二十一、残炭(Carbon Residue)
21.1 基本概念
油品的残炭值,是指油品在特定的高温条件下,经过蒸发及热裂解过程后,所形成的炭质残余物占油品的质量百分数。主要用于内燃机油:柴油机油、汽油机油的测定。
21.2 监测的意义
残炭值的大小与油品的化学组成及灰分含量有关。除灰分外,油品中的胶质、沥青质及多环芳烃等物质是残炭的主要来源。故通常情况下,残炭值可用来表征油品的相对生焦倾向的大小(含有生灰添加剂的油品除外),用于指导原料的选择及油品的生产工艺。
21.3 分析方法
目前我国正在使用的残炭测定方法共有4种:康氏法(GB268):微量法(GB/T17144)、电炉法(SH/T170)和兰氏法(SH/T160)。康氏法是世界各国普遍采用的一种标准方法;微量法是近些年国内外普遍采用的一种简便而高效的残炭测定方法,我国于1997年正式列为国家标准方法;电炉法源于原苏联,使用的国家很少;兰氏法因其残炭数据与康氏残炭间只存在近似关系,故较少被采用。鉴于不同残炭测定方法的工作原理、实验装置、操作条件等因素均存在一定差别,利用不同方法得到的测定结果间的相关性如何一直是油品分析工作者关心的问题。
康氏法有: GB268、ISO 6615、ASTM D189,三个方法是一致的。把已称重的试样置于坩埚内进行分解蒸馏。残余物经强烈加热一定时间即进行裂化和焦化反应。在规定的加热时间结束后,将盛有碳质残余物的埚置于干燥器内冷却并称重,计算残炭值(以原试样的质量百分数表示)。
21.4 相关知识点
康氏法广泛应用于多种石油产品。本方法和ZBE 30001《石油产品残炭测定法(兰氏法) 》这两种方法所测得的残炭值,不但在数值上不相同,而且它们之间也找不到满意的相互关系。对于一些不容易装入兰氏焦化球的重质残渣燃料油、焦化原料等油料,宜用本方法测定残炭燃烧器燃料的残炭值,可用来粗略地估计燃料在蒸发式的釜型和套管型燃烧器中形成沉积物的倾向。同样,不含硝酸戊酯(或如果含有硝酸戊酯,则只要事先测定未加此添加剂基础燃料)的柴油,残炭值大体上与燃烧室的沉积物有对应关系。
二十二、LNF磨粒分析
22.1、基本概念
使用CCD成像技术和先进的图像处理程序,通过测量润滑油中颗粒尺寸分布、增长趋势和磨粒形状来识别颗粒形貌、生产率和机械故障的严重程度。
22.2 监测的意义
相当于颗粒物分析和铁谱分析 ,参考颗粒污染物和铁谱分析的意义。
22.3 分析方法
ASTM D7596《LNF磨粒分析 润滑油自动颗粒计数和颗粒形状分类的标准》方法概述:将样品置于LNF磨粒分析仪的转盘中,样品通过检测器上的导管进入成像仪内自动进行颗粒计数和形貌分析,仪器原理如下图:
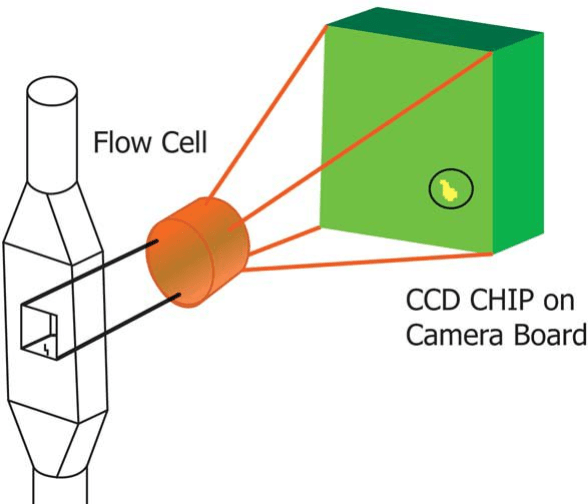
