1、适用范围
本方案适用于大型压缩机组、大型烟机机组等石化大型机组的润滑油系统油路的油运主动性维护。
2、编制依据
- API 614《石油、化工和气体工业用润滑、轴密封和控制油系统及辅助设备》
- SH 3501《石油化工有毒、可燃介质管道工程施工及验收规范》
- ASTM D6439《蒸汽、气体和水电涡轮润滑系统的清洗、冲洗和净化标准指南》
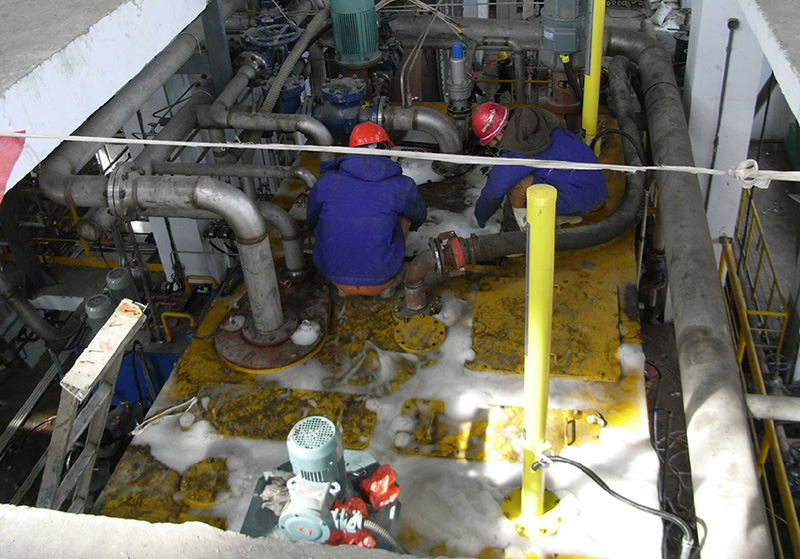
3、施工准备
3.1、技术准备
3.1.1 人员准备
参加施工的人员必须具有相关作业的资格证书,对参加作业人员进行技术方案交底,施工人员充分熟悉现场及施工图纸、熟悉每道工序内容、工作要点、问题处理方法及报检流程。
3.1.2 资料准备
- 1)设计文件,包括机组平面布置图、安装图及相关专业的施工图齐全;
- 2)具备有关的施工规范及经建设/监理单位确认的施工技术文件;
- 3)必须有制造厂技术文件,包括材料质量证明文件、制造、装配等质量检查记录、试验报告及使用说明书。
3.2、施工材料和机具
安装需要的主要施工材料包括:乙烯密封带、棉布、海绵、塑料桶、精面粉、不锈钢网纹塑胶管、塑胶管、耐酸石棉板、钢板、焊条、无缝钢管、法兰、阀门、压力表、过滤网、砂纸、不锈钢丝网、耐酸手套、口罩、防风眼镜等;b)主要工机具:滤油机、手动葫芦、千斤顶、机油枪、紫铜棒、手锤、撬棍、呆扳手、梅花扳手、螺丝刀(一字、十字)等。
用于油路油运的钢管、钢板、法兰,螺栓、垫片,阀门各种型钢等临时材料,均应具有制造厂提供的质量证明书,其质量不得低于国家现行标准的规定,并经外观检合格。
3.2、作业条件确认
- (1)施工场地平整,达到“四通一平”,施工用水、电、气达到使用条件;
- (2)试运行现场具备可靠的照明、通信和消防设施,消防通道畅通;
- (3)设备的施工场地的与其它正在施工的系统有可靠的隔离或隔绝;
- (4)有工具及施工材料等存放场地,有相应的防风、防雨、防冻等防护措施;
- (5)对不参与系统油运设备、仪表组成件,特殊管道组成件等隔离、拆除、保护工作完;
- (6)管道系统中的弹簧支架、膨胀节等,油运前应检查确认其锁定牢固可靠。
- (7)所有管线应按流程图编号,在所有配对法兰处按编号打对应钢印;如无钢字模具,也可使用不掉色的记号笔或其他器具做编号,当使用记号笔做编号时应确保在使用浸泡式化学清洗过程中也不会脱落。
- (8)对截止阀、调节阀、单向阀等有方向要求的阀门必须标示安装方向。
- (9)对温控阀的每一个配对法兰处做方向标示。
- (10)对过滤器和油冷器的切换阀做阀位标示。
- (11)对与轴承箱等相连等的钳工拆卸的管线也应做永久性位置标示。
