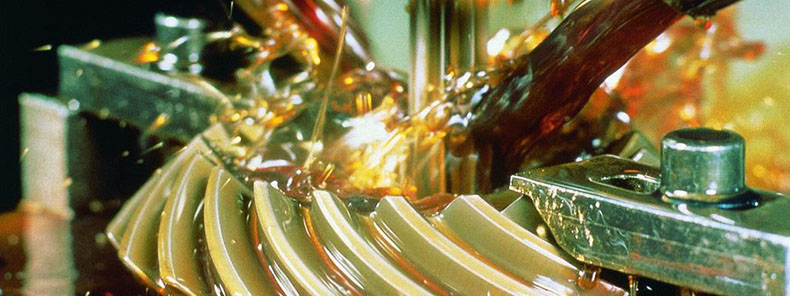
一、概述
金属加工是工程学的一个分支,是通过成型、机械加工、焊接、铸造、热处理等过程来制造零件、机器和构件。金属加工润滑剂是指用于金属切削、磨削、冲压、轧制和拉拔等各种加工过程的润滑剂,主要包括金属切削润滑剂(包括磨削)、塑性加工润滑剂(包括冲压、轧制、拉拔)、热处理和防锈油脂等。
20世纪90年代以来,我国的汽车、电子、机械加工等行业从国外引进的大型、先进机械设备越来越多,各种新型金属材料不断投人应用,金属加工工艺技术水平也得到提高,同时环境法规的要求日益苛刻,对金属加工润滑剂的质量要求越来越高,面临着一轮新的全面升级换代。
二、金属加工润滑剂分类
金属加工润滑剂的分类方法很多。根据其所应用的加工工艺类型,可分为金属成型、金属切削、金属防护和热处理等四大类,根据金属加工润滑剂的组成和介质状态可分为油基型(矿油型)和水基型,后者又可进一步分为乳化油(可溶性油)、微乳液(半合成液)、合成液。美国材料与试验协会按金属加工润滑剂的组成将其分为五类(ASTM D2881)。GB/T 7631.5《润滑剂、工业用油和有关产品(L类)的分类 第5部分 M组 金属加工》等效采用ISO 6743-7,将金属加工润滑剂分为润滑性为主(共8种产品)和冷却性为主两大类。
更多分类标准请参考润滑油分类标准汇总表。
三、金属加工润滑剂的应用
全球每年消耗金属加工润滑剂约213x 104t,其中北美约占28%、西欧约占23%、远东约占26%、其他地区约占23%。从产品品种分布看,金属铸造用润滑剂约占32%、交通设备加工的润滑剂约占25%、机加工约占16%,普通铁制品润滑剂次之,都是金属加工润滑剂用量较大的行业。亚太地区每年消耗金属加工润滑剂57x104t左右,随着越来越多的国外金属加工行业将其生产转移到中国大陆,对金属加工润滑剂的需求也越来越多,所占比例也越来越高,中国目前金属加工润滑剂需求大约为25x104t/a,其中切削加工所需润滑剂比例占38%、成型加工占36%、防锈油脂13%、热处理润滑剂占8%、其他金属加工润滑剂占5%左右;若按行业来看,金属制造所需润滑剂占30%、机加工和交通设备制造所需润滑剂各占20%左右。
四、金属加工润滑剂的作用及其性能要求
各种金属加工工艺不同,润滑剂所发挥的作用不同,其技术要求也各不相同,大多数金属加工润滑剂都要求包含控制摩擦、减少磨损,控制热量和金属表面保护等基本性能,近来安全环保和回收的要求不断提高。
- 控制摩擦:防止金属之间直接接触,能降低摩擦、减少能耗。
- 减少磨损:润滑剂帮助控制工件材料的磨损在允许范围内,同时要有效地减少刀具及模具磨损。
- 控制热量:热加工过程中控制加工工件热损失所造成的温度梯度;冷加工过程中均匀散热以避免工件过热。
- 可控的活性和稳定性:对模具、工件、机具不腐蚀或锈蚀,使用过程性能稳定,对压力、温度、污染物等因素不敏感。
- 金属表面保护:具有比较良好的润湿、扩散性能,保护并改善金属表面质量,提高光洁度及精度不影响后道工序:要求残留在工件表面的润滑剂尽量少,并且对喷漆、电镀、焊接、印刷等后道工艺无不良影响。
- 环保、安全及易于回收:要求金属加工润滑剂无毒、无害、对皮肤无刺激,废液易于处理。
综上所述,在金属加工过程中,金属加工润滑剂不是孤立的因素,应该将其当成整个润滑计划和系统工程的一部分,与工厂所有润滑剂和润滑装置组成了一个完整的摩擦学体系,才能更好地实现金属材料的加工。
四、主要金属加工工艺及其润滑剂
不同金属加工工艺的润滑剂,其质量要求各不相同,本节重点介绍轧制、冲压、切削、拉拔以及电火花加工等过程所需润滑剂及其发展趋势。