22.4 相关知识点
通过LNF磨粒分析能同时了解到油品的NAS,ISO清洁度以及五种磨损颗粒(切削磨损颗粒、疲劳磨损颗粒、滑动磨损颗粒、非金属颗粒、其他颗粒)的大小数量等信息,从而系统地掌握润滑系统中的磨损颗粒和污染物的情况,对判断设备是否运行正常或者是否需要预先性维护具有重要的意义。
二十三、蒸发损失(Evaporation Loss)和挥发性(Volatility)
23.1 基本概念
蒸发损失:在有恒定气流抽出的条件下,润滑油试样在坩埚内加热所产生的挥发性油蒸气的质量损失。
挥发性:液体形成蒸气的趋势。
23.2 监测的意义
润滑油的挥发性与油耗、粘度稳定性、氧化安定性有关,这些性质对多级油和节能油尤其重要。蒸发损失与润滑油的挥发度成正比,蒸发损失越大,实际应用中的油损耗就越大。液压油在使用中蒸发,还会产生气穴现象和效率下降,可能给液压泵造成损害。
23.3 分析方法
润滑油蒸发损失的测试方法有GB/T7325-1987《润滑脂和润滑油蒸发损失测定法》和SH/T0059-2010 《润滑油蒸发损失测定法 诺亚克》。
GB/T 7325方法是把放在蒸发器中的润滑油试样置于规定温度的恒温浴中,热空气通过试样表面22h,然后根据试样的质量损失计算蒸发损失,可以测定在99-150℃范围内的任一温度下润滑油的蒸发损失。该方法主要用于合成润滑油和润滑脂的蒸发损失评定。
SH/T 0059-2010方法参照ASTM D5800-08标准编写并进行了修订。SH/T 0059方法是试样在规定的仪器中,在规定的温度和压力下加热1h,蒸发出的油蒸气由空气流携带出去。根据加热前后试样量之差来测定润滑油的蒸发损失。
国外主要测试方法有ASTM D972,DIN 51581和JISK2220 (5.6) 等。
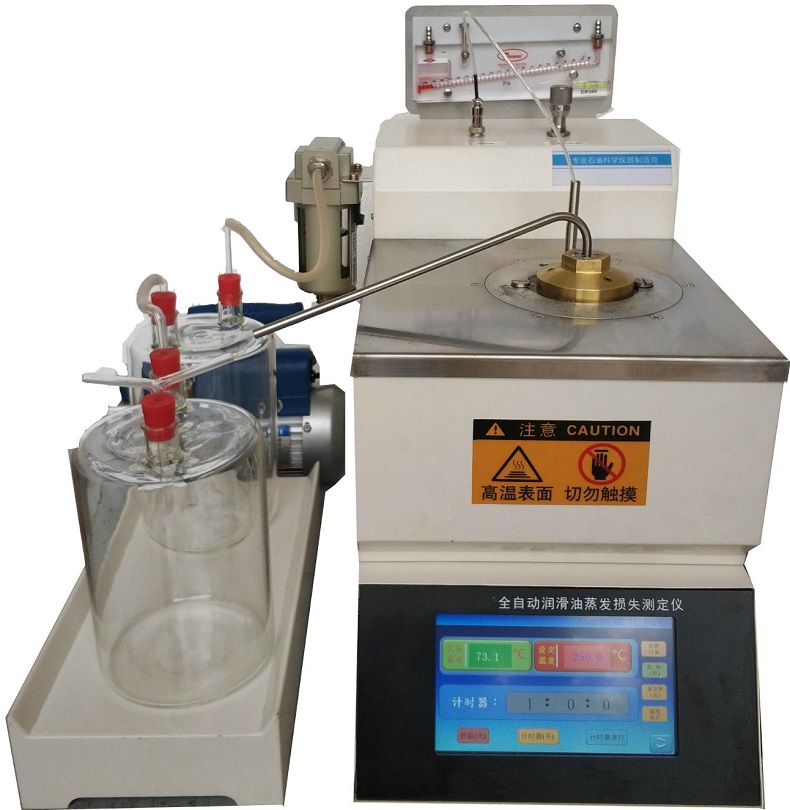
23.4 评定标准(报警指标/换油指标)
部分合成航空润滑油要求蒸发损失损失小于一定值。
23.5 变化的原因
- 用于新油性能的测定。
23.6 采取措施
- 无。
23.7 相关知识点
部分机组使用粘度较小的润滑油,造成现场油雾多、卫生差,部分油箱甚至设置了专用的排油烟风机和收集器。
二十四、相容性(Compatibility)
24.1 基本概念
润滑油相容性实验分为:润滑油与润滑油的相容性实验,润滑油与橡胶的相容性(密封性)实验。
24.2 监测的意义
润滑油在线置换过程中,确保两种油品不发生异常反应,生成过多的沉淀物,导致油品性能降低。润滑油使橡胶密封件溶胀、 收缩、硬化、龟裂,质量增加或减少 ,导致密封失效。
24.3 分析方法
24.3.1 两润滑油相容性实验
