化通常是缓慢的。因此,经常检查颜色对于快速的现场测试是有用的。一个明显的颜色变化就意味着某些东西发生了变化。要找出原因,必须进行更详细的检查。试验方法ASTM D1500是定义润滑剂颜色的标准方法。颜色变暗本身并不是引起警报的原因(除非有额外的测试支持)。
4.4.8 密度
这个测试只对污染有意义。例如,磷酸酯EHC流体不能耐受矿物油的污染。这项试验对于确定降解程度没有什么价值。通常使用的方法是做法D1298(比重计)。
4.4.9 闪点
润滑油的闪点必须远远高于最低适用安全要求。闪点对于检测柴油或低沸点溶剂的污染很有用。但是,燃点对于确定废油的降解程度意义不大,因为正常降解对燃点的影响不大。常用的方法是测试方法ASTM D92(克利夫兰公开口杯)。
4.4.10 不溶物
戊烷不溶物(测试方法ASTM D893)可能包括油不溶物和一些源于油或添加剂降解的油不溶性树脂物质,或两者兼有。甲苯不溶性材料可能来自(1)外部污染,(2)燃油碳和降解燃油的高碳化材料,以及添加剂,(3)发动机磨损和腐蚀材料。工业用油也可以用试验方法D2273进行不溶性测试。不溶物的显著增加表明了潜在的润滑问题。不溶物的测量还可以帮助评估新油的性能特征或确定设备故障的原因。
4.4.11 分水性
由于油冷却器泄漏、系统正常呼吸等原因,水可以进入润滑系统。水通过与金属作用催化氧化而对油产生不利影响。它还会消耗水敏感的油添加剂,如某些类型的防锈剂,并可能导致生锈和腐蚀。对于一些油,水会沉淀到储油罐的底部,在那里它应该排掉作为一个常规操作程序。净化系统也将帮助去除水。不幸的是,如果油的水可分离性较差(破乳性较差),大量的水可能会留在系统中,从而产生问题。除了对油和添加剂的化学影响外,油的润滑性能也会受到不利影响。使用试验方法ASTM D1401充分测量了油的水分离特性。该测试确定了大量水从油水乳状液中分离所需的时间。根据设计,水不会与一些润滑油(如发动机油)分离。这些油中的分散剂添加剂可以分散水、燃烧残留物、污垢和氧化化合物。
4.4.12 防锈性能