金属轧制及其润滑剂:轧制是在一定条件下旋转的轧辊给予轧件压力,使轧件产生塑性变形的一种加工形式。其中,在再结晶温度之上进行的轧制称为热轧,低于再结晶温度的轧制称为冷轧。轧制加工的材料可以是钢、铜、铝、锌及其合金,最终产品可以是棒材、角钢、管材、中厚板、薄板、箱材等。
冷轧是指金属在再结晶温度之下进行的轧制,其产品具有表面质量好、尺寸精度高、机械性能好、可以生产薄而小的轧件的优点;有利于生产组织性能要求高的产品,如硅钢板、汽车板凳。但冷轧时压力大,对设备的精度和强度要求高,能耗也大。冷轧工艺的润滑剂除应具备一般润滑剂的基本功能以外,特别要求润滑性能好、冷却能力强、性能稳定、使用方便、清净性强、防锈性能好等。
热轧是指金属在再结晶温度之上进行的轧制,主要目的是改善组织与性能、精确成型。热轧工艺的润滑主要采用深度精制的植物油和合成酯(也不排除矿物油),如棕榈油、菜籽油等,基本上是由Quaker,日本大同、D.A Stuart等专业公司生产并提供服务。一般热轧工艺要求润滑剂具有良好稳定的润滑性能、润湿性能、抗氧化性能和抗乳化性能,并且无毒,对人体没有危害等。
4.1 钢冷轧工艺及其润滑剂
在宽带钢冷轧加工过程中,轧辊、轧制工艺技术及轧制润滑剂是影响轧制钢板表面质量的三大因素。轧辊技术经过多年的发展已开发出多品种、多系列的光辊、毛辊技术,满足了工业生产的应用要求。冷轧工艺技术发展日新月异,从20世纪20年代美国成功地轧出宽带钢至今已有近90年的历史,由单机架单张钢板轧制工艺发展到酸洗一冷轧一连续退火的全连续化工艺;酸洗机组采用了湍流式酸洗工艺,克服了传统酸洗酸回收困难和钢材损耗大的缺点,冷轧机组除了现广泛采用的AGC(厚度自动控制)技术外,开发了中间辊可轴向移动的HC轧机、可连续变化轧辊凸度的CVC轧机、对辊交叉的PC轧机、轴向移动雪茄形工作辊的UPC轧机以及CVC-HC联合轧机等。
冷轧轧制油,随着冷轧工艺各项技术的进步而不断发展。早期使用的冷轧润滑剂是水。由于水的润滑能力有限,且存在严重的锈蚀问题,第二次世界大战前,冷轧厂开始用棕榈油等作为轧制润滑剂。由于棕榈油来源匮乏,导致了使用动植物油脂,如牛油和现在正在使用并称为“代用棕榈油”的大批其他有机材料的发展。油脂类及其他有机材料具有优异的润滑性能,提高了冷轧板的表面质量,但随着轧机的设计速度越来越高,在冷却方面存在着致命的缺陷,这又促进了乳化技术的发展。20世纪70年代初,被称为开发和利用“代用棕桐油”这种有机材料的时代,其油性组分是多轻基的酯,如由C12-C18的饱和、非饱和脂肪酸合成的酯类物质。随着冷轧技术的快速发展,其他合成有机材料也陆续应用到工业化生产上来,但是直到今天,冷轧轧制油仍没有统一的标准。
近年来,国外著名公司推出NUPD (New Uniform Particle Size Distribution), CPS(Control Particle Size)、UPD (Uniform Particle Size Distribution)等冷轧润滑剂技术,在轧制油组分不变的情况下,注重了对乳化体系、特别是颗粒尺寸的控制,形成所谓的新乳化体系。因为轧制油在应用过程中随着温度、高压喷嘴剪切、连续循环等因素的变化,影响乳化液中油粒粒径的分布,从而影响乳化液的离水展着性,严重影响轧制油的润滑性和轧机清净性。新乳化体系就是通过保证轧制油在应用过程中粒径分布始终保持在一定范围,从而保证了润滑性和清净性。
国内冷轧油研制始于20世纪70年代末,武钢从德国引进1700mm五机架连轧机时,试机采用轧制油为Quaker 88-183M。为此,国内由洛阳石化工程公司炼制研究所、武汉钢铁公司、石油化工科学研究院、武汉油脂化学厂等单位联合,一起开展了轧制油本地化攻关;80年代中期,带钢轧制变薄后又开发了具有较高皂化值的冷轧薄板轧制油;随着冷轧技术发展以及市场对冷轧薄板质量要求的提高,90年代中期,又开发了高清净性冷轧轧制油液。
