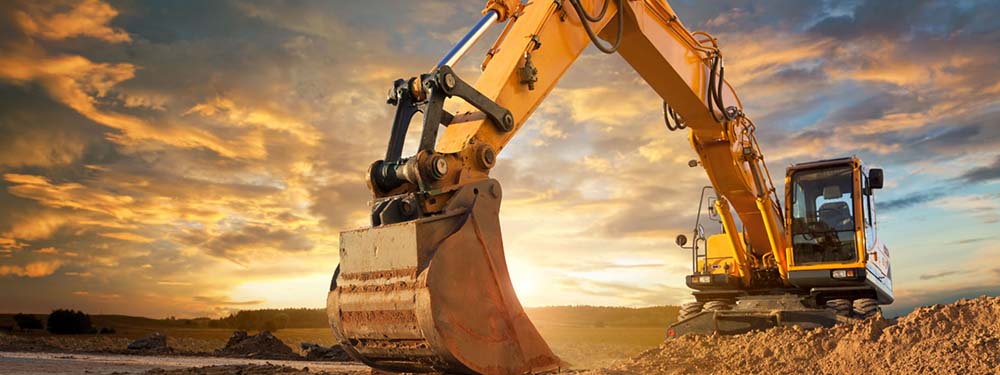
一、液压系统温升过高的原因及防治
在一般液压系统中,液压介质的正常工作温度为40~60℃。如果液压油温升过高,可使机械产生热变形,液压元件中热胀系数不同的运动部件因其配合间隙变小而卡死,引起动作失灵、影响液压系统的传动精度,导致部件工作质量变差。此外,还可使油的黏度降低,泄漏增加,泵的容积效率和整个系统的效率会显著降低。由于油的黏度降低,滑阀等移动部件的油膜变薄和被切破,摩擦阻力会增大,导致磨损加剧。油温过高使橡胶密封件变形,加速老化失效,降低密封性能及使用寿命,造成泄漏。高油温还会加速油液氧化变质,并析出沥青物质,降低液压油的使用寿命。析出物堵塞阻尼小孔和缝隙式阀口,导致压力阀卡死而不能动作。
1.1 温升过高的原因
- 油箱容积太小,散热面积不够,未安装油冷却装置,或虽有冷却装置但其容量过小。
- 按快进速度选择油泵容量的定量泵供油系统,在工作时会有大部分多余的流量在高压下从溢流阀溢回而发热。
- 系统中卸荷回路出现故障或因未设置卸荷回路,停止工作时油泵不能卸荷,泵的全部流量在高压下溢流,产生溢流损失而发热,导致温升。
- 系统管路过细过长,弯曲过多,局部压力损失和沿程压力损失大。
- 元件精度不够及装配质量差,相对运动间的机械摩擦损失大。
- 配合件的配合间隙太小,或使用磨损后导致间隙过大,内、外泄漏量大,造成容积损失大,如泵的容积效率降低,温升快。
- 液压系统工作压力调整得比实际需要高很多。有时是因密封过紧,或因密封件损坏、泄漏增大而不得不调高压力才能工作。
- 气候及作业环境温度高,致使油温升高。选择油液的黏度不当,黏度大黏性阻力大,黏度太小则泄漏增大,两种情况均能造成发热温升。
1.2 温升过高的原因
- 根据不同的负载要求,经常检查、调整溢流阀的压力,使之恰到好处。
- 合理选择液压油,特别是油液黏度,在条件允许的情况下,尽量采用低一点的黏度以减少黏度摩擦损失。
- 改善运动件的润滑条件,以减少摩擦损失,有利于降低工作负荷、减少发热。
- 提高液压元件和液压系统的装配质量与自身精度,严格控制配合件的配合间隙和改善润滑条件。采用摩擦系数小的密封材料和改进密封结构,尽可能降低液压缸的启动力,以降低机械摩擦损失所产生的热量。
- 必要时增设或加强冷却能力。
二、EH系统中电液伺服阀常见问题及对策
- EH系统普遍采用磷酸酯抗燃油。在使用过程极易劣化,主要表现为污染颗粒度的增加和酸值升高。伺服阀是一种很精密的元件,对油质污染颗粒度的要求很严,一般要达到NAS 5级,酸值应小于0.2mgKOH/g。抗燃油污染颗粒度增加,易造成伺服阀卡涩,同时,使阀芯磨损,泄漏增加。酸值的升高,对伺服阀部件产生腐蚀作用,特别是对伺服阀阀芯及阀套锐边的腐蚀,这是使伺服阀泄漏增加的主要原因。
- 有些电厂伺服阀的密封件腐蚀、老化现象严重,有的甚至变形、掉渣,引起伺服阀泄漏。由于使用了与伺服阀密封件不相容的油液,不仅使伺服阀密封件腐蚀、老化,影响其使用寿命,而且残留伺服阀中的油液将污染系统的抗燃液,加速抗燃液的劣化。