润滑剂提供的防锈保护对某些系统是重要的。在流体流动的区域,被静态水滴覆盖的表面,以及偶尔被润滑剂溅到的区域,都需要保护。含有防锈剂添加剂的新油必须满足测试要求,如测试方法ASTM D665。在使用中,这种添加剂可以通过以下方式消耗:(1)发挥其应有的作用,(2)用水去除,(3)吸附在磨损颗粒和其他固体碎屑上,或(4)与污染物发生化学反应。在碱水或污水进入系统的特殊情况下,添加剂的去除会更快。试验方法D665程序A(蒸馏水锈蚀试验)通常足以确定内陆设备的令人满意的防锈剂水平。对于海洋使用,建议采用试验方法D665程序B(海水锈蚀试验)。
4.4.13 泡沫特性/抗泡性
泡沫特性用ASTM D892测试方法进行测量,该方法显示了油的泡沫倾向和泡沫产生后的稳定性。此试验可用于排除设备中的油发泡问题。系统起泡问题有三个可能的根源。
- 机械——系统设计可以对润滑剂的发泡趋势产生重大影响。
- 消泡剂——消泡剂可以被机械去除(由于精细过滤、离心、机械剪切或吸附),因为它们是分散的,不溶于油中。
- 污染——应设法识别和去除污染物。在不能充分做到这一点的情况下,可以通过添加消泡剂来纠正。
4.4.14 空气释放性能
由在诸如轴承、联轴器、齿轮、泵和回油路等设备中,润滑油与空气的搅拌可能会在油中产生细小的气泡分散。如果在储油器中的停留时间过短,使气泡上升到油面,则空气和油的混合物将在润滑油系统中循环。这可能导致无法维持油压(特别是使用离心泵),轴承和齿轮上的油膜不完整,以及液压系统性能差或故障。在试验方法ASTM D3427中,油中含气减少到0.2%所需的时间被记录为气泡分离时间。
4.4.15 碱值
新的和旧的石油产品(特别是柴油发动机润滑油)可能含有碱性添加剂。这些物质的相对含量可以用酸滴定法测定。这个基数是油中基本物质含量的量度,因此也是添加剂损耗的量度。评价范围必须根据经验来确定。碱值测定法(ASTM D2896 高氯酸电位滴定法和ASTM D974 颜色指示剂滴定法)不能提供等效的检验结果;应该始终如一地使用一种方法。
4.4.16 氯含量