- (12)确认各电加热器停用并断电。
- (13)系统润滑油倒空,并从各导淋处确认,必要时可用空气吹扫。
- (14)安排合适的清洁场地,应具有临时电源、清洁水、蒸汽、工厂风等资源,满足管线分类堆放场地,冬季必须设置在采暖厂房内,环境温度不小于10℃。
- (15)准备管线的封口材料,如干净的白棉布或加厚的塑料布等,确保清洁后的管线在运输和回装过程中不被污染。
4、设备、管线拆除及清洗
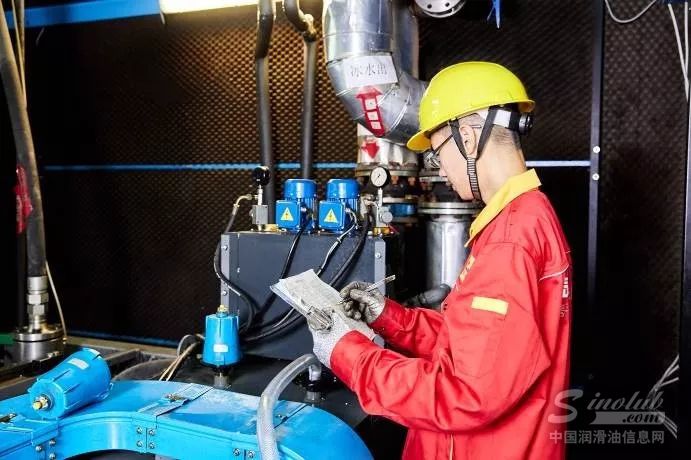
- 4.1将系统管线、设备拆除并运送至清洁场地,清洁前尽量将管线拆分成较短的单元,避免清洁时高压水枪枪头或蒸汽无法达到预期部位,造成部分管道清理不干净。对每个拆卸管线、管件做好记录。
- 4.2对拆卸下来的管线、阀门和设备部件用蒸汽吹扫脱脂,在确认安全的情况下优先使用中压蒸汽脱除附着在管道、设备内壁的粘性油脂。管道外壁增加简易保温措施可以缩短吹扫时间,以蒸汽出口管道内壁不再残留粘性油脂为合格标准,可用干净的白纸或白棉布测试,标准为肉眼不可见油渍。注意温控阀等不耐高温的元件不能使用蒸汽吹扫,应解体后用棉布和溶剂清洁。注意各支线、导淋必须逐个吹扫。
- 4.3脱脂完成后,对于不锈钢管线可采用高压水射流对管线和设备内壁附着物进行清洗,清洗过程中阶段敲击清洗的管道和设备,以便得到更好的清洗效果。对于碳钢管线,如管内壁有锈蚀,则应先采用化学清洗的方式进行除锈清洁,化学清洗钝化完成后再使用高压水清洗。清洗完毕后,须对管线内壁进行检查,标准为肉眼不可见颗粒。注意各支线、导淋也必须逐个清洗确认。
- 4.4高压水清洗完毕后,应采用清洁的热空气对管线和设备进行干燥,以脱除残留在管道、设备内壁的液态水。如无热空气,则先使用蒸汽吹扫加热管线,然后迅速用干净空气吹扫。
- 4.5热空气干燥时要翻滚管道和设备,避免水在低点集聚,每一个支线和导淋都应吹扫干净。干燥完成后须逐点确认,可使用干净的吸潮纸在出口处检查,标准为纸不潮湿和无肉眼可见的湿点。
- 4.6干燥完的管线、部件须马上使用白棉布或加厚塑料布封口,封口须牢靠,防止运输和搬运期间破损。如发现在回装前封口破损,则必须重新清洁。
- 4.7油箱、油气分离器等能进人的设备清理。打开后充分置换待内部可燃气体检测合格后人员进入清理,先用海面等吸油能力强的材料清除残油,再用棉布把金属表面清理干净,最后用面团将金属表面、死角逐一清理干净,验收标准为面团肉眼不可见污染物或变色。最后一次清理和检查需注意进入人员应穿干净的一次性连体服,防止污染。
