十五、抗磨性(Anti-wear Properties)/极压性(Extreme Pressure Properties)
15.1、基本概念
润滑油的抗磨性和极压性是衡量润滑油润滑性能的重要指标。抗磨性是指润滑油在轻负荷和中等负荷条件下,能在摩擦副表面形成润滑油薄膜以抵抗摩擦副表面磨损的能力。极压性是指润滑油在低速高负荷或者高速冲击负荷条件下,抵抗摩擦副表面发生烧结、擦伤的能力。
15.2 监测的意义
润滑油在使用过程中时常会因极压抗磨添加剂损耗降低润滑油的抗磨性能,导致设备润滑部件的异常磨损。在开展设备润滑磨损状态监测过程中,有必要对新油和在用油的极压抗磨性能进行不定期的抽查,以确保润滑油品的极压抗磨性满足设备需求。
15.3 分析方法
润滑油抗磨损性能的测定方法很多,“四球法”应用最为广泛。
- 润滑剂极压性能测定法 四球法:GB/T 12583等效采用ASTM D2783;
- 润滑剂承载能力的测定 四球法:GB/T 3142;GB/T 3142与GB/T 12583《四球法 润滑剂承载能力测定法对比 论文》;
- 润滑油承载能力的评定法 FZG目测法:SH/T 0306修改采用ASTM D5182,主要应用于齿轮和变速箱用油评定,汽轮机油也常用;
- 润滑油抗磨损性能的测定 四球法:SH/T 0189修改采用ASTM D4172;
- 润滑剂摩擦系数测定法 四球法:SH/T 0762修改采用ASTM D5183。
GB/T 12583方法概要:四球机的一个顶球,在施加负荷的条件下对着油盒内的三个静止球旋转。油盒内的试样投设三个试验钢球。主轴转速为1760r/min±40 r/min,试样温度为18~35℃。按本标准的规定逐级加负荷,做一系列的10s试验直至发生烧结。
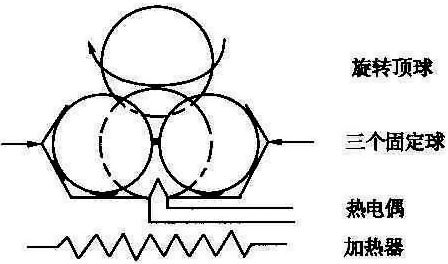
四球磨损试验机示意图
下面是“四球法”测定润滑油抗磨性和极压性的主要检测指标。
- 最大无卡咬负荷PB值,即在试验条件下钢球不发生卡咬的最高负荷。它表征油膜强度。
- 烧结负荷PD值,即在试验条件下使钢球发生烧结的最低负荷。它表征润滑油的极限工作能力。