用微库仑法测定磷酸酯EHC液中氯的含量。过量的氯离子会导致电化学腐蚀,因为流体以快速的速度流过小的开口。
4.4.17 电阻率
由低电阻率的磷酸酯EHC液会引起伺服阀的腐蚀。
4.4.18 矿物油的含量
润磷酸酯EHC流体中的矿物油含量必须最小化,以保持防火性能。
4.4.19 乙二醇含量
醇基防冻液泄漏到曲轴箱是严重的,因为冷却剂往往干扰润滑剂及其润滑能力;它还会促进污泥的形成。由于乙二醇氧化以及乙二醇和润滑剂之间的相互作用,冷却液中的乙二醇会增加曲轴箱中清漆沉积的形成。润滑油的位移、淤积和沉积物的形成都会导致发动机故障和可能的振动发作。在较低水平检测乙醇基冷却液污染是很重要的,因为早期发现可以采取纠正措施,防止泄漏的冷却液积累和严重损坏柴油机。
4.4.20 燃油稀释
柴油机在正常运行时,可能会发生某些燃料稀释。然而,过度燃料稀释是在可能的性能问题方面的关注。
4.4.21 颗粒污染度
在运行中,固体很少有机会进入润滑油系统,尽管在灰尘非常多的地区,机组可能在室外,一些固体可以通过安装或操作不当的通风口、密封和进气口进入。在运行过程中,设备可能会开始积累大量的颗粒物。有些可能是通过添加补脂油进入系统的。在轴承轴密封处,粉煤灰可能与空气一起吸入。其他污染物可能是磨料降解(即磨损颗粒)和系统中产生的腐蚀产物。无论来源是什么,都不能容忍油中存在磨蚀性固体,因为它们会造成轴承和轴颈的划痕和损坏,并导致控制机制故障和卡死。这些必须用过滤器或离心机或两种方法去除。系统油的清洁度可通过颗粒计数(通过电子颗粒计数器)来确定。清洁度等级可以用诸如ISO FDIS 4406.2这样的分类系统来表示。ISO 4406使用一个数字代码来表示每毫升油中大于4μm(建议值)、6μm和14μm的颗粒数。ISO 4406分配整数值来表示粒子的范围,粒子的上限随每个连续数字翻倍。所需的清洁度等级有时由设备制造商或用户指定。
4.4.22 磨粒浓度(WPC)