4.2 铜铝带、板、箔轧制及其润滑剂
我国铜、铝轧制,曾经长期使用菜油、机械油等代替,轧制的成品在退火后表面发污发暗,甚至产生污斑,严重影响产品质量及销售。20世纪80年代以后,我国新建了一大批大、中、小型铜铝材箔厂,引进或自行建造了高速轧机。引进高速轧机配套使用的进口油能较好地满足高速轧机的铜铝带、板、简冷轧要求,达到光亮退火要求,但质优价高。近年,中国石油兰州润滑油研发中心、洛阳石化工程公司炼制研究所、上海石油商品应用研究所、空军油料研究所、广州机床研究所等单位均已成功研制出优质的铜铝带、板、箔轧制油,可用于高速铜铝材轧机。
虽然国内轧制油的研制工作只有20多年的时间,但经过研究人员的不断努力,国产冷轧轧制油的应用性能已经赶上国外同类冷轧轧制油水平,如中石油润滑油公司相继开发的不锈钢、铜、铝轧制用润滑剂。
4.3 金属冲压及其润滑剂
冲压加工属于金属塑性加工的一种,是通过模具对板料施加外力使之分离或产生塑性变形,从而获得一定几何尺寸、形状和性能的零件加工方法,通常称为板料冲压加工或板料成形加工。厚度小于4mm的板料冲压通常在常温下进行,所以又称为冷冲压,超过4mm的则多在加热后冲压,称为热冲压。
冲压加工适用范围很广,大到各类轧钢厂的不同材质(铝、不锈钢、合金钢甚至非金属材料等)、不同厚度板材的冲裁和冲压,小到人们日常生活用品,如各种饮料罐、洗衣机外壳、洗衣桶、热水瓶外壳、电视机彩色显像管零件、汽车挡泥板、车顶板、箱盖板等的制造。金属板材冲压成型加工涉及汽车、拖拉机、机械、电力、航空航天、仪器仪表、军工国防以及日用品等许多领域。目前,80%的汽车壳体,70%的高精密仪器仪表元件都是采用冲压成型加工制成。冲压件在形状和尺寸精度方面互换性好,可以满足一般的装配和使用要求,由于加工中冲压件经过塑性变形其内部晶粒细化,因此金属的内部组织得到改善,机械强度有所改善,使得冲压件具有重量轻、刚度好、精度高和外表光滑的特点;冲压加工生产效率极高,汽车覆盖件等大型冲压件可达每分钟数十件,高速冲压的小件则可达上千件;由于所用坏料多为板材或卷材,一般又是冷态加工,因而适于自动化、机械化生产,冲压加工的材料利用率高,一般可达70%~85%,冲压加工的基本工序可分为分离和成型两大类,分离是使坯料一部分与另一部分分离的工序如剪切、落料、冲孔等,成型是改变金属坯料的形状而不破裂的工序如弯曲、拉延和各种成型加工等。国外特别重视金属压力加工用润滑剂的研究,润滑剂种类不断增多,产品逐步形成系列化,但大多数执行企业标准。典型的有德国Wilnelm DIETZ的万能压延油、德国FUCH的ZW3036润滑剂、美国CASTROL的乳化型104冲压油和158冲压油,近年有逐步由公司转移或合并到大公司的迹象,许多大学及汽车公司也在进行研究。
冲压润滑油在冲压加工过程中起到非常重要的作用。20世纪80~90年代是国内冲压油品种、质量发展较为迅速的时期,国内引进了许多冲压设备以及模具,对冲压润滑剂的需求也较为急迫。例如,洛阳炼制研究所、上海石油商品应用研究所等单位相继开发了汽车行业用冲压油、彩色显像管零件冲压油、DI罐冲压油、浴缸成型冲压油等产品。由于冲压加工涉及领域、加工材料以及加工零件精度、尺寸大小、变形复杂度的不同,对冲压油的性能要求也各不相同,加上各地相继从国外引进了多条冲压加工生产线,目前国内已有的冲压油性能尚不能完全满足冲压加工工艺的技术要求。
金属冲压润滑剂的发展趋势是向具有更优异的极压性、抗磨性、清洗性方向发展。为简化工序、提高生产效率,需要油品低粘度化,为提高工件质量,需要提高油品的润滑性能。