- 综合磨损值ZMZ,是润滑油在所加负荷下使磨损减少到最小的抗极压能力的一个指数,它等于若干次校正负荷的算术平均值。
- 磨斑直径D,是指润滑油在负荷为392N,时间为60min的长磨条件下,钢球表面的磨损斑痕的直径,用来评价润滑油的抗磨能力。
15.4 评定标准(报警指标/换油指标)
用于评定新油的极压抗磨等级。
15.5 变化的原因
- 极压抗磨添加剂消耗。
15.6 采取措施
- 加换油。
15.7 相关知识点
根据摩擦副的接触应力选择低、中、高极压性能的润滑油。接触面的应力计算和润滑油的极压性能选择可参考JB/T 8831《工业闭式齿轮的润滑油选用方法》或ANSI/AGMA 9005-E02《工业齿轮润滑》。
现代设备负荷的增高和工作环境的恶劣,使许多设备特别是那些低速重载的摩擦副表面间难以形成完整连续的抗磨润滑油膜。在这种条件下,全凭润滑油中的极压抗磨添加剂与金属起化学反应、在摩擦副表面生成剪切应力和熔点都比原金属要低的极压固体润滑膜来防止摩擦副表面烧结磨损。例如重负荷的工业齿轮油、车辆齿轮油等对极压抗磨性能都要有较高的要求。若极压性能不好,则在高负荷、冲击负荷的作用下,润滑油很难起到良好的抗磨作用,加速摩擦副的异常磨损。因此,对有极压性能要求的润滑油必须进行极压性能检测。四球法的PD值检测是评价润滑油极压性能最简单且最实用的方法之一。
十六、光谱分析
16.1 基本概念
光谱分析分为红外光谱和元素光谱。红外光谱主要用于分析添加剂消耗、污染物累积、油品的降解、水污染等趋势监测。元素光谱主要用于监测添加剂元素、磨损金属和污染物的含量;元素光谱原子发射光谱法和原子吸收光谱法。
16.2 监测的意义
润滑油在使用过程中基础油氧化降解、添加剂消耗、污染物混入以及设备磨损都需要及时进行监测,通过监测这些物质的含量的变化趋势可分析判断设备的运行状态。
16.3 分析方法
16.3.1 原子发射光谱法:
SH/T 0853修改采用ASTM E2412《在用润滑油状态监测法 傅里叶变换红外(FT-IR)光谱趋势分析法》。方法概要:
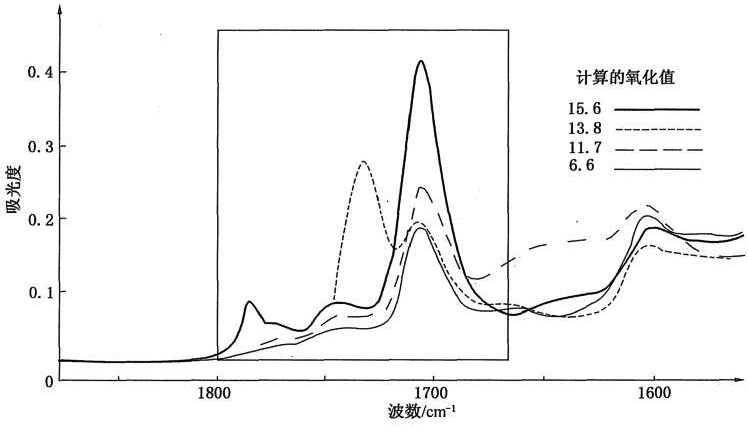
红外光谱分析新油配方中含有羧基组分
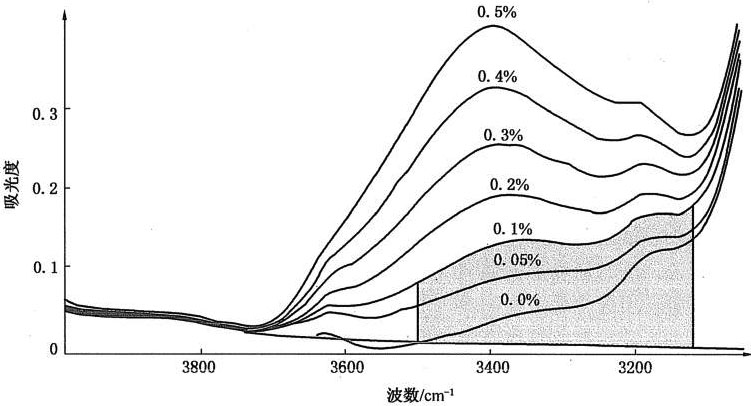