润滑油之间的相容性实验是测试两种润滑油混兑后再一定条件下是否产生沉淀以及理化性能是否改变,主要用在润滑油(在线)替换前进行,ASTM D7155《涡轮机油混兑相容性实验》。方法概要:两种油液分别以90:10、50:50、10:90、比例,充分搅拌混合后在65摄氏度的烤箱中储存23-25 小时,在外线照射,然后进行评估,混合液的任何一项指标应介于两种油液之间或优于性能更优者认为合格,否则认为该项测试不合格。
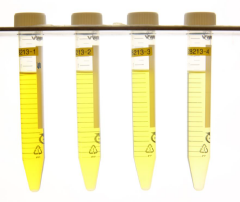
24.3.2 润滑油与橡胶件相容性实验
实验标准有SHT0877、SH/T0429、GJB1820。
方法概要:橡胶在润滑油中浸泡一定时间后,可能发生溶胀、收缩、硬化、龟裂,质量增加或减少,硬度也可能变大或变小,其他力学性能如抗张强度也可能变化。若润滑油与橡胶相容性好,则上述变化较小,否则上述变化较大。
24.4 评定标准(报警指标/换油指标)
两润滑油混合后的指标不低于较差的一种润滑油的指标。
24.5 变化的原因
- 两种润滑油的添加剂发生反应。
- 润滑油与橡胶发生反应。
24.6 采取措施
- 无。
24.7 相关知识点
在液压系统中以各种类型的橡胶作为密封件者很多,在机械中的油品不可避免地要与一些密封件接触。橡胶相容性不好的润滑油可使橡胶溶胀、收缩、硬化、龟裂,影响其密封性,因此要求润滑油与橡胶有较好的适应性。液压油标准中要求橡胶密封性指数,它是以橡胶圈浸在油中一定时间的变化来衡量的。
二十五、剪切安定性(Shear Stability)
25.1 基本概念
剪切安定性是指油品抵抗剪切作用,保持粘度以及和粘度有关的性质不变的能力。
25.2 监测的意义
润滑油中的粘度指数改进剂是链状高分子聚合物,工作时在零件摩擦表面不断受到剪切,使分子扭变、断裂,造成润滑油相应温度下的粘度下降,粘温性变差。所以多级油(内燃机油)规格项目中对剪切安定性提出了要求。
25.3 分析方法
测定剪切安定性的方法很多,有超声波剪切法SH/T 0505-2017《含聚合物油剪切安定性的测定 超声波剪切法》、喷嘴剪切法SH/T 0103-2007 《含聚合物油剪切安定性的测定柴油喷嘴法》、SH/T 0845-2010《传动润滑剂粘度剪切安定性的测定 圆锥滚子轴承试验机法》、威克斯泵剪切法、FZG齿轮机剪切法,这些方法最终都是测定润滑油品的粘度下降率。
通过测定润滑油在高温高剪切速率条件下的表观粘度测定也可以反映油品的剪切安定性,实验方法为SH/T 0703-2001润滑油在高温高剪切速率条件下表观粘度测定法 多重毛细管粘度计法。
方法概要:在规定温度下,将30ml试样在聚能器(超声波振荡器)中受超声波剪初10min引起的粘度损失,以油的粘度下降率来表示。
25.4 评定标准(报警指标/换油指标)