不同材质板材对冲压油要求很不一致,如普通钢板(包括硅钢板、冷轧钢板、热轧钢板),以及镀锌钢板对冲压油防锈性能要求特别高,一般不使用防锈性差的氯系油,不锈钢板不易生锈,但容易产生划痕、擦伤,可使用氯系油,对铜以及铜合金板,则应严禁使用硫系油,硫容易使铜板变色,铝是两性金属、容易水解,对于铝以及铝合金板,不宜使用水溶性冲压油等。
五、金属切削加工及其润滑剂
金属切削是利用带刃口的切削工具(刀具或砂轮)在切削机床上将工件的多余金属切去,使工件获得规定的形状、尺寸和表面质量的工艺。按其所用切削工具的类型可以分为切削加工和磨削加工两大类:切削加工采用不同的刀具,进行车削、钻削、锭削、铣削、刨削和拉削等加工,而磨削加工采用不同的磨料和磨具,进行磨削、珩磨、研磨和超精等加工。
金属切削润滑剂是金属加工润滑剂中用量最大、影响面最广的一类油品,其总用量约占金属加工润滑剂的38%,国内每年用量约为10x104t,一般以水基为主约占3/4,油基约占1/4。
1860年前后,车、铣、刨、磨、齿轮加工和螺纹加工等各种机床相继出现,也标志着切削液较大规模应用的开始。19世纪80年代,美国科学家首先进行了切削液的评价工作,F.W.Taylor发现并阐明了使用泵供给碳酸钠水溶液可使切削速度提高30%~40%的现象和机理。针对当时使用的刀具材料是碳素工具钢,切削液的主要作用是冷却,故提出“冷却剂”一词,人们把切削液也称为冷却润滑液。随着人们对切削液认识水平的不断提高以及实践经验的不断丰富,发现在切削区域中注入油剂能获得良好的加工表面。最早,人们采用动植物油作为切削液,但动植物油易变质、使用周期短。20世纪初,人们开始从原油中提炼润滑油,并发明了各种性能优异的润滑添加剂。第一次世界大战后,开始研究和使用矿物油和动植物油合成的复合油。1924年,含硫、氯的切削油获得专利并应用于重切削、拉削、螺纹和齿轮加工。刀具材料的发展也推动了切削液的发展, 1898年发明了高速钢,使切削速度较前提高了2~4倍;1927年德国首先研制出硬质合金,切削速度比高速钢又提高2~5倍。随着切削速度提高,切削温度也不断提高,油基切削液的冷却性能已不能完全满足切削要求,这时人们又开始重新重视水基切削液的优点。1915年生产出水包油型乳化液,并于1920年成为优先选用的切削液用于重切削。1948年在美国研制出第一种无油合成切削液,并在石油价格高昂的20世纪70年代得到大量应用。近十几年来,由于切削技术的不断提高,先进切削机床的不断涌现,刀具、工件材料的发展和人们环境保护意识的加强,对切削液技术提出了新的要求。
- 环保型的绿色切削液:矿物油逐渐被生物降解性好的植物油和合成酯所代替;切削液不含对人体有害和对环境有污染的添加剂。
- 切削液的绿色使用:推广集中冷却润滑系统,即把机械加工设备各自独立的冷却润滑装置合并为一个冷却润滑系统,使切削液维护管理上水平;研究干切削和最小量润滑切削,以减少切削液的使用量,研究和推广使用切削液废液处理新工艺、新技术,以确保排放的废液对环境无污染。
- 低油雾、长寿命、多功能、浅颜色的切削润滑剂,可以满足越来越苛刻的环保法规要求,保证工人的身体健康。
金属切削加工存在着其特有的多样性、复杂性,国内各金属加工厂使用的润滑油也多种多样。另外,由于金属加工用油生产工艺简单、设备投资较少、参与竞争的专业润滑油公司少等原因,能调配金属切削润滑剂的中、小企业比比皆是,市场混乱,质量参差不齐,大多数切削润滑剂存在不同方面的质量缺陷,如润滑性能、渗透性能不好,不能满足极压抗磨需求,进而造成产品的光亮性差、刀具磨损严重甚至影响使用寿命,防锈、抗菌等第二性能差,产品毒性、刺激性大,严重危害金属加工工人的身体健康,产品废液不易处理或生物降解性差,不能满足环保法规的要求等。
六、电火花加工及其润滑剂
电火花加工是利用浸在工作液中的两极间脉冲放电时产生的电蚀作用蚀除导电材料的特种加工方法,又称为放电加工或电蚀加工(EDM)。