红外光谱 水含量
16.3.2 原子发射光谱法:
GB/T 17476等效采用ASTM D5185《用感应耦合等离子体原子发射光谱法(ICP-AES)测定使用过的润滑油中的添加元素、磨损金属和污染物以及基础油中选定元素》。本标准可测定使用过的润滑油中各种添加剂元素、磨损金属和污染物的含量。它也能测定基础油或再生基础油中多种金属含量的变化。所测定的元素包括:铝 、硼 、钡、钙、铬、铜、铁、铅、镁、锰、铝 、镍、磷、钾、钠 、硅、锡、银、硫、钛、钒和锌共 22种元素。
方法概要: 油样可不经过消解直接稀释后测定。将待测油样或经稀释后的油样放置在光谱仪的高压火花里激发“燃烧”,使油样中的各元素原子被激发为高能态。核外电子从不稳定的高能轨道跃迁回原轨道,同时释放出具有特征波长的光子,形成发射光束。发射光束由光栅按其波长分开,通过光电倍增管或固体检测器将各光谱的光信号转化为电信号而被测定。各特征波长发射光的强度大小与油样中相应元素的含量成正比。
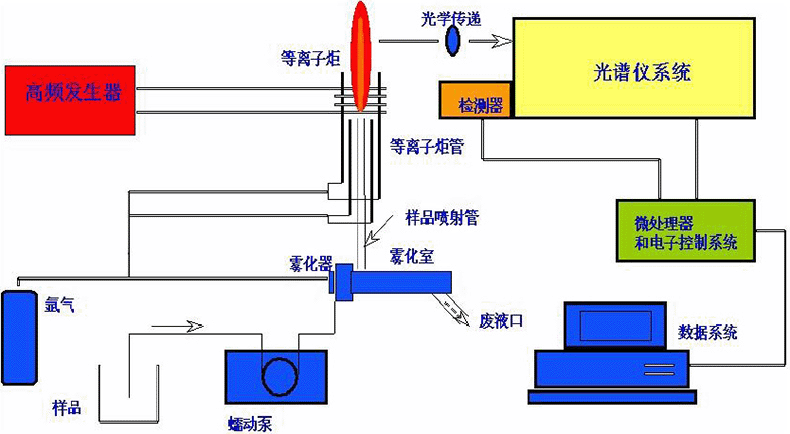
16.3.3 原子吸收光谱法:
方法有SH/T 0228《润滑油中钡、钙、锌含量测定法(原子吸收光谱法)》,SH/T 0061《润滑油中镁含量测定法(原子吸收光谱法)》等。
方法概要:油样首先进行预处理,配制成待测样品。将样品吸入火焰并汽化转变成气态自由原子状态,同时将具有与被分析元素相同特征波长的光束射入火焰。所测元素的自由原子吸收射入的特征波长的光能而产生吸收信号,吸收光能量的大小与被测油样中该元素的含量成正比。
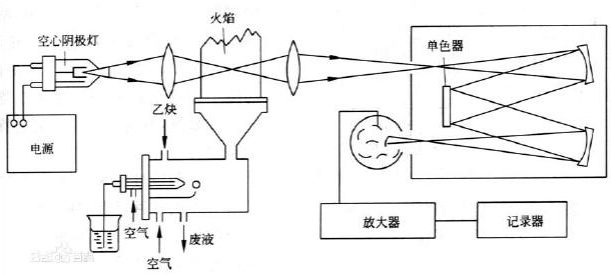
16.4 评定标准(报警指标/换油指标)
原子发射光谱:金属磨损量<10-20ppm。添加剂元素:±25%;
16.5 变化的原因
- 磨损
- 污染
16.6 采取措施
- 进行磨屑分析。
16.7 相关知识点
方法对比:
原子发射光谱法:该方法的特点是检测速度快、测定元素范围广、操作简便,故被广泛用于油液监测领域,但测量精度比原子吸收光谱要低。