研究表明,大、小磨损颗粒的分离和测量对相关机器磨损状态的检测和诊断是有益的。用于测量WPC的技术不应被视为颗粒计数,而应被视为特定磨损金属浓度的测量。评估结果时应谨慎,因为分离和测量技术可能是特定于合金的。为了检测磨损趋势的突然增加,并减少灾难性故障的可能性,对某一特定设备的磨损粒子浓度进行了一段时间的监测。
4.4.23 磨屑分析(WDA)
磨损碎片的微观分析可以用来描述正常摩擦磨损、严重滑动磨损、切削磨损、齿轮磨损或轴承磨损的磨损状况。此外,这种碎片分析可以发现纤维,砂/污垢,润滑油降解残留物,红色氧化物,黑色氧化物,铁球。对于每一种磨损状态,即磨损磨屑的大小和同一类型的颗粒浓度的组合,都可以给出相应的转速。
4.4.24 元素分析
发射光谱可以用来分析在旧润滑油中发现的元素。这种分析通常局限于溶解的物质或小于8µ的颗粒。发现的元素来自磨损碎片、添加剂和污染。
- 金属部件上的一些磨损可以认为是正常的(尽管不是理想的)。大量的金属污染物通常意味着严重的机器故障。
由于不同的机器部件是由不同的金属制成的,所以特定金属的存在表明哪些部件正在磨损。当一台机器被取样多次时
(或当测试了多台同一类型的机器时),进行评估,以确定金属浓度是否超出正常范围。如果设备上的金属浓度以异常高的速度增加或超出正常范围,则表明该设备可能存在问题。当没有历史数据可用时,就有可能对某一特定磨损金属及其浓度没有给予足够的重要性。 - 某些元素被发现作为润滑油添加剂,也可以分析,以确保适当的添加剂存在,并没有其他无机添加剂表明交叉污染已发生。应对未使用的油进行分析,以便为将来的比较建立基线。
- 油中的污染物(如污垢和水)可以携带整个机器,造成严重的磨损或腐蚀。污垢的存在可以通过硅(或铝)的存在来检测。淡水和处理过的水的无机成分可以用元素分析来检测。例如:钙来自未经处理的水,钠和镁来自海水,钾、钠或硼来自冷却水。EHC液体的存在,钠、铝、钙、镁是最常见的地球释放富勒年代或活性氧化铝进入系统或生产的可溶性和不可溶性金属皂液(可以有不利影响发泡和空气释放属性)。
4.5 状态监测项目
4.5.1 一个良好的状态监测方案是基于四个因素:
- 获得有代表性的样本,并在适当的时间间隔进行检测;