无。
25.5 变化的原因
- 用于新油性能的测定。
25.6 采取措施
- 无。
25.7 相关知识点
加入增黏剂的润滑油在使用过程中,由于机械剪切的作用,润滑油中的高分子聚合物被剪断,使油品粘度下降,影响正常润滑。
二十六、分析式铁谱法(Analytical Ferrography)
26.1 基本概念
在用润滑油中磨损颗粒在分析式铁谱仪的磁场作用下沉积在基片上,然后在铁谱显微镜下对磨损颗粒的形态、尺寸和覆盖面积进行观察和测量,定性分析机械的磨损状况。用于分析内燃机油、齿轮油、液压油等油品在使用过程中机械零部件产生的磨损颗粒的形态、尺寸大小和浓度变化趋势。
26.2 监测的意义
铁谱的目的是根据在油中观察到的颗粒的数量和类型来诊断被取样机器的工作状态。正常运行的机器显示一致的粒子浓度和粒子类型从样品到样品。颗粒浓度的增加,伴随着颗粒类型的大小和严重程度的增加,预示着磨损的开始。
26.3 分析方法
国内一般采用SH/T 0573-93在用润滑油磨损颗粒试验法 分析式铁谱法 ,国外一般采用ASTM D7690-11(2017)《用分析铁谱法对使用中的润滑剂颗粒进行显微表征测试》。
在用润滑油中的磨损颗粒在分析式铁谱仪的磁场作用下沉积在基片上,然后在铁谱显微镜下对磨损颗粒的形态、尺寸和覆盖面积进行观察和测量,以分析机械的磨损状况。
26.4 评定标准(报警指标/换油指标)
暂无,依靠分析人员的长期积累的经验。根据磨损颗粒的类型和材质,结合摩擦副材质,判断磨损部位及严重程度。
26.5 变化的原因
- 异常磨损。
26.6 采取措施
- 监控磨损的发展趋势,结合状态监测判定机器可运行的时间。
26.7 相关知识点
SH/T 0573-93 在用润滑油磨损颗粒试验法 分析式铁谱法 磨损颗粒定性分析:
- 正常磨损颗粒的特征是薄片状、表面光滑,颗粒细小均匀,长轴尺寸为0.5~15 um,厚度为0.15~1um。在机械磨合阶段,还产生一些长条状、扁平状的颗粒,这种颗粒也属于正常磨损颗粒。
- 切削磨损颗粒的特征是线状、卷曲状、弧状、车屑状、长条状,当硬摩擦面有锐边时,产生较粗大的切削磨损颗粒,长度为25~100 um,宽度为2~5 pm;当两个摩擦面之间存在一个硬的夹杂物时,产生较细小的切削磨损颗粒,长度为5~10 um,厚度约为0.25mm;
- 滚动疲劳磨损颗粒有三种形态:疲劳剥落碎片、球状和层状颗粒。(1)、疲劳剥落碎片长轴尺寸一般大于10 um,最大可达100 um ,形状因子小于5:1,有一个光滑的表面和不规则的周边。(2)、球状颗粒直径一般为1~3um,最大可达10um;(3)、层状颗粒是扁平的薄片、长轴尺寸为20~50 um、形状因子大于30 :1、颗粒表面有一些空洞。