原子吸收光谱法:润滑油添加剂元素原子吸收光谱分析法的主要特点是精度高,测定元素范围广。但该方法的检测速度较慢,难以满足油液监测快速、大量的要求,所以应用面不广。
十七、铜片腐蚀(Copper Corrosion)
17.1 基本概念
润滑油中活性硫化物、低分子有机酸、无机酸、碱对金属的腐蚀作用。
17.2 监测的意义
润滑油对机械零部件的腐蚀,主要是油中活性硫化物、有机酸、无机酸等腐蚀性物质引起的。这些腐蚀性物质一方面是基础油和添加剂生产过程中残留下来的,另一方面则是油品在使用过程中的氧化产物。为了保证油品对机械设备不产生腐蚀,腐蚀试验几乎是评定新油质量的必检项目。
17.3 分析方法
GB/T 5096《石油产品铜片腐蚀试验法》与ASTM D130《石油产品铜片腐蚀试验法》方法相同。
方法概要:将一块已磨光好的铜片浸没在一定体积的试样中,根据试样的产品类别加热到规定的温度,并保持一定的时间。加热周期结束时,取出铜片,经洗涤后,将其与铜片腐蚀标准色板进行比较,评价铜片变色情况,确定腐蚀级别。
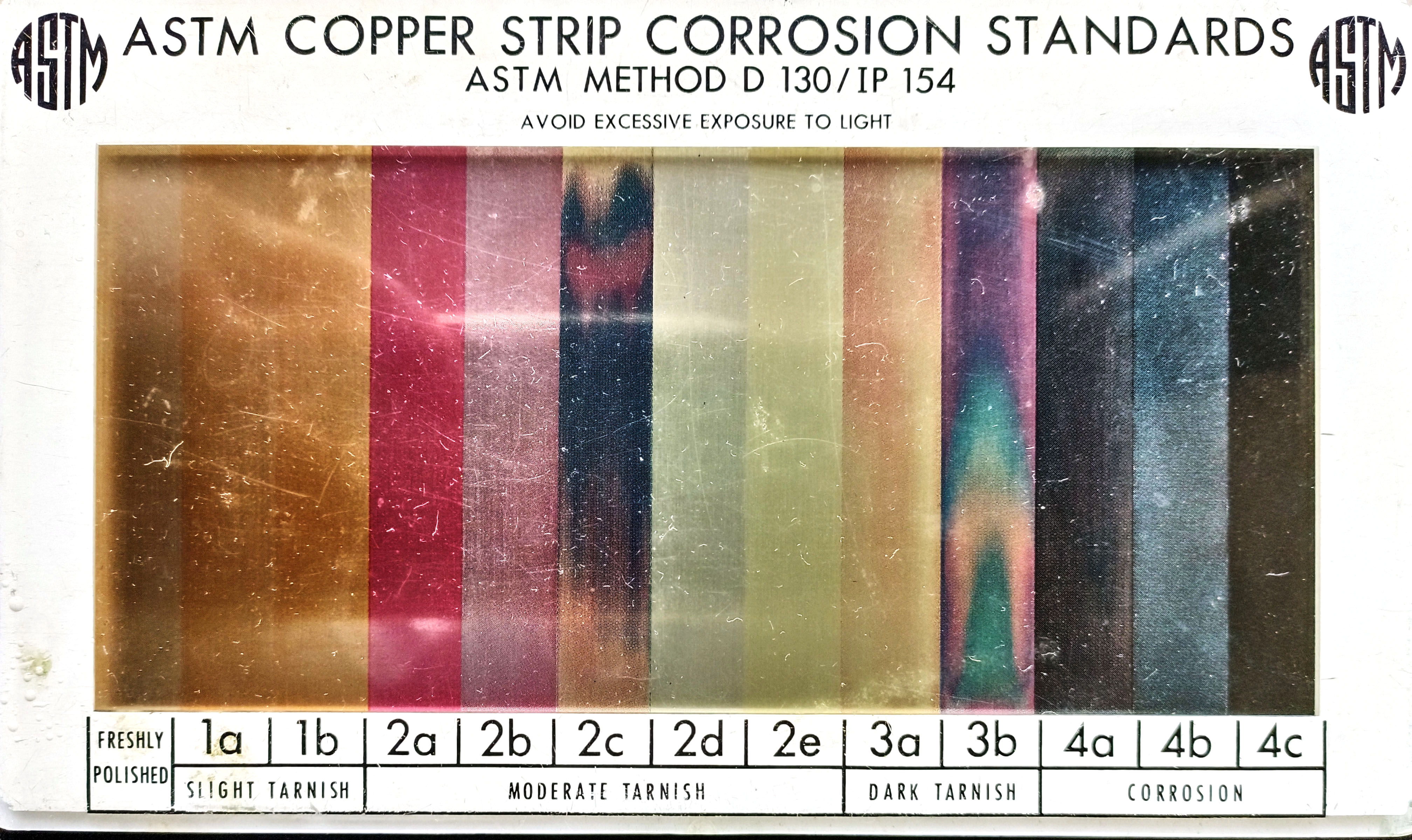
ASTM D130铜片腐蚀比色卡
腐蚀标准色板分级,分为四度12级:1无腐蚀;2为中度,2c开始认为有轻度腐蚀,新油不允许;3为深度,3a已认为有腐蚀;4为重度腐蚀,4a已是严重腐蚀。
17.4 评定标准(报警指标/换油指标)
不同润滑油对铜片腐蚀的接受程度差别很大,例如:汽轮机油2a,齿轮油3b。
17.5 变化的原因
- 添加剂消耗。
- 污染。
- 系统维护不正常(如疏于排水、排水设备故障等)。
17.6 采取措施
- 调查原因,进行必要的维护和操作更改。
- 加换油、排气、脱水。
- 重新检查锈蚀试验,如果试验结果没有变化,请与油供应商协商可能的补救措施。
17.7 相关知识点
原油中含有硫化物,大部分硫化物在提炼过程中被除去。然而,在石油产品中残留的硫化合物中,有些可能对各种金属有腐蚀作用,这种腐蚀性与总硫含量不一定直接相关。油品制备时残留的无机酸和碱,对金属的腐蚀作用。
十八、颗粒污染度(particulate contamination level)
18.1 基本概念
颗粒污染度,也叫清洁度或颗粒度,是指通过检测油液中污染粒子的分布、大小尺寸及数量来评价油品的清洁程度。 颗粒污染度标准分为颗粒度测定方法、测定标准、分级标准。