- 测试数据的记录、趋势和解释;
- 纠正措施步骤;
- 跟进维修措施。
4.5.2 油样的取样和测试
时间表应根据设备使用的关键和严重程度量身定制。表2中包含的时间表是典型的,应该只作为一个指南使用。请参阅OEM(原始设备制造商)说明或其他法规指南的润滑剂测试要求。除了表2中的测试外,在油中发现的或从系统中除去的任何沉积物都应检查和识别(如果可能的话)。
- 推荐的(R)检测是监测的最低水平。这些测试提供了有关特定流体质量和使用在役流体的设备状况的大部分信息。(间接测量这些特性的替代测试设备可以根据用户的判断和风险被替换。)
- 可选(O)测试是指那些可以提供关于油或设备状况的额外信息的测试。这些测试可能对某些但不是所有的设施有益。如果样品量或分析时间有限,省略这些测试的影响通常小于省略推荐测试。
- 根据需要(AN)测试可以提供有关操作问题的信息。例如,发泡特性测试可以确定发泡问题是由于油还是机械原因。根据需要,还可以根据其他测试的结果执行测试。例如,当磨损颗粒浓度高于某一水平时,可以进行磨损碎片分析。
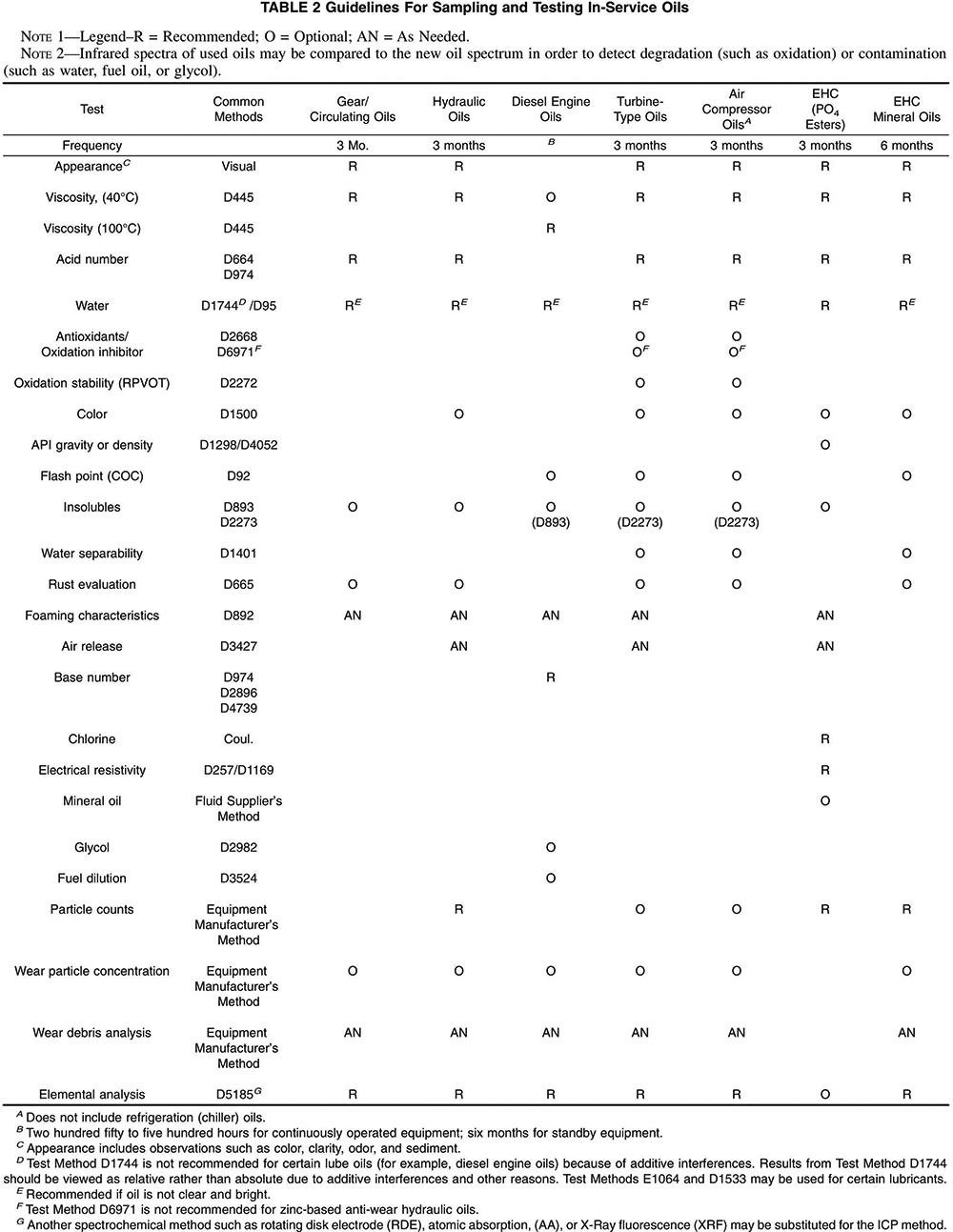
注:使用过的油的红外光谱可以与新的油光谱进行比较,以检测降解(如氧化)或污染(如水、燃料油或乙二醇)。
4.5.3 测试数据的记录、趋势分析和解释
保持测试结果和补充监测的准确记录非常重要。强烈建议用图形表示关键参数,如酸值、抗氧化剂、磨损粒子浓度、碱值、磨损金属和RPVOT。通过这种方式,不寻常的趋势变得明显,并更好地估计剩余的使用寿命。对测试数据的解释应考虑到一些因素,如油的添加(补充或更换油),可能的油的混合,新安装的部件和最近的系统检查。表3中提供了各种润滑油类型的警告级别指南。油供应商或原始设备制造商(OEM),或两者,指南取代表3。这些警告级别也应该与趋势信息一起考虑。
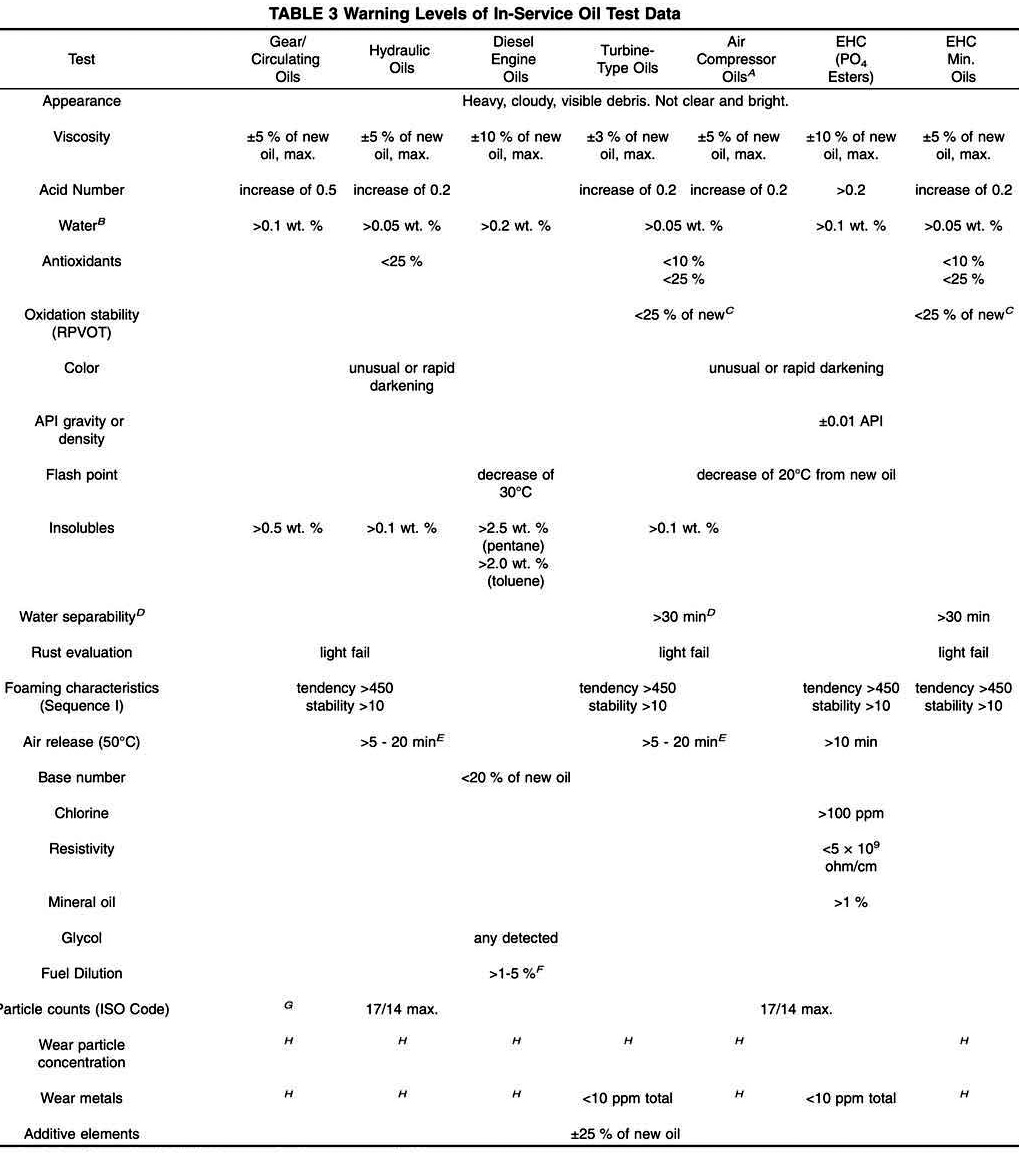
4.5.3 操作步骤