进行电火花加工时,工具电极和工件分别接脉冲电源的两极,并浸入工作液中,或将工作液充入放电间隙。通过间隙自动控制系统,控制工具电极向工件进给,当两电极间的间隙达到一定距离时,两电极上施加的脉冲电压将工作液击穿,产生火花放电。在放电的微细通道中瞬时集中大量的热能,温度可高达10000℃以上,压力也有急剧变化,从而使这一点工作表面局部微量的金属材料立刻熔化、气化,并爆炸式地飞溅到工作液中,迅速冷凝,形成固体的金属微粒,被工作液带走。这时在工件表面上便留下一个微小的凹坑痕迹,放电短暂停歇,两电极间工作液恢复绝缘状态。紧接着,下一个脉冲电压又在两电极相对接近的另一点处击穿,产生火花放电,重复上述过程。这样,虽然每个脉冲放电蚀除的金属量极少,但因每秒有10^6次脉冲放电作用,就能蚀除较多的金属,具有一定的效率。
按照工具电极的形式及其与工件之间相对运动的特征,可将电火花加工方式分为以下五类:
- 利用成型工具电极,相对工件作简单进给运动的电火花成形加工;
- 利用轴向移动的金属丝做工具电极,工件按所需形状和尺寸做轨迹运动,以切割导电材料的电火花线切割加工;
- 利用金属丝或成形导电磨轮作工具电极,进行小孔磨削或成形磨削的电火花磨削
- 用于加工螺纹环规、螺纹塞规,齿轮等的电火花共轭回转加工;
- 小孔加工、刻印、表面合金化、表面强化等其他种类的加工。
电火花加工主要用于加工具有复杂形状的型孔和型腔的模具及零件;加工各种硬、脆材料,如硬质合金和淬火钢等,加工深细孔、异形孔、深槽、窄缝和切割薄片等,加工各种成形刀具、样板和螺纹环规等工具和量具。
电火花加工油是电火花加工工艺使用的润滑介质,主要起到绝缘、冷却和排屑作用。电火花加工工艺初期,曾较多使用水做工作液,优点是冷却性好、不易着火,但绝缘性、抗腐蚀性和加工精度较差,因此近年来多使用矿物油、合成油作电火花加工油,之后使用煤油、锭子油、机械油等。随着电火花加工工艺的进步,对电火花加工油性能要求也越来越高,出现了矿油型电火花加工油,20世纪70年代曾经成为市场主流,我国改革开放以后,陆续从国外引进了许多高性能的电火花加工机床,由于矿物油型电火花加工油对人体有一定的刺激,影响工人的身体健康,就促进开发了新一代高性能电火花加工油——合成型电火花加工油。合成型电火花加工油是指正构烷烃、异构烷烃,颜色浅,对人体刺激小,由于其中不含催冷效果良好的芳烃,从而加工速度稍低于矿油型电火花加工油。
国外目前使用高速合成型电火花加工油,即在合成型电火花加工油基础上添加一些烯烃齐聚物、高聚物,以改善合成型电火花加工油的烟雾和冷却性能不足的缺点,如日本石油公司生产的ED电火花加工油、阿拉尔公司生产的FE和RP电火花加工油以及Mobil,BP等公司相关产品。
电火花加工油的发展趋势是开发具有良好绝缘性、电极清净性以及冷却性的高速合成型产品。
电火花加工油(放电加工油,电火花机油)由于高闪点、低粘度,能疏通放电通道,快速排渣,沉淀金属颗粒、炭粉,而且芳烃含量低、氧化安定性好,这样热稳定性更好、寿命长、使用价值高。
在闪点尽量高的前提下,电火花加工液的粘度要低。因为在电加工过程中,可放电的接触面距离是0.03~0.06mm,低粘度油的渗透性好、散热性好,电极与工件之间不易产生金属或石墨颗粒对工件表面的二次放电,这样既能提高表面的光洁度,又能相对防止电极积炭率,也是保证其热稳定性、氧化安定性的根本。
改进了操作工艺(加入混粉,如硅粉、铭粉等),粉末的特点是通过搅拌可使加工液更均匀、更稳定实施放电;使加工表面波纹减少,尤其适合大面积的塑料模具;大型石墨电极及筋条加工时,能均匀、稳定的高速放电;实施镜面电火花成型加工时,可使精加工时间缩短20% - 30%。
第二代电火花加工油(放电加工油,电火花机油)的使用寿命为两年左右,更换周期是两年一次。当电火花加工油(放电加工油,电火花机油)陈旧时,会使加工速度减缓,还要注意工作液的液压要调节合适。