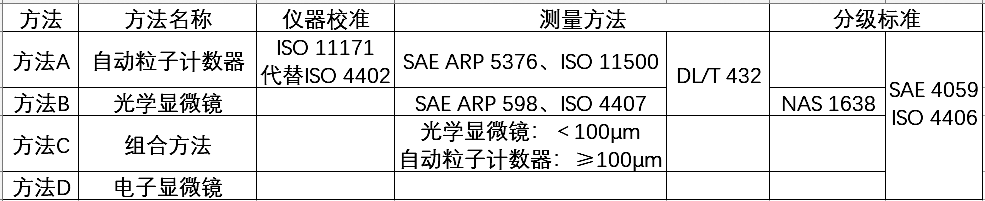
参考 SAE 4059F
测定方法有自动颗粒计数法和显微镜测定法;测定标准有:DL/T 432(自动颗粒计数法和显微镜测定法)、ISO-11500(自动颗粒计数法)、 ISO 4407(显微镜测定法)等;分级方法有NAS 1638(显微镜测定法和称重法)、SAE 4059F(自动颗粒计数法和显微镜测定法) 、ISO 4406、GB/T 14039等。
18.2 监测的意义
润滑油在实际应用中的污染是不可避免的,对液压介质进行污染控制的目的是为了最大限度地保持液压介质的清洁,从而延长设备和润滑油的使用周期。
18.3 分析方法
根据仪器测试的原理不同,可以分为两类:自动颗粒计数法和显微镜对比法。
18.3.1 自动颗粒计数仪法
依据遮光原理来测定油的颗粒污染度。当油样通过传感器时,油中颗粒会产生遮光,不同尺寸颗粒产生的遮光不同,转换器将所产生的遮光信号转换为电脉冲信号,再划分到标准设置好的颗粒度尺寸范围内并计数。
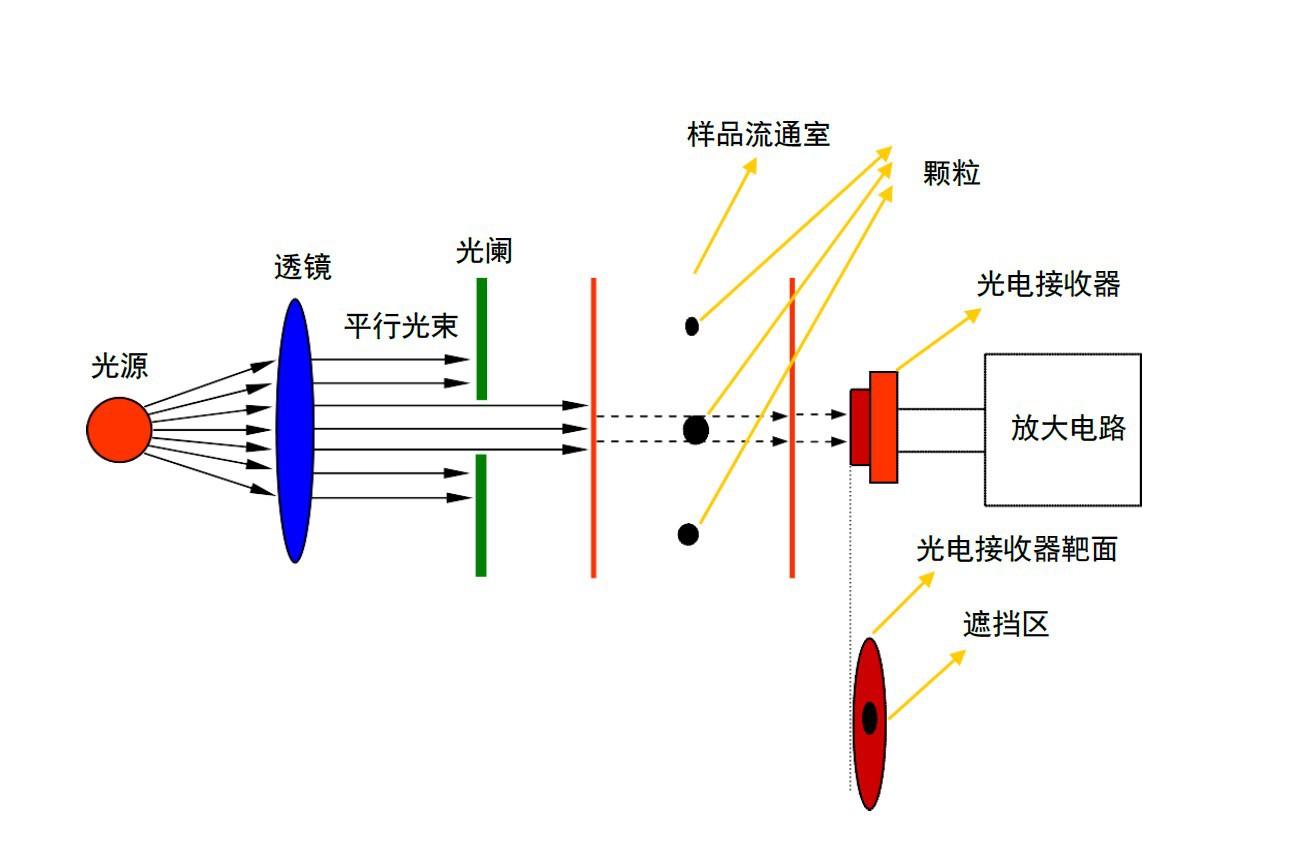
使用自动颗粒计数器计数所报告的污染等级代号由三个代码组成,该代码分别代表如下的颗粒尺寸及其分布:
- 第一个代码代表每毫升油液中颗粒尺寸≥4μm(c)的颗粒数;
- 第二个代码代表每毫升油液中颗粒尺寸≥6μm(c)的颗粒数;
- 第三个代码代表每毫升油液中颗粒尺寸≥14μm(c)的颗粒数;
18.3.2 显微镜对比法
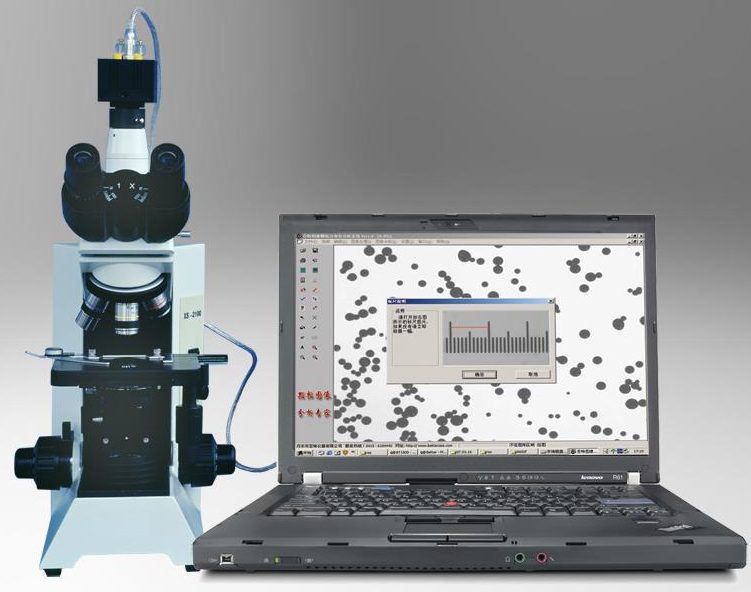
显微镜对比法油液污染等级用>5μm和>15μm两个尺寸范围的颗粒浓度代码表示。相当于自动颗粒计数器计数的6 μm和>14μm。
18.3.3 颗粒物数量、代码的换算
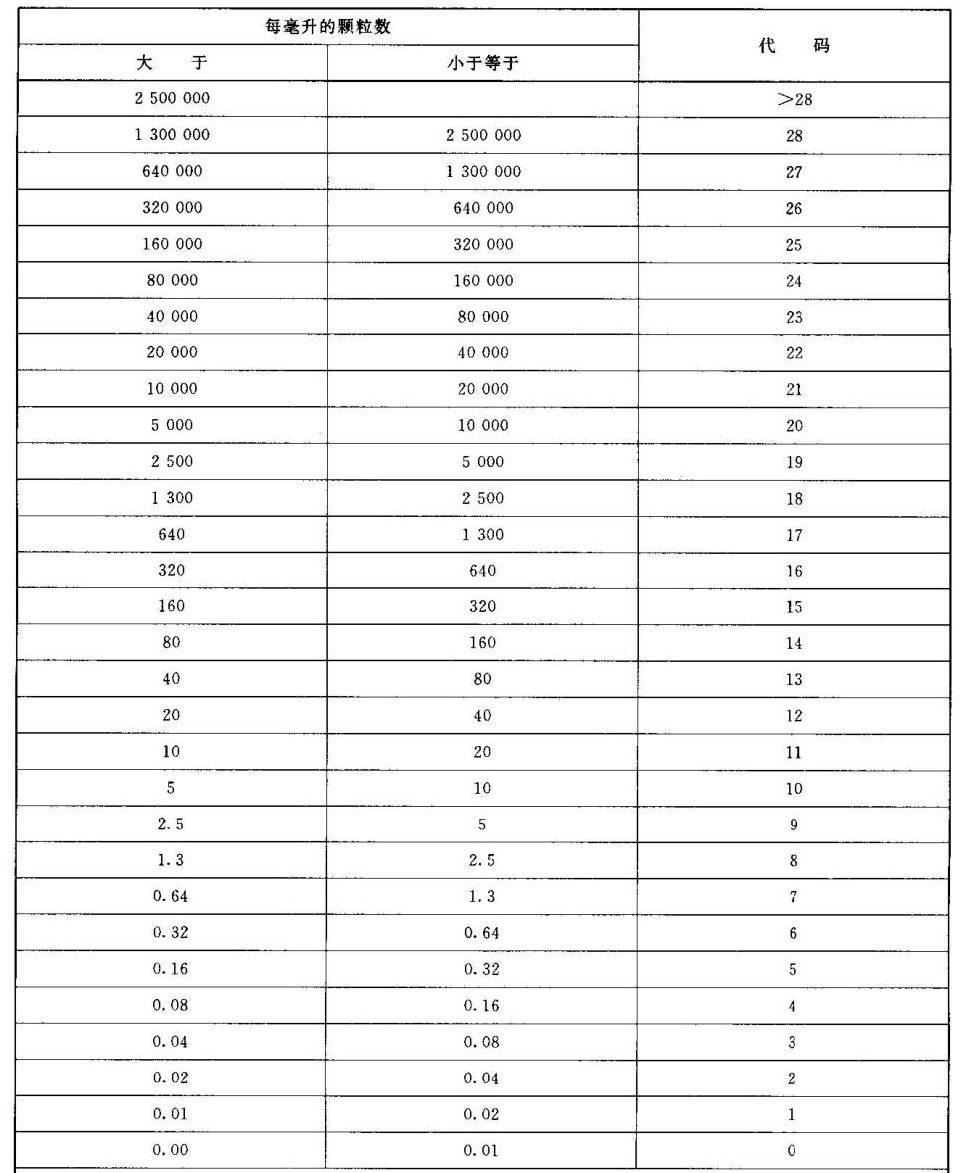
颗粒物数量、代码的换算
ISO和SAE标准是按照100ml计量的,上述颗粒数*100,等级不变。
18.3.4 ISO等级、NAS等级的换算