监控程序的主要目的是确保设备长期无故障运行。这只有在必要时采取迅速和适当的行动步骤才能实现。这些行动步骤必须基于对测试结果的正确解释(见表4),通常是在一段时间内收集的。纠正措施一般不应根据一个测试结果采取,因为它可能是不正确的,由于不良的采样或错误的测试。在继续之前,建议重新取样和重新检测。由油供应商或原始设备制造商建议的操作,或两者都建议的操作将取代表4中的操作。
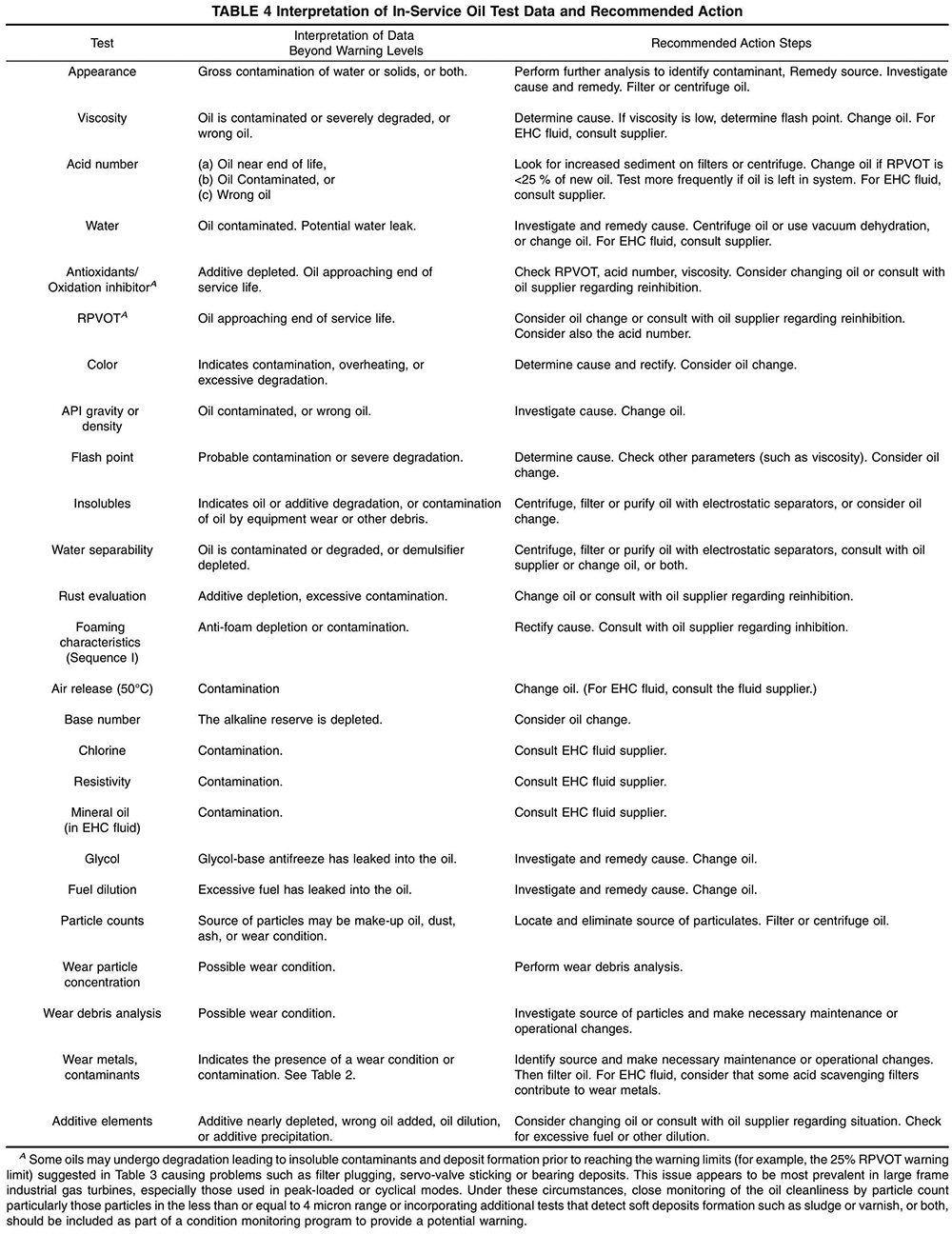
注:有些油在达到警告限值(如表3中建议的25% RPVOT警告限值)之前可能会发生降解,导致不溶性污染物和沉积,从而导致过滤器堵塞、伺服阀卡死或轴承沉积等问题。这一问题似乎是最普遍的大型框架工业燃气轮机,特别是那些使用在峰值负载或循环模式。在这种情况下,通过颗粒计数来密切监测油品的清洁度,特别是那些小于或等于4微米范围内的颗粒,或结合其他测试来检测软沉积物的形成,如油泥或清漆,或两者兼有,应作为状态监测程序的一部分,以提供潜在的警告。
4.5.5 在用润滑油中污染物(无机元素)的来源
磨损金属、添加剂和污染物的可能来源如表5所示。这个表格是工业资料的汇编。它的目的是作为一项指南,不应被认为是包罗万象的。除所需的润滑剂外,任何来自润滑剂的添加剂元素都可以被描述为污染物。
的来源.jpg)
注:青铜合金通常含有88%的铜,8%到10%的锡和2%到4%的锌。巴氏合金通常含有84 - 92%的锡,4 - 8%的铜和4 - 8%的锑。铅基巴氏合金通常含有75 - 80%的铅,5 - 10%的锡和15%的锑。
4.5.6 维修跟踪
当对油品监测程序中的设备进行维护时,所进行的工作和发现的问题应记录在案,并提供给负责解释油品测试数据的人员。通过这种方式,测试数据解释器可以(1)确保执行了推荐的维护,(2)提出更好的建议,(3)更好地了解测试数据如何与设备问题相关联。
五、预览及下载
部分文档较大,加载稍慢:
文档类型:PDF(图片),注册后免费下载,下载异常请联系微信:haorunhua_com
文字版价格面议。
下载地址:登录后显示。