对于铝合金、陶瓷采用放电加工有特殊的作用。由于铝合金、铅锡合金等材质易加工,但电蚀的碎末排渣困难,质轻且附着性好,要求电火花加工油(放电加工油,电火花机油)的粘度一定要小,这样在电加工过程中,不易产生二次放电。
在碳化硅、氧化物、砌化告等高强度陶瓷的放电加工中,使用电晶体脉冲(动)的方式来刻模放电加工,并要求在优质电火花加(放电加工油,电火花机油)中进行,其施与电压在100V以下,电极材料则用纯铜。
七、金属拉拔及其润滑剂
金属拉拔是通过模具孔缩小加工材料截面积,获得高精度、高光泽度的线材和管材的种塑性加工工艺。它广泛应用于加工碳钢、不锈钢、铜、铝及其合金等各种金属,可生产直径大至数十毫米的棒材、管材,小至数微米的计算机导线等数千种不同规格、用途的产品,比较重要的是铜管拉拔.
拉拔方式主要有传统的直线拉伸工艺与先进的圆盘拉伸工艺,与直线拉伸工艺相比,圆盘拉伸工艺的优点主要有拉料长、速度高(最高达1200m/min)的特点,因此对润滑剂的要求也很高。为满足国内外空调铜管市场不断增长的需求,国内多家企业相继引进了高速铜管拉伸生产线,要获得高的生产率,并生产出合格的产品,必须有高品质、多功能的工艺润滑油与强化的金属材料加工过程相适应。
铜管拉拔润滑剂主要分为铜管拉拔外模油和铜管拉拔内模油,其中外模油主要为拉拔铜管外壁用油,起到的润滑、冷却、防护等作用;内模油用于拉拔铜管内壁与移动芯头之间挤压时的润滑以防止卡塞和粘结。由于铜管的特殊性能,国标标准一般都要求“表面清洁光亮,不应有影响使用的有害缺陷”。所以对铜管拉拔内外模油的主要要求是具有良好的润滑性能和良好的退火清净性。由于使用工况的不同,外模油除了有良好的润滑性能和退火清净性之外,还应有适当的冷却作用,以及时移走拉拔过程中产生的热量。外模油在使用过程中通过循环油路来实现润滑、冷却、防护等目的。拉拔内壁主要是移动芯头和铜管内壁之间的摩擦,一般是在拉拔前人工加人一定量的润滑剂,所以要求内模油的粘度要大,以保证加工过程中的润滑,一般内模油40℃运动粘度在130~ 4000mm2/s 之间,以适应不同工况条件的需求,内模油的主要作用为润滑与防护。无论内外模油都须在拉拔完成后经500~ 650℃退火后拉拔油必须全部挥发(热脱脂)。
目前市售的铜管拉拔外模油主要有矿物油型、乳化液型及合成油型等。其中矿物油型相对价廉,但退火清净性较差;乳液型拉拔液也相对低廉,但容易产生霉变进而影响使用寿命,并且废液处理较难;合成油型拉拔油主要为酯类油,具有良好的退火清净性,但价格较贵。
丙烯酸酯类(ACR)管拉拔外模油在国内外一直没有统一标准,铜管拉拔时对润滑剂的要求比较严格,既要保证较高的油膜强度和一定的运动粘度,良好的铜片防腐蚀性,又要保证退火后较少的残留量,最重要的是在退火时能够汽化,并在一定温度下裂解,裂解后残碳量低,选用的润滑剂必须符合要求,以保证拉拔后的铜管表面光洁度高。我国目前冷凝管生产企业使用的拉伸润滑剂,大多属于经验配方型,有的是直接沿用其他加工方式用的润滑剂。这类润滑剂品质水平较低,缺乏良好的综合性能,尤其是对于ACR管退火后的高清洁度难以达到要求,难以满足铜管拉伸过程的全面要求,不能充分发挥先进设备的生产能力,进口润滑油价格昂贵,造成生产成本高。
八、金属热处理及其润滑剂
金属热处理是将金属工件在一定的介质中加热到适宜的温度,并在此温度中保持一定时间后,又以不同速度冷却的一种工艺。金属热处理是机械制造中的重要工艺之一,与其他加工工艺相比,热处理一般不改变工件的形状和整体的化学成分,而是通过改变工件内部的显微组织,或改变工件表面的化学成分,赋予或改善工件的使用性能。详见《 热处理油》一文。
九、金属加工润滑剂的分析评定与管理