两种清洁度标准不能直接比较或转换,因为两种体系的基本原则相差很大。ISO 4406是 ≥4μm、≥6μm 、≥14μm或>5μm、>15μm;NAS 1638 是分段计数的,5~15μm、15~25μ m、25~50μ m 、50~100μ m 、>100μ m 。SAE 4059包括了这两个标准。但是根据经验和设备运行使用情况,可做如下简单换算。
- 21/17/14可以换算为NAS 8级,理由是:工程实际应用表明,对摩擦副影响最大的是6-14μm的颗粒;小于6μm颗粒进入摩擦副影响不大;大于14μm颗粒不能进入摩擦副,所以影响也不大。为方便记忆,直接用中间一个数字减9即可,即:17-9=8。
- -/17/14 前面的“-”表示4μm的不用考虑;
- */17/14 前面的“*”表示4μm的太多,无法计量。
18.4 评定标准(报警指标/换油指标)
API 614等使用标准一般要求“19/17/14 ”或更好“18/16/13“ 或OEM。新产品往往不能达到 “19/17/14 ” ,而需要在使用1-2周后才能达到该标准。
18.5 变化的原因
- 新建/检修系统时,未彻底清理干净:油箱、泵、管路、驱动机构/润滑部件,举例:PSA管路现场焊接;
- 系统使用过程中产生的:运动部件磨损、润滑油讲解;
- 外界污染:加油过程、尘杂环境。举例:磨煤机。
18.6 采取措施
- 定位和消除微粒来源。
- 检查油中是否含有不溶性和磨损金属。
- 通过过滤或离心或两者一起清洗系统油。
18.7、相关知识点
NAS1638是分段计数的,有5个尺寸段。由于实际油液各尺寸段的污染程度不可能相同,因此被测油样的污染度按其中的最高等级来定。这会引起一个问题。例如,测出的5~15μm的污染度可能是4级,15~25μm颗粒的污染度可能是6级,25~50μm可能是5级,而50~100μm颗粒的污染度可能是8级,这时数据就很难处理,往往使得概念不清。如果保守的话,就会按照规定判定为8级,认为系统很脏。而事实上,新的磨损理论表明只有尺寸与部件运动间隙相当的颗粒才会引起严重的磨损,也就是说5~15μm的颗粒危害最大,而50~100μm由于无法进入运动间隙,对磨损的影响却不大。
- 润滑油系统中的污染物从何而来?