- 伺服阀是高精密液压元件,其抗污染能力差,对运行、维护、检修有相当高的技术要求。抗燃液性能指标的劣化对伺服阀的影响很大,伺服阀的许多故障都与油质有关,因此必须对抗燃油进行再生净化处理,使其性能指标符合运行标准。要加强对抗燃油的油质维护,增加一些油质处理设备,保证抗燃油的油质污染颗粒度和酸值在标准范围内。
三、液压系统泄漏的危害及控制
液压系统泄漏影响着系统工作的安全性,造成油液浪费、污染周围环境、增加机器的停工时间、降低生产率、增加生产成本及对产品造成污损,因此,对液压系统的泄漏必须加以控制。
3.1 泄漏的原因
- 冲击和振动造成管接头松动;
- 动密封件及配合件相互磨损;
- 3油温过高及橡胶密封与液压油不相容而变质。
3.2 控制泄漏的措施
3.2.1 少冲击和振动。
为了减少承受冲击和振动的管接头松动引起的泄漏,可以使用减震支架固定所有管子以便吸收冲击和振动,或适当布置压力控制阀来保护系统的所有元件,也可使用低冲击阀或蓄能器来减少冲击。
3.2.2 减少动密封件的磨损。
对于多数动密封件,要做到精确设计、正确安装、合理使用,从而可保证长时间相对无泄漏工作。具体措施有:消除活塞杆和驱动轴密封件上的侧载荷;用防尘圈、防护罩和橡胶套保护活塞杆,防止磨料、粉尘等杂质进入;设计选取合适的过滤装置和便于清洗的油箱,以防止粉尘在油液中累积;使活塞杆和轴的速度尽可能低。
3.2.3对静密封件的要求。
静密封件在刚性固定表面之间防止油液外泄。合理设计密封槽尺寸及公差,使安装后的密封件受到一定挤压产生变形,以便填塞配合表面的微观凹陷,并把密封件内应力提高到高于被密封的压力。当零件刚度或螺栓预紧力不够大时,配合表面将在油液压力作用下分离,造成间隙或加大由于密封表面不够平而可能从开始就存在的间隙。随着配合表面的运动,静密封就成了动密封。粗糙的配合表面将磨损密封件,变动的间隙将蚕食密封件边缘。
3.2.4 合理设计安装板。
当阀组或底板用螺栓固定在安装面上时,为了得到满意的初始密封和防止密封件被挤出沟槽和被磨损,安装面要平直,密封面要求精加工,表面粗糙度要达到0.8μm,平面度要达到0.01/100mm。表面不能有径向划痕,连接螺钉的预紧力要足够大,以防止表面分离。
3.2.5 控制油温防止密封件变质。
密封件过早变质可能是由多种因素引起的,一个重要因素是油温过高。温度每升高10℃则密封件寿命就会减半,所以应合理设计高效液压系统或设置冷却装置,使油液温度保持在65℃以下;另一个因素可能是使用的油液与密封材料的相容性问题,应按使用说明书或有关手册选用液压油和密封件的型式和材质,以解决相容性问题,延长密封件的使用寿命。
四、油中气泡的来源及其对系统的危害
4.1 气泡的来源
液压油在生产、储运以及系统在大气压力下工作,油液中含有空气是不可避免的。往往把油中空气称之为掺混空气,掺混空气是以直径很小的球状气泡悬浮于油中。掺混空气的生成有两条途径:
- 主要是通过油箱和泵的吸入管掺混入油内,如油箱油面太低,泵吸入管口半露于油面或淹深很浅时,均可将空气吸入;若泵的进油管路漏气,则大量的空气会被吸人;系统回油管口高于油箱油面时,高速喷射的系统回油卷带着空气进入油中,又再度经油泵带入系统。
- 溶解于油液中的空气,对油的物理性质没有什么直接的影响。但溶解了一定数量的空气处于饱和状态的油液,流经节流口或泵入口段,当绝对压力下降到油液的空气分离压时,油中过饱和的空气就会被析出,使本来溶解于油中的微细气泡聚集成较大的气泡出现在系统中。
4.2 气泡对系统的危害
4.2.1 造成系统工作不良。
在液压传动系统中,油液是动力的传递介质,在没有空气混人的场合下,其压缩率约为(5~7)x10-10m3/N,也就是压力增加10MPa时,容积仅被压缩减少0.625%。因此,在一般的液压系统中可以认为油是非压缩性流体,而不考虑其压缩性。一旦油中混入空气,其压缩率便会大幅度增加,油液本身具有相当高的刚度或是大的体积弹性系数(压缩率的倒数)则大大减低,严重地危害着系统的工作可靠性,如自动控制失灵、工作机构产生间歇运动、被加工件的废品率增大等。
4.2.2 造成油温升高。
气泡如在泵等的瞬间压缩之后,其温度会急剧升高。如果气体不溶解于油中,其绝热压缩的温升近似值可通过计算得到。例如,将35℃的气泡加压至3.5MPa时,其温升可达到580℃。气泡在达到高温之后,其周围的油便会产生燃烧,成为系统油温骤然升高的主要原因。然而,空气是难以导热的,油中存有气泡时,其导热系数大大减低,将会严重地影响着油的冷却效果。
4.2.3 导致气蚀的发生。
油中气泡被油液带到高压区时,体积急剧缩小,气泡又重新凝聚为液体,使局部区域形成真空,周围液体质点以高速来填补这一空间,质点互相碰撞而产生局部高压,形成液压冲击,使局部压力升高可达数百甚至上千个大气压力。如果这个局部液压冲击作用在固体壁面上,可引起固体壁面的剥蚀,称之为气蚀现象,它对系统的危害性很大。此外,油中气泡还能引起系统的震动和噪声的增加以及泵的容积效率减低等不良影响。
4.3 气泡去除方法
采用油箱自然去除法,就是靠气泡自身的浮力而自行浮至油面溶入大气的方法。气泡的直径一般为0.25~0.5mm,如果气泡界面的油液没有作向上运动的话,完全要靠自身浮力克服油液的摩擦阻力而向上运动。根据斯托克斯法则可知,气泡的上浮速度与气泡的大小及油液黏度有关,也就是说上浮速度与气泡大小成正比、与油液黏度成反比。如直径为0.3mm的气泡在黏度为100mm2/s的油液中每分钟只上浮30mm。由于泵的搅拌作用,微细化后的气泡再经阀口高速喷出成为乳化液状气泡,即使在油箱内滞留相当长的时间,靠自行浮上也是极其困难的。油箱除具有储油、冷却功能之外,体积大的一个根本原因就是考虑到气泡的去除。美国API 614《石油、石化和天然气工业润滑、轴封和控制油系统及辅助设备》规定油箱的体积不得小于泵流量的5倍。但是,采用大体积油箱,往往使装置整体结构变大。