- 4.8不能进人的设备,如高位油槽等,应先检查内部清洁度,如内表面干净无肉眼可见杂质,则倒空残油后立即将各管口封闭,防外物污染。如内部不干净则可采用管线的清洁方式进行彻底清洁,必要时可拆下,移至工房清洁。
- 4.9无法拆卸的管线须安照管线清洁的步骤进行在线清洁。应特别注意在线清洁过程中的低点、死角的处理,须花费更长的时间处理。
- 4.10换热器应抽芯处理并按上述的处理方式逐一清洁,并应对管束进行水压强度测试和气体检漏测试。
- 4.11油冷器和润滑油过滤器的换向阀应进行压力试漏,应对两个不同的位置方向测试内漏和外漏,要确保阀门回装后在两个位置均不发生内漏。如试漏不合格,则应更换密封件。
- 4.12调节阀、自励阀清洁完毕后应进行行程测试;安全阀清洁完毕后应校验合格;系统内阀门清洁完毕后应进行严密性试验合格;视镜、呼吸阀、仪表引压线根阀等也应清洁干净,必要时可更换新的。
- 4.13压缩机本体的润滑油通道应要求维修人员用白棉布和清洗剂清洗干净。
- 4.14如必要,则应同步对润滑油泵解体检修。最低要求为确认润滑油泵转子表面干净,肉眼不可见异常杂物。
- 4.15压缩机轴承箱扣盖之前,应用面团和吸尘器将轴承箱内部清洁干净后再合盖。
- 4.16长期存储的设备必须将轴承箱打开进行彻底的清洁,包括电机的轴瓦。
- 4.17油运时跨接压缩机和汽轮机应优先选用夹钢丝的内壁光滑的透明塑料软管,并提前将管内清理干净,必要时可提前用润滑油油运干净。
- 4.18新配制的管线,应按原始施工要求进行清洁处理。
- 所有的验收环节均应做纪录。
5、设备、管线回装
- 5.1按法兰标记顺序回装管线和管路元件,所有管线和管件在回装前才能拆除封口。如当天不能完成全部回装,则应将敞口部位再次封口,以防止杂物进入管线。
- 5.2润滑油过滤器和润滑油冷却器的三通换向阀回装时应进行两个位置和方向确认。
- 5.3润滑油温控阀回装时应确认介质流向正确。
- 5.4单向阀、截止阀、调节阀等有方向要求的阀回装时应逐一确认。
- 5.5主油箱、油气分离器、油冷器高位油槽等设备封闭,蓄能器充压确认。
- 5.6润滑油过滤器滤芯更换新滤芯。
- 5.7临时油运线连接完毕并确认牢固,隔离盲板安装就位。
- 5.8所有法兰连接紧固后应对所有垫片的安装进行检查并使用力矩扳手逐一确认。
6、系统气密检查
- 6.1将各回油管线呼吸阀拆除,用盲板或管帽隔离。
- 6.2系统放空阀、倒淋阀关闭。
- 6.3润滑油气相放空线盲板隔离。
- 6.4通过倒淋接清洁过的胶管将清洁空气补入系统,系统缓慢充压,充压过程中人员巡回检查是否有明显泄漏点。
- 6.5系统充压至操作压力,关闭空气补入阀,观察系统压力下降速度,同时人员巡回检查用气密瓶检查漏点。验收指标为2小时压力降不大于5%。