- 润滑油中的固体颗粒会对运动表面有何影响。
十九、剩余使用寿命(RULER)
19.1 基本概念
通过测量润滑油中抗氧化剂的剩余浓度来定量地测定润滑油的剩余使用寿命。
19.2 监测的意义
润滑油中的抗氧剂会随之使用时间延长逐渐消耗,首先消耗的是酚类抗氧剂(先导型抗氧剂),而后消耗的是胺类抗氧剂(分解润滑油被氧化形成的产物)。通过监测这两类抗氧剂的含量来表征润滑油的剩余寿命。低端润滑油只有酚 类抗氧剂。
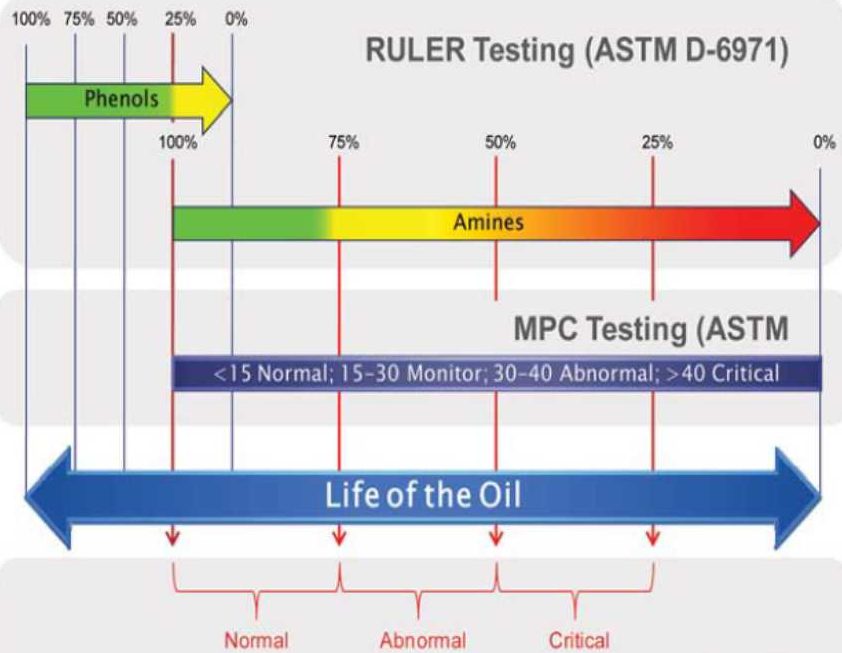
酚类 胺类抗氧剂消耗顺序 润滑油寿命
19.3 分析方法
RULER的检测基于线性伏安法。原理是在特定的电压值下,溶液中抗氧化剂的化学活性被激活,形成氧化电流,并得出一条氧化电流对时间的曲线,即报告中”剩余抗氧化剂含量图” 上的曲线,简称”RULER曲线”。随后通过软件将新油与旧油的RULER曲线进行峰面积相比,算出旧油中剩余抗氧化剂含量。润滑油中抗氧化剂种类主要分为胺类和酚类。通常情况下,在8~12s产生胺类的吸收峰;13~16s产生酚类的吸收峰,如下图所示。
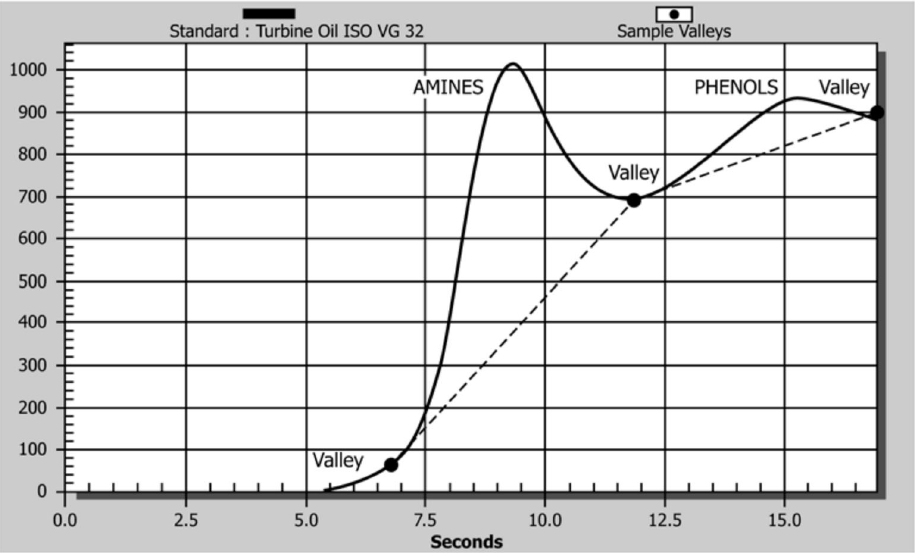
横坐标代表检测时间,单位”s”;纵坐标代表电流的反馈。
润滑油剩余使用寿命测定的方法:
- ASTM D7590在用润滑油主要的抗氧化剂含量测定 线性扫描伏安法;
- ASTM D6971无锌透平油中受阻酚和芳香胺抗氧化剂含量测定 线性扫描伏安法;
- ASTM D6810-13无锌透平油中受阻酚抗氧化剂含量的标准试验方法 用线性扫描伏安法;
- ASTM D7527-10润滑脂中抗氧化剂含量的标准试验方法 线性扫描伏安法。
方法概要:汽轮机油抗氧化剂含量(RULER)的测定方法为ASTM D6971,结果报告为抗氧化剂胺类、酚类的百分含量。具体检测步骤如下:
- 新油RULER图(下图细线):取一定量待测油样的新油置于RULER专用测试试剂中,摇匀、静置后检测,得RULER曲线A;
- 在用油RULER图(下图粗线):取与新油相同含量的在用油于RULER专用测试试剂中,摇匀、静置后检测,得RULER曲线B;