在金属加工润滑剂开发过程中,要利用相关的理化分析、模拟评定以及现场试验等方法进行润滑剂的研发,为了合理用油、节约用油、保证设备正常运转,提高所加工产品的质量,通常要在使用前对金属加工润滑剂进行系统分析评价,在金属加工润滑剂使用过程中,也要不断的运用各种理化分析、模拟评定等方法对产品质量进行监测,定期的抽样检查。
9.1 金属加工润滑剂的分析评定
金属加工润滑剂特性差别很大,同一类产品也有很多不同的特性,再加上金属加工润滑剂没有统一的质量标准与评定试验方法,分析评定又有水基、油基区分,性能描述又有理化与使用两个方面,因此差别很大。
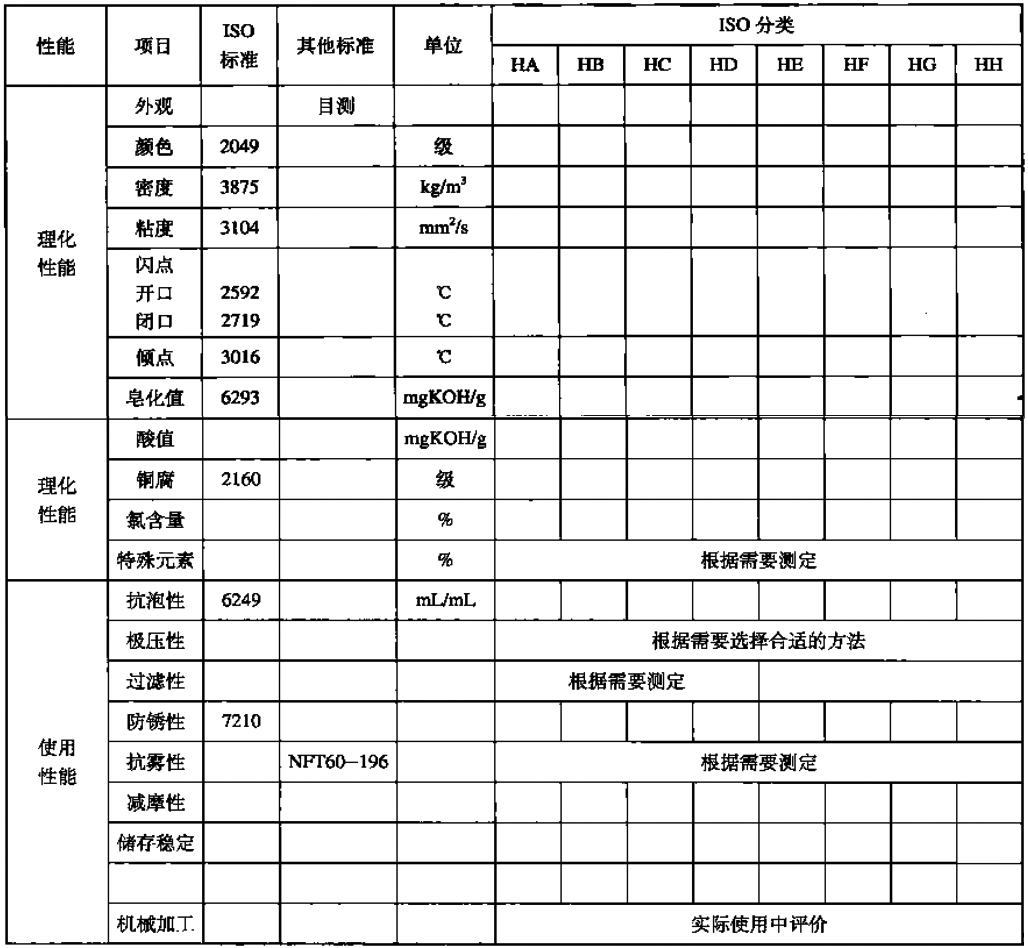
油基金属加工润滑剂常用分析评定
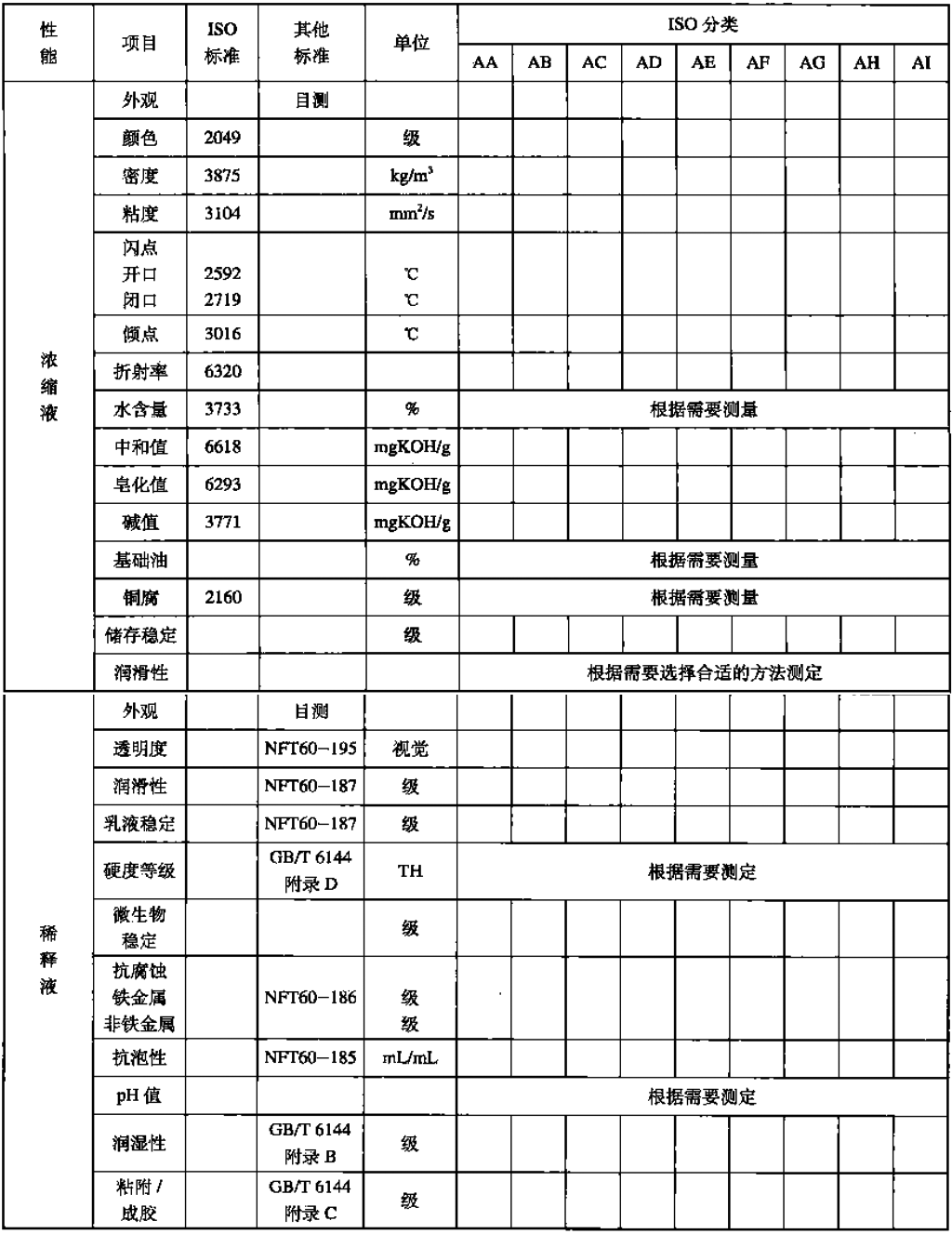
水基金属加工润滑剂常用分析评定项目
十、金属加工润滑剂管理
为了发挥金属加工润滑剂的最佳使用效果,除应熟悉金属加工润滑剂性能、特点、选用知识外,还必须要掌握金属加工润滑剂的管理知识。这对于延长其使用寿命、提高经济效益,乃至满足工艺要求是不可或缺的。
10.1 金属加工润滑剂保管
金属加工润滑剂管理的第一步就是产品的接收与保管,在储存过程中金属加工润滑剂变质的主要原因是容器损坏、湿气凝结、不当室外贮存以及不当的混兑等。
工业上常用200L大桶装金属加工润滑剂,卸车时要避免油桶损坏或工人受到伤害,存放金属加工润滑剂理想的地方是室内,油桶不应当放到蒸汽或者其他加热器附近,也可以分层码放,按先后购入顺序使用以避免油质变坏;如无条件要存放室外,则应采取适当的措施将不良后果降至最低,如避免存放时间过长、避免日晒雨淋、油桶摆放顺序应两个桶塞水平、桶下垫支架或木条;还要注意,镀锌桶不适宜储存金属加工润滑剂,因为其所含添加剂可能与锌产生化学反应,产生於渣严重污染润滑剂;水基润滑剂凝点一般-5℃左右,寒冷地区注意防止冻结,因为可能导致分层而影响使用效果,金属加工润滑剂大多是可燃物质,运输、储存、使用过程中注意防火。
10.2 油基金属加工润滑剂
使用管理与水基金属加工润滑剂相比,油基产品相对劣化缓慢,只要按时补充新油即可长期使用,但也不能忽略管理。特别在更新时,一定要预先清理油路,除去油渣和碎屑。在实际使用过程中,要注意以下几点:
(1)防止混入水而导致润滑性、防锈性等性能的下降。混人水可能是天气原因、使用不当或者上道工序使用水基产品等多种原因。若已经进人水,少量的可采用加热或活性白土过滤方法除去,若进入量较大则要更换新油或者由专业厂家处理,以免造成生产事故。
(2)由于其他品种润滑油漏入导致金属加工润滑剂稀释、各种性能下降。这种情况在实际使用过程中要加以防范,因为漏入的产品与金属加工润滑剂难以分辨,但粘度、添加剂组成大相径庭,会导致金属加工润滑剂产品的性能发生很大变化,从而导致生产出现严重问题。
(3)由于碎屑、淤渣堆积导致金属加工润滑剂质量劣化。罐底、容器底部如果堆积过多的碎屑、淤渣将会促进质量劣化,导致粘度上升以及产生胶状物质,尤其在切削加工过程中更应引起注意,必须采取过滤或者磁吸附等措施。
10.3 水基金属加工润滑剂使用
管理与油基金属加工润滑剂相比,水基产品变质较快,给管理带来一定麻烦。水基产品经水稀释后使用,前者称浓缩液,后者称稀释液(工作液),其使用状态是呈胶态状的分散体系,而不是像油基产品的均一体系。从动力学来讲,本身就是不稳定体系,如果有异物混人或者给予一定的化学、物理能量,则稳定性更差,必然改变了实际使用性能发挥。
在金属加工过程中,使用水基润滑剂的加工方式很多,集中在切削加工和轧制加工中,少量在线切割、冲压、拉拔等加工工艺中。就其用量而言,切削、轧制加工用量最大。不同金属加工所使用的水基润滑剂也不尽相同,在管理上既有共性又有特殊性。水基金属加工润滑剂产品多以浓缩液形式出售,使用时应用满足要求的水稀释。浓缩液管理与油基产品基本相同,含水的浓缩液随着水含量的增高则趋于稀释液,而稀释液管理是一个系统的工程。
1)浓度的控制
水基稀释液允许在一定浓度内使用,若浓度过高,增加使用成本,而且一旦混人漏油容易形成凝胶状物质难以过滤;相反,浓度过低,则会发生工具寿命短、加工工件精度不良、防锈性下降产生腐蚀、稀释液腐蚀等问题,所以要准确控制稀释液的浓度。可以采取控制油罐容量、每日消耗量,采用自动稀释装置、定期测量浓度等办法。正确地控制使用液的浓度,不仅可以防止工具损坏事故,还可以延长稀释液使用寿命。稀释液在使用中应注意以下几点:
(1)使用中要经常清除乳液槽表面漂浮的油层及脏物,乳液通道、收集槽、过滤器要经常清理,根据乳液使用情况更换或者补加新液。
(2)工件前道工序的残留物要清洗干净,并使表面干燥以免影响乳化液的性能。
(3)要注意乳液配制的顺序,必须将浓缩液倒人水中,还应考虑使用水的质量,如混浊程度、酸碱离子等对乳液质量的影响,使用中对乳液质量也要随时监测与控制。
2)防锈的管理
水基产品稀释后使用,对设备、工具、工件的腐蚀与油基状况不同,如果稀释液中含有大量的磷酸根、氯离子、硫酸根等杂质,则稀释液的润滑性、防锈性会急剧下降。如果工件停留时间较长、气候变化产生了容易腐蚀的环境,则要对工具采取防锈处理。
3)防腐蚀的管理
稀释液含有大量的水分以及容易产生细菌、真菌等微生物生存的营养物质,很容易腐蚀变质,产生酸臭味、液体变成灰褐色、pH值急剧下降、防锈性急剧下降、乳化液分层、加工性能下降、严重缩短使用寿命等恶果。
要阻止微生物繁殖很困难,但可以采取有力措施加以抑制。更换新液之前,完全清除给油系统内的金属屑和异物,采用杀菌剂进行充分灭菌处理后再装人新液,尽量采用软水配制乳化液,避免使用无机盐含量多的水,及时补充新液,维持在一个规定的浓度范围内,过低会造成润滑性、防锈性下降导致工件精度不够以及工具损害,过高增加成本、消泡性下降以及加大对皮肤的刺激等,保持稀释液pH值在9左右,如果设备长时间不用,则应该定期向乳液罐鼓风或者让稀释液打循环,以防止细菌滋生;防止漏油混入稀释液,一旦进入要迅速清除,设置高效除屑装置,防止碎屑在罐内堆积;定期加入杀菌剂,如有腐蚀迹象则加大剂量。
10.4 金属加工润滑剂毒性
长期接触金属加工润滑剂,尤其切削润滑剂可能会引起皮肤病,如接触性皮炎、毛囊炎、肿瘤等。这是因为稀释液是碱性物质可以造成皮肤脱脂或者使用溶剂清洗时造成脱脂,油性组分会堵塞汗毛孔引起发炎、稠环芳烃引起皮肤角质层鳞状化等等。在实际使用金属加工润滑的过程中要注意以下几点:
- 衣服要清洁,上班戴护臂以及围裙;
- 开始工作前、饭前、离开车间前用碱性不大的洗涤剂洗手,并涂抹油性护肤膏以保持一定油性;
- 勿用汽油等有机溶剂洗手;
- 稀释液定期检测。
10.5 金属加工润滑剂废液处理
金属加工润滑剂在使用过程中性能逐渐劣化,加工性能下降甚至产生臭味,说明使用寿命已到期,应该更换新液。油基产品处理与平常润滑油类似,水基产品则不同。
水基金属加工润滑剂主题是水,但因为腐蚀不允许直接排入水体,需经处理达到国家排放标准后才可以排放。水基润滑剂是含油污水中难处理的一种,因为其中含有大量的表面活性剂等,可以采用物理处理、化学处理和生物处理、燃烧处理等方法进行。
物理处理是利用废液中的悬浮物质与水的密度不同的原理,进行沉降或者离心分离等办法除去。
化学处理是针对物理方法不能处理的废液,可以采用加入无机絮凝剂、有机絮凝剂加速粒子沉积;氧化剂或电解;活性炭吸附、离子交换树脂吸附等。
生物处理采用活性污泥法将废液中有害物质分解掉。
燃烧处理采用直接燃烧或者蒸发、燃烧方法处理。
更多信息请参考《润滑油脂及其添加剂》一书。