- 6.6如需对油箱进行试漏,则应制定专项方案。
- 系统无法建立气密的密封面应建立台账,油运时须重点检查。
7、系统注油和油运
- 7.1系统注入新油,油箱注入70%液位时可投用电加热器。如当日不启动润滑油泵,则需要专人监控润滑油箱的油温并做纪录,高于40℃则应停用电加热并断电。
- 7.2在油箱回油总管加装100目滤网(0.1mm的钢丝,刚开油运时可使用临时锥型过滤器,流通面积大,避免回油不畅或高点跑油。如不能加装锥形过滤器则必须控制润滑油流量),润滑油、控制油、密封油各注入点加100目滤网(可以判断具体每个支路的清洁程度)。
- 7.3油温达到启动油泵的条件后,启动润滑油泵。
- 7.4油运应逐个系统进行,先油泵小循环运行,再分单元逐个系统投用。在回油管与油站油箱接口处加150目滤网。待油循环2~3天,滤网上无大颗粒杂质时,将滤网换成180或200目。滤网无明显杂质时,将进油管复位,在各进油管与机组本体接口处加180或200目滤网。
- 7.5在油冲洗的过程中,按油的流向用木锤沿管道敲击各焊缝、弯头、三通,并定期排放或清理油路的死角和最低处积存的污物。
- 7.6油运投用时应缓慢投用,确认各密封点无泄漏后再逐步升压提量。在各系统投用时应确认不溢出,密切观察各回油视镜和回油管呼吸阀,满管但不溢出。
- 7.7油运应有足够的流通量,尽可能采用高流量油运,特别是回油总管的管顶,必要时可调节润滑油供油压力,但要防止高点溢出。
- 7.8油运应包括所有管线,如安全阀旁通、油箱的回油线等,并做好纪录。
- 7.9油运期间应对各压力调节阀和自立阀进行调校,对润滑油泵仪/电自起逻辑进行测试。
- 7.10油运期间应对各备用设备进行测试,包括备用油泵在线切换、两台润滑油过滤器多次在线切换和更换滤芯、两台油冷器多次切换等,确认备用设备完好备用,三通切换阀完好不内漏,并做好纪录。
- 7.11油系统大循环油运后,每隔1小时检查一次临时过滤器确认油运情况,直至合格。合格标准为100目滤网每平方厘米肉眼可见的颗粒物不超过1个。
- 7.12投用密封油时应确保密封隔离气投用正常,否则密封油系统不允许进压缩机,避免润滑油泄漏至压缩机内部及进出口管线。
- 7.13全系统油运时每1小时检查一次滤网(包括回油总线和各注入点),直至两次检查均合格。合格标准为100目滤网每平方厘米肉眼可见的颗粒物不超过1个(垫片挤出的石墨不要算,主要看尘杂),颗粒的最大尺寸不应超过0.25毫米。润滑油入口处加设200目滤网,通油4h后,每平方厘米可见软杂质颗粒不超过两点,不得有任何硬质颗粒,允许有少量纤维体。
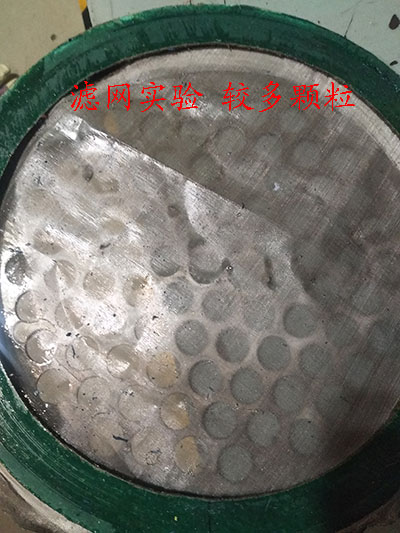