- 解图:将A、B曲线数据导入电脑进行解析。
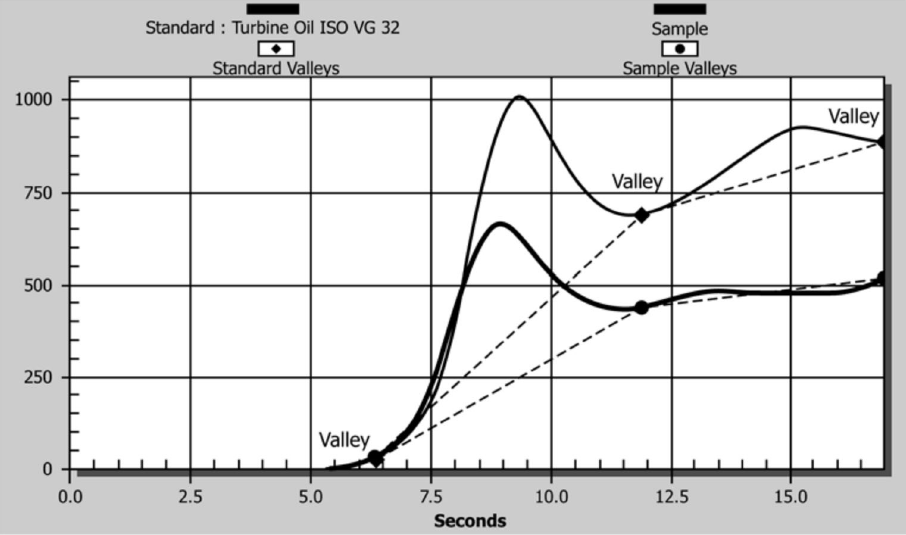
19.4 评定标准(报警指标/换油指标)
酚类或胺类抗氧剂>25%。
19.5 变化的原因
- 消耗
19.6 采取措施
- 加换油
- 咨询油品供应商补充添加剂。
- 监测漆膜和污染物。
19.7 相关知识点
润滑油中抗氧化剂种类主要分为胺类和酚类。酚类抗氧化剂易挥发,先降解;胺类抗氧化剂耐高温,后降解,但易形成漆膜。
十二、漆膜倾向性(MPC)
20.1 基本概念
用膜片比色法测定在用涡轮机油中不溶的有色物质,用不溶物的含量表示润滑油生成漆膜(Varnish)倾向性程度, 简称MPC,漆膜倾向性指数。
20.2 监测的意义
该测试可作为润滑油生成不溶物的趋势监测,作为润滑油状态监测的一部分,应用在ASTM D4378《在用蒸汽、燃气和联合循环涡轮机的汽轮机矿物油监测的标准操作规程》。
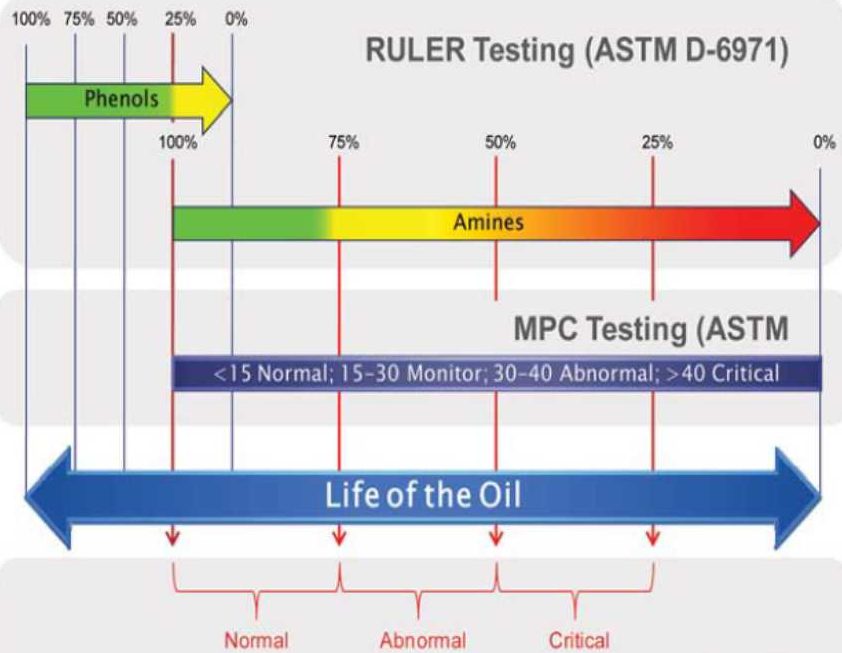
20.3 分析方法
GB/T 34580-2017《用膜片比色法测定在用涡轮机油中不溶有色物质的方法》 ,它参照采用ASTM D7843-12,最新版为 ASTM D7843-21 。
方法概要:用直径为17 mm、孔径为0.45 um硝基纤维素材料的微孔滤膜将不溶物从运行涡轮机油中分离出来,并用色差仪来测量该膜的颜色,结果用CTELAB色度中的∆E来表示。
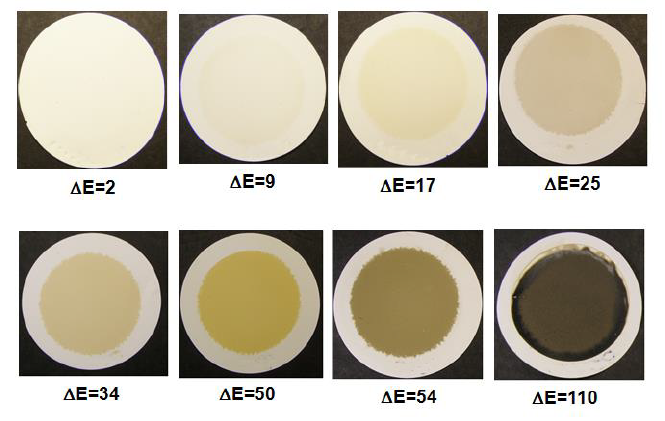
20.4 评定标准(报警指标/换油指标)
- ∆E <15:正常;
- ∆E 15~30:监控;
- ∆E 30~40:不正常;
- ∆E >40:严重。
20.5 变化的原因
- 润滑油被氧化。
20.6 采取措施
- 颗粒污染物;
- 监测氧化性能;
- 采取措施去除漆膜;
- 更换油品。
20.7 相关知识点
对机组润滑油进行状态监测时,一定要结合颗粒污染物、漆膜倾向性指数、氧化性能(例如旋转旋转氧弹)等指标进行综合分析和判断,同时关注轴瓦温度变化情况。