- 严重滑动磨损颗粒的特性是长轴尺寸在20um以上,形状因子大于5:1、小于30 :1、表面有明显的滑动条纹、有时出现高温引起的色彩。
- 有色金属的磨损颗粒特征是颗粒不按磁场方向排列。而以随机方式沉淀,它们大多偏离铁磁性磨损颗粒链或处在相邻两链之间,并往往带有有色金属本身的特征颜色。
- 铁的氧化物中红色氧化物颗粒在白色偏振光下呈红棕色多晶体团状,主要成分是aFe2O3,而黑色氧化物颗粒在白色反射光下呈黑色,表面有蓝色和桔黄色的小斑点,主要成分是不成固定比例的Fe3O4、a Fe3O4 ,和FeO的混和物;
- 摩擦聚合物特征是在双色光下可观察到无定形的胶体中嵌有金属磨损颗粒,金属磨损颗粒呈红色,而胶体呈透明的绿色。
- 腐蚀磨损颗粒的特征是颗粒非常细小,即使在放大倍数为1000的情况下,单个颗粒也不容易区别开来,颗粒在谱片出口区两侧有堆积,并在整个谱片上都能观察到。
- 切削磨损颗粒、疲劳磨损颗粒、严重滑动磨损颗粒、腐蚀磨损颗粒、金属氧化物都属于不正常磨损颗粒,它们的大量出现意味着机械的磨损严重。
- 谱片的加热分析:(1)调节谱片加热器,使温度达到330±10℃。(2)将谱片置于谱片加热器上,加热90s,(3)在铁谱显微镜下观察磨损颗粒表面生成的氧化层的特征回火色,通常在白色反射光下,铸铁磨损颗粒呈草黄色,低合金钢磨损颗粒呈蓝色。
二十七、色度(Color)
27.1 基本概念
用标准比色卡定量表述石油产品(润滑油、加热油、柴油燃料油和石油蜡等)的颜色等级。
27.2 监测的意义
石油产品颜色的测定主要用于生产控制,是一项重要的质量特性,因为颜色很容易被产品的用户观察到。在某些情况下,颜色可以作为材料精制程度的标志。当某一特定产品的颜色范围已知时,超出该范围的变化可能表明可能受到另一产品的污染。
27.3 分析方法
GB 6540等效采用ASTM D1500《石油产品颜色测定法》。 方法概要:将试样注人试样容器中,用一个标准光源从0.5-8.0值排列的颜色玻璃圆片进行比较,以相等的色号作为该试样的色号。如果试样颜色找不到确切匹配的颜色,而落在两个标准颜色之间,则报告两个颜色中较高的一个颜色。
27.4 评定标准(报警指标/换油指标)
GB/T 14541《电厂用矿物涡轮机油维护管理导则》≤5.5;SH/T 0599《液压油换油指标》变化<2。
27.5 变化的原因
- 污染。
- 过度降解。
27.6 采取措施
- 确定原因并纠正,或考虑换油。
27.7 相关知识点
颜色并不总是产品质量的可靠指南,不应该在产品规格中不加区分地使用。
感 谢 !
课程到此结束,欢迎大家并提出宝贵意见。下期课程讲解设备润滑所涉及到的标准规范。
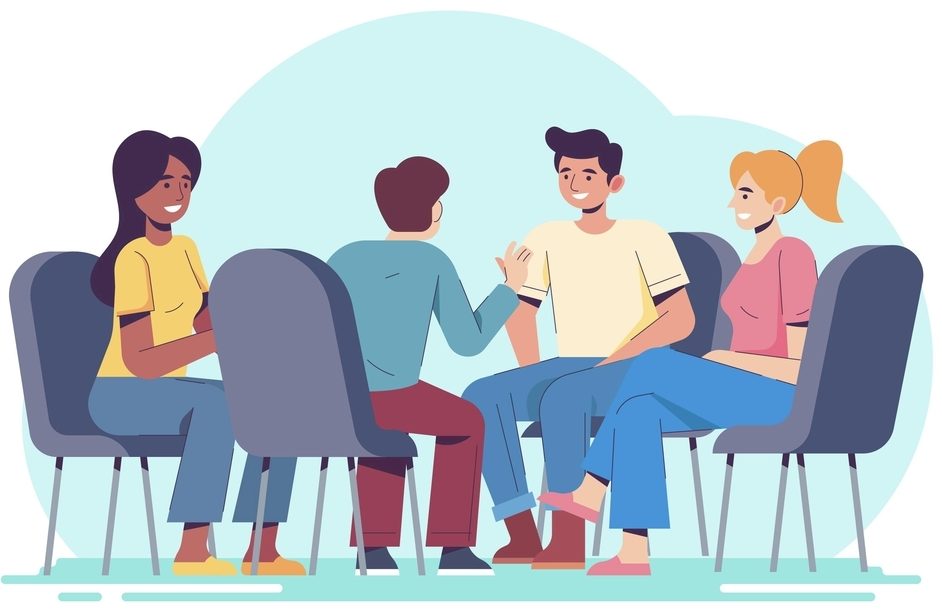