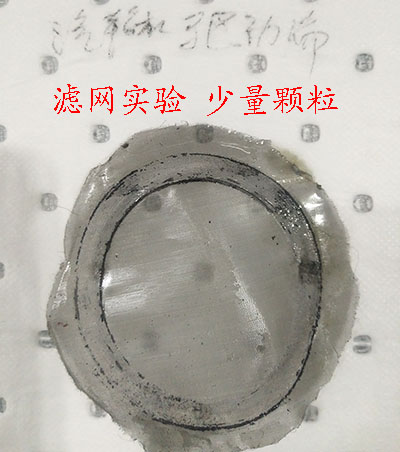
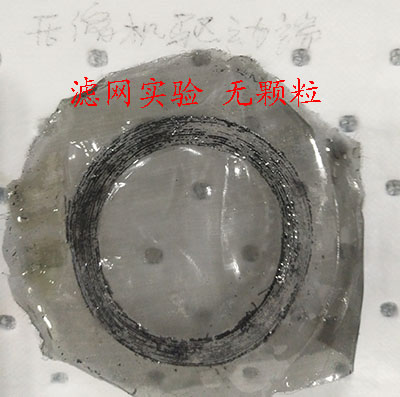
- 7.14润滑油油运首次合格后,对润滑油取样分析,除了常规样外还应根据API 614《石油、石化和气体工业用润滑、轴密封和控制油系统及辅助设备》的要求做润滑油的污染度分析。除常规理化指标合格外,要求润滑油污染度等级不大于ISO -/17/14的等级要求。
- 7.15高位油箱底部容易残留杂质,开始时需频繁停泵,使高位油箱的油流下,带出杂质。
- 7.16油冲洗时,应满足下列各项要求:
- (1)油循环必须用压缩机厂家规定的润滑油。
- (2)油箱在加入润滑油前已作检查,内部没有任何肉眼可见的污物;
- (3)所有管路都要经过清洗。
- (4)事先对制造厂带的油管线、阀门、设备要抽检。
- (5)系统油循环检验合格后,拆除临时设施,装好流量、温度、压力等检测部件。并将各轴瓦拆出,检查是否有杂质,清洗后回装。
8、质量保证措施
- 8.1设备管口必须及时封闭,定期检查封闭好的敞口部位,保证其封闭完好。
- 8.2已油运合格的管道系统,不应再进行切割,开孔等修改作业,必须进行修改作业时,可采用机械切割或开孔等方法,切口部位管内部清理干净,并用氩弧焊进行封底焊,否则应重新按要求对管道系统进行局部分段吹洗油运。
- 8.3吹洗合格封闭的管道系统,未经许可不得拆开,防止二次污染。
- 8.4管道系统油冲洗时,防止死角(如:局部低点,高点,管道附件内部等)部位冲洗不净,应在这些部位加设排放点或拆开冲洗,保证冲洗质量。
- 8.5管道系统冲洗前,加置的盲板,拆除的管道组成件及仪表等应做好记录,确保冲洗合格后,管道系统复位准确无误。
9、安全要求
- 9.1所有进入现场的员工应按规定穿戴公司统一发放的工作服、安全帽、工作鞋等个人防护用品。
- 9.2施工现场的危险部位应设置安全警示牌,设置警戒绳并配置灭火器,严防明火,周围禁止电气焊施工。
- 9.3在油箱上配临时管时应在远离油箱处预制好后再进行安装。
- 9.4油箱内照明必须使用安全电源或用手电筒照明禁止使用太阳灯。
- 9.5油系统冲洗时法兰口有滴油时要及时处理以免引起火灾。
- 9.6对施工用过的手套、油棉纱等废弃物应与其他废弃物品放入现场的垃圾桶内,集中处理。
- 9.7油箱加油时,使用合适的漏斗进行操作,避免油外漏,若有漏油,将事先准备的锯沫覆盖在上面吸入一段时间,再进行清扫。
- 9.8对润滑残渣不得随处乱扔,应在完工后收集清理,每天要保持工作场地清洁卫生,做到文明施工,保障施工的安全。
预览与下载
文档类型:word
下载地址:登